White cement: features and applications
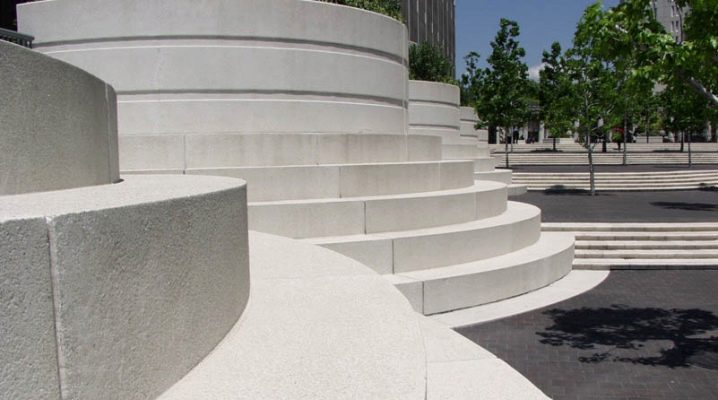
On the shelves of hardware stores, the buyer can find not only ordinary cement, but also white finishing material. The material differs significantly from other types of cement in the composition of the initial components used, price, quality, manufacturing technology and field of application.
Before starting work with this type of building material, it is necessary to carefully study the properties and characteristics of the composition, the peculiarities of working with the solution, to determine the bona fide manufacturers who produce high quality goods that meet all technical norms and standards.
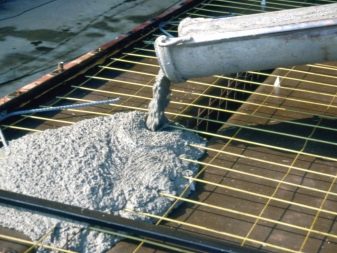
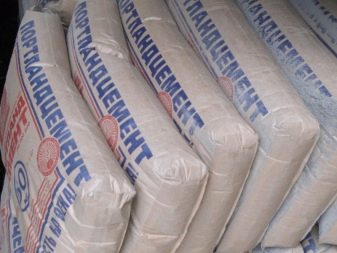
Peculiarities
White cement is a type of high quality cement mortar that has a light shade. The light tone of the building material is achieved by combining certain types of components and using special production technologies. The base is clinker with a low iron content. Additional components for obtaining a light shade are refined carbonate or clay compounds (gypsum powder, kaolin, chalk, crushed lime and chloric salts).
High strength values are achieved by rapidly decreasing temperature (from 1200 to 200 degrees) after the firing process in an environment with a minimum oxygen content. The main condition for achieving such a white color during heat treatment in ovens is the absence of soot and ash. The burners are only fueled with liquid and gaseous fuels. Grinding of clinker and raw materials is carried out in specialized crushers with basalt, flint and porcelain slabs.
Cement mortar of all brands has high frost resistance and resistance to negative environmental influences.
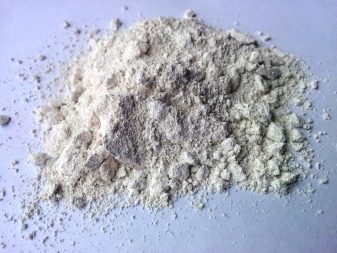
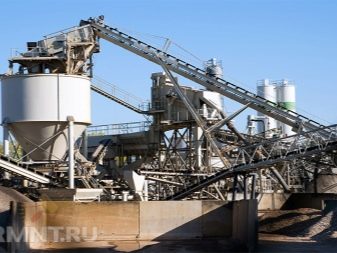
All characteristics of white cement are significantly superior to those of standard mortars:
- fast hardening process (after 15 hours it gains 70% strength);
- resistance to moisture, solar radiation, low temperature indicators;
- high structural strength;
- the ability to add a colored dye;
- high degree of whiteness (depending on the variety);
- low level of alkalis in the composition;
- multifunctional and versatile properties;
- affordable price;
- environmental Safety;
- the use of high-quality raw materials and modern production technologies;
- high decorative qualities.
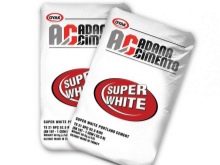
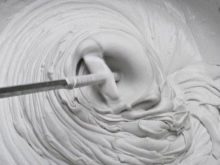
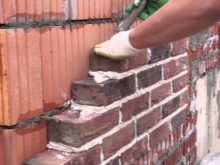
White cement is a versatile material with a wide range of applications:
- production of finishing solutions (decorative plaster, grout for joints), the drying time depends on the type of filler;
- production of plaster, tiles, decorative stone for facade work;
- production of sculptures and decorative elements of the interior (fountains, columns, stucco moldings);
- production of white concrete, reinforced concrete structures (balconies, stairs, architectural forms and fences);
- production of mortars for stone and tiles;
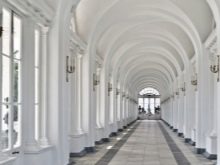
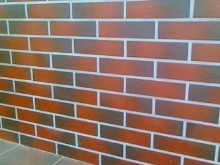
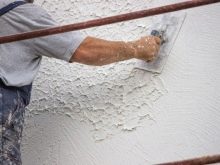
- production of white or colored finishing bricks;
- preparation of a mixture for self-leveling floors;
- road marking and airfield runways.
For the production of white cement, manufacturers must have special equipment for the extraction, grinding, roasting, storage, mixing, packing and shipping of raw materials.
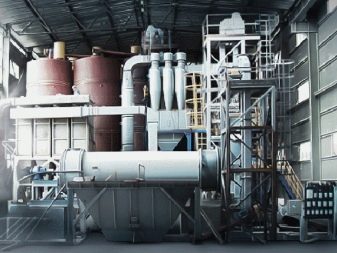
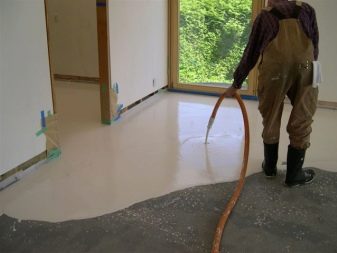
Specifications
White cement is produced in accordance with the standards and requirements established by GOST 965-89.
Cement is produced in several grades, depending on the level of strength:
- M 400 - average level of solidification, high percentage of shrinkage;
- М 500 - medium level of hardening, low percentage of shrinkage;
- M 600 - high level of solidification, minimal shrinkage.
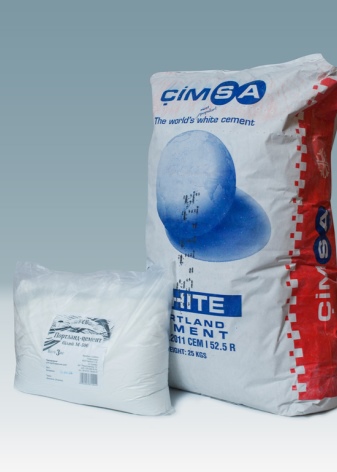
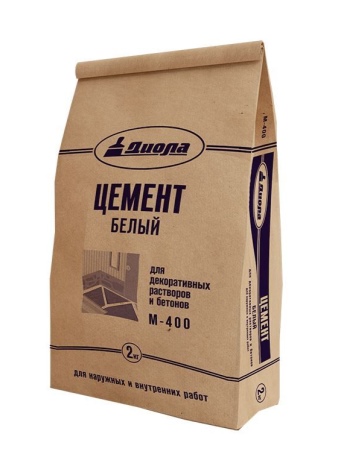
The decorative whiteness of the material divides the mixture into three grades:
- 1st grade - up to 85%;
- 2nd grade - not less than 75%;
- 3rd grade - no more than 68%.
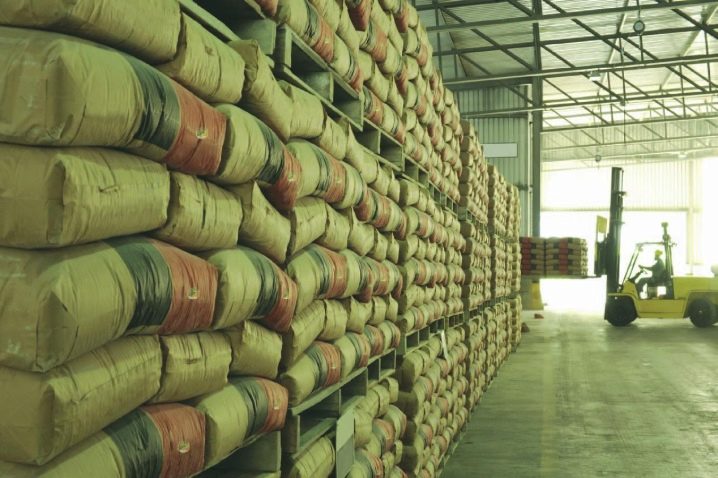
Manufacturers distinguish three ways to obtain clinker:
- Dry - without the use of water, all components are crushed and mixed with the help of air, after firing the necessary clinker is obtained. Advantages - savings on heat energy costs.
- Wet - using liquid. Advantages - accurate selection of the composition of the sludge with a high heterogeneity of the components (sludge is a liquid mass with a water content of 45%), the disadvantage is a high consumption of thermal energy.
- Combined type is based on wet production technologies with intermediate clinker dewatering up to 10%.
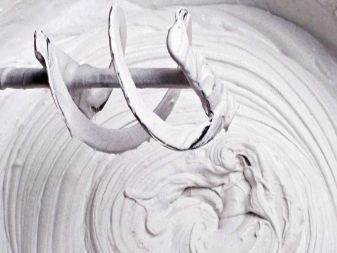
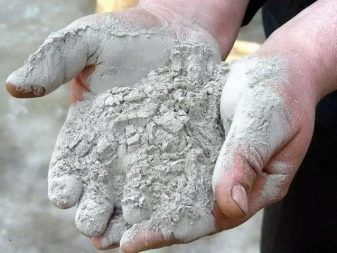
To knead the solution at home, it is necessary to mix industrially refined quartz sand or river washed and seeded sand, crushed marble and white cement. The required proportions are 1 part cement, 3 parts sand, 2 parts filler. Mix the components in a clean container without dirt and corrosion. The fraction of aggregates is minimal, the color of other materials should not be gray, but only white.
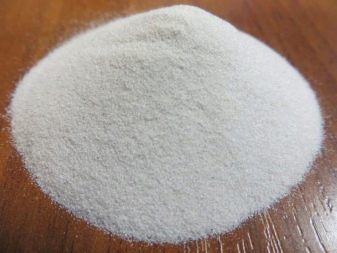
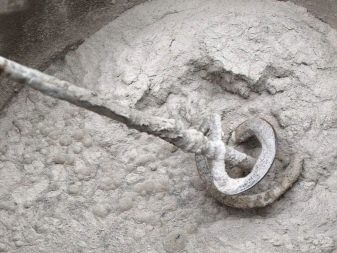
Persistent pigments added to the composition of the solution will help to make the part-cement colored:
- manganese dioxide - black;
- escolaite - pistachio;
- red lead iron;
- ocher - yellow;
- chromium oxide - green;
- cobalt is blue.
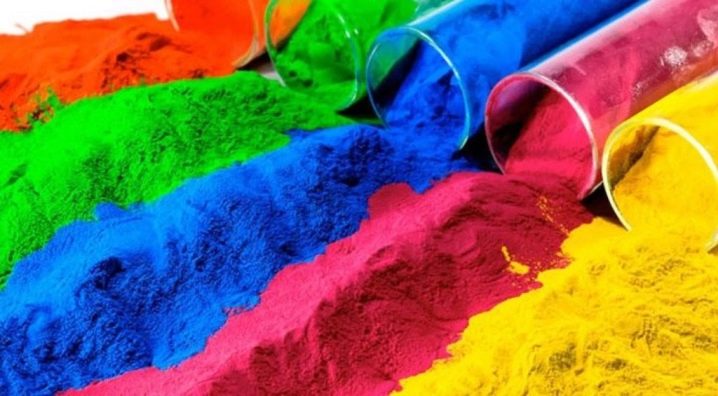
Manufacturers
White cement production is carried out by many foreign and domestic companies:
- JSC "Shchurovsky cement" - a leader among Russian manufacturers. The advantage is fast and convenient delivery. Disadvantages - the green tint of the product, which significantly reduces the scope of its application.
- Turkey Is the world's largest manufacturer and exporter of white cement. Building materials stores offer their customers white Turkish cement of the M-600 brand with the Super White marking and with a whiteness of 90%. The mixture is produced by a dry method and has a number of advantages, which include: affordable price, European quality standards, weather resistance, smooth surface, high perniciousness and compatibility with various finishing materials. The main producers of Turkish cement are Adana and Cimsa. Cimsa products are most in demand in the construction markets of Europe and the CIS countries. Products of the Adana brand are a new product of construction stores, gaining their place in this segment of finishing materials.
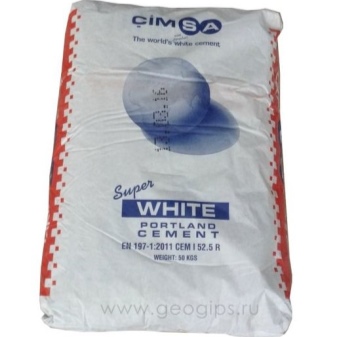
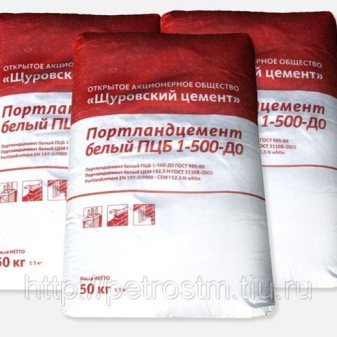
- Danish cement occupies a leading position among its counterparts, has a high quality, is produced by qualified specialists using innovative technologies, has the M700 marking (with high strength). Advantages - low alkali content, even whiteness, high reflective characteristics, has a huge scope of application. Disadvantages - high price.
- Egyptian cement - the newest and cheapest finishing material in the world construction market. Disadvantages - difficulties and interruptions in supply to specialized markets.
- Iran ranks 5th in terms of production of white cement in the world. Iranian cement grade M600 is produced in accordance with international quality standards. Physical and chemical performance is at a high global level. The products are packed in 50 kg polypropylene bags, which ensures complete safety during transportation.
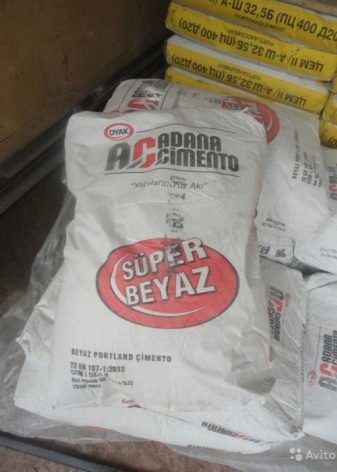
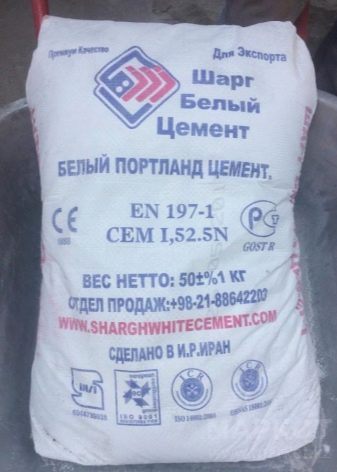
Advice
For high-quality work using white material, experienced builders are advised to take into account some of the features:
- To obtain a high-quality solution, it is necessary to use only marble chips and sand with a low percentage of iron, as well as clean water without heavy salts and impurities.
- After 20 hours, 70% hardening occurs, which will significantly reduce the time spent on repairs.
- Versatility, color fastness and aesthetic whiteness allow the material to be harmoniously combined with other decorative elements of the interior.
- Strength and resistance to the appearance of chips and cracks will reduce additional costs for repair and restoration of the structure.
- The tools used for finishing work must be kept perfectly clean, all surfaces must be cleaned of corrosion and dirt.
- Deepening the reinforcement into a reinforced concrete structure to a depth of at least 3 cm will avoid corrosion of metal surfaces and the appearance of stains on the white coating.
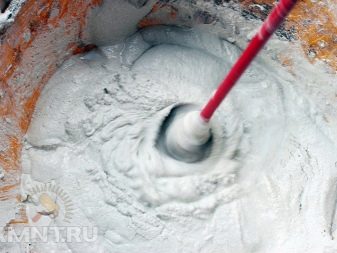
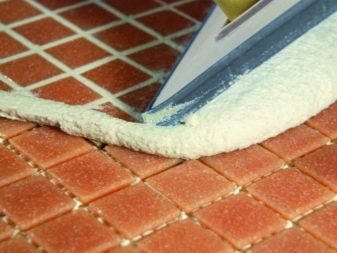
- It is obligatory to apply gray cement on the iron structure with a thickness of at least 30 mm.
- You can use in the production process plasticizers, retarders and additional additives that do not affect the color of the solution.
- Titanium white can be used to increase the percentage of whiteness.
- It is necessary to dilute the solution with extreme caution, observing all safety rules and using personal protective equipment for the eyes, face and respiratory organs.
- Cement can be stored for 12 months in undamaged original packaging.
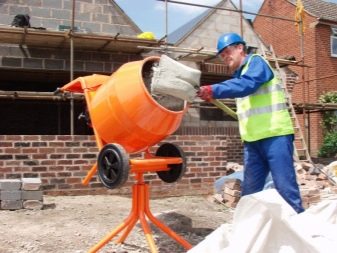
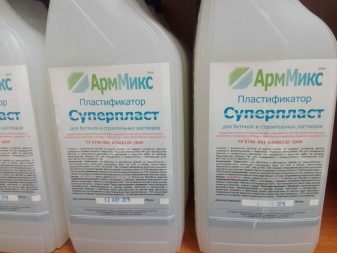
Cement is the backbone of any construction process. The reliability, strength and durability of the structure depend on the quality of the selected material. The modern building material market offers a huge range of goods. Before making the final choice, it is necessary to carefully study all manufacturers and their proposals in order to avoid purchasing a low-quality product with low technical properties and characteristics.
For information on how to prepare a white cement mortar, see the next video.
The comment was sent successfully.