Features of the use of cement-sand mortars

Cement-sand mortars are rightfully recognized as one of the most popular and demanded compositions for construction and repair. They are very often used in various works, and it can be not only residential, but also industrial premises. Such solutions are considered easy to use, so they can be safely purchased even by inexperienced home craftsmen. Today we will take a closer look at the features of the use of cement-sand mixtures.
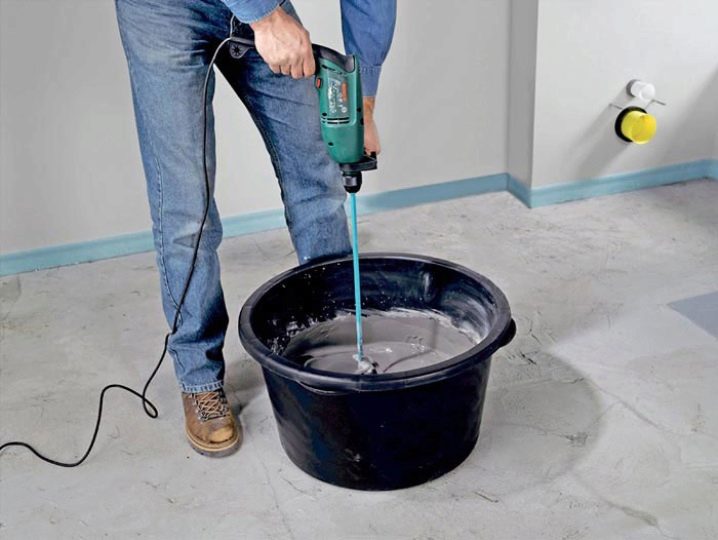
Peculiarities
High-quality cement-sand mixtures are unlikely to ever lose their popularity. Such compositions are distinguished by increased reliability and durability, which determines their relevance and relevance.
A cement-sand mixture is a special product that has a special composition of components combined in the correct ratio. Each element corresponds to certain parameters.
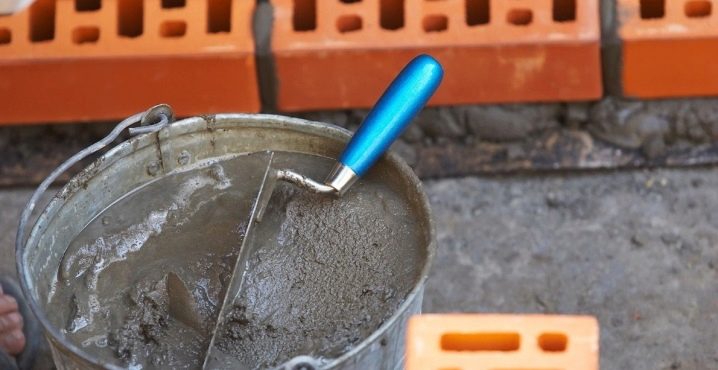
It is not so difficult to guess what such compositions are - it is enough to pay attention to their name. The composition of such mixtures contains fractional sand and cement. Often, these components are supplemented with various additives with different effects. The choice of a suitable solution depends on the purpose of its use.
Another feature of such solutions is that they cannot be used on their own. As a rule, they play the role of the main component in various mixtures. Using a high-quality composition, you can achieve the highest quality and aesthetic result of the work.
In addition, cement-sand mixtures are distinguished by the fact that they can be used both for indoor and outdoor work. They are also used in the manufacture of reliable reinforced concrete walls for various reservoirs and waste.
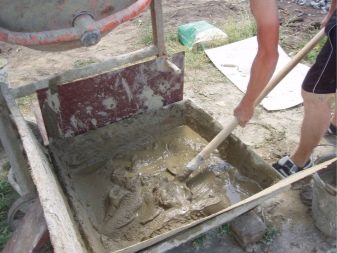
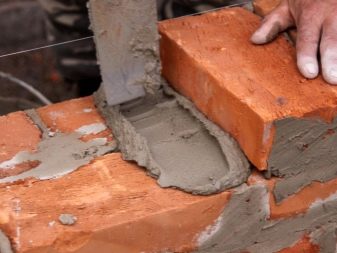
Cement-based mortars have their strengths and weaknesses. First, you should familiarize yourself with the advantages of such formulations:
- In stores, you can find many options for cement-sand mixtures, which include additional components. Such elements make the formulations better and more reliable.
- A quality mixture with a suitable composition will not suffer from temperature extremes or frost.
- The choice of such mixtures is very large. Modern consumers can choose the most easy-to-use composition for which it is not necessary to accurately calculate the amount of all components. It is enough to pour the ready-made mixtures with water and mix well.
- Such mixtures are reliable and durable. That is why they are used in the decoration of building facades.
- Cement-sand compositions are not afraid of high levels of moisture.
- Such materials boast a long service life. Even being on the facade of a building, they can last at least 15 years.
- Cement-sand mixtures have increased adhesion to a wide variety of substrates. They can be safely used in the design of concrete, brick, stone and block surfaces.
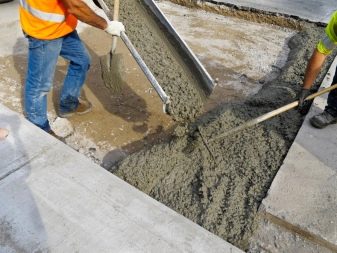
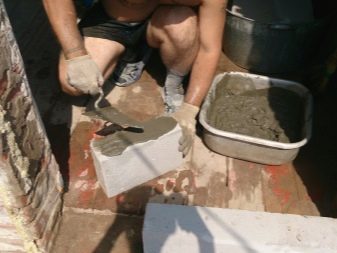
There are no ideal building and finishing materials. Cement-sand mortars are no exception. They have several minor disadvantages:
- Ready-made mixtures are more expensive than the individual components that are in their composition.
- If you have prepared a solution, then you cannot store it for a long time.It is necessary to dilute the composition in exactly the amount that you need to carry out certain works.
- Self-preparation of the mixture, of course, is cheaper, but more laborious. In addition, you will need to be careful about the proportions of the necessary components in order for the solution to be of high quality and effective.
- In most cases, such compounds do not adhere well to wood or painted substrates.
- It is also not recommended to apply a cement-sand mixture to gypsum. Too dense and heavy layer can damage such a base or even tear it off.
- Heavier and more viscous formulations are very difficult to work with. They are difficult to level.
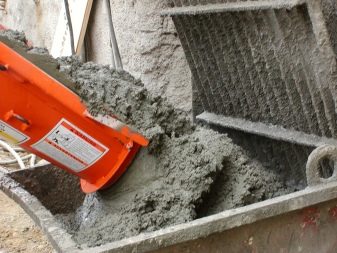
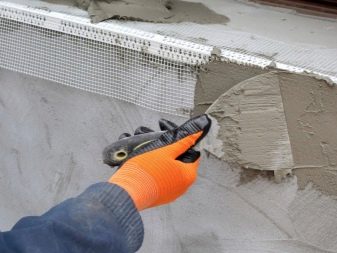
As you can see, there are no serious disadvantages of cement-sand mortars. To avoid many problems, it is quite enough to competently treat the process of mixing the solution. Then it will turn out to be of high quality and it will be easy to work with it.
Specifications
Let us consider in detail what technical characteristics modern cement-sand mixtures have in accordance with GOST.
Density
The thermal conductivity and strength of the cement-sand layer largely depend on the level of its density. In pure form (without additional components), such solutions are rather heavy. They are distinguished by high density, amounting to 1600-1800 kg / m3 in solid state.
Cement-sand coatings are usually quite durable. High density layers are ideal not only for interior and exterior finishing, but also in the formation of a floor screed.
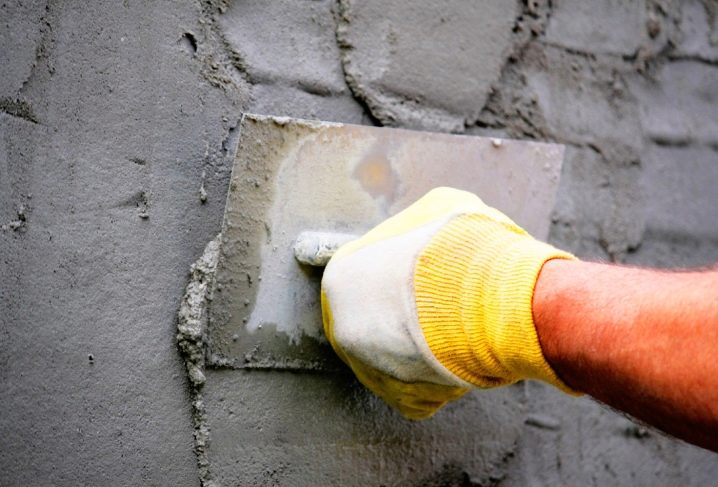
Heat conduction properties
Due to the high density, the thermal conductivity of such finishing materials is very high. In a room with such a design, a comfortable temperature and sufficient warmth will always be maintained. A similar effect cannot be achieved with a lighter gypsum with a porous structure.
The thermal conductivity coefficient of cement-sand mixtures is 0.3 W. If we are talking about non-shrinking plaster with a similar base, then its heat-conducting level is most often 0.9 W.
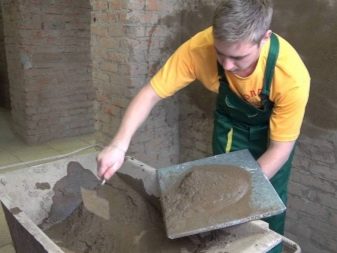
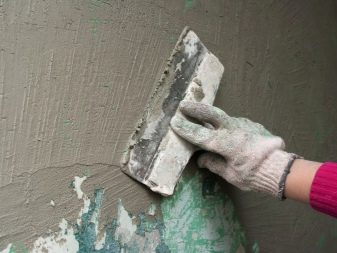
Vapor permeability
This characteristic is very important for any finishing material. Without it, condensation and excessive dampness will accumulate in the room. Over time, this will lead to the formation of mold and mildew.
For cement slurries, the vapor permeability parameter is 0.09 mg / mhPa.
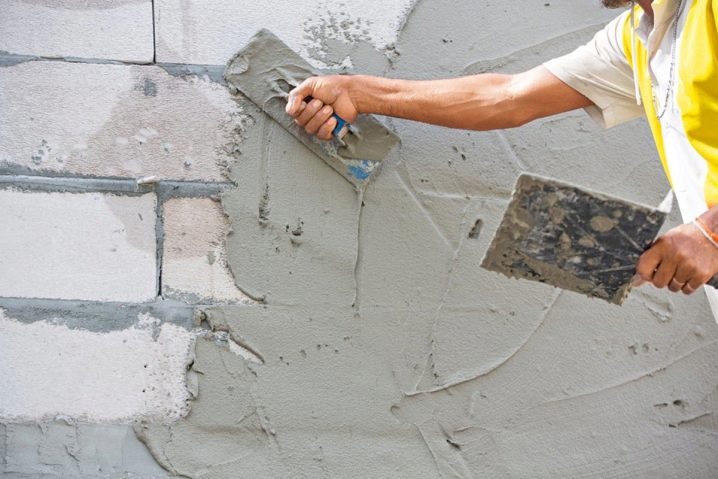
Drying time
The drying time of the cement coating directly depends on the thickness of the layer. So, in conditions of temperatures from +15 to -25, a layer of 2 cm will dry out for 12-14 hours. The thicker the layer of the applied solution, the longer it will harden. Experts recommend not to touch the finished surface for another day after all the work. Of course, this rule is not categorical, but this way you can avoid damage to the freshly applied layer of cement.
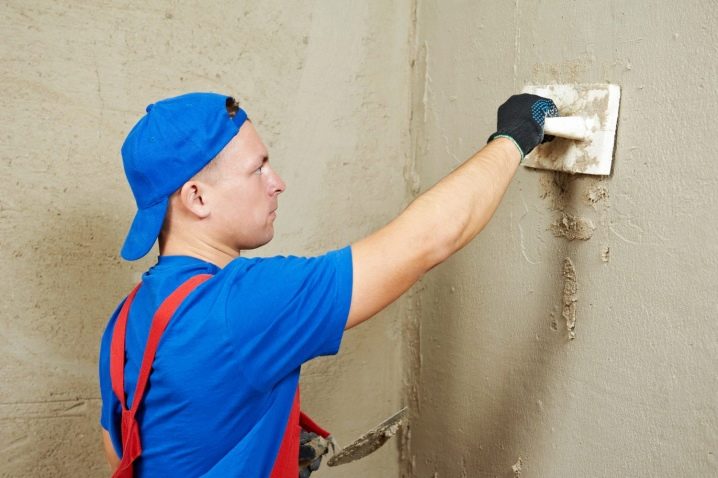
Varieties
There are several types of cement-based mixtures. They are often found in specialized stores, but not every customer knows how they differ from each other.
M100
This composition is used for the manufacture of plastering materials. In such a cement-sand mixture, not only the main components are present, but also lime. Because of it, the proportion of cement is noticeably reduced.
The M1000 is relatively inexpensive. It is used not only in the preparation of high-quality plaster, but also for leveling certain surfaces and eliminating various defects. These can be cracks, noticeable drops, potholes, or ugly crevices.
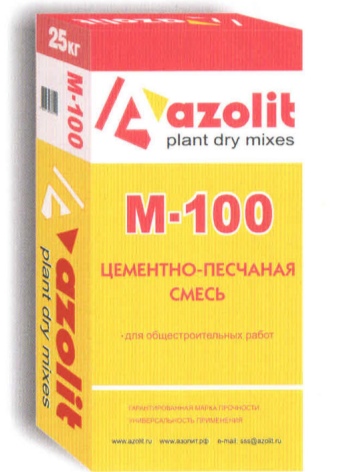
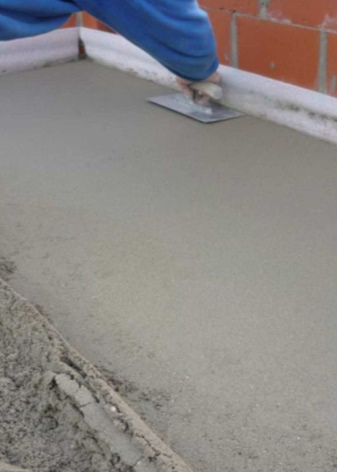
M150
The cement-sand mixture of this brand is referred to as universal. It is used to prepare plaster and masonry compounds.
The mixture with the M150 marking can also be addressed in the case of a reliable screed formation. It is quite often used in various repair work.
Almost any composition can be replaced with a cement-sand mixture in everyday life. The main thing is to determine in advance what properties the solution should have. Often, various components are added to such a product, making it stronger and more durable. It is also worth noting that the M150 cement mixture is distinguished by its democratic cost.
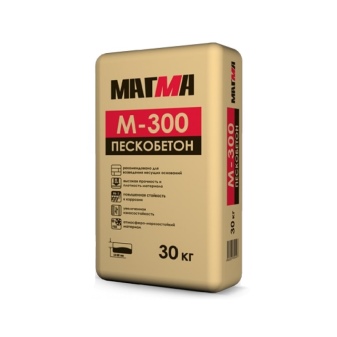
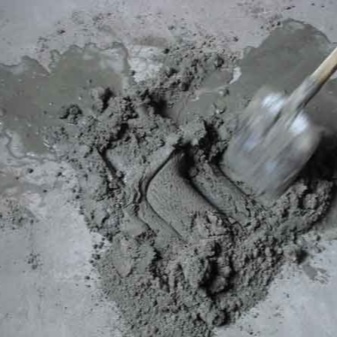
The main characteristics of such a cement-sand mortar include:
- the recommended layer thickness is from 5 to 50 mm;
- consumption per square meter - about 16.5 kg;
- the setting time of the composition is only 2 hours, and it will take 24 hours to fully cure.
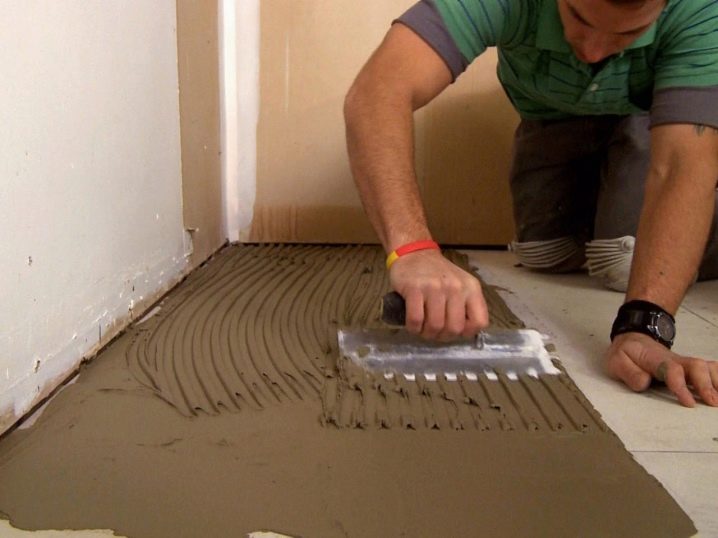
The stores sell ready-made masonry mortars M150. If you are planning to purchase such a mixture, then you need to pay attention to what additional components are present in its composition.
M2000
Such compositions with a cement base are often called assembly and masonry. They are available in different versions.
Each of the varieties of M200 mixtures is designed for one or another application:
- making plaster;
- preparation of masonry mortar;
- making a screed or foundation.
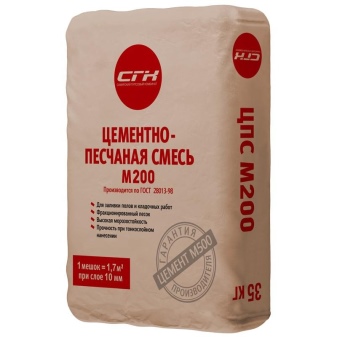
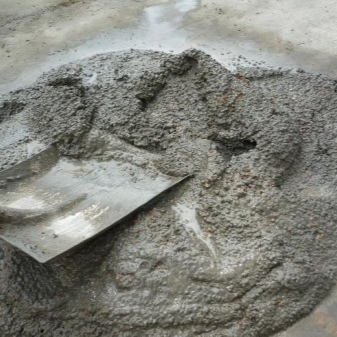
The layer of such a cement-sand mixture is quite dense and reliable. The approximate consumption of such a composition is 7.5-8.5 kg per sq. m (with a layer thickness of 5 mm).
M300
In everyday life, such popular mixtures are called sand concrete or foundation composition. Such products are more expensive than all of those listed, and the scope of their use is not as wide as, for example, those with the M150 marking.
Compositions M300 are used in cases where the work requires a mixture of increased strength. Experts recommend purchasing such solutions when installing large mounting structures or massive screeds. But as for the preparation of plasters, this mixture is absolutely not suitable here.
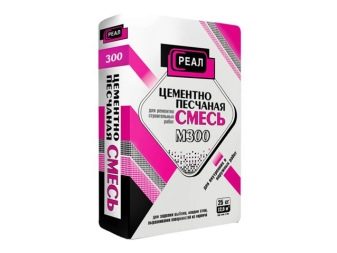
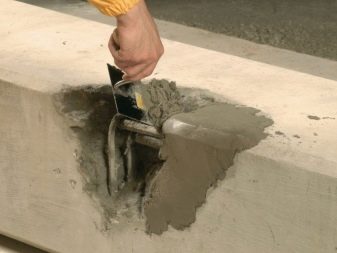
Scope of application
Currently, cement mixes are very popular. Many repair and finishing works cannot do without them. For example, it can be plastering, brick cladding, cinder block or aerated concrete masonry, as well as a floor screed. The ratio of all the necessary components present in the content of the solution directly depends on the permitted scope of its use indicated on the original packaging, as well as the brand and strength properties of the material.
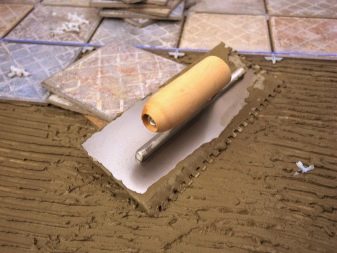
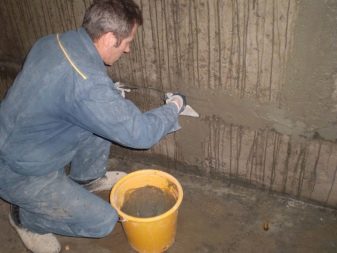
Most often, such compositions are used in the course of interior decoration. In such mixtures, there is a small amount of cement. In addition, there is lime in the interior finishing solutions. For such cement-sand compositions, very fine sand with a homogeneous structure is selected.
Universal compounds can be safely used for masonry, and for interior, and for facade finishing work. In such mixtures, there is an average content of such a component as cement. Often, universal solutions are supplemented with various plasticizers.
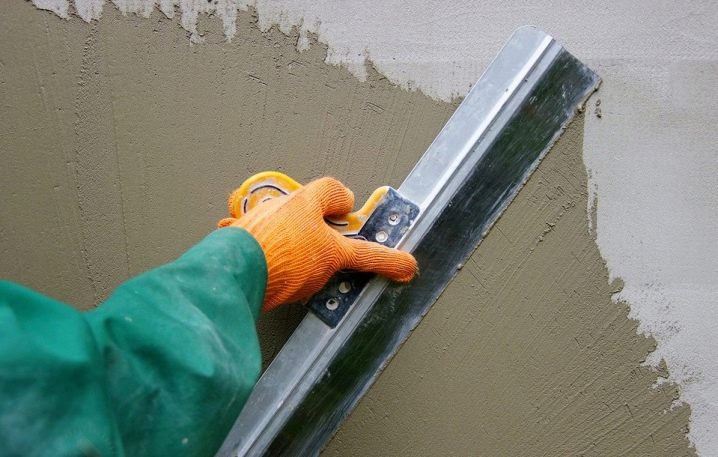
As for masonry mortars, they are used in the construction of mid-rise brick buildings, in the preparation of the floor screed and for facade finishing work. In these mixtures, as a rule, there is an increased content of cement, as well as hydrophobic, frost-resistant and anti-shrinking substances.
Currently, there are more reliable mixtures (M400, M500, M600), which are used in the construction of multi-storey buildings. In such solutions, a high content of cement, as well as reinforcing fibers and plasticizers.
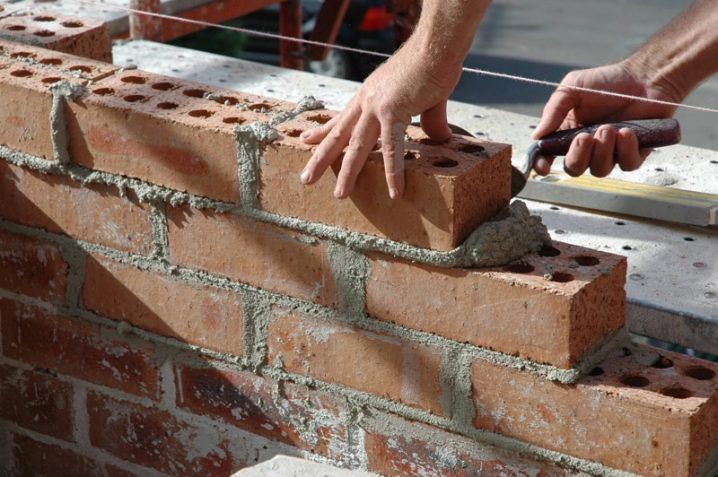
Most formulations are often used for the construction of floor screeds. Stronger, more reliable materials with high markings can be used to prepare a coating that does not require further finishing.
Cement-sand mixtures are ideal for optimal leveling of floors or walls. With their help, you can eliminate many defects of such bases, which is especially important if you plan to lay tiles on them or glue paper wallpaper.
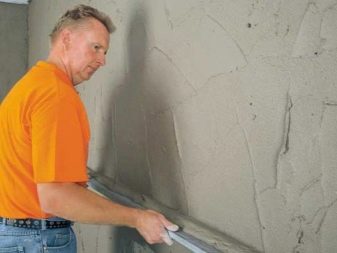
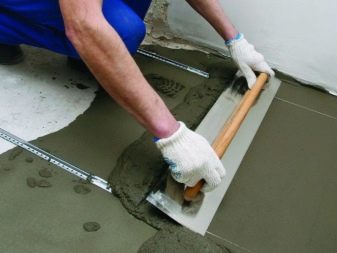
How to cook?
It is quite possible to make a cement-sand mixture on your own.To do this, you should adhere to the correct proportions and not waste time in vain, so that the composition does not begin to dry out. Consider several options for preparing such a solution.
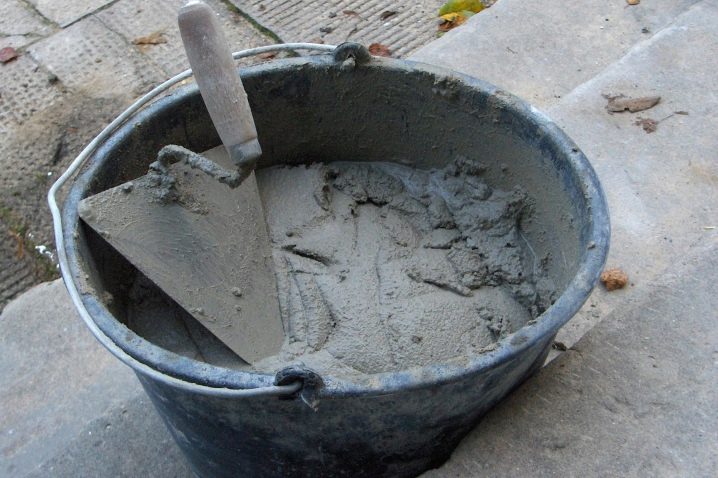
For screed
For such work, cement marked M400 or M500 is most often used. If you chose the 400 grade, then you need to adhere to the proportion of 1 to 2, and in the case of the M500 - 1 to 3.
So that cracks and other similar damage do not appear on the hardened coating in the future, fiber should be added to the solution at the rate of 0.7-0.9 kg per m3.
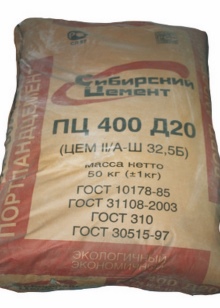
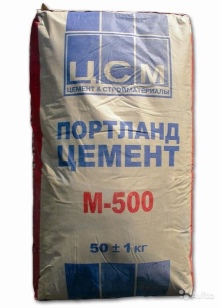
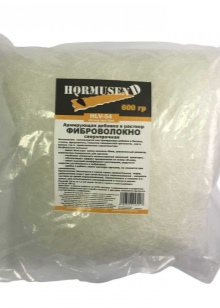
For masonry
In this case, the thickness of the seam determines the quality of the finish. Much depends on how the sand was prepared. It must be carefully sieved and dried. As a rule, 3-5 parts of bulk material are taken for one part of the cement component.
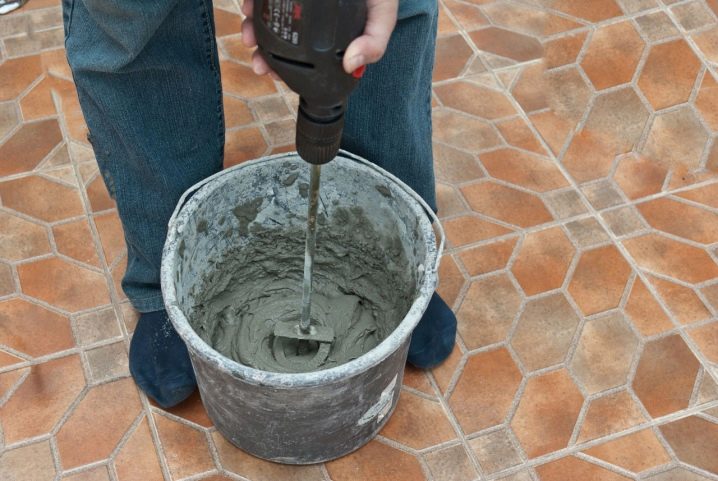
Experts recommend making masonry mixes in moderation. First, you should check the quality of the resulting composition on a separate surface, after which it will be much easier to calculate the proportion of binders and the sand itself. At this moment, the approximate consumption of the cement-sand mixture for the masonry becomes clear. Thanks to such actions, significant waste of material can be avoided.

For plaster
The preparation of such formulations is quite simple. In this case, it is necessary to knead all the components in a 1 to 3 ratio.
The preparation of a high-quality and durable solution depends not only on well-selected components, but also on thorough mixing. It is almost impossible to achieve the desired effect by manual method, even if you use a ready-made composition.
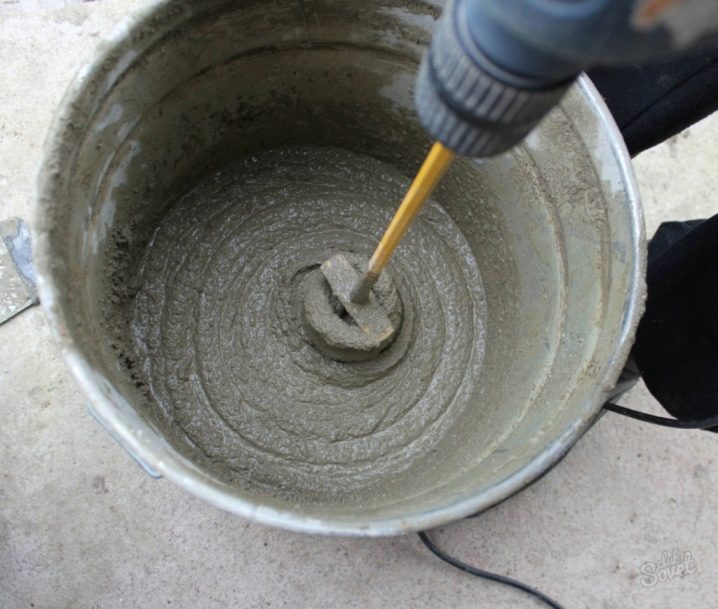
To thoroughly mix the solution, you can use special attachments for perforators or electric drills. Such devices are found in many stores and differ in affordable prices.
Additives
Useful components are often added to cement mixtures to improve their performance.
The function of additional components is performed by the following elements:
- Slaked lime. Water is added for this component. Depending on its volume, the desired state of lime is formed. This can be fluff or lime water. Extinguishing must be done a couple of weeks before direct repair work.
- PVA glue. This simple but useful component is required to provide additional adhesion to the formulation. Thanks to him, the cement-sand mortar will adhere better to one or another base. In addition, the glue will give the mixture additional plasticity, so it will be much easier to work with it. Such additives are especially relevant when it comes to plastering walls.
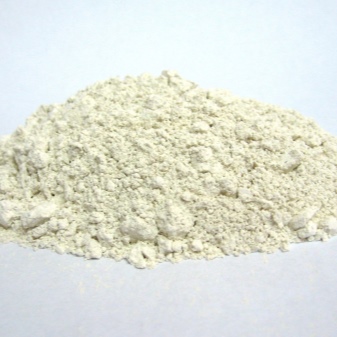
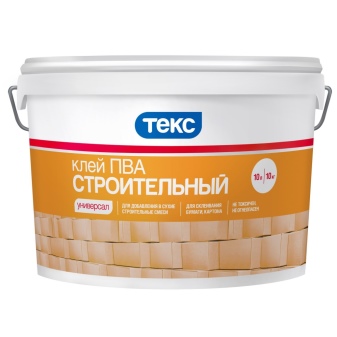
- Dishwashing detergent / liquid soap. These components can be used to give the finishing material increased plasticity. They need to be added immediately after water in the amount of 50-100 g. If you overdo it with these components, the mixture will be foamed - soap bubbles provoke this effect.
- Graphite / carbon black. These constituents are used to impart color to the solution.
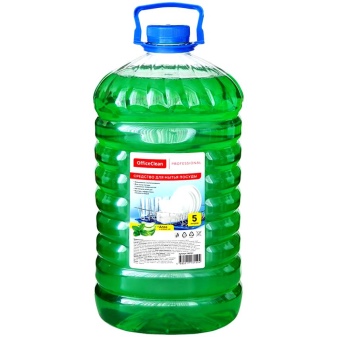
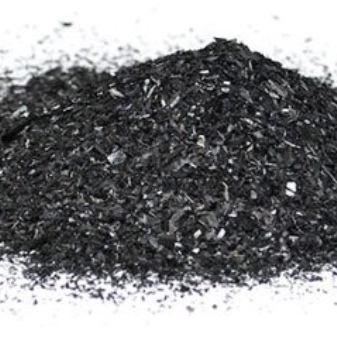
How to calculate the required amount?
It is recommended to proceed directly to construction and finishing work only after a competent calculation of the required amount of cement-sand material.
It is necessary to calculate the volume of the cement slurry, and then multiply them by the cost values (per 1 cubic meter) specified in the description for the purchased mixture. Most often, these parameters are indicated in the form of "consumption per m2". In this case, a layer with a thickness of 1 cm is meant. To find out what the material costs per m3 will be, you just need to multiply the resulting value by 100.
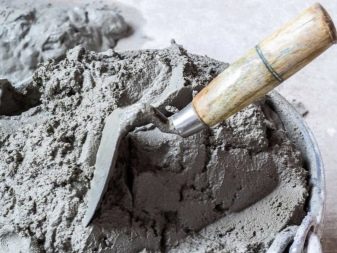
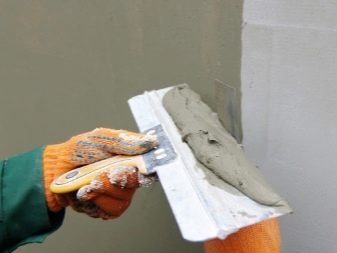
The most common flow rates are:
- for high grade formulations - up to 2200 kg per m3 (in this case, a layer of material of 1 cm is meant);
- for light plasters with lime in its composition - 1200-1600 kg per cubic meter.
As for calculating the consumption of a mixture for plastering or screed, there is nothing complicated here. But the calculation of the mortar for masonry, first of all, depends on the experience of the master. If you strictly adhere to the appropriate technology, then the consumption of the cement-sand mixture will be about 25% of the total volume of the wall. True, there are times when this figure is 35%, if you try very hard. This can be done economically by making the seams thick enough and avoiding splashing.
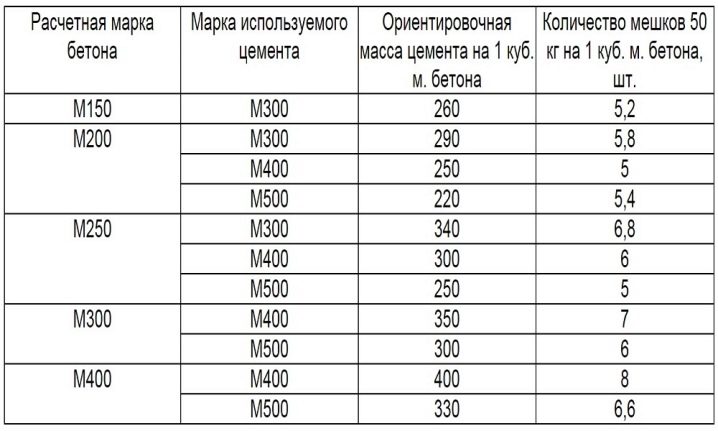
Setting time
Typically, the setting time of cement-sand mixtures is about 1-1.5 hours. This indicator, first of all, depends on the water content in the solution. Based on the setting time, experts advise preparing the composition in small portions.
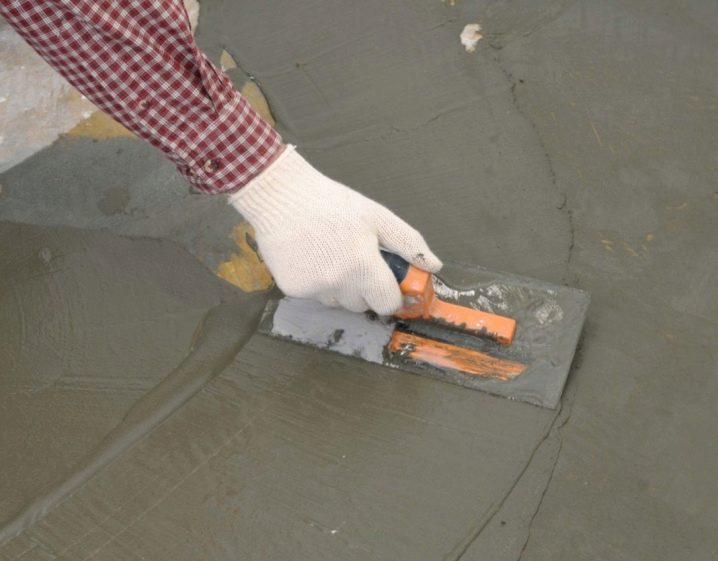
Manufacturers
Currently, the range of high-quality and durable cement-based mortars is greater than ever. Of the large number of different manufacturers, the most popular and demanded ones should be distinguished.
"Monolith"
This large manufacturer specializes in the production and sale of cement-sand mixtures in Kirov. The range of "Monolith" is represented by high-quality and reliable M150 class compounds, which are ideal for plastering various substrates, sealing joints, as well as for masonry work inside and outside buildings.
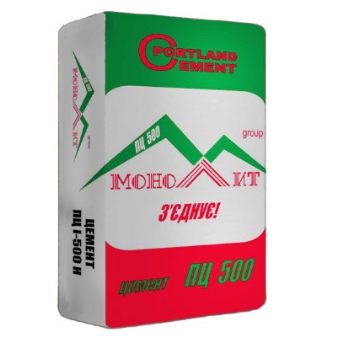
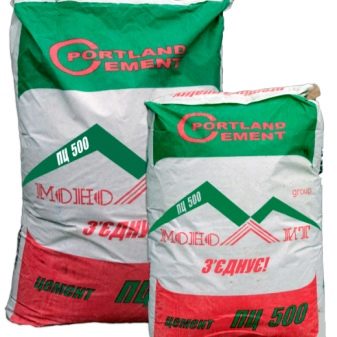
The manufacturer also offers strong M300 class compounds that can be used in the manufacture of high-strength concrete structures.
Knauf
This well-known and large brand produces high-quality cement and plaster mixes represented by the Grünband, Diamant, Zokelput, Sivener, Unterputz, and Adheziv lines.
This product boasts excellent thermal insulation performance. It can be used for both indoor and outdoor decoration work. Most Knauf cement compositions contain additional components that enhance their positive qualities.
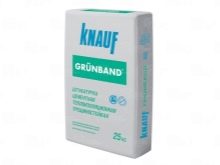
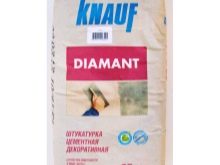
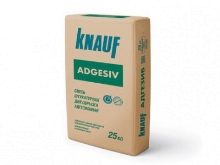
"Real"
This is another well-known manufacturer that produces high-quality cement mixtures of the M100 (200), M150 and M75 classes. The assortment of the company "Real" allows consumers to choose the best option for a variety of repair and finishing works.
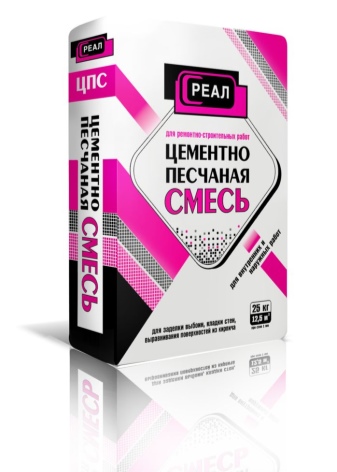
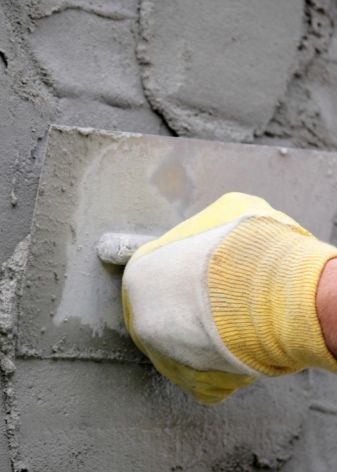
Dry mixes "Real" are supplemented with components that provide frost resistance, so they can be used not only for interior, but also exterior decoration.
Dauer
The German company Dauer offers a choice of consumers high-quality and inexpensive cement-sand mixtures for the preparation of screeds, facade and interior decoration, as well as for the installation of bricks or blocks.
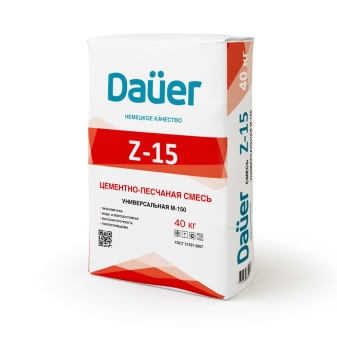
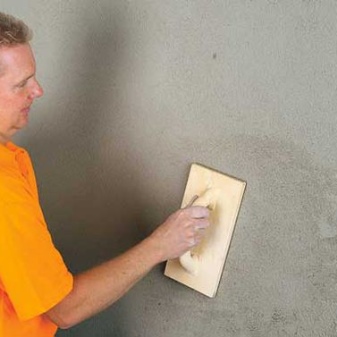
Dauer dry mixes are popular because of their low consumption. Coupled with a democratic price, this quality makes such finishing materials the most profitable from an economic point of view.
"BaltPiterStroy"
This is another large Russian manufacturer that produces cement-sand mortars of all well-known brands. In addition, the assortment of this company also includes other popular products, for example, crushed stone, sand, gravel, rubble stone, bag cement and even deicing agents.
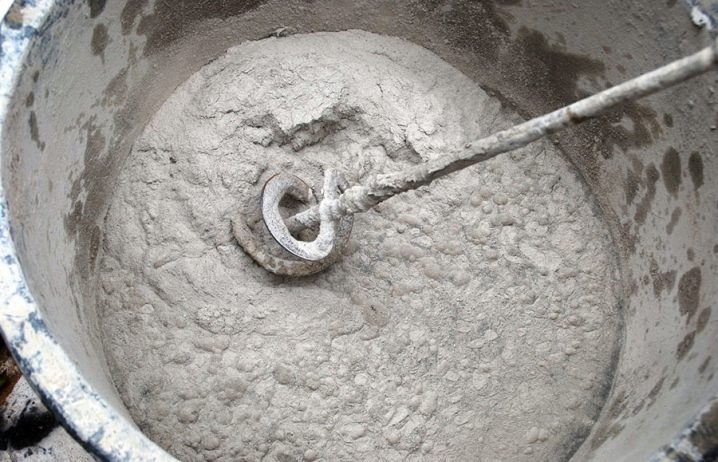
"Stroyservice-Novablock"
The assortment of this popular manufacturer is represented by Novanlock dry mortars, which were previously called Plita Milks, as well as cement-sand compositions. In addition, the company offers a high-strength sand and gravel mixture with the M300 marking.
The unsurpassed quality of Stroyservice-Novablock products is due to the production of an industrial scale using modern plant equipment.
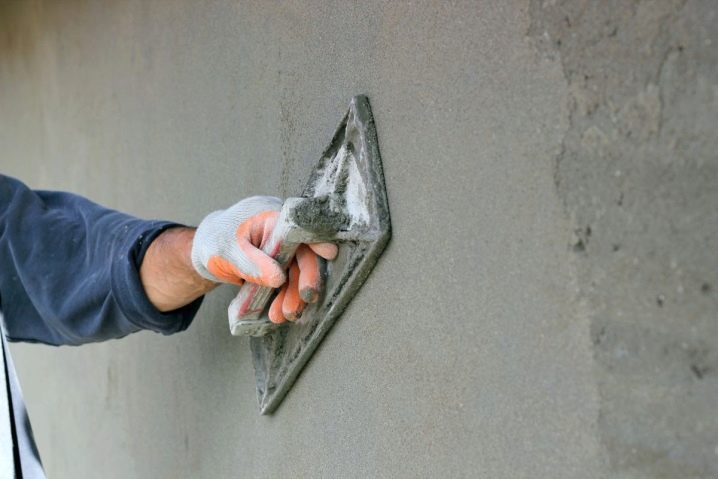
"Adamant SPB"
The plant with the memorable name “Young drummer” belongs to LLC “Adamant SPB”. It offers the widest range of high quality concrete, reinforced concrete structures, cement, sand and gravel.
As for the cement-sand mixtures of this manufacturer, they are represented by all possible brands, from simple and inexpensive M100 to high-strength M400.
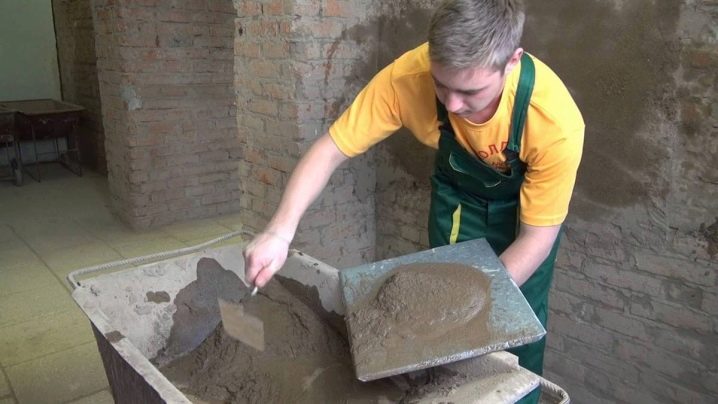
Advice
For many years, cement-sand mixtures have been the most common and demanded materials used in repair and finishing work.
When leveling the walls with a cement-sand composition, be sure to use beacons. Without them, the work will be more laborious, and the result may not suit you.
When purchasing a cement mortar, pay attention to its production time. The cement can be stored for 6 months in a dry space. If the humidity in the room was increased, then the quality of the building material will noticeably suffer from this.
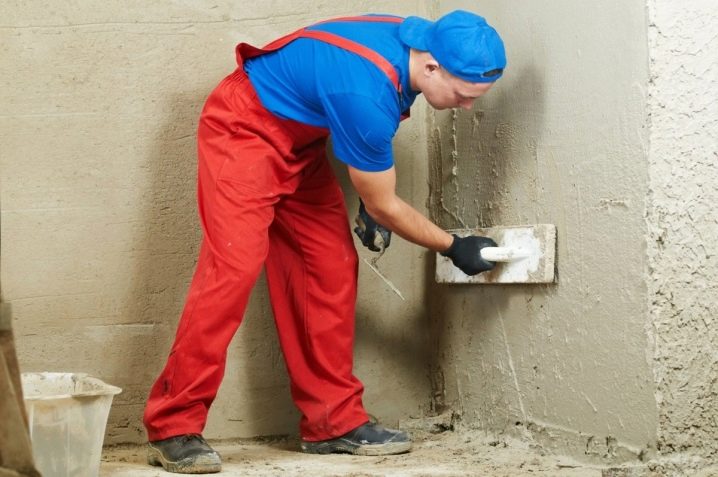
Do not forget that after preparation, the cement mortar should be used within 2 hours. Otherwise, it will simply dry out and it will be impossible to use it. When adding water to the solution, it should be borne in mind that its volume should be equal to the volume of cement.
It is not recommended to finish wooden bases with simple cement-sand compositions, however, for this, clay mortars with a certain cement content can be used. With such mixtures, you can safely handle both internal and external bases.
Consider the impressive weight of cement-sand mortars. On a weak and unreliable basis, they may not last long.
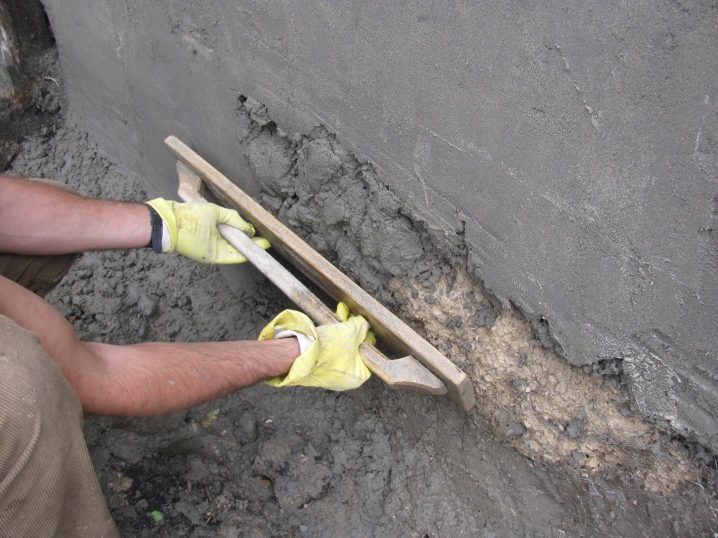
Tools and containers that you use during work must be washed immediately after they are finished. Otherwise, the solution will dry out and it will be almost impossible to remove it from the fixtures.
Many consumers are wondering which cement-sand mixtures will be the ideal solution for arranging the foundation. According to experts, the high-quality and reliable composition of the M300 is perfect for such purposes. It is not recommended to use simpler and cheaper mixtures (such as M100).
If you want to extend the drying time of the composition, then in no case should you add additional portions of sand or cement to it. Water will not be able to sufficiently dissolve such dry formulations, and the material will turn out to be unusable.

To prepare the solution, it is recommended to use a metal or plastic container. Keep in mind that ordinary river sand is not used in the preparation of the mixture. Instead, it is necessary to dig up bulk material in the ground. Don't make the solution too thin. Otherwise, it will not fit well on one or another base, and will also slide off the spatula.
Do not skimp on buying a high-quality cement-sand mixture. A low-quality composition can be not only capricious in work, but also very short-lived. Refer to products from well-known and popular suppliers. This way you protect yourself from buying inferior mortar.
How to mix the cement-sand mortar correctly, see the video below.
The comment was sent successfully.