Fiber cement slabs for facades: description and characteristics
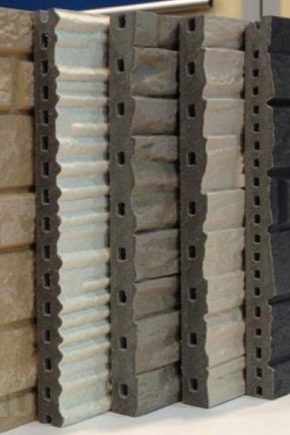
There is a huge variety of materials for construction and repair on the market. Even if you deliberately limit your search to only options suitable for facades, the choice is very difficult. It will be useful for any homeowner and novice builder to familiarize themselves with the properties of a promising fiber cement board.
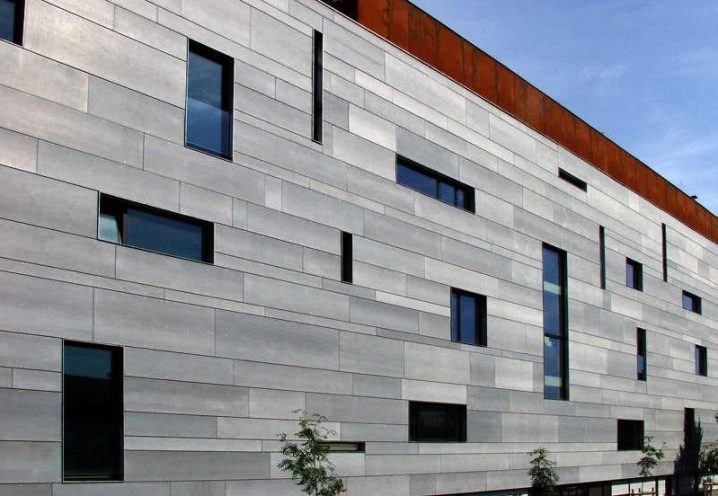
What it is?
Fiber plate helps to make the facade of the home really flawless in appearance. Approximately 9/10 of the total mass of the product falls on cement, which allows you not to fear deterioration of the environmental characteristics of the house. At the same time, excellent strength is guaranteed by the introduction of reinforcing fibers and fibers. These additives increase the operating time of the blocks and make them immune to corrosion processes.
What is important, fiberboard plates do not catch fire, and this immediately distinguishes them from many other options for finishing the facade.
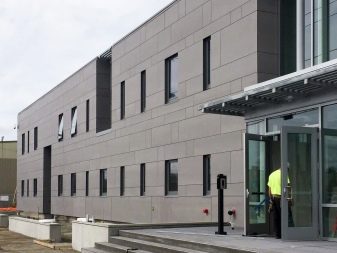
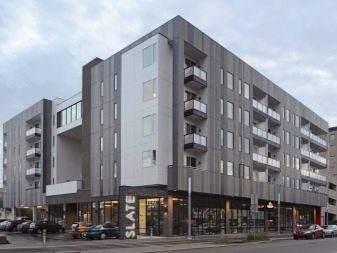
The material works excellently at both high and low temperatures. Biological and chemical influences encountered in everyday conditions do not pose a danger to him. Mechanical strength in general is also guaranteed. Resistance to visible and ultraviolet radiation is also useful for the consumer.
Fiber cement is twice as light as porcelain stoneware when compared to siding, while lightening the load on the foundation does not mean less reliability or heat leakage. The material is cleaned by itself, the main types of contaminants in contact with fiber cement are destroyed, after which rain or snow washes their remains down.
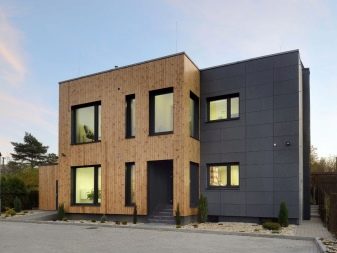
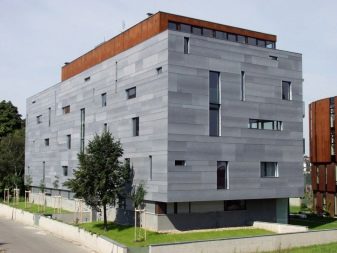
Options
Fiber cement board has not only impressive technical characteristics. It is able to imitate the appearance of natural stone, including granite. It is very easy to install slabs if you have at least minimal experience and basic construction skills. But if you do not have complete confidence in your abilities, it would be more correct to turn to professionals for help.
The main advantages of such a coating are as follows:
- minimal risk of lime formation on the walls, since the blocks are produced using an autoclave;
- the disappearance of the need to prepare the wall and correct its shortcomings;
- affordability with properties comparable to more expensive analogs;
- the ability to finish the facade in any season;
- covering the main structural material from negative meteorological influences.
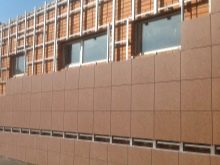
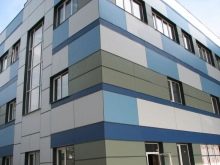
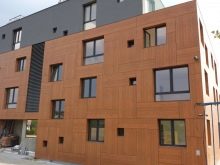
Modern technologies allow the use of fiber cement blocks for the implementation of the most intricate design solutions. There are all possibilities to choose the perfect tone or texture of the details. Unfortunately, there is no way to buy a fiber cement slab with a thickness of 8–9 mm, the maximum indicator is 0.6 cm; the width of the parts varies from 45.5 to 150 cm, and the length - from 120 to 360 cm. The popularity of such solutions is also due to their lightness: a single block is never heavier than 26 kg. And this not only simplifies construction, but also allows you to do without any lifting equipment.
It is also very important to remember about the high rate of water absorption. It reaches 10% of the weight of the product, which leads to deformations up to 2% (insignificant for strength, but which can affect the aesthetics and the state of adjacent blocks and seams). Finally, the fiber cement block is not sawn or cut by hand, so an electric tool should be used.
It is with the mass of the structure that its fundamental drawback is associated. In principle, it is possible to lift such a block alone, but it is unlikely to be convenient and easy.
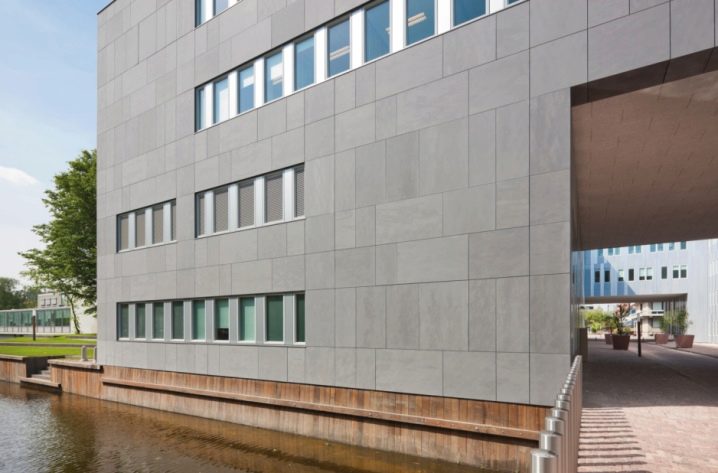
Where can you use it?
- Slabs based on fiber cement proved to be the best where it is required to imitate natural stone inexpensively and with minimal load on the foundation. Solutions that look like brickwork are no less in demand.
- Fiber cement slab is excellent for bath facades and interior decoration. These designs have excellent fire resistance. And some manufacturers additionally strengthen it, achieving maximum security.
- Many people have already appreciated all the advantages of hinged facade structures. A large and light slab allows you to complete all the work in a minimum time, close the slightest imperfections in the surface of the building. In production, these blocks are hardened, and they become very durable. Since the outer side is coated with acrylic and polyurethane, there is no risk even when installed close to a pond or in places where heavy rainfall occurs.
- To create ventilated facades from fiber cement slabs, no special efforts are required.
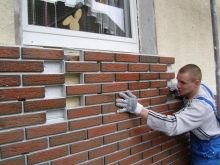
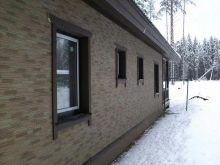
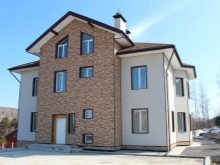
Gap-free laying is done using a similar technology. The difference is that you can limit yourself to a single crate and put the panels directly on the insulation. This measure allows you to reduce labor costs and reduce financial costs. Regardless of the method chosen, the need for materials is calculated in advance.
To work, you need the following tools:
- profiles of various types;
- self-tapping screws;
- dowel-nails;
- accessories that complete the external composition of the panels.
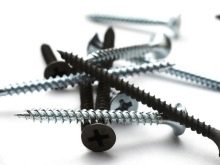


Manufacturers overview
- Completely Russian product "Latonite" cannot be named. The latest developments of foreign companies are used in its production. But this is only a plus, since the company is constantly improving the product and periodically adding new versions to its range.
- If you need products with maximum fire resistance, it is recommended to pay attention to the modification Flamma... She performs well not only in the exterior, but even next to a hot stove.
- A quality Finnish version is, of course, "Minerite"... The slabs supplied from Finland are not only decorative, they also increase the thermal efficiency of buildings.
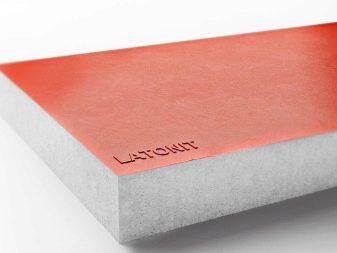
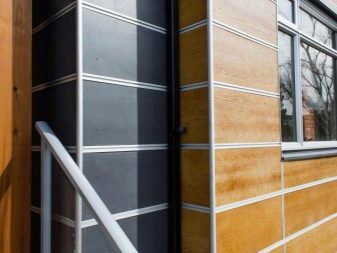
- And here is the fiber cement of the Japanese brand "Nichikha" it is worth choosing for those who want to avoid shrinkage after installation and immediately proceed with the finishing. Another brand from the Land of the Rising Sun Kmew cannot boast of such a characteristic. It has been in production for the fifth decade and has absorbed a wealth of developer experience.
- If you return to Europe again, you should pay attention to Danish Cembrit, proving in practice, year after year, compliance with the most stringent standards.
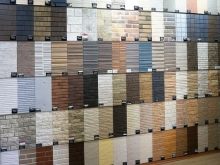
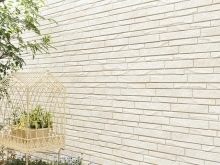
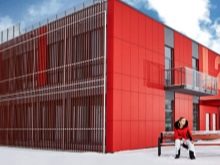
- But the use of blocks can also bring considerable benefit. "Kraspan"... The company has concentrated its efforts on the production of finishing materials for the facade and has already opened over 200 representative offices in Russia. This means that you can purchase goods directly, without intermediaries, almost everywhere.
- "Rospan" Is another attractive domestic brand. In its assortment there are far from only fiber cement boards.
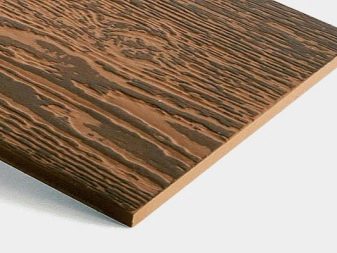
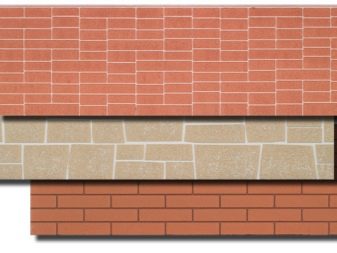
How to choose?
When choosing fiber cement boards, there are a number of subtleties that sellers usually keep silent about.
- So, a part painted in production will be more expensive, but unpainted one still has to be coated with paint, and it is not too easy to do it manually. It will be easy to keep up with the fashion if you buy blocks of fiber cement, imitating decorative plaster. Oak bark coating is especially popular among designers. Good design results are also obtained by using the decor "Flock", "Mosaic", "Stone crumb".
- When choosing, it is useful to pay attention to the density and the specific gravity of the material, for its natural or artificial components.It is very important to think about suitable dimensions and geometric shapes of the coating. In addition to the plates themselves, you have to choose decorative strips for them. The preference for coloring to match the main wall or in contrasting colors depends solely on personal taste and design concept. If the typical dimensions are not enough, you can order longer and wider slats, but not more than 600 cm.
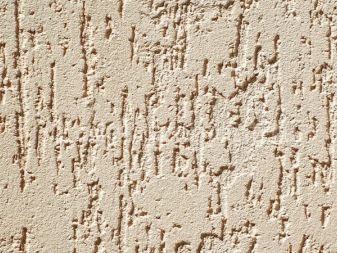
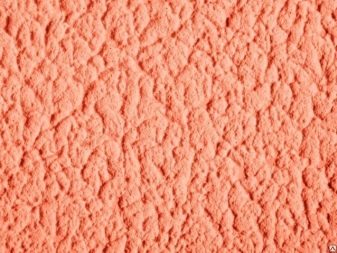
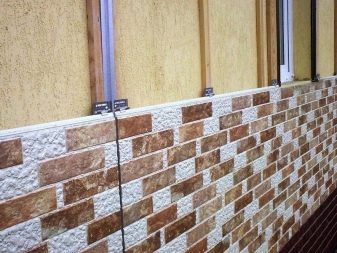
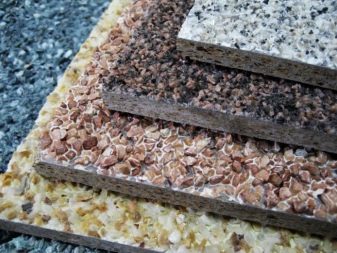
For horizontal and vertical seams, as well as for decorating corners, there are special types of planks. When assessing the need for them, you need to pay attention to the following features:
- the total height of the building;
- dimensions of the plates;
- number of corners;
- the number of windows and doors, their geometry.
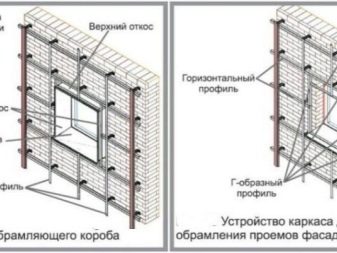
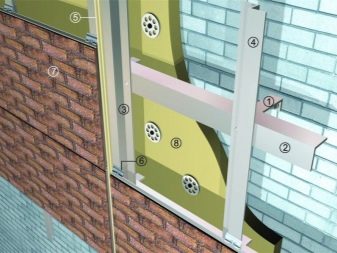
- The structure of the boards does not have to be flattened. There are options that add marble particles or create relief. The most practical size is with a width of 8 mm, often products with a width of 6 or 14 mm are also bought. If you need to get unusual dimensions or non-standard design, you will have to submit an individual order. This will certainly affect both the timing of the work and its cost.
- In the most critical places and when decorating the facade of the bath it is recommended to use smooth boards with a paint layer, treated with fire retardants. Coating with pebble plaster will appeal to those who are looking for blocks with the longest possible service life. In addition, it is more durable than other options.
Fiber cement-based siding "breathes". But at the same time, it surpasses a simple tree in fire resistance, shape stability in various weather conditions and resistance to aggressive insects.
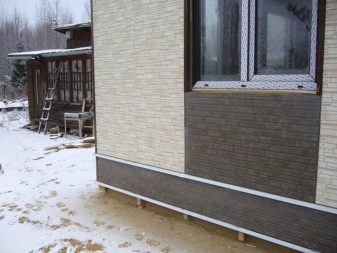
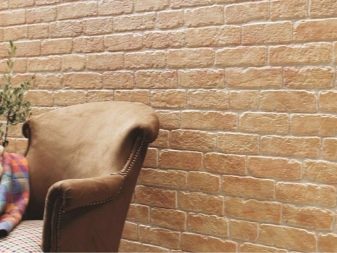
Cladding instructions
The installation of various types of fiber cement boards, if different, is quite insignificant. General technological approaches are stable in any case. The first step is to thoroughly prepare the surface. Although it is formally considered not to be used, responsible builders and seasoned professionals never risk doing so. Removing the old coating and exposing the slightest irregularities, dismantle any parts protruding beyond the contour, eliminate damage.
The next step is to place marks where the brackets will be attached. The mounting distance is 0.6 m vertically and 1 m horizontally.
Most professionals and even experienced DIYers make metal subsystems because wood is not reliable enough. However, this largely depends on personal choice and on what is available to the performers.
Before finishing the house with fiber cement siding, it is required to prepare an insulating layer.
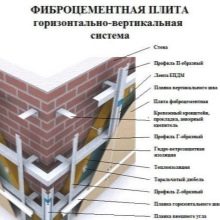
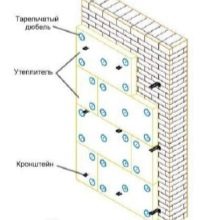
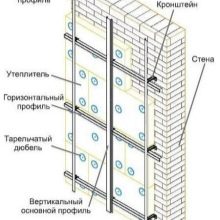
A typical solution in this situation is the use of fiberglass, which is attached to dowels with a wide head. The slabs themselves are attached using staples or nails. You can choose the appropriate method based on the thickness of the blocks.
The panels should be purchased with a margin, even a simple cut to the exact size can bring a loss of 5-7%. The gaps between the plates must be closed with dividing strips, otherwise the most even joint will not be obtained.
In order for the facade surfaces to retain their attractive appearance for a long time, it is recommended to cover these strips on top with a layer of sealant. You should not try to mount fiber cement panels using "wet" technology, it will only ruin everything. When doing the work with your own hands, you need to choose such dowels that will sink at least 3 cm into the material. From the insulation to the boards used, a gap of at least 4 cm is always left. The upper strip of the panels is equipped with a ventilated backing, which ensures effective air circulation. At the outer corners, steel corners are placed in the color of the main coating.
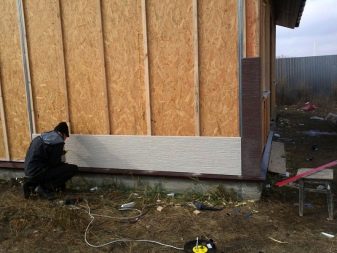
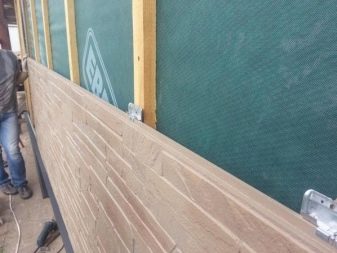
When installing with grooves, clamps are used, and only the attachment of the thinnest elements to the frame profiles vertically is done with self-tapping screwscomplemented by a sealing tape. In this case, the assembly pitch is reduced to 400 mm vertically.Where the panel is attached, there must be an opening at least 50 mm from the outer edges of the material. The creation of very large gaps, both vertically and horizontally, is not allowed. They should be at most 0.2 cm. Horizontal ligaments, where decorative ebb is used, are allowed to be made with a gap of 1 cm.
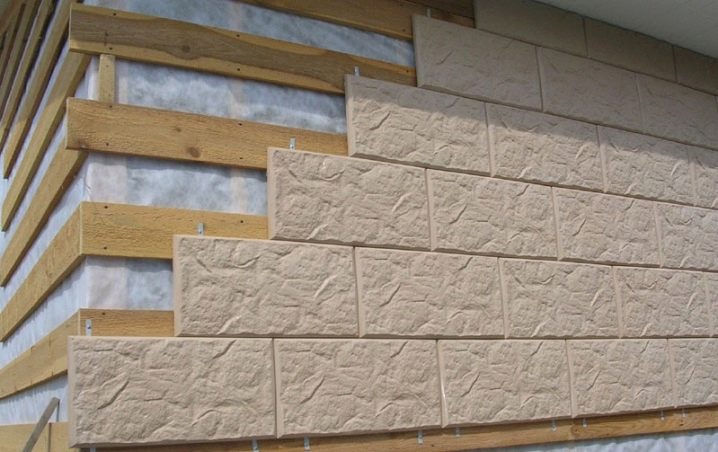
You will learn more about the installation of fiber cement boards in the next video.
The comment was sent successfully.