Diesel hammers: device and varieties
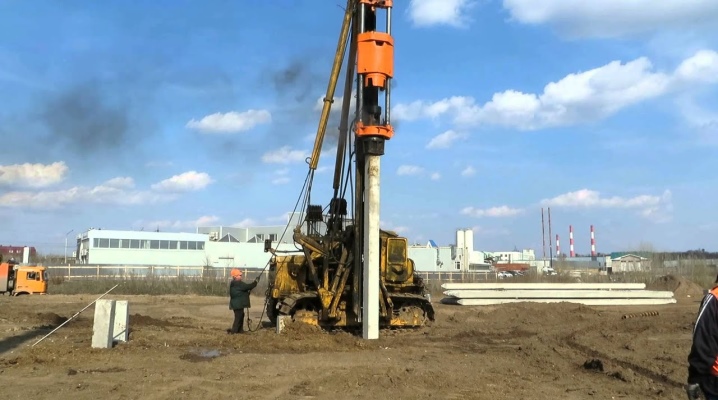
Diesel hammer is a special device designed to drive piles into the ground. The principle of operation of such equipment is similar to that of a diesel engine. It is worth taking a closer look at what an aggregate is and what types it has.
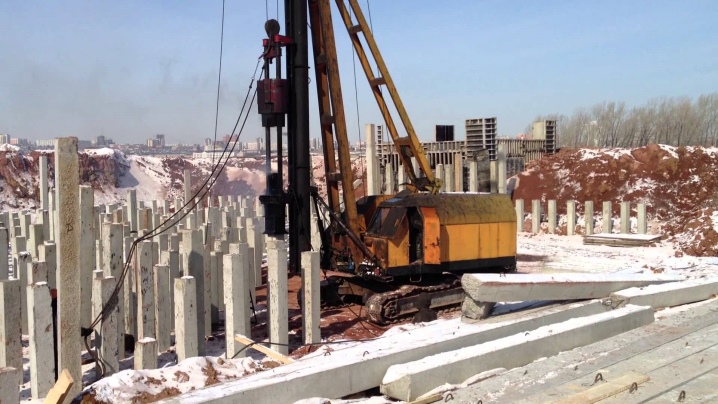
What it is?
A diesel hammer is a direct-acting internal combustion engine, the purpose of which is to drive pile foundations. The principle of operation of the pile driver is similar to that of a two-stroke diesel engine. Features of such equipment:
- in autonomy of work;
- easy operation;
- simple design.
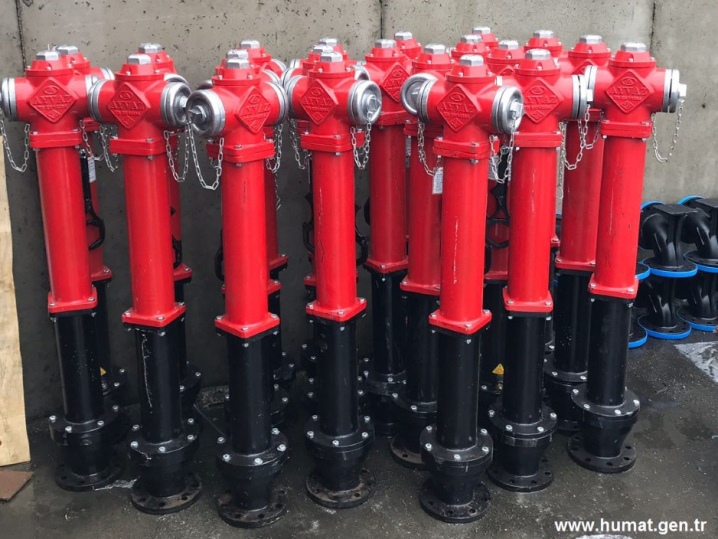
For operation, diesel hammers are suspended from a special boom, using device grips that provide lifting and lowering of equipment. It is noteworthy that such grips are also called "cats".
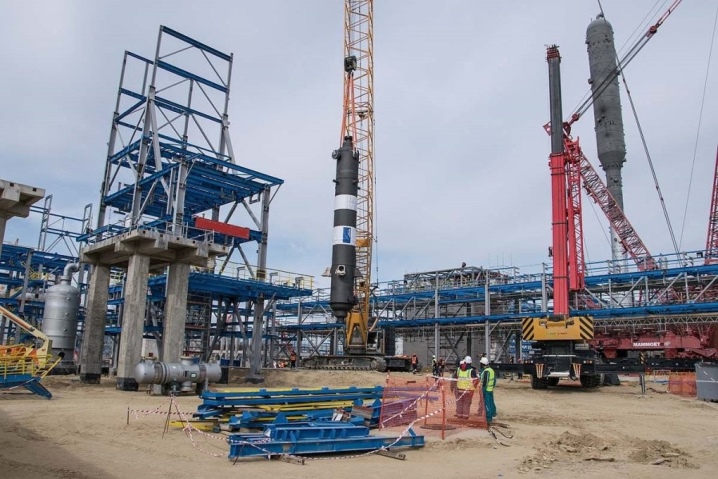
They allow the hammer to move up and down in a given direction and drive the pile.
Advantages and disadvantages
Regardless of the type of diesel hammer, such units have their positive and negative sides. The pluses include:
- simple design;
- autonomy of work;
- high performance characteristics.
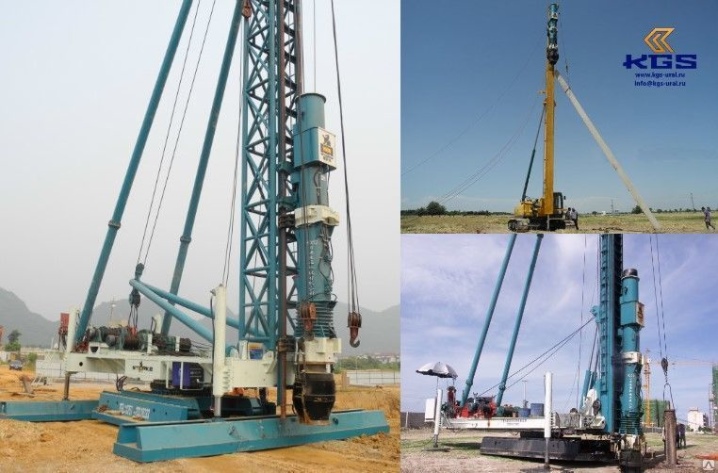
As for the shortcomings, there are not so many of them. The first is the vibration of the ground that occurs after being hit by a hammer. The second disadvantage is the large amount of dust generated during operation. Another disadvantage is the increased emission of harmful substances, leading to atmospheric pollution and deterioration of working conditions.
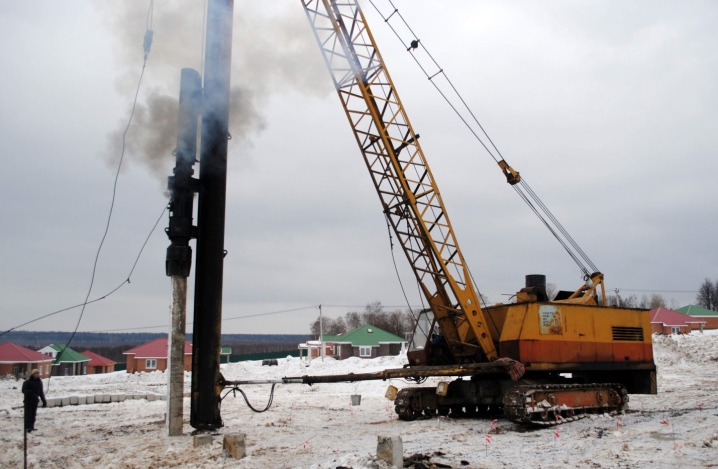
Device and principle of operation
The design of a diesel hammer includes the following elements:
- piston block;
- shock or working part;
- pump;
- hinge support.
In turn, the drum part also contains additional elements. Its design includes a cylinder, a fuel tank and "crampons".
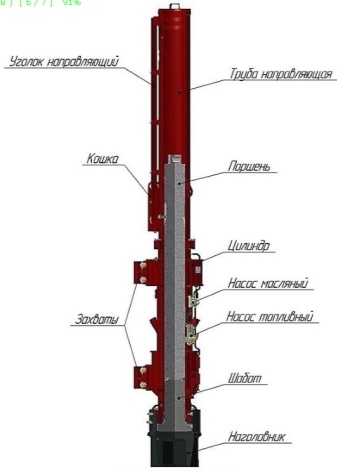
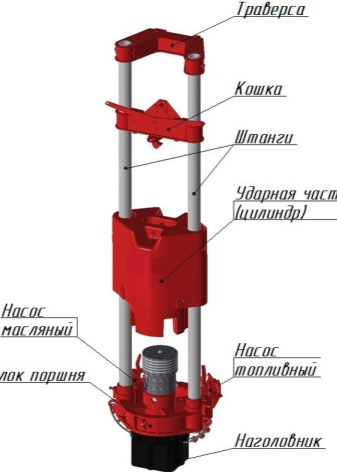
With the help of the latter, the hammer is suspended on the drift cables. The hammer frame is assembled from guides located in a vertical plane. They are usually connected with a headrest from the bottom to ensure the rigidity of the structure. The upper part of the hammer is considered to be impact, and it moves freely.
The headrest of the structure contains a piston due to which the structure moves. The principle of the hammer is not as complicated as it might seem. The blow to the headgear occurs after the cylinder can be raised to the stop, where the traverse is located, and then sharply lower it. It should be noted that at the time of ascent, the air is compressed, due to which the temperature rises. At the same moment, a stream of liquid fuel enters it, which instantly ignites and forms gases, allowing the cylinder to rise sharply.
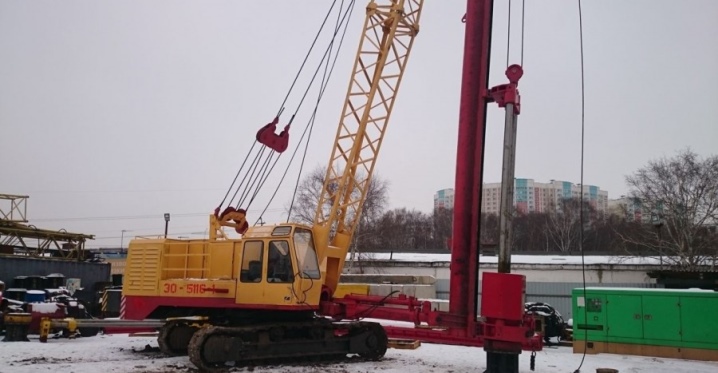
When the cylinder reaches the traverse and begins to move downward, the air in it will begin to compress again. Thus, when the element descends, an explosion will occur again, after which the cycle will repeat. This is how the unit works.
One of the key parts of the hammer is the fuel pump.
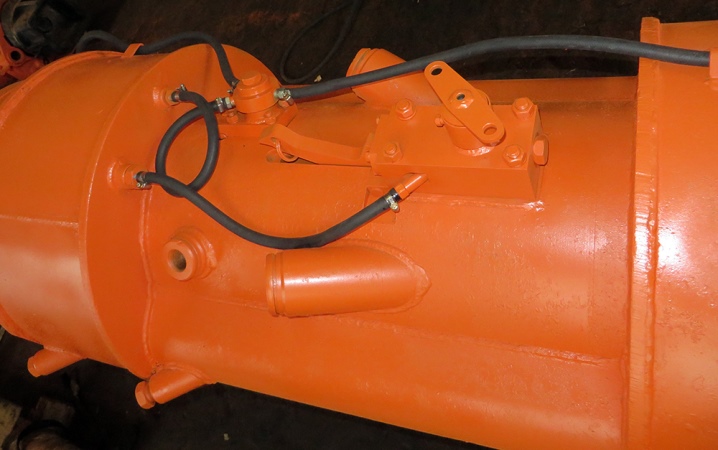
With its help, a timely discharge of the combustible mixture into the cylinder, which is located on the headrest, occurs. The mixture enters through a special fuel line, at the end of which there is a nozzle. Releasing the lever activates the injector and the fuel enters the cylinder. The lever itself is located at the top of the pump structure.
It is noteworthy that the fuel supply process is automated, and it is carried out directly by the cylinder when it falls down. This result is achieved due to the provided stop from the outside.
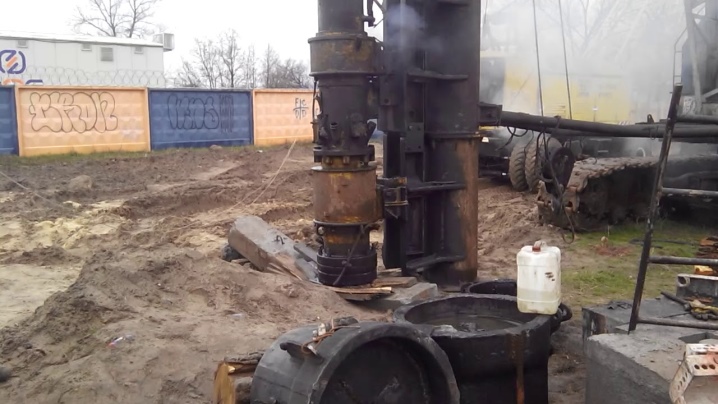
A device with a hook is placed between the traverse and the cylinder. It holds the cylinder in the required position. The device is fixed by means of a winch cable, due to the work of which the hammer is lifted during the installation of the equipment on the pile.
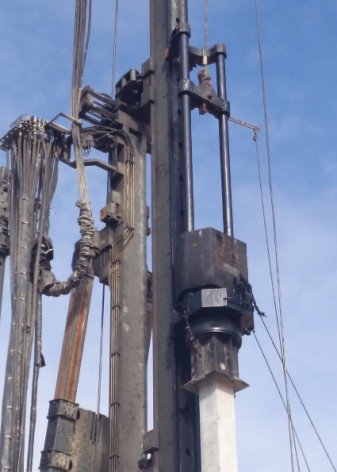
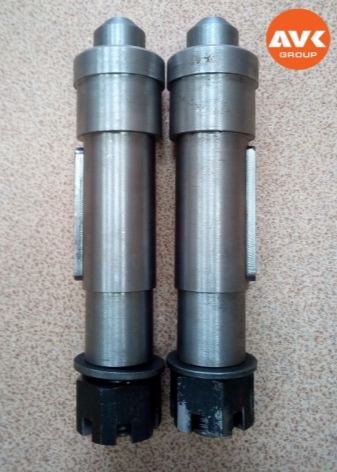
Basic types
First of all, you need to pay attention to the fact that there are several classifications of diesel hammers. It is worth taking a closer look at two of them, since they are the most popular.
By design type
If we consider the classification by design features, then diesel hammers are divided:
- on tubular;
- rod.
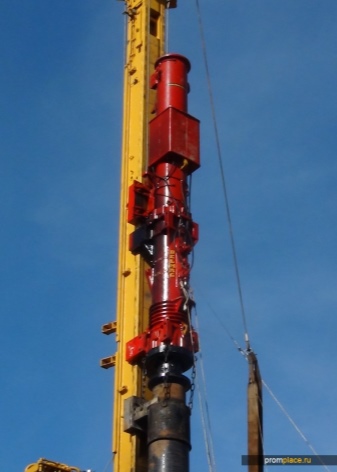
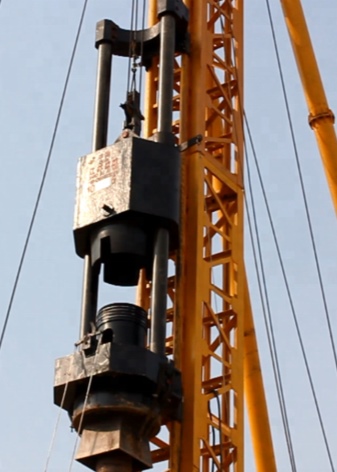
The features of these types should be considered separately, depending on the type chosen.
Rod
The design contains the following elements:
- a piston that stands on a special support;
- vertical guides;
- a system for supplying a combustible mixture;
- "Cats", providing fixation of the structure in the required place.
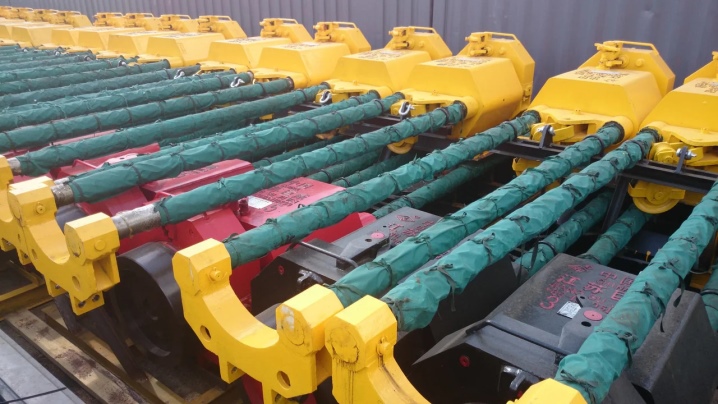
Upon closer examination of the details, you will notice that the block is a monolithic structure.
It is cast inside the hammer body, and in the block itself, in addition to the piston, there are also compression rings, hoses through which fuel flows, and nozzles. The latter are responsible for spraying the mixture in the pump.
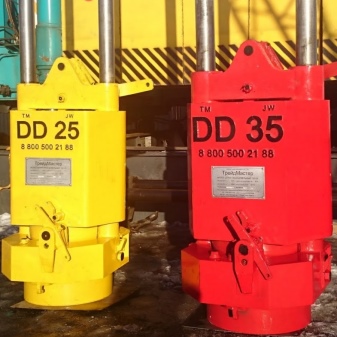
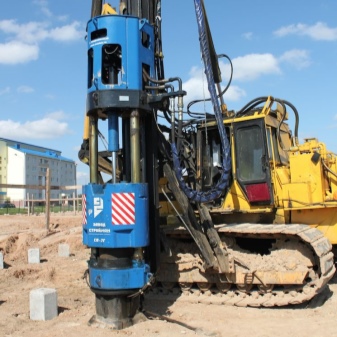
The block itself, as already noted, is on a hinged support. Its bottom wall holds vertical guides that allow the hammer to move during pile driving. To make the structure more rigid, it was decided to connect the guides to each other with a horizontal traverse.
When the equipment starts up, the hammer moves along the rails. It moves up and down to drive piles. Additionally, it should be noted the presence of a chamber for combustion of fuel fluid at the bottom of the body of the impact part.
Tubular
The peculiarity of the design of tubular diesel hammers is that it is completely unified and created on the basis of a tractor. In other words, the production of such equipment is carried out according to a proven and well-established scheme.
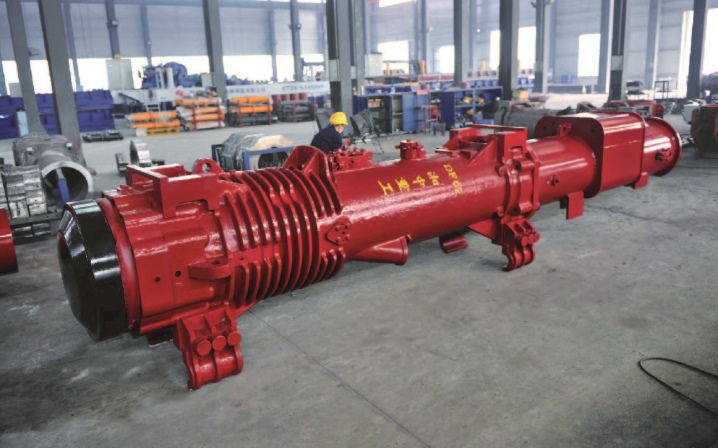
Thus, such a hammer is practically indistinguishable from a standard tubular apparatus.
Basic structural elements.
- "Cats". They are the main equipment for fixing the hammer. The advantage of the device is the presence of an automatic mechanism that ensures the timely fixation of the element or its reset.
- Impact piston. Contains compression rings for improved performance.
- Shabot. This is the striking surface, in the process of hammer operation, in contact with the striker.
- Working part cylinder. In it, an explosion of the fuel mixture is carried out, which ensures the lifting of the hammer.
- Cooling system. Prevents equipment overheating.
- Lubrication system. Provides durability of the structure.
- Guide tube. It is made of high strength steel.
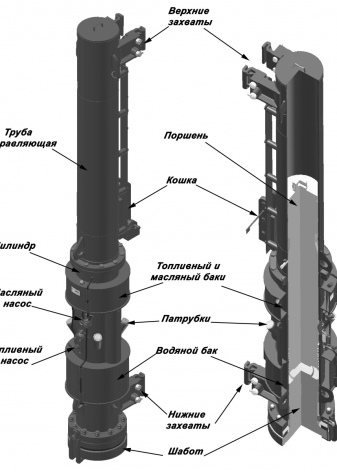
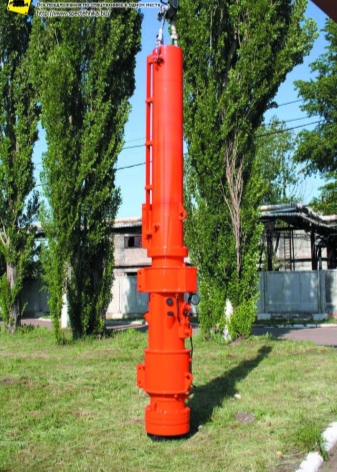
The difference between the two types of construction is the presence of a forced water cooling system. It is available for tubular-type units, and for sucker-rod units it is absent.
In this regard, when using equipment of the second type, it becomes necessary to organize regular breaks. This is done so that the structural elements cool naturally. If this is not foreseen, the hammer may fail.
By weight
The classification by weight of the striking part of the hammer implies the presence of three groups:
- light hammers - up to 600 kg;
- medium hammers - 600-1800 kg;
- heavy hammers - all tools weighing more than 2.5 tons.
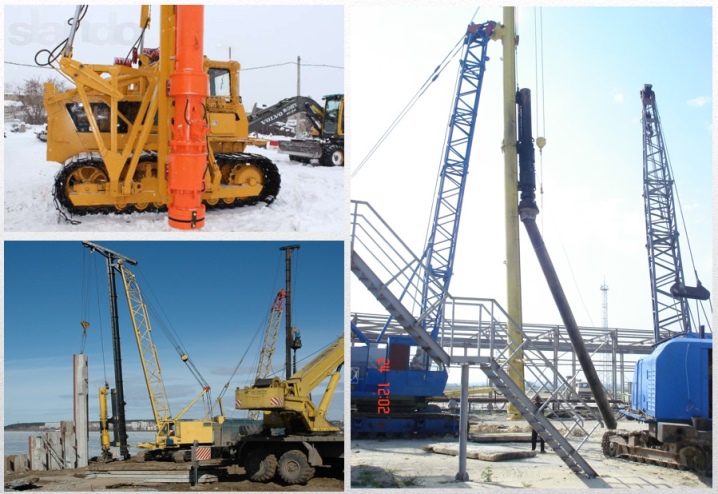
The latter are considered the most demanded at any construction site. The former are used for driving small piles in soft soils, as well as for various studies.
Features of operation
First of all, it is necessary to pay attention to the fact that the combustion of the fuel is carried out at the moment when the spherical recesses located on the woman and the shabot are connected to each other. When the elements are connected, a chamber is formed, inside which, under the influence of high temperatures, the fuel mixture explodes.
The flow of fuel into the chamber is carried out by means of injection. As soon as the liquid self-ignites, the woman instantly moves up to the stop, and then immediately begins to descend back. This is how the pile is driven.
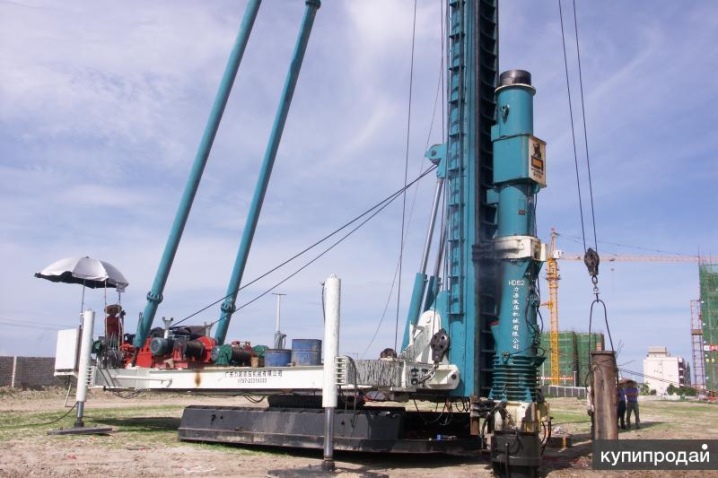
When comparing the two types of diesel hammers, it can be noted that sucker rod breakers are significantly inferior in terms of service life. Tubular structures last longer. This is mainly due to the automated cooling system.
Hammers for driving piles are used only if the soil density indicators meet the established requirements and are considered low enough to drive the structure.
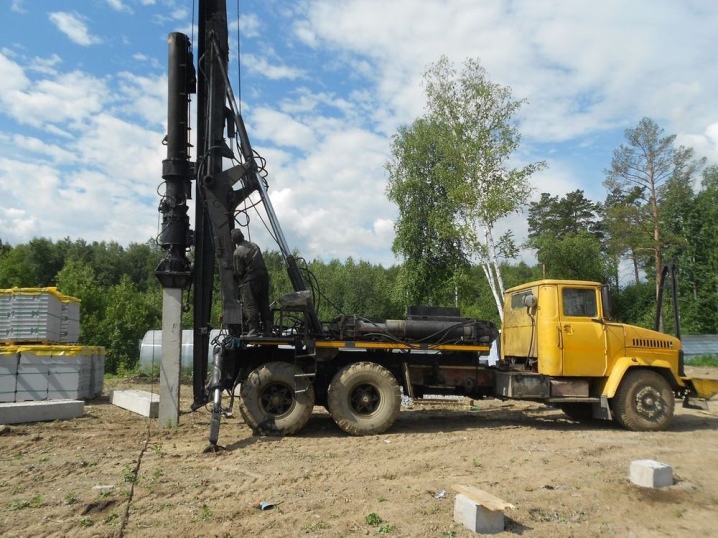
This is explained by the fact that the equipment has a small impact energy. It is approximately 27-30% of the potential energy. In this regard, heavy hammers are considered the most popular, the weight of which reaches 2.5-3 tons. The impact force of such devices of the method exceeds 40 kJ, and the installation itself can perform up to 55 blows per minute.
Tubular hammers are called universal hammers. They are used for driving reinforced concrete piles, regardless of the type of soil at the construction site. The advantage of the design is that it can be used when working with permafrost soil. However, in this case, you will need to drill a channel.
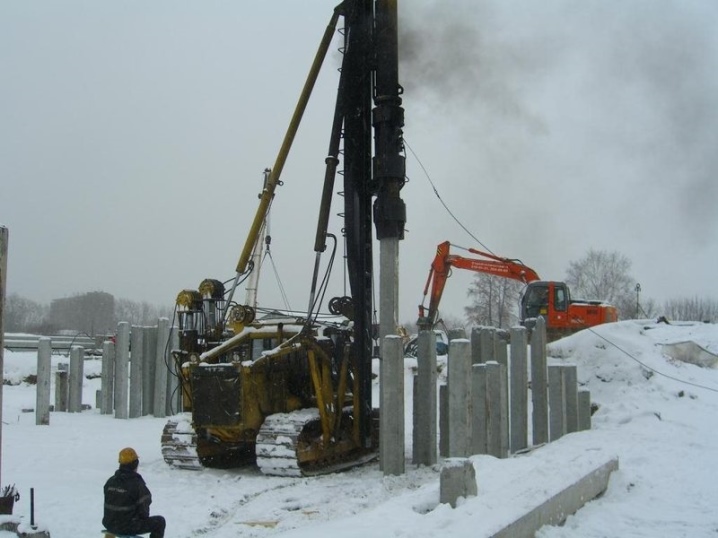
The sequence of the hammer is as follows.
- First, the piston part is docked with the crumb.
- Then both elements are raised to the top position. To do this, use a copra winch.
- The third stage is automatic undocking of elements. This is done so that the striking part begins to fall along the guide.
- During the fall of the hammer, the pump is turned on. Inside it, fuel is pumped into a special recess.
- As soon as the hammer reaches the desired position, air is compressed inside it, and a fuel mixture is injected.
- When the piston strikes the surface of the shabot, an explosion occurs, due to which the hammer rises up again. In this case, the energy is distributed to the lifting of the element and to driving the pile.
The immersion and operation of the hammer is carried out due to the impact of several types of energies at once: shock and gas-dynamic.
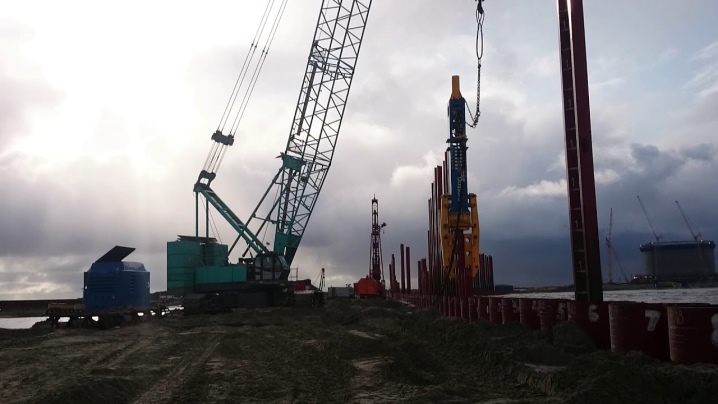
Diesel hammer operation in the video below.
The comment was sent successfully.