How to dilute cement correctly?
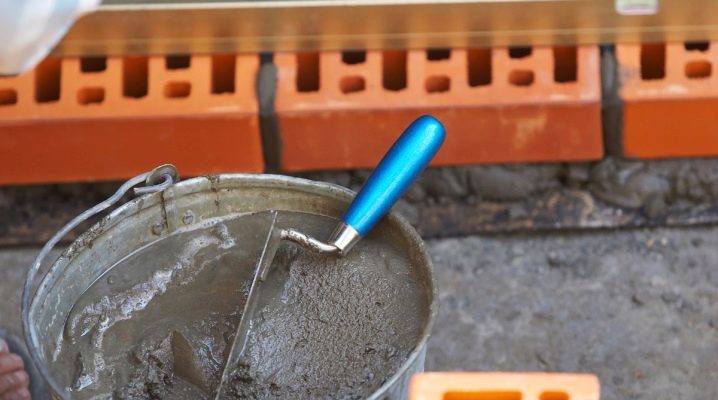
Those who are faced with construction and repair work, at least once, had a question about how to properly prepare cement, since it is one of the most common bases that is used in construction and repair work. Often, when mixing a solution, builders do not comply with the proportions required by the standards for preparing the mixture, which affects the end result: a structure made in this way becomes unusable over time. In this regard, the correct cement dilution technique is considered below, by completing which you can get a high-quality solution for future construction.
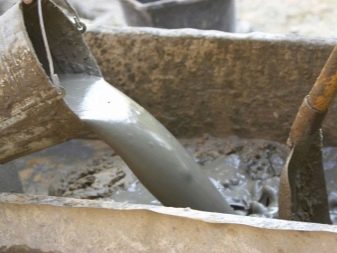
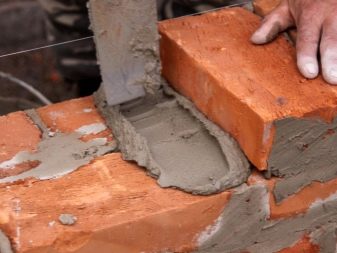
Peculiarities
Cement has long acquired the status of the most demanded material used for construction. With its help, concrete is obtained, which is used for the foundations of future structures. The cement composition is the main binder for obtaining a concrete mixture.
The cement itself is an astringent mineral powder, which, when combined with water, becomes a viscous mass of grayish color and after a while hardens in the open air.
Powder is made by grinding clinker and further adding minerals and gypsum. Thickened cement can be adversely affected by aggressive media and plain water. To improve the characteristics, a hydroactive material is added to the cement composition, which prevents the penetration of salts. Corrosion resistance increases with the addition of a special polymer additive to the initial composition of raw materials, which significantly reduces porosity and prevents adverse physical and chemical effects on the environment.
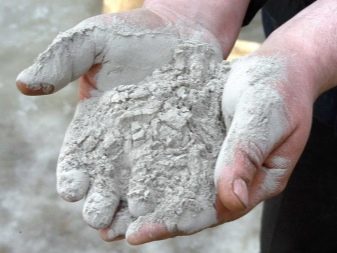
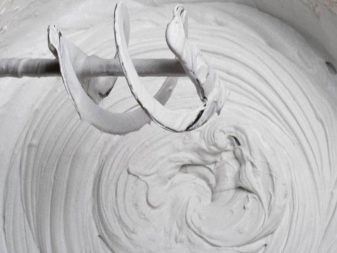
All kinds of cement compositions absorb different volumes of water. The grain size of the material has a fairly high density, three times the density of water. As a result, when a large amount of water is added, part of the cement will not dissolve, but will end up on the surface of the prepared solution. Therefore, the material will settle, and the top of the structure from the resulting cement mortar will turn out to be an unstable and cracking structure.
The cost of a material depends on the quality of its grinding: the finer the constituents of the cement, the more a person will pay for it. This is directly related to the setting speed: a finely ground composition hardens much more rapidly than coarsely ground cement.
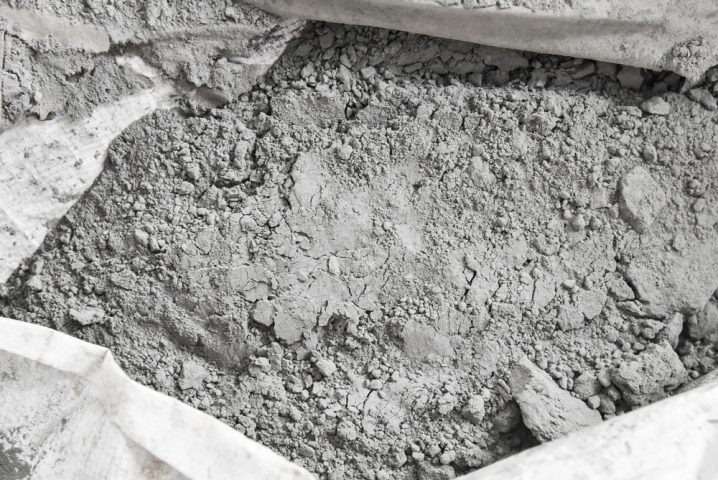
To determine the grain size composition, the material is sieved through a sieve with meshes of less than 80 microns. With a high-quality cement composition, the largest part of the mixture is sieved. But at the same time, do not forget that fine grinding is of better quality, but in the future it will require a larger volume of water. Therefore, it is recommended to give preference to a composition with both small particles (up to 40 microns) and large (up to 80 microns). In this situation, the cement mixture will have all the necessary and acceptable properties.
The possibility of thawing and freezing is one of the main characteristics of the cement mixture. The water in the porous areas of the cement structure expands in volume up to 8% at low temperatures. When this process is duplicated, the concrete cracks, which contributes to the destruction of the constructed structures.
In this regard, cement is not used in its pure form in construction work. Wood pitch, sodium abietate and other mineral additives will help to increase the service life and enhance the stability of concrete.
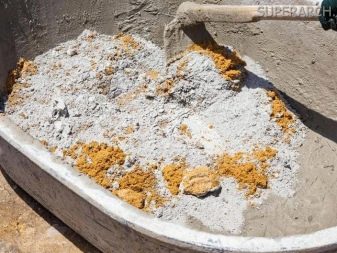
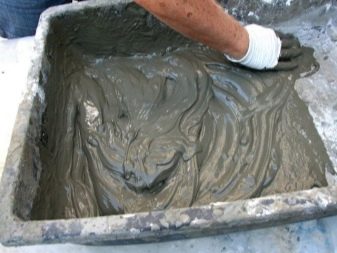
Recipes
Before making a cement base, you need to determine for what purpose it will be needed. Each mixture requires specific proportions. Below are the most common options for preparing cement mixtures.
- For plastering walls. To obtain this type of mixture, it is required to use a ratio of cement and sand in a ratio of 1: 3. The rate of water is equal to the amount of cement. To obtain the desired consistency, the water is gradually added to the dry mixture. If it is necessary to carry out construction work inside the premises, preference is given to the M150 or M120 brands, and when planning facade plastering - the M300 brand.
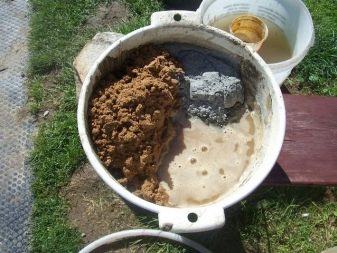
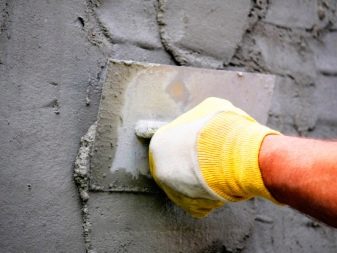
- Brickwork. In this case, a cement to sand ratio of 1: 4 is required. The M300 and M400 grades are the best option for this type of construction work. Often this mixture is diluted with slaked lime, which acts as a binder. The amount is calculated for one part of cement and two tenths of slaked lime.
Thanks to this component, you can get a plastic material, which is quite comfortable and simple to use. The required volume will be determined during the addition process before a solution of the required consistency is obtained. It is recommended that you get a mixture that does not run off the trowel at a 40 degree angle.

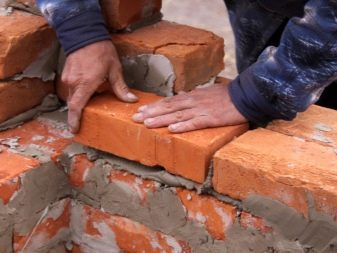
- Floor screed. The standard proportion for this composition is 1 part cement base to 3 parts sand. The M400 brand is ideal for this. In this case, water is taken in the volume of one second to the already added part of the cement.
For a better screed, water should not be poured in full volume, since it is extremely important that the mixture becomes plastic and stretches well - this will guarantee that all empty areas on the base of the screed are filled.
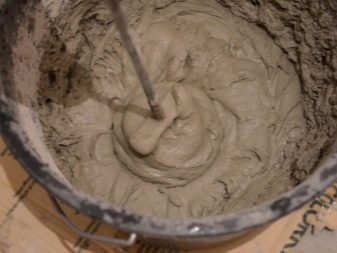
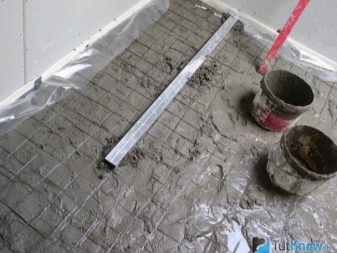
- Concrete mix. To obtain concrete, 1 part of a cement base, 2 parts of sand and 4 parts of gravel are used. When planning, you can use the resulting concrete mixture as a foundation for the future premises. In this case, it is recommended to purchase materials of the M500 brand. The rate of water is equal to one half of the part of the cement base. The water should be used clean and potable.
Mixing should be done in a concrete mixer. You need to apply the resulting concrete mixture within an hour. For a better composition, add alabaster.
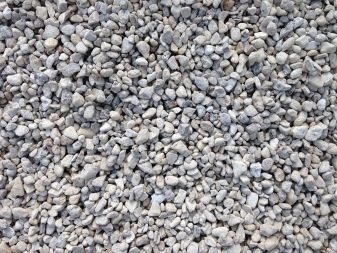
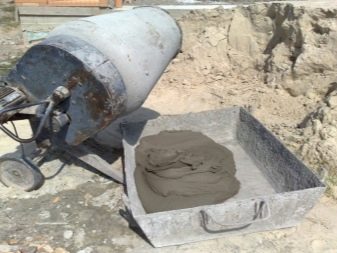
How to breed correctly?
Do-it-yourself mixing of cement at home is recommended to be performed in a container made of metal or plastic. To do this, you need a shovel, spatulas and a drill with various attachments. With a large volume of cement preparation (from 1 to 3 cubic meters), it will be more practical to use a concrete mixer. All the necessary tools, materials, as well as the breeding site are prepared long before the start of work.
It is worth remembering that the prepared mixture must be applied immediately after receiving it, then it begins to harden, and its operation is impossible.
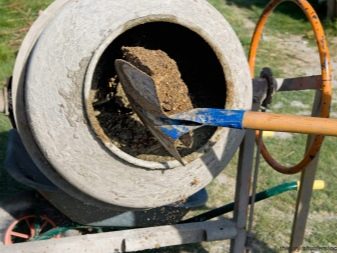
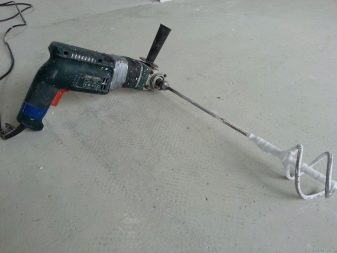
The sand must be rinsed and dried in advance. Wet fillers are not added in any way - this will violate the ratio of water to cement. The conformity check is determined as follows: the grade with the stability determined at the factory is divided by the number of sand fractions. It is preferable to mix the cement using clean water (it is also allowed to use melt, rain and drinking water). In order to give plasticity, you can enter a soap solution, lime, a plasticizer, but not break the norm: more than 4% of the astringent proportion of the composition.
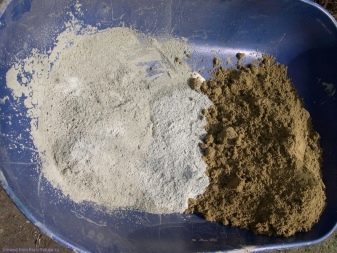

The sequence for introducing materials into the container is determined by the kneading method. If specialized equipment is not used, then sand is sieved into the container, then cement, and then water is added. With the help of a concrete mixer, water is added first, followed by sand and cement. With any method, the cement base is diluted within 5 minutes. During this period of time, the base should become a uniform consistency.
A well-diluted mixture remains on the spatula and slowly flows from it, and if it is turned over, then there are no lumps or poorly diluted particles in it.
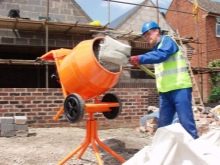
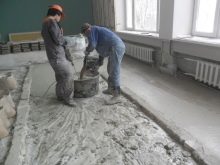
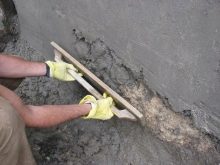
Advice
Sifting through sand can seem boring and unnecessary. But if there is a need to get a high-quality and even surface, then you should get rid of all kinds of impurities in the sand. For sifting, use a sieve or fine mesh.
Another budget option is to drill holes in the bottom of the bucket.using a thin drill. For a large amount of sand, you can build a wooden frame on which you need to stretch a metal mesh. After that, all that remains is to place the sand and shake it by the edges of the frame. The resulting material with fine grains is perfect for a cement mixture.
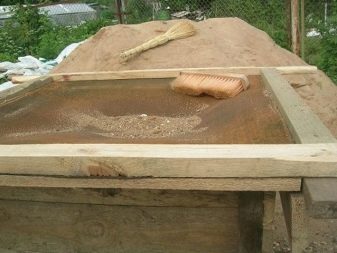
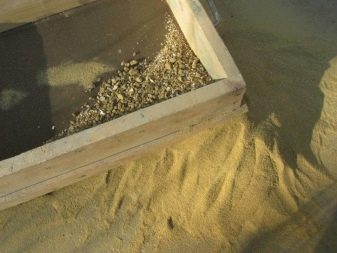
To obtain a homogeneous mixture, sand and cement can be kneaded using a special attachment for a drill or a spatula. If necessary, you can mix a larger volume of the mixture - in this case, a concrete mixer or a wide bathtub is used, in which all the components are stirred with a shovel. A budget option is to use a piece of old linoleum as a base for stirring the solution.
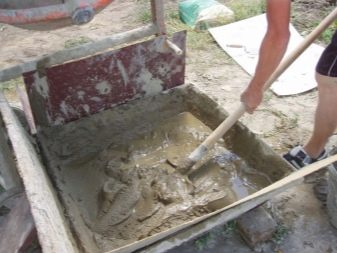
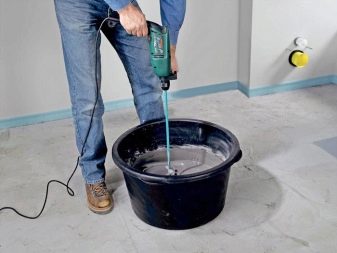
After obtaining a homogeneous solution, the required volume of water is added, which is approximately equal to the amount of the cement mixture. It should be constantly stirred until a homogeneous mass is obtained. It is not necessary to achieve an overly liquid consistency - the solution sets well enough and does not drain when turning the spatula.
The prepared solution is recommended to be applied no later than two hours from the moment of its receipt. In this regard, it is necessary to plan the time for which the resulting mixture is sold.
When purchasing a finished material, you need to be sure that it was prepared just before being sent to the buyer. It is advisable to study all the information about the product before making a purchase to make sure what constituents the solution consists of, as well as how to use it.
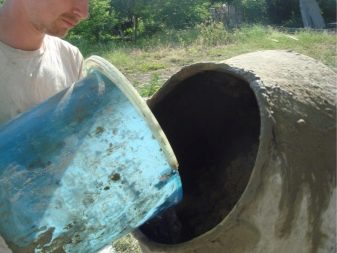
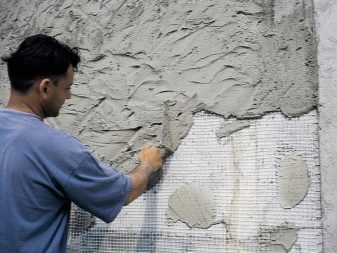
All cement mixtures have the same constant components, which include cement, quarry sand, crushed stone and water. Their ratios change due to the stringy element. In other words, the higher the cement grade, the thicker the prepared mortar will be. For example, 1 cubic meter. m cement mixture will be consumed in the following way: grade M150 - 230 kg, grade M200 - 185 kg, grade M300 - 120 kg, grade M400 - 90 kg.
The proportions vary depending on the selected grade and type of concrete. For manual laying, the mixture can be used by combining the components in this way: cement grade M300 - one part, sand - three and a half parts, crushed stone - five parts, water - one second part. Upon completion, you will get a concrete mix of the M50 brand.
It is important that water is used without all sorts of impurities: oil, compounds containing chlorine, residues of other solutions.
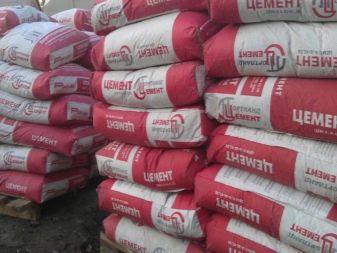
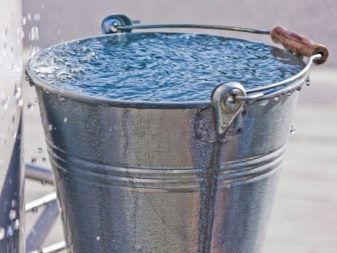
Cement with added lime is obtained as a result of different proportions. In this case, the place of use plays a significant role. For example, when using a plaster mixture in areas of greatest wear, it is recommended to increase the binder.
However, there is a single sequence for preparing the solution:
- add clean water to the lime container in advance;
- combine sand with cement;
- stir the mixture in the lime liquid.
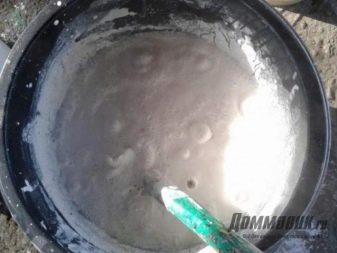
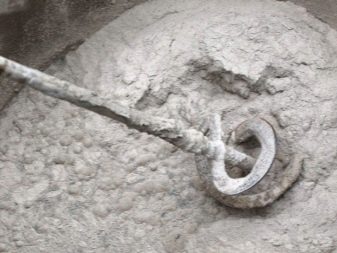
Having basic knowledge of cement mortar, you can speed up the process of its preparation, as well as choose the right ingredients.
For information on how to mix the cement mortar correctly, see the next video.
The comment was sent successfully.