How to make a table for a circular saw with your own hands?

The circular saw is an excellent maneuverable tool with high productivity. However, like all tools, the saw has some disadvantages. For example, you may have trouble cutting large pieces of wood. In such a situation, a special table made by hand will help you. This design will allow you to easily and quickly cut large parts without unnecessary problems.
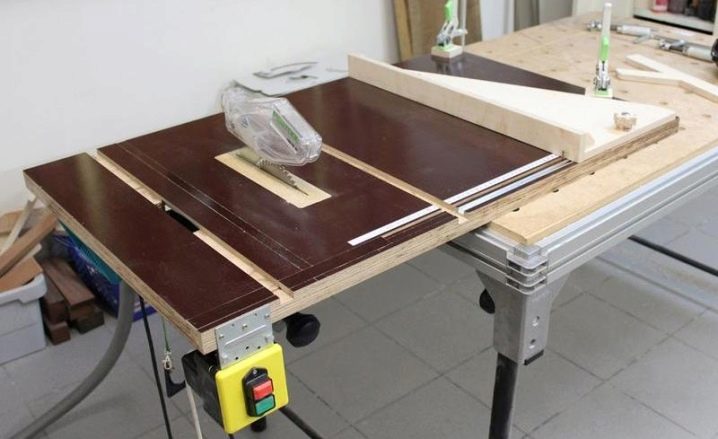
Selection of tools and materials
At the beginning of work, you need to make sure that all the necessary raw materials are always at hand, as well as a set of tools that would be useful throughout all actions. To create a table, you need the following materials:
- plywood about 2-3 centimeters thick or an identical piece of chipboard;
- wooden bars measuring 40x40 millimeters;
- metal building corners - 12-15 pieces;
- self-tapping screws of different lengths and bolts of different classifications;
- glue used in carpentry;
- means for treating the product against moisture and rust;
- external socket;
- cable;
- switch.




This set of materials is required for a standard construction of ordinary dimensions with an area of just over one square meter. Almost any hand-held circular saw can work on such a table, except for tools with small discs, since the cutting depth sags by an average of 1-2 centimeters during attachment to the tabletop.
The following tools will come in handy for your work:
- marker or thick pencil;
- tape measure, metal ruler, angle;
- jigsaw;
- screwdriver;
- Grinder;
- drill;
- sandpaper.

Manufacturing process
It is quite simple to create with your own hands a multifunctional design for an electric circular saw, however, it is necessary that the manufacturing process goes strictly according to certain stages. Strict adherence to the advice is necessary so that there are no problems or difficulties.
- First of all, each master must create a drawing and a plan for the future product. According to the drawings, the work is much easier to perform, the risks of making something wrong or of poor quality are reduced. At the planning stage, you need to take into account the dimensions of the future structure as clearly as possible.
- After creating a plan and a rough sketch of the product, as well as preparing all the necessary materials and a set of tools, we begin to manufacture the table body. We align all the edges of the bar with a plane. Then, from sheet material and aligned bars, we assemble the base, the dimensions of which were determined at the planning stage. The working surface area is usually about 1-1.5 square meters. All parts are attached to each other with bolts and screws. At the end of the work, we get a box without the upper and lower parts.


- Next comes the manufacture of a tabletop for a sawing machine, it is cut out of plywood or chipboard sheet based on the size of the frame. The table top should be the same area or slightly larger. The main thing is that it does not outweigh the body to one side. If the table top is made of non-laminated material, then it should be sanded and trimmed. Further, using a ruler and a pencil on the tabletop, the marking of the attachment points of the electric saw to it, as well as the upper part of the table to the main body, is carried out.
- The next step is to cut the hole for the saw itself.For this, measurements are taken of the support shoe of the sawing machine, which will later be used on this structure. On the reverse side of the tabletop, the corresponding markings are made, which will precisely determine the attachment point and the area along which you need to make a cutout for the circular disc. For accurate marking, it is better to draw axes that connect exactly in the center of the plywood sheet. After determining the axes and making accurate markings, you need to cut out a hole for the disc, and also drill holes for attaching the saw shoe.



- The circular saw is attached to the plywood tabletop from the back (inside). To do this, you need to make 4 holes in the shoe of the saw itself, their diameter should be about 1 centimeter. Then you should completely align the saw and match all the markings so that the tool is level, all the marks and holes correspond to each other, the disk freely fits into the central hole of the tabletop. In order for the saw to be securely attached to the table, it is necessary to use special countersunk plow bolts, the head of such bolts should be deeply immersed in the sole of the tool and not stick out.
- Then the saw is set aside and the assembly of the table continues. In order for the structure to be stable. special attention should be paid to her legs. The legs that diverge downward will provide the best stability of the structure. They are fixed with large bolts and nuts.
The length of the legs is determined individually, in accordance with the height of the person who will work at the table. Ideally, the tabletop, and, accordingly, the saw itself should be located just above the master's belt.



- The next step is to attach the tabletop to the cabinet. At a distance of about 3 centimeters from the edge, you need to make holes in the corners of the plywood, then holes are drilled in the corner bars for further fastening the bolts in them. Further, the parts are connected using steel fittings M8.
- After the structure is assembled, it is necessary to fix a special switch on the table, which will regulate the turning on and off of the saw with an electric motor. To do this, cut a hole in the housing for the switch and fix it with bolts, special glue or a construction screed. There must be electrical power from the switch to the saw itself, which means it must be connected to any electrical source in your workshop using a cable. It is attached from the side of the lower part of the countertop using construction fasteners.
- Then you can make special stops. First, a cross beam is made, it greatly simplifies the work with the structure. It is carried out mainly from plywood or chipboard. First, you need to cut out 2 strips equal in length to the width of the table, the second side should be about 100 millimeters, the corners of the strips must be rounded.



- Then the workpieces are ground and fastened with self-tapping screws at a slight angle, a metal corner is screwed inside. After that, the strips are attached to the table on movable furniture rails, which will allow these stops to move along the entire table.
- If you wish, you can make various additions to this design, it all depends on your skills. Some craftsmen remove the safety guard and all the devices for adjusting the inclination of the blade, this allows you to get an additional few millimeters of cut. Some replace the factory platform with a turntable of their own manufacture, with a professional approach this also gives a number of advantages in work.
- The construction is completed with the stage of processing and preparation for operation. Once again, the entire table should be sanded, wiped and varnished or with special agents that ensure durability of use and repell moisture and rust.



Installing a circular saw in a homemade table
After making the main body, the electric saw is being installed in a homemade table.
- At the stages of manufacturing the table structure, all the necessary holes were cut out in the tabletop.
- When installing a stationary saw, it is necessary to perfectly adjust the inclination of the tool, otherwise the sawing of wooden parts will be of poor quality. The first step is to install the tool on the finished tabletop in all grooves and determine whether you need to change the slope. If the angle does not correspond to the desired one, then you will have to adjust it using special bolts, this is the easiest option. Or you can cut out special blocks that will be attached to the tabletop, and already on top of them, at the right angle, an electric saw will be attached.
- When the tool is in place correctly, all holes converge, position and bolt the soleplate to the table and tighten them from the inside using nuts with lock washers.
- After the hand-held circular saw is installed, you need to take a block slightly larger than those with which the tilt angle was adjusted and fasten it to the tabletop in the place where the saw platform was marked.



This block is needed so that after dismantling the circular saw from the table, you can build it in exactly the same place without using any additional markings.
Advice
- Before using the electric saw on the table, you should check the saw blade itself using a square, since some unscrupulous manufacturers do not install the blade exactly at an angle of 90 degrees, as a result, the cuts turn out to be beveled.
- If during work you plan to use the table also for storing tools on it, then the dimensions of the tabletop should be more than a square meter in area.
- For manufacturing, it is better to use high-quality and durable materials, otherwise the table will not last long.
- The table can be supplemented with anything you like, for example, some manage to attach a special vacuum cleaner or a riving knife with a disc protection to it, so that chips and residues from cutting wood do not fly around.
- Choose a place for the table in advance, and also make sure that the floor where the table will be installed is level.
- If you have the desire and certain skills, you can make a folding tabletop or lifting table, but this will take more time and materials.
- If the table shakes or vibrates during operation, adjust the feet with suitable pieces of rubber.



Since a circular saw is an electrical device, it is better to work with it by a specialist who understands electricity. It is also better to entrust the transfer of the switch to another place to a specialist.
Safety engineering
- it is preferable to carry out work with wood, metal and chemicals outdoors or in a well-ventilated area;
- the workplace must be kept clean and tidy;
- periodically it is necessary to check the stability of the structure, as well as the serviceability of equipment and electrical appliances;
- before turning on the saw, you need to make sure that it is well fixed;
- when working, you need to use special glasses and gloves;
- keep a first aid kit close at hand.

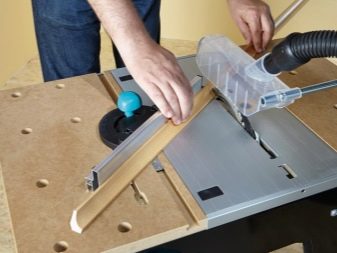
Making a table for a circular saw is not so difficult, but it does require some skill in joinery. Having at hand the necessary tools and materials and clearly following the step-by-step instructions, you can make a table of the required dimensions, as well as equip it with all the necessary additions.
For information on how to make a table for a circular saw with your own hands, see the next video.
The comment was sent successfully.