How to make a circular from a grinder with your own hands?
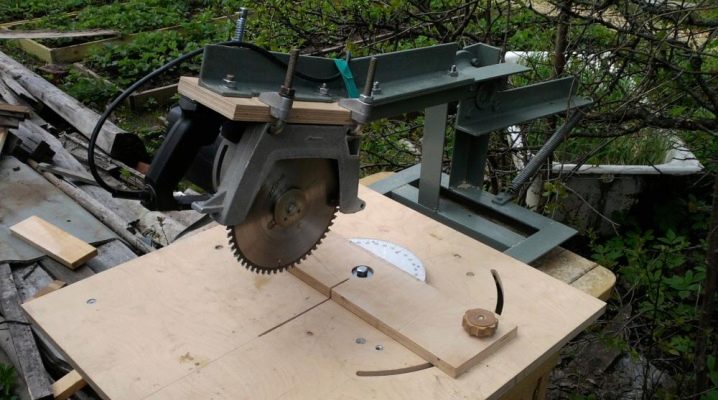
Almost every private building has a utility room. It most often stores building materials and tools, implements and agricultural machinery.
This article will focus on how to independently make a circular saw based on an engine from a grinder from improvised tools left over after repairs.


Design features
It is possible to carry out work on transforming one type of saw into another using old elements left over from repairs. With locksmith skills and ingenuity, you can effortlessly cope with this task.
Distinctive features of this type of device are that there are circular saws from a grinder as a home-made machine or manual device fixed on a table or other base.
If you have an old grinder, then the engine is best removed from it and used as the core of a future saw. A washing machine motor is also suitable.


Any circular has several main components:
- homemade table as a stable frame;
- saw stand;
- engine from angle grinder;
- slip stop;
- a bar for adjusting the cutting height;
- reducer, saw blade.


This machine is suitable for cutting small wooden beams. When it is planned to process wood in large quantities and large dimensions, it is better to purchase ready-made production equipment. Its cost is high, however, this purchase will be an ideal solution for business.
To work safely on the circular saw, care should be taken when choosing a blade for it. The grinder is a complex tool and you cannot use a disc from it for cutting wood products. It can jam at any time.
Rotating at a very high speed, such an element is capable of crushing the tree into chips, from which you can get injured. This is because there is a high temperature load on the disk during processing. It is best to purchase a new product specifically for your circular saw.

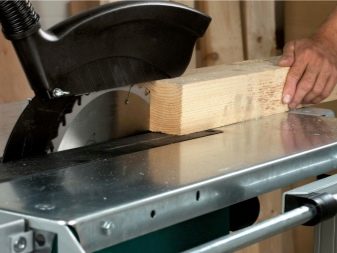
If the circular is fixed to the floor, then the frame should be fixed with fasteners (corners) to ensure its stability. For the manufacture of the bed, you can take an unnecessary cabinet or several sheets of chipboard. However, it is safer to make it out of metal..
The main work surface of the countertop is best made of plywood or laminated chipboard. The table must be very firmly on the floor so that vibration is negligible.
The disc is installed on the saw with a smaller diameterthan the one used for the grinder - this will prevent the engine from overheating. You can buy it both in auto parts stores and in specialized construction markets. The engine power of the grinder, from which the circular is made, should not be less than 1600 watts.
A more complex option involves the installation of additional elements: a pulley system, a belt drive. With this method of manufacturing, a homemade structure will take the form of a production machine. The presence of a belt will reduce the speed of the disc rotation.

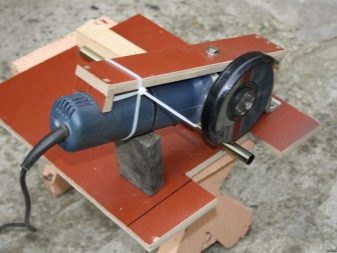
Necessary tools
To work, you will need tools, building materials or pieces of pieces of assembly parts of old furniture.
You will need:
- pliers, screwdriver, adjustable wrenches, hammer;
- metal sheet, corners, nuts, bolts, screws, fasteners;
- grinder and electric drill, switch and socket;
- screwdriver, ruler.


Step-by-step instruction
The process of making a circular from a grinder with your own hands includes a number of stages:
- first of all, you need to make a base table;
- install the grinder itself and the disc;
- attach the stop bar;
- supply electricity;
- conduct a test run.
The main element of both the mini-sample and the stationary version of the circular is the frame table. You can make it using the drawings, or build it to your liking, observing the basic principle of making such a part of the saw. Everything will depend on the size of the wood material that you are going to cut in the future.
We will tell you how to convert a grinder into a miniature circular. With its help, you can saw bars, small boards, slats used for repairs or in private households.


The table looks like a workbench, the base of which is most often made of lumber.
- First, they take sheets of chipboard and hammer together a miniature table from them., the legs of which are performed at such a height that a grinder is placed under the bed. Attach them to the stiffening ribs. Those, in turn, are made of small boards and fixed along the edge of the tabletop at a distance of 7-10 cm from its bottom side using self-tapping screws.
- It is advisable to make the upper work surface of laminated plywood.... When the tabletop (bed) is ready, it is turned upside down and marked for the installation of a grinder and a saw blade. An element from a grinder is taken as a basis, measurements are made on it for a slot for a new disc. At its ends, the extreme boundaries of the future hole (slots) are marked with a pencil. Then take a drill and drill the formed points.


- After that use a ruler to connect the edges of the holes formedby drawing two parallel lines across their width. Part of the countertop inside such lines is cut out with a grinder. The disc slot is ready.
- Then you should purchase a new disc from the store... The best option would be to buy a sample for woodworking with a size of 125 mm with carbide teeth - there can be 24, 36, 48 of them.
- A bar is screwed under the working surface of the table, to which the grinder is attachedusing clamps. It can be fixed with self-made clamps and tightening nuts. At the same time, the disk itself is installed in the table (in the cut hole). It should be positioned so that most of it is on the surface. It is advisable to mount the protective visor. It is sold in any hardware store, so you can easily buy such an item. They usually attach it to the hinges, making it possible to recline the visor.


- A stop bar is made from a metal corner or from a plastic trim of an old plinth... You can fix it on plywood or chipboard. In length, this bar should be the same as the working surface of the table. Screw the bar (stop) at a distance of at least 2 cm from the saw blade teeth. At the ends of the rail, two holes are made and fixation is carried out in the table using bolts or ordinary self-tapping screws.
- The board or block to be treated must fit completely on the table topbecause when the blade moves at high speed, the lumber is subject to vibration. It is impossible to keep the lumber in weight - there is a possibility of serious injury.
- At the next stage of work on the inside of the mini-table they attach an electrical outlet, through which the wire is run and then the switch is installed. Usually, its fixation is carried out from the outside of one of the stiffening ribs. The wire from the switch is directed to the power source - thus the electricity is supplied to the circular.
When the saw is ready, make a test run and cut small blocks, paying attention to the speed of rotation of the blade.
This concludes the work.


Craftsmen, in order not to make a table for a circular, use a vice as a supporting frame... At the very beginning, a grinder is clamped with a disc on the edge of a regular table by removing the protection and unscrewing the grinder's handle. Then they take plywood or chipboard to form a frame in which a hole is made for a disk. They fix it by drilling a hole, a bolt is inserted into it. It should line up with the hole on the grinder where the handle is attached. The bolt is tightened to the stop using a wrench.
A stop bar or limiter is made from scrap materials. They fasten it with bolts at the ends of the bed using ordinary self-tapping screws. Under the weight, the grinder can lean forward and hook the tabletop itself with the disc. In this case, a handle is needed. It can be unscrewed from the old seaming key and screwed into the grinder, making a support for the engine.
Such a miniature home-made design works clearly, cutting the slats and beams produces efficiently.


Operating rules
The use of structures such as homemade saws equipped with discs in wood processing imposes certain responsibilities on their owners.
In addition to a table well fixed to the floor and a protective cover on the disc, it is necessary to organize the supply of sawmill material in both directions: from right to left and back. Boards and slats cannot be moved along the bed while the circular is in operation with your hands, for this you should use a bar or its analogue made of wood. It is not recommended to be near the rotating blade at a distance less than 25-30 cm.Do not keep your hands close to the saw - fingers can be injured.
You need to turn on and off the circular saw using a button located either on the side or in front of the unit. When the disc rotates, it is forbidden to stand behind it or in front of it.


Security measures
To avoid eye contact with small wood when sawing, as well as chips, it is imperative to work with glasses. Care should be taken to make sure that the sawing is done in a well-lit room or that the circular saw is in an area open to sunlight.
When working with cutting material, make sure that there are no nails or large knots in it.... This circumstance can provoke a breakage of the disc or a change in the direction of a moving bar or rail. In the best case, the engine can be damaged and the disc dull. In the worst case, the building material escaping from the hands will injure the person who is engaged in sawing or people who are nearby.
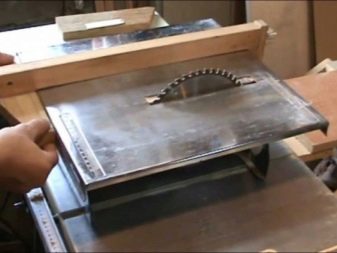

Do not turn on the circular saw with wet hands. It is strictly forbidden to carry out work under the influence of alcohol. Cuttings of sawn material can only be removed from the working surface of the bed when the cutting blade has come to a complete stop.
Thus, anyone who knows how to work with construction tools and who has the skills to make wooden or metal structures can make a circular at home. It is necessary to follow the rules for operating the unit. Such a saw will become your assistant in the future and will significantly reduce the labor costs for processing sawn timber used in a personal household.
For how to make a circular from a grinder with your own hands, see the next video.
The comment was sent successfully.