What is slag cement used for and how to make a mortar?
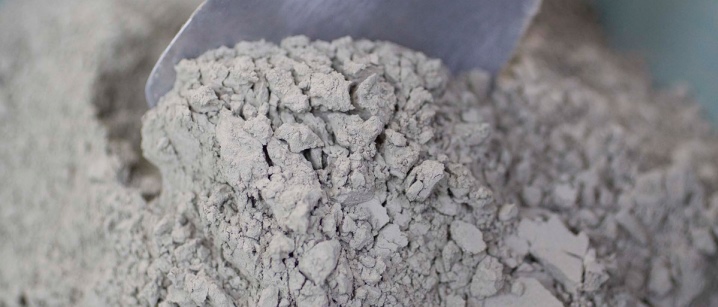
Slag cement is an artificially obtained hydraulic substance with a pronounced astringent effect. It is somewhat analogous to Portland cement. Its main feature is that it contains finely ground metal industry waste, namely slag.
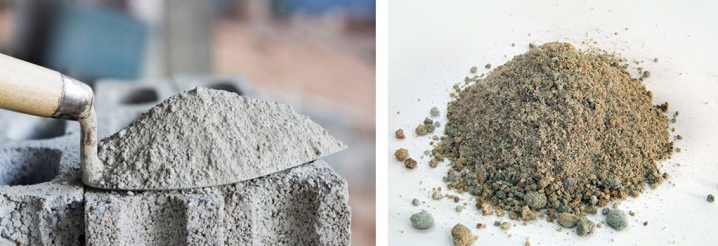
What is it and how is it produced
Granulated blast-furnace slag is obtained as a waste in the process of smelting ferrous metal. It has inherent properties that apply to general construction Portland cement, but there are differences. In the form of a finely ground product, it is active in the manifestation of astringent properties, interacting with water, and also with hydration products of clinker-type minerals (those that are part of simple Portland cement).
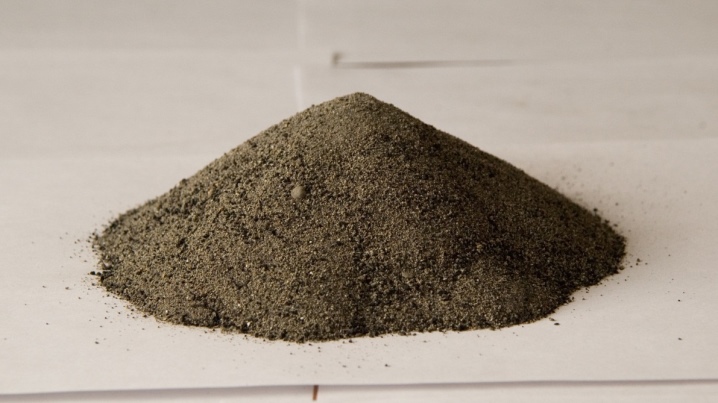
Slag cement components are:
- clinker - it contains no more than 6% magnesium;
- slag - up to 80%, the optimal amount of this component depends on what requirements are put forward for the binder product;
- gypsum - both natural pure and with a content of phosphorus, fluorine and boron, no more than 5% of gypsum should account for the entire mass.
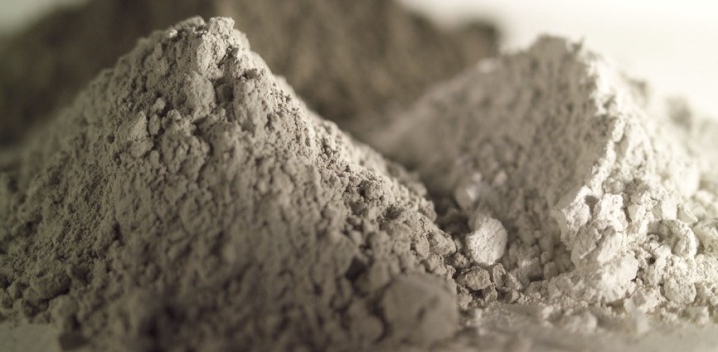
Cement with slag is considered a binder, the use of which is not limited to any one direction. The question why, in principle, slag is added to cement, can be answered as follows: a concrete solution, including cement and slag, has a low cost. And if we compare the price of a concrete solution based on standard Portland cement with cement with slag, the second will be financially more profitable. That is, it is not better in principle, but more profitable with almost equal characteristics.
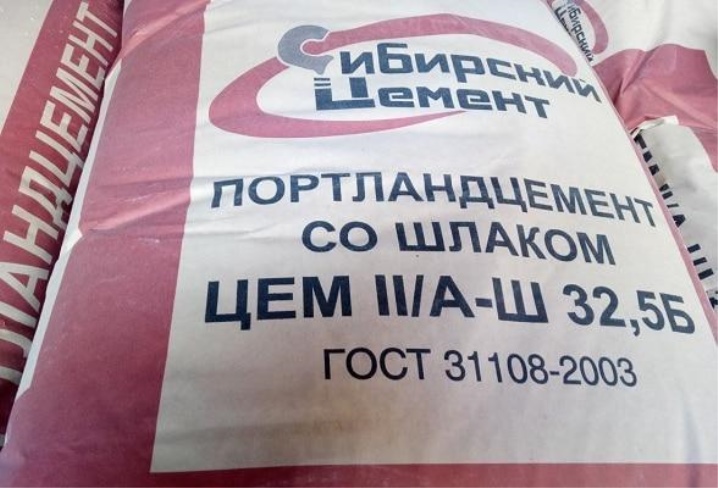
By the way, about the characteristics. The mixture of slag and cement is also good because the temperature of heat release in it will be relatively low.
And also this product:
- has increased resistance to the influence of waters (sulphate and fresh);
- characterized by increased heat resistance;
- has high frost resistance (with the condition of using the precast concrete steaming technology).
In general, the conclusion is that the standard business case decides in the choice of materials.
The cost price of the described product does not include the significant costs of extraction, grinding and processing.
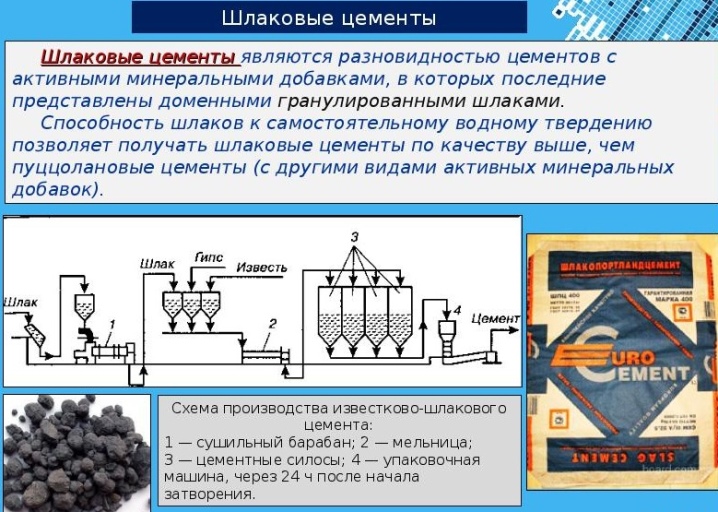
The material is obtained from Portland cement clinker, slag, clay and limestone. The fact is that in the production of cement it is the chemical composition of the material that is important, and not its physical structure. Therefore, you have to choose the source with great care. When producing this cement, both basic and acidic blast-furnace slag can be used.
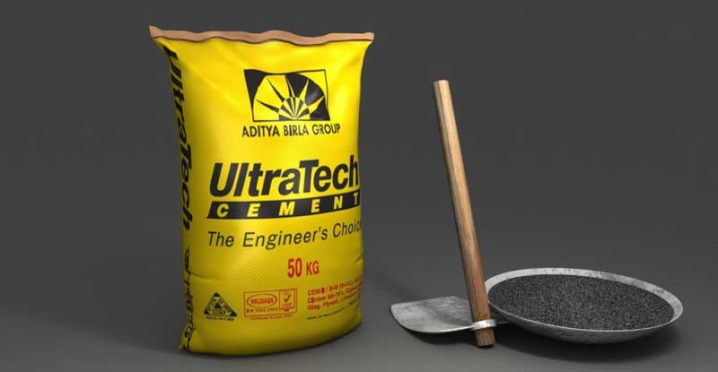
By the way, the slags themselves can be granular and non-granular, but nevertheless the former are used much more often, and the point is, again, in the economic component.
But there is another reason for using granular slag: the very process of producing the final product with non-granular slag becomes significantly more complicated. But those slags that are added to the product after firing are granulated without fail.
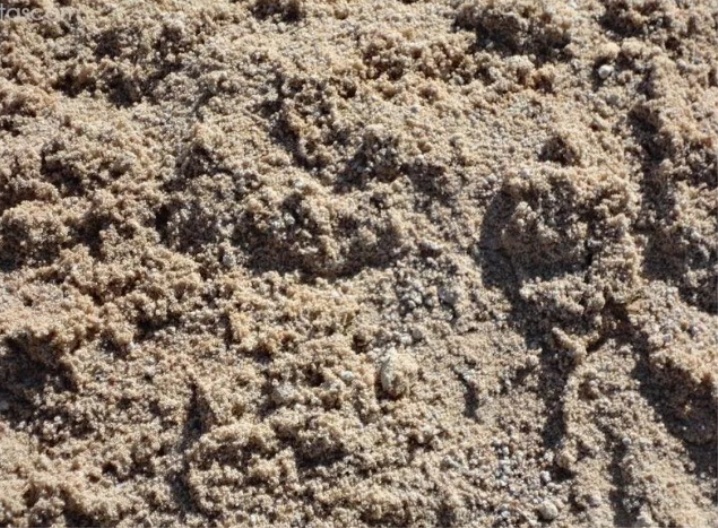
Attention! The percentage of slag in the cement should not exceed 60.
As practice has shown, cement in fusion with slag means obtaining a material that is strong, rather reliable, not very durable, but quite convincing for many purposes. That is why this product is so actively used in multi-storey construction.With its help, slabs and armored belts are made, structures underwater and near-water structures, it also helps in thermal insulation, when casting some products in construction. That is, completely different construction goals can be achieved using this product: with high efficiency, economic feasibility and great opportunities.
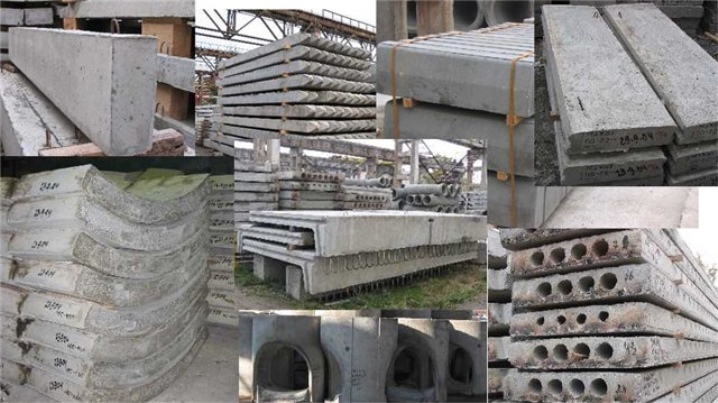
Species overview
ShPC (slag portland cement) is divided into two main types - normal-hardening and fast-hardening.
Normally hardening
Material properties are described in GOST 10178-85. The material differs in that the more slag in it, the longer the mixture will harden. The less heat will be produced by the hydration reaction.
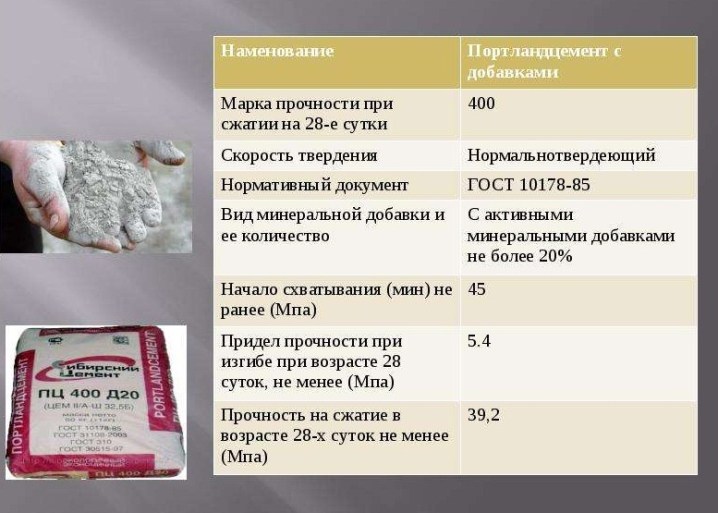
After solidification, the slag should not react with water, which is why the mixture is often used to create structures with high humidity.
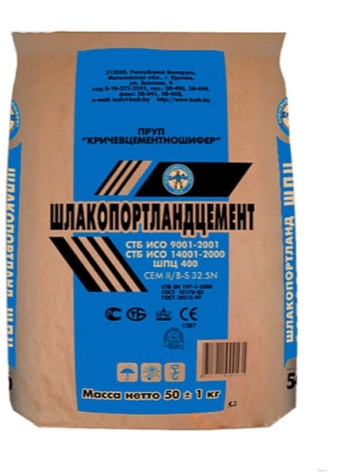
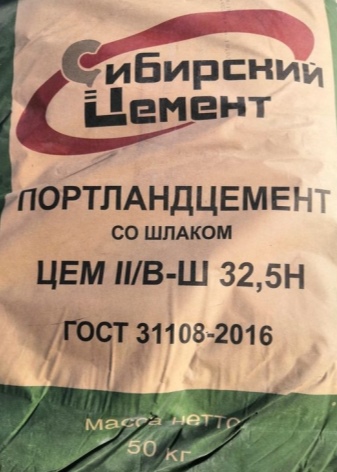
Fast hardening
Special additives are added to this material to help speed up the process. Additives can be of mineral etiology and volcanic, that is, ash or pumice.
It is worth remembering that the shelf life of slag cement is lower than that of a simple dry cement mortar.
From the time of shipment of the product, no more than 45 days should elapse before the material is used. But using an expired product means taking a lot of risk. It loses its performance properties, and significantly.
The question often arises whether the differences between Portland cement and slag Portland cement are significant. Yes, they are significant, if only by the fact that the first will cost significantly more than the second. And also Portland cement acquires finishing strength faster than SHPC (it hardens completely after 3 weeks). In principle, there is no slag in Portland cement, there is clinker and mineral composition with additives-accelerators. But the density of the SPC is lower than that of Portland cement, as well as its weight will also be lower - more precisely, the weight of the structures made of it.
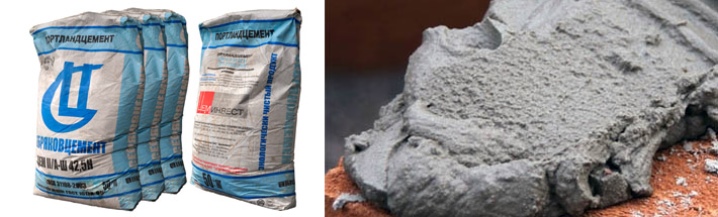
What is it suitable for
This material is especially in demand if it is necessary to build concrete, as well as reinforced concrete structures that will constantly be in contact with the aquatic environment (for example, the ShPC M400 contains at least 21% of granular material). The product has sufficient strength properties for this. It is taken to make high-quality concrete mortar, to make wall panels and produce dry mixes. This type of cement does not lose to the same M500 brand in fact in anything, but this brand is a classic cement.
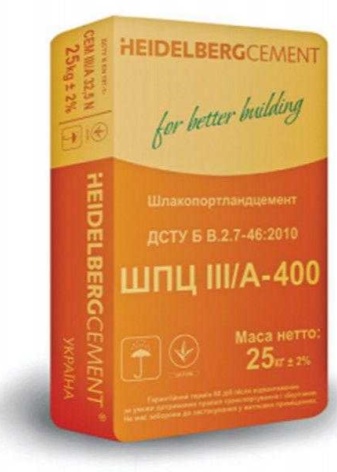
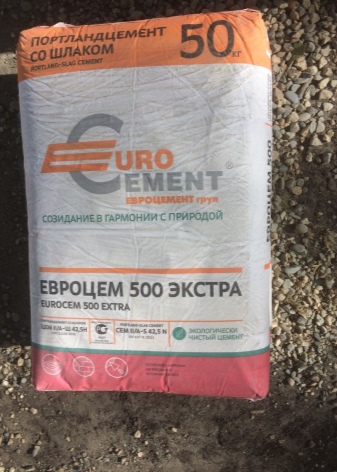
Yet again, the construction of walls and ceilings using reinforcement - cement with the addition of slag has succeeded here as well. It is actively used on large-scale construction sites, and its lightness helps it in this (when compared with silicate and ceramics, SPTs, of course, is not a fluff, but it wins significantly).
Why is weight so important: the matter is in the load on the parts of the foundation and structural parts of the structure - it will be reduced.
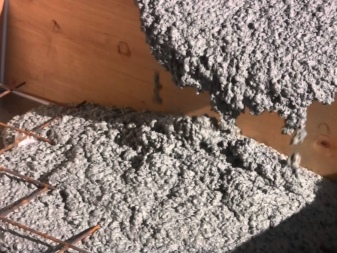
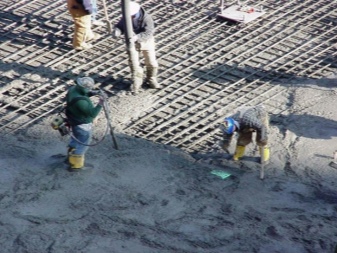
The builder has the ability to make slabs of impressive dimensions using cement with slags - installation time is saved, as well as money. And the transportation of SPTs-panels usually does not cause problems.
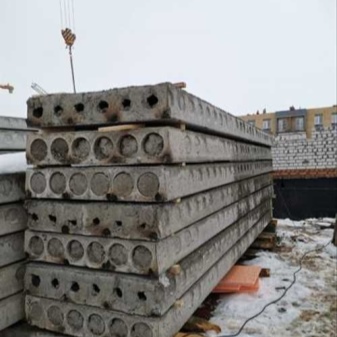

Where the material is used - areas of application:
- construction of monolithic and prefabricated elements (meaning both private construction and industrial);
- manufacturing of structures that require the fastest possible hardening of the base;
- paving roads with fast setting of the mixture;
- construction of flyovers and bridges;
- production of paving slabs and paving stones;
- low-rise construction with its different stages - from filling the walls to working with the foundation;
- replacement of mortar for plaster and masonry.
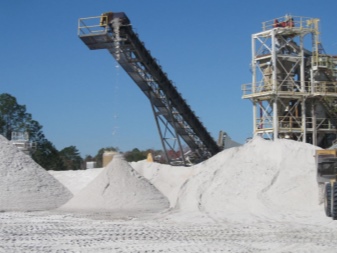
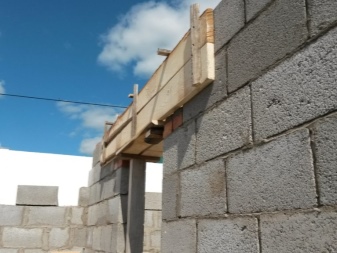
The material is actively used in the manufacture of reinforced belts, which are also often found in multi-storey construction. The material works great in combination with conventional heaters as a means of thermal insulation.Class 50 is considered the best choice for reinforcement, class 35 is for the construction of load-bearing elements, class 25 is more than suitable for not the most important, small structures, class 10 is used in thermal insulation.
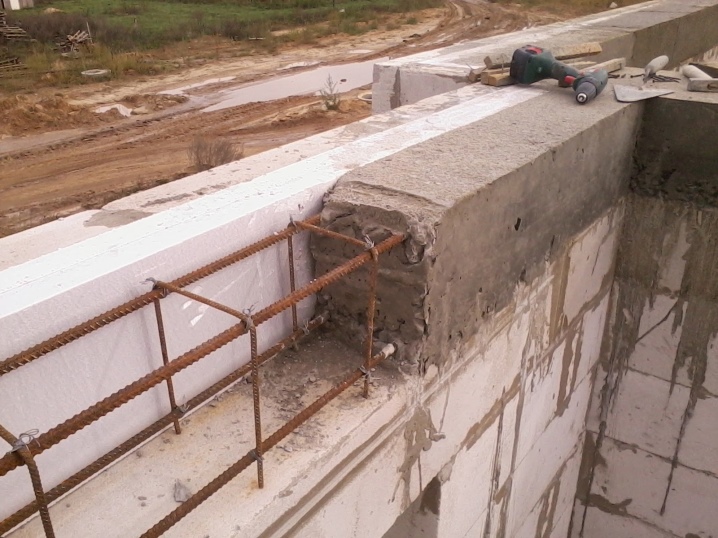
Application proportions
If it is decided to finish internal surfaces with this product, preference should be given to coarse-grained slag. It will be required for a solution of about 6 parts. The remaining 4 parts will fall on fine-grained granular slag. But in this case, any cement is used for concrete.
To finish the external facade, it is necessary to dilute the solution in different proportions: use 7 parts of coarse-grained slag for 3 parts of fine-grained slag.
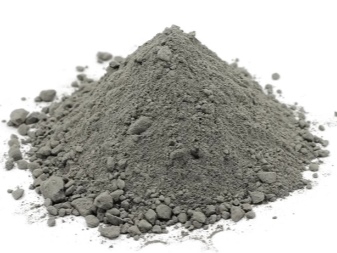
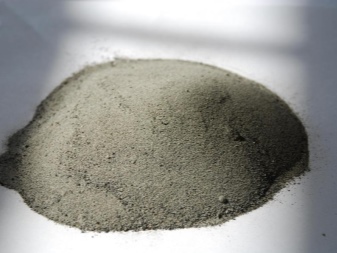
Cement must be taken of high quality with high resistance to external influences.
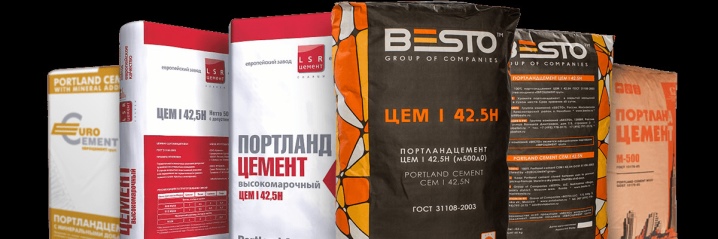
For effective pouring, as well as in the event that the time reserve does not run out, you can take non-granulated slag. Of course, the solidification of such a mixture will be slow, but the quality of the coating outperforms the mixture with a granular composition. Cracks do not form quickly on such a surface, but on a floor filled with granulated slag, they may appear in a couple of years.
To finish the outer part of the protruding foundation, granular slag is also required. The larger the surface has to be finished, the larger the granules should be in the slag - this is the ratio. Feedback also works.
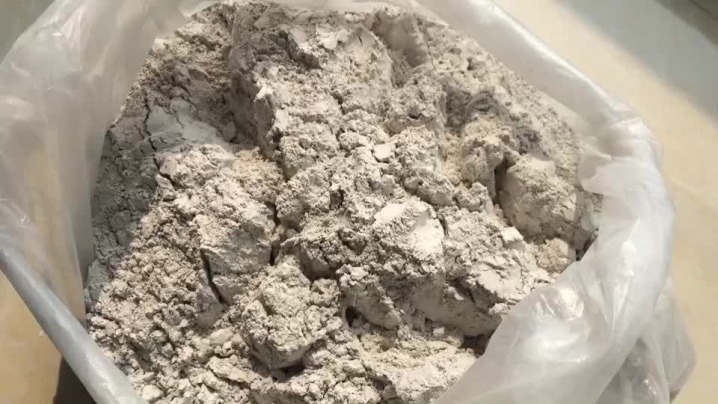
How to make slag concrete yourself:
- a few hours before work, the slag should be moistened with water - this affects the durability of the concrete, which is formed in the course of subsequent actions;
- the components are mixed in the ratio indicated above (choose the right one according to the goal), everything is thoroughly mixed;
- after adding water to the composition, it must be kneaded again in order to obtain a homogeneous state of the mixture;
- to get an average grade of concrete, 4 parts of slag (less often 5) and 2 parts of cement to 2 parts of sand are used;
- it is imperative to use the finished product correctly, this must be done within an hour and a half;
- if it is necessary to reduce the cost of the solution even more, then cement can be combined with lime in proportions of 3 to 1.
The proportions are indicated on the package with the mixture.
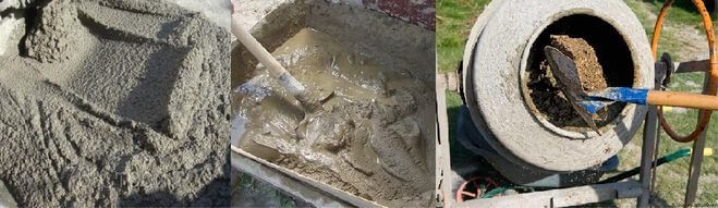
The material obviously has many advantages, especially for those construction work where economy prevails. But it also has disadvantages, which in some situations may outweigh the advantages. For example, cement with slag shows some "capriciousness" at thermal drops. And although it is considered frost-resistant, it cannot be used for a long time in conditions of low temperature. Finally, the material prescribes careful maintenance of the structure in case of heat: it will have to be regularly moistened and covered with polyethylene.
So far, concrete mixtures and construction locks with SHPC are not used very actively, and they are often made in factory conditions, and in construction they are used under the supervision of experienced specialists. But nevertheless, the product cannot be called a very rare material either. Probably, modernization in the production of this hydraulic binder should be expected.
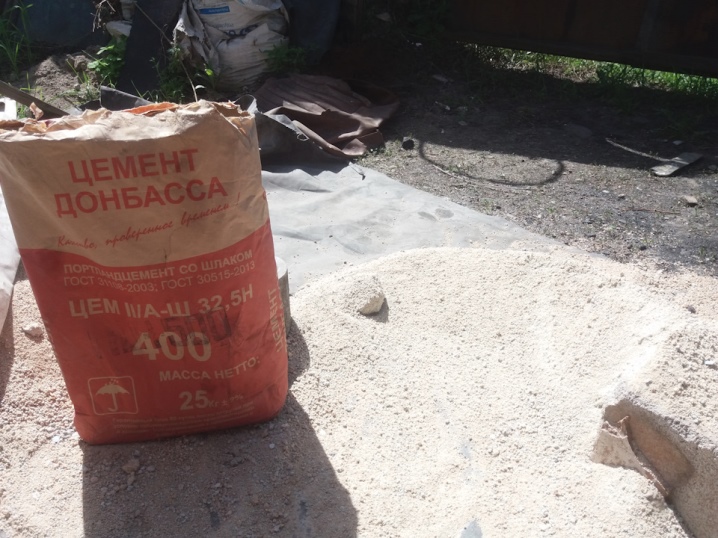
A detailed overview of the use of slag cement in the next video.
The comment was sent successfully.