All about subfloors
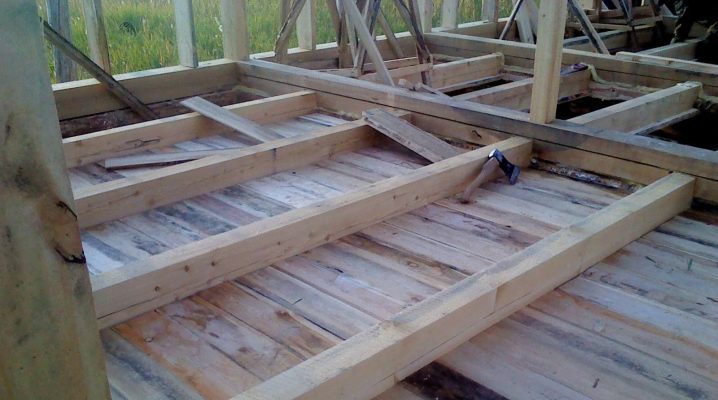
A subfloor is the basis for a quality floor covering. From the material in this article, you will learn what it is, what it happens, how it is mounted on different bases.
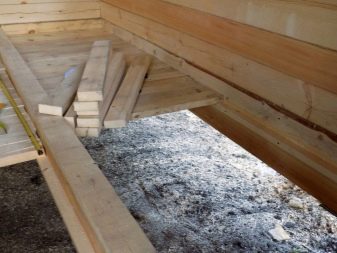
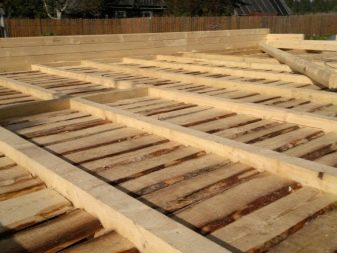
What it is?
Subfloor - a decking with a complex structure, laid on top of floor slabs or beams... It is irreplaceable in the construction of various structures. You can do without it in the case of building a summer house, a guest house, or a technical building.
In other cases, it is the primary leveling base or the base for finishing. It differs in the type of structure, it is made from different building materials.
Different raw materials are used in the production of subfloors, which depends on the type of buildings and the type of structure... Moreover, the design itself performs a number of tasks.
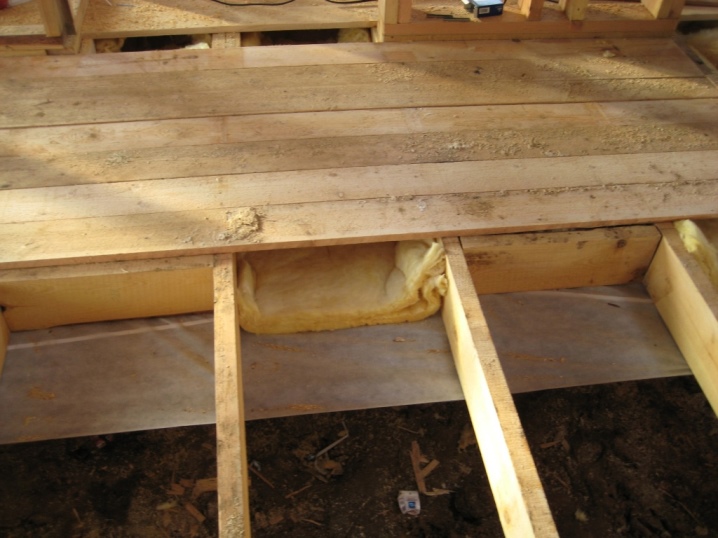
It reduces heat losses, levels the base and increases the load-bearing capacity. The rough pie device consists of base layers that perform specific functions.
- Underlying (lower) layer is needed so that the materials lying on top evenly load the floor. It is carried out in the form of a slab or a prepared ground base.
- The leveling layer is laid immediately after the previous one. Levels existing irregularities in the base as necessary. It can be classic and oblique. In the classical form, it is covered with sand and crushed stone, for this, concrete is also used.
- The intermediate layer is a necessary interlayer... Its only task is to bind the two previous layers of the rough pie.
- Insulating layer performs the functions of moisture insulation, sound insulation, is a heat insulator. Based on the type of material selected, it differs in thickness and density.
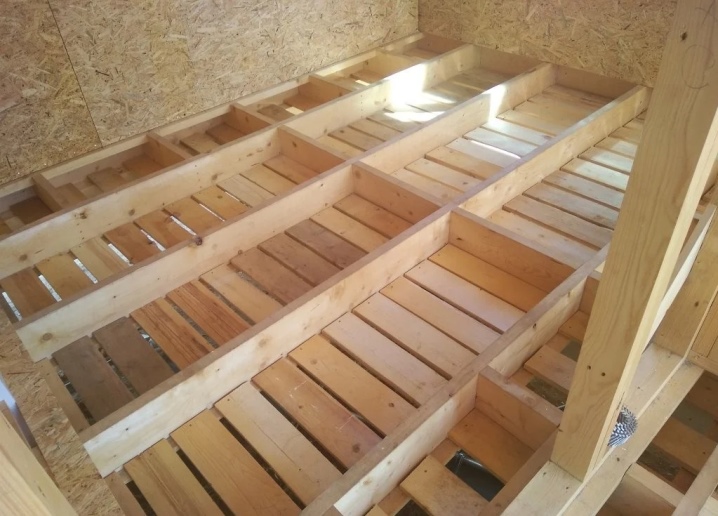
The device of this design is cheaper than a filler screed. In addition to the subfloor, the subfloor can be a cranial board that is flush with the bottom of the beams.
The arrangement technology consists of comprehensive measures to create a solid, reliable base for any material to be laid.
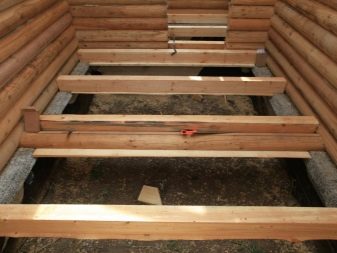
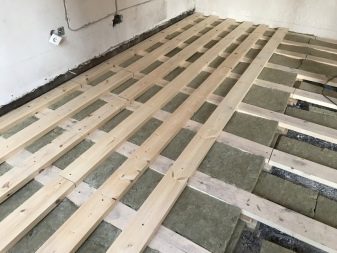
Views
The type of structures differs based on the finish material, load requirements and moisture resistance. In addition to the soil, the foundation is the foundation of the rough pie.
The rough floor is equipped with a strip foundation, logs, beams. The execution technology depends on the nuances of the foundation, the presence of an underground, the microclimate in the future building.
The execution technique is dry and wet. In the first case, they resort to creating a prefabricated dry screed by means of expanded clay or concrete. In addition, they equip adjustable bases with plywood, log, chipboard.
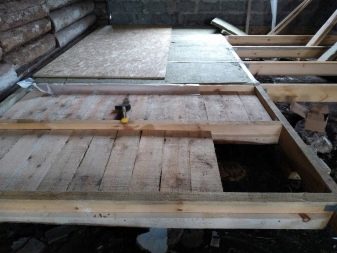
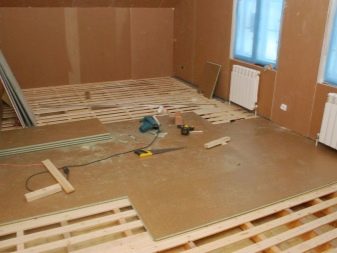
Wet methods of arrangement are to use bulk solutions and screeds. At the same time, screeds, depending on the technology, are single-layer and multi-layer.
The most popular building materials are concrete and timber. Each installation method has its own characteristics.
Concrete
Concrete floors in a brick house are quite even and reliable. They are made by pouring a concrete screed. The working solution is mixed from cement and sand.
The arrangement procedure is short, but the floors dry completely in about 1 month. They gain strength and become especially durable, inert to static and aerodynamic loads.
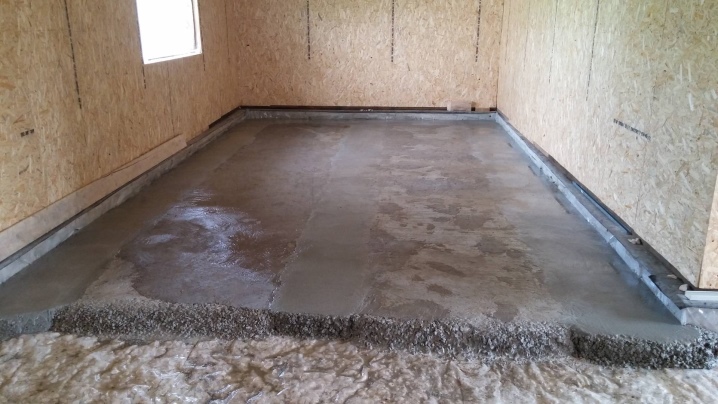
The cost of the work is low, which explains the demand for equipment from most builders when building private houses. Subfloor technology is performed on the ground or slab floors.
The difference between the methods lies in the arrangement of the sand and crushed stone cushion, the type of heat and waterproofing. The height of such a base varies between 5-15 cm.
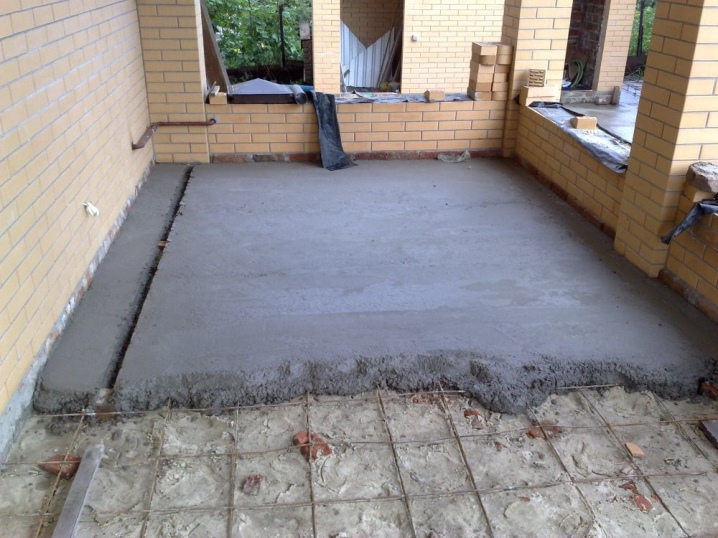
In addition to the concrete solution, crushed stone, reinforcement, wire (for the lattice and the formation of the frame), heat and water insulators are used in the work. The basic set of tools includes a concrete mixer, a shovel, a trowel, as a rule, a building level.
A vibratory rammer is used for compaction, and a needle roller is used to get rid of bubbles. Reinforcing frame structure is needed to strengthen the strength and prevent cracking of the floor.
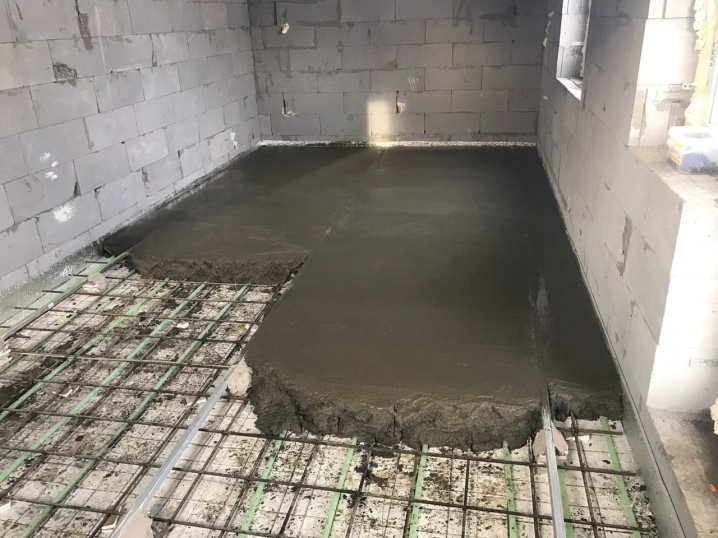
Wood
Rough floor on logs - the best solution for the residential part of the house... With this type of arrangement, the floor is laid on wooden blocks resting on the foundation.
This building material is environmentally friendly, non-toxic, safe. It is durable, has a special texture. Wood planks are the material for the top of the rough pie. Hemming can be done under or on top of beams.
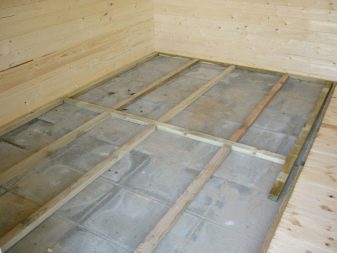
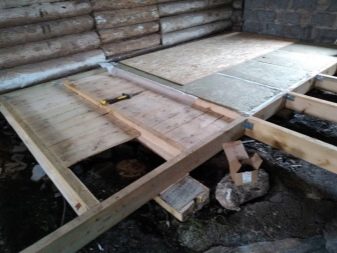
The disadvantage of the first option is the smaller thickness of the insulating layer. The disadvantage of the second is that the height of the lag is greater than the thickness of the insulating membrane.
We use boards treated with fire retardants and antiseptic. The flooring can be made from different raw materials (moisture-resistant plywood, edged boards, particle board, chipboard, OSB boards).
The structure of a handmade pie consists of a bar, a cranial bar, a filing, a waterproofer, a heater, a vapor barrier, and a board.
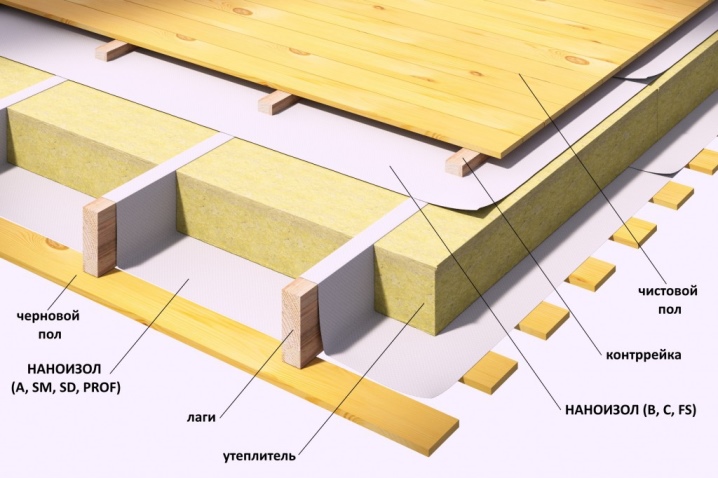
With the modern scheme of laying the rough floor, insulation is provided without counter-lattice... The boards are placed on the edge, a wire net is laid on which the insulation and waterproofing agent will rely.
To eliminate excess moisture, a membrane is used, then stone wool, vapor barrier. The final layer is wooden boards.
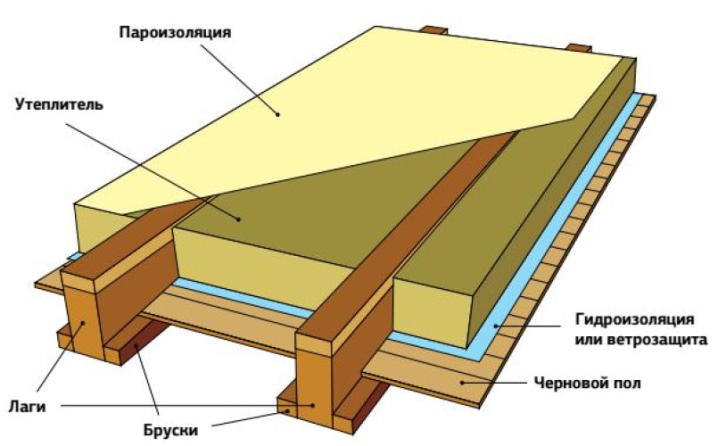
Mounting
When erecting structures, they resort to using different schemes for arranging the subfloor. In an apartment, it can be filling a rough screed, in a private house - installing boards on logs.
Floor finishing technology can be combined. Options for a rough pie in frame structures on screw piles, houses made of aerated concrete, wood depend on various factors.
For example, the subfloor on the second floor (attic, attic, balcony) can serve as the final floor surface. At the same time, insulation is a mandatory stage of installation.
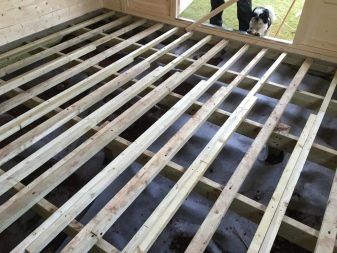
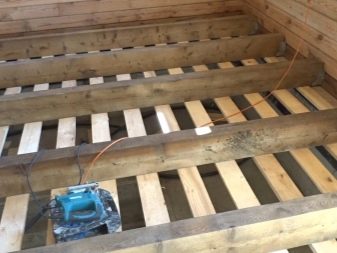
When the overlap of the cold attic is equipped, a vapor barrier is placed on the filing, then a heater, waterproofing, ventilation is provided, and then a subfloor is laid.
On wooden floors
The beams are treated twice with an antiseptic solution. This is done in 2 stages. If the ends are placed on the foundation, a couple of layers of roofing material are laid between the wood and concrete.
The recommended step length is 0.55 m. This width eliminates the need for cutting mineral wool. The beams are fastened with metal clamps.
After installing the beams, check the height level: the top faces must lie in the same plane. You can control the height with a rail or level.
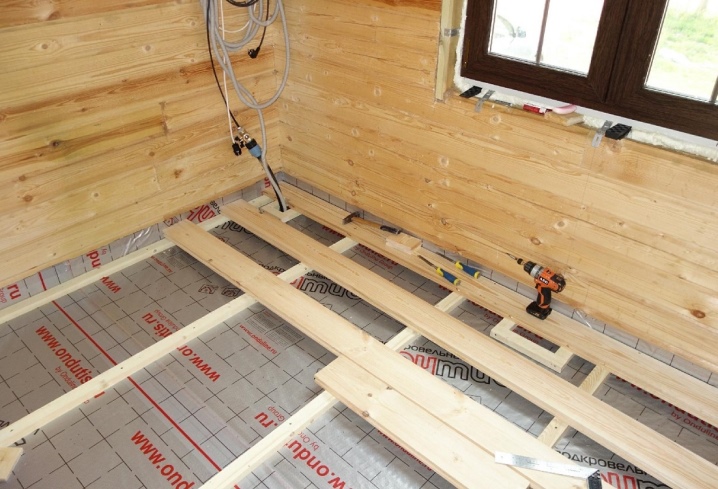
If necessary, you need to level the plane with wedges (preferably made of plastic or metal) or by cutting off excess height. Wooden wedges should not be used to avoid subsidence and squeak.
Next, you need to connect the lags and cranial bars.... They are needed to support plywood or wood boards. The selected building material is cut taking into account the beam spacing.
When cutting sheet material, the width of the blanks is reduced by 1-2 cm. A perfect fit is not needed, since all the voids are subsequently filled with polyurethane foam.
The prepared frame is laid with a vapor barrier. As it, you can choose a rolled membrane or ordinary plastic wrap. The material should not have cuts or holes.
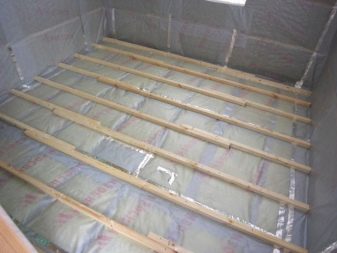
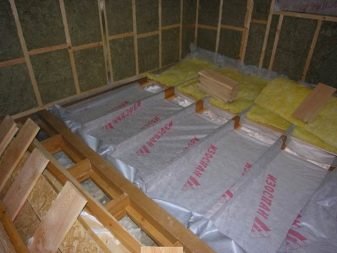
When choosing a film, they try to take dense polyethylene. It or the membrane is fixed with a stapler, after which all joints are closed with construction tape.
Then mineral wool is laid on the base.... If the interval between the lags is less than its width, the material is tamped along the edges. After it fills the base, a second layer is laid.
Wherein the flooring is shifted by 1/3 of the sheet. The thickness of the insulating material should be selected taking into account the climatic characteristics of a particular region. For middle latitudes, 10 cm is enough, for northern latitudes - 15 cm.
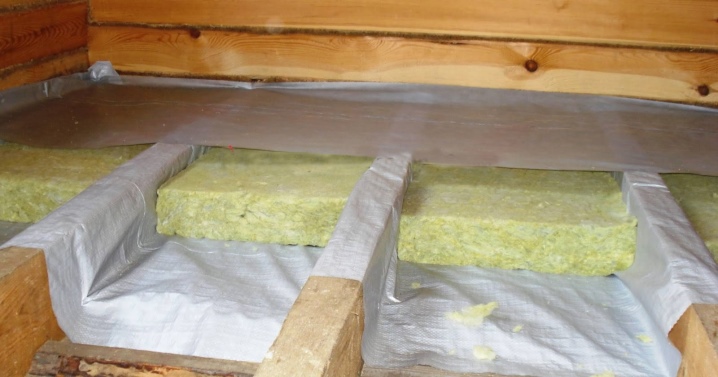
After the insulation, a waterproofing layer is laid. In the places of the beams, it is fastened with a stapler, the joining edges are connected with tape.
Then it is necessary to fill wooden slats with a thickness of 2-3 cm. They will contribute to the ventilation of the finished floor, and will become a prophylaxis against mold.
At this stage, the arrangement of the warm floor is almost ready. It remains only to lay sheet material or boards that serve as a base for linoleum or carpet.
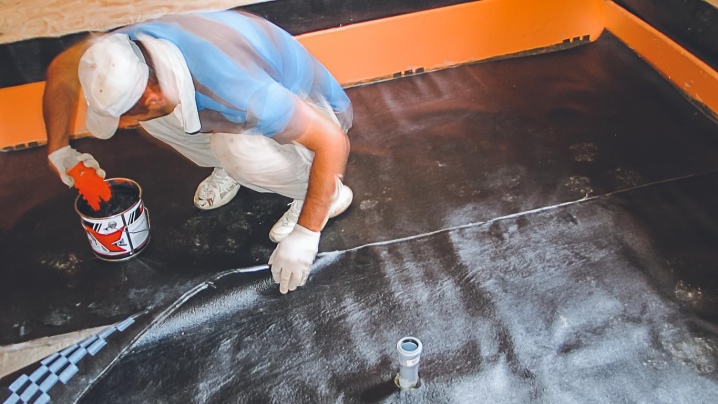
On concrete
In a private house, a concrete screed is especially relevant if there is a high probability of high humidity. Arrangement of the subfloor begins with the removal of the old topcoat. Existing cracks, potholes and other defects are removed, the surface is removed from dust and primed.
When it dries, a prepared cement mortar with a thickness of no more than 4-5 cm is poured onto the base. To make the base even, it is leveled using the rule.
When the screed is completely dry, a hydro and vapor barrier is laid on it. Finishing material (linoleum, carpet, laminate) is laid on top of these materials.
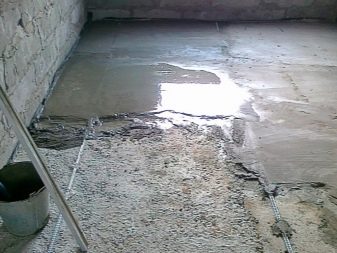
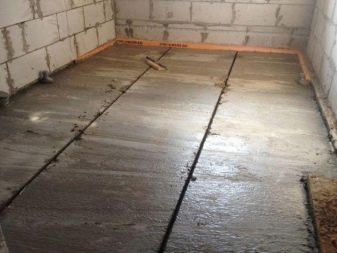
When the logs are planned to be placed on a concrete screed, work begins with the preparation of the base. It is cleaned of dust, covered with a deep penetration primer.
After drying, waterproofing is laid on the base and all joints are tightly connected. The logs are leveled, fixed on the beams at the opposite walls. In the future, other bars are laid with subsequent fixation.
If necessary, soundproofing material is placed under the logs. The work uses a bar with a length equal to the parameters of the room.
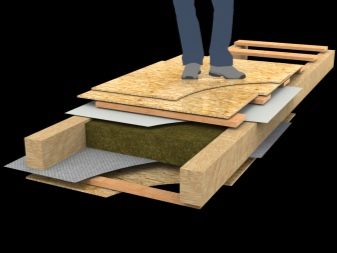
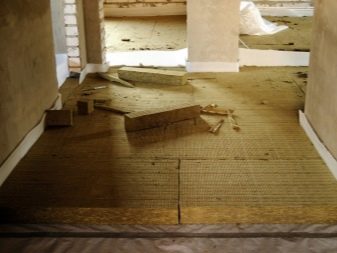
After laying the lags on the base and checking the horizontal position, they are fixed. After that, the insulation is laid the same as when arranging the subfloor on the ground.
A moisture-resistant plywood or floorboard is laid on top of the log. The arrangement of the sheets should be staggered. They are pruned if necessary. Do not join the flooring in one line.
The subfloor must not rest against the walls. The minimum clearance is 3 mm. A fine finish is laid on top of it. It can be parquet, ceramic or vinyl tiles, linoleum.
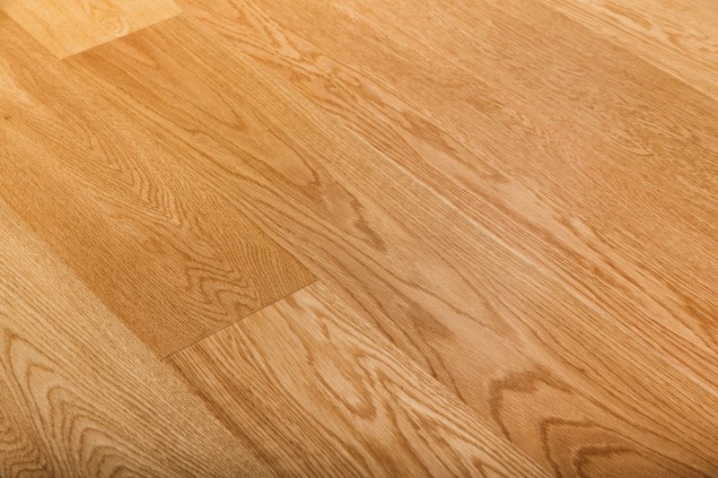
On the ground
When arranging a subfloor on sand, concrete of the M 300 and higher grade is used. The relevance of higher classes of building materials is explained by the increased load. They are resorted to in case of unsatisfactory soil.
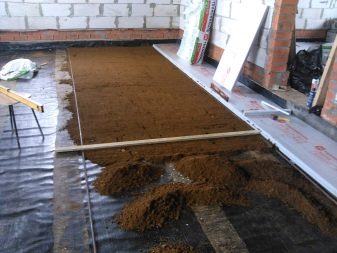
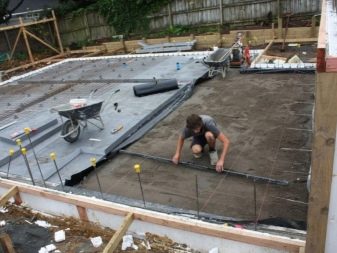
The technology is produced with the creation of a reinforcing grid. The durable and reliable sub-base has a multi-layer construction, consisting of:
- dense base;
- sand and gravel mixture;
- concrete screed;
- vapor barrier membranes;
- insulating material;
- film polyethylene;
- reinforcing concrete layer.
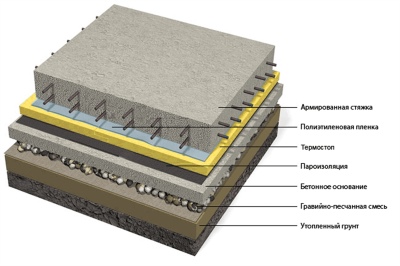
A step-by-step instruction consists of a series of sequential steps. Initially, the zero point is determined for an objective assessment of the amount of soil work.
The soil is then tamped well to minimize soil subsidence and cracking of the concrete. After that, a sand cushion is poured onto the base, adding the shrinkage thickness to the required height.
The layer is moistened, rammed with a vibrating machine to the planned height. A gravel (expanded clay) layer is poured over it. Next, the foundation of the draft layer is carried out.
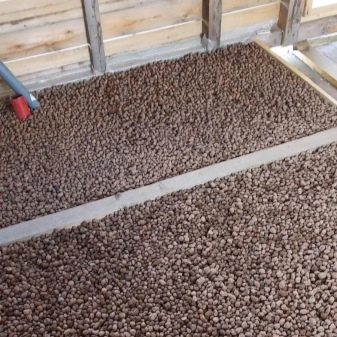
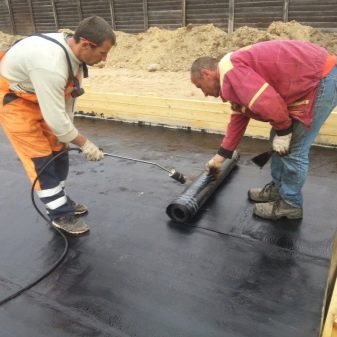
The thickness of the first screed is 4-5 cm. The height difference should not be more than 0.4 cm.
The next step is the wiring of the waterproofer. In addition to the membrane, roll bitumen or dense polyethylene film is suitable from polymer.
A wide material is laid without joining, a narrow one is laid with an overlap.The joints are sealed with construction tape. The material used must not have holes.
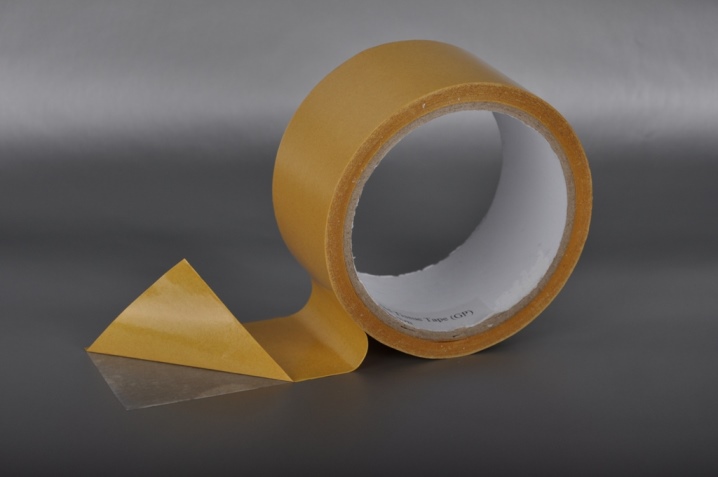
The margin should be 15-20 cm on each side. These allowances are placed on the walls. The excess is cut off after the second screed has been laid. In some cases, the waterproofing is installed directly in front of it.
The waterproofing layer is covered with fiberglass, polyester or PVC insulation. The work uses extrusive polystyrene foam, polystyrene of the PSB50 and PSB35 brands, mineral wool.
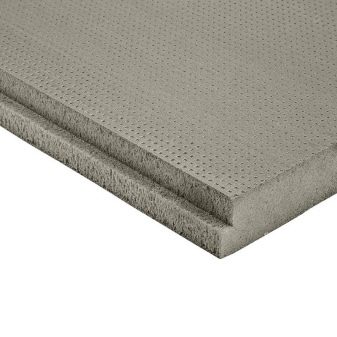
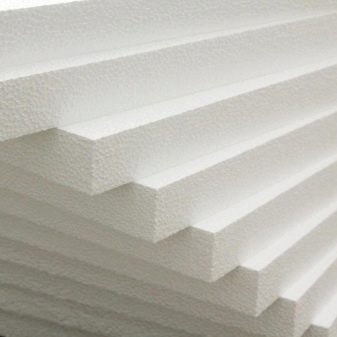
When choosing foam, it is sheathed with polyethylene from 2 sides. Mineral wool is also insulated with a film so that it does not absorb moisture from the cement layer.
Useful Tips
Starting the arrangement of the subfloor, the calculation of the maximum permissible load is performed. When the coating is laid on logs, taking into account the safety factor is especially important.
Based on the purpose and operating conditions of the room, the thickness of the beams and the step between them are selected. Standard material is a bar with a section of 150x50 mm.
If lumber with a flat surface is chosen, the floor is fixed from below, from above, from the side. When rounded beams are used in the work, the fixation is lower or upper.
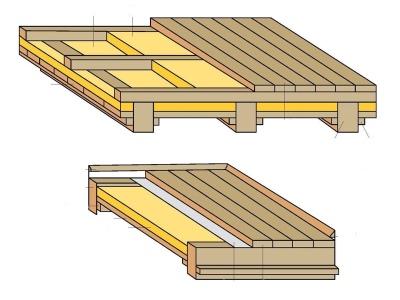
In order for the flooring to meet expectations, it is necessary to initially take into account the purpose of the room, the type of finish. This will determine not only the spacing between the beams, but also their thickness and width.
To simplify your work, it is better to equip the sub floor using plywood or OSB boards. The technology is simple and allows you to prepare the floor base for further finishing in a short time.
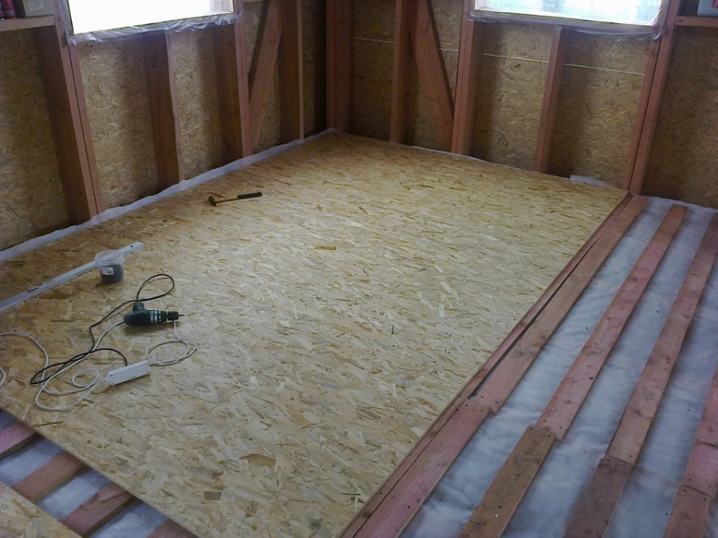
To avoid common mistakes, it is worth considering a few nuances.
- Buy exclusively moisture resistant sheet material.
- Docking of building materials is performed strictly along the lags.
- Sheets are laid with a small gap, retreating from the walls too.
- The voids in the future must be filled with foam.
- The length of the self-tapping screws should be 1.5 times the height of the plates.
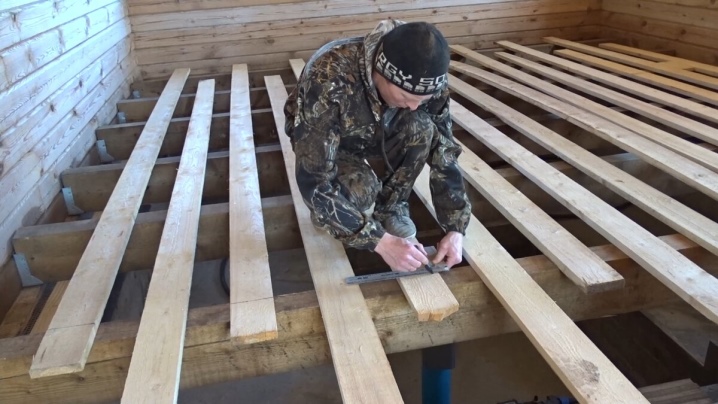
It is impossible to save on building materials, otherwise the quality of work and the reliability of the floor will suffer. In the absence of repair skills, it is better to entrust the work to professionals.
You cannot simplify the technologies developed over the years on your own. An unprofessional approach to the construction of the subfloor will jeopardize the entire construction.
The boards must be dry. Installation should be done in good weather. Due to waterlogging, there is a risk of loss of the load-bearing characteristics of the wood. Along with drying, it will decrease in size.
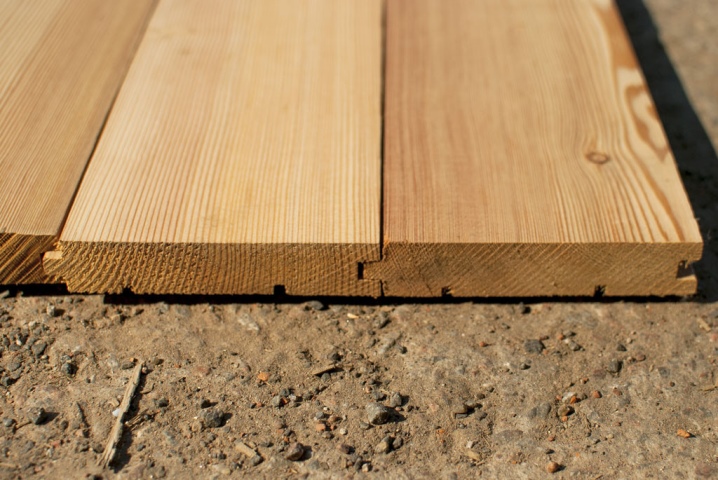
When arranging the subfloor between 2 floors, the cranial bars are stuffed along the length of the beams. If they are stuffed across, the height of the walls will decrease.
When laying steam and waterproofing, carefully read the instructions for a specific material. Steam comes out in the 1st direction, if you choose it incorrectly, moisture and dampness cannot be avoided.
A vapor barrier consisting of small pieces must not be installed. An attempt to save money will have negative consequences. To minimize wet evaporation, the soil under the floor is covered with roofing material.
A warm rough pie is arranged on the 1st floors of low-rise buildings. If the room on the top floor is unheated, you shouldn't spend money on expensive repairs.
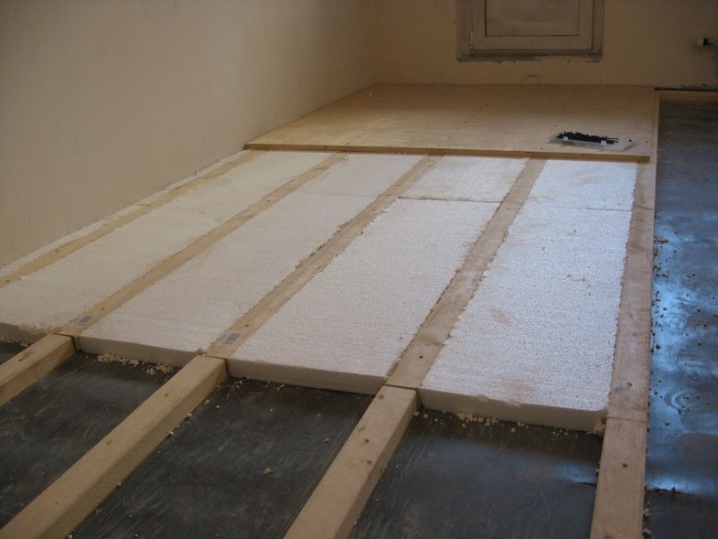
The comment was sent successfully.