All about drilling rigs
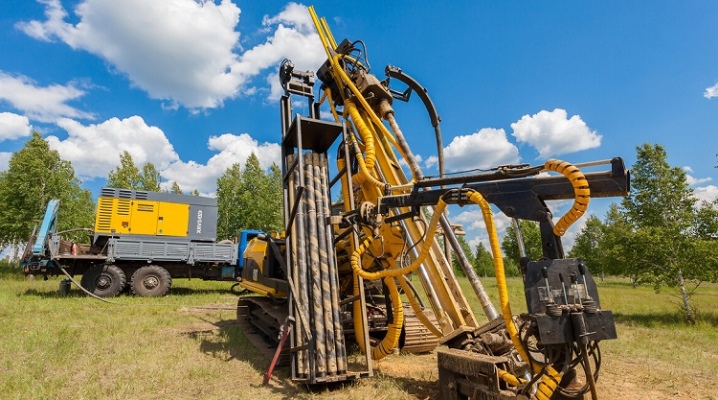
To know everything about drilling rigs, about their classes and types, it is necessary for a lot more people than it seems at first glance. Before choosing drilling rigs for wells or traveling systems for the rigs themselves, you still need to familiarize yourself with spare parts and diagrams. We'll have to figure out what is included in such a technique, how to install it and what measures should be taken during maintenance.
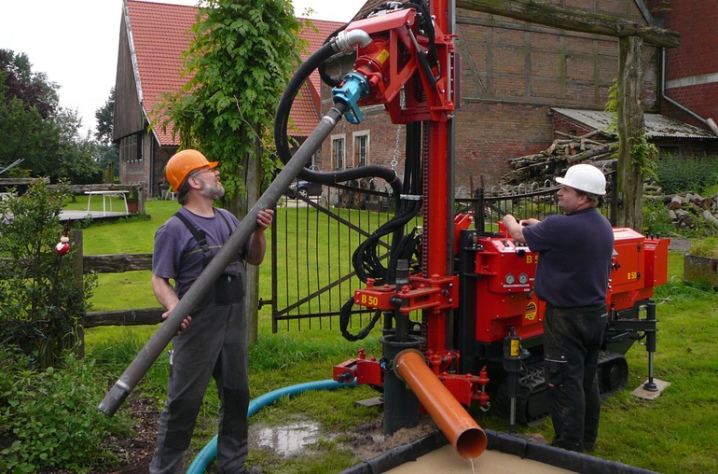
What it is?
It should be said right away why they say exactly "drilling rig", and not just a drill or a drill. The fact is that the methodology for performing such work has become significantly more complicated. And for normal operation, it has long been required not just a "blade or pin piercing the ground," but a whole complex of units. The list of devices that are part of the installation depends on:
- special purpose drilling rig;
- the selected method of penetration;
- actual conditions for drilling operations.
For example, onshore oil production systems in most cases consist of:
- towers and winches;
- spire type coils;
- special capacity;
- devices for the formation of drilling mud;
- pumps;
- emission protection systems;
- autonomous electric generator;
- cementing complex and a number of other parts.
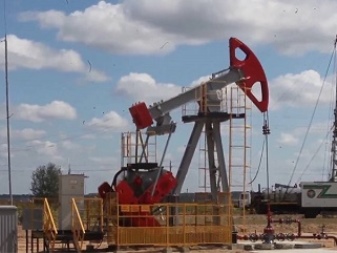
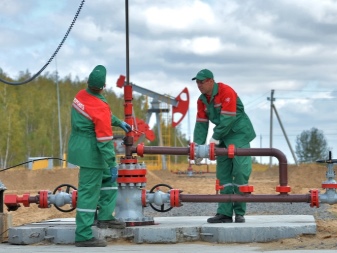
The basic operating principle of the drilling rig remains the same as in ancient times. A mechanical device (tip, drill) driven by it crushes the soil and rocks that it encounters on its way. From time to time, drilling of the well is replaced by the extraction of the drilling tool, its blowing (flushing) from clogging crushed masses. The shape of the passable canal and its slope can vary greatly. And yet, in most cases, the drilling system works strictly vertically, because it is more convenient and more efficient. Can be applied:
- shock rope;
- screw;
- rotational technologies;
- drilling with an annular face;
- continuous face penetration;
- penetration with a hard alloy tool.
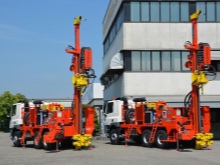
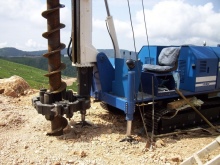
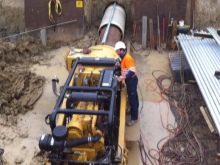
When are they needed?
Drilling rigs are needed very often for water drilling. Process water can also be extracted from relatively shallow depths. But drinking water supply is the safest and most stable from artesian sources. They can even be reached by many relatively compact mobile units. Drilling wells is even easier. Experienced craftsmen only need a minimum of time when using a good tool.
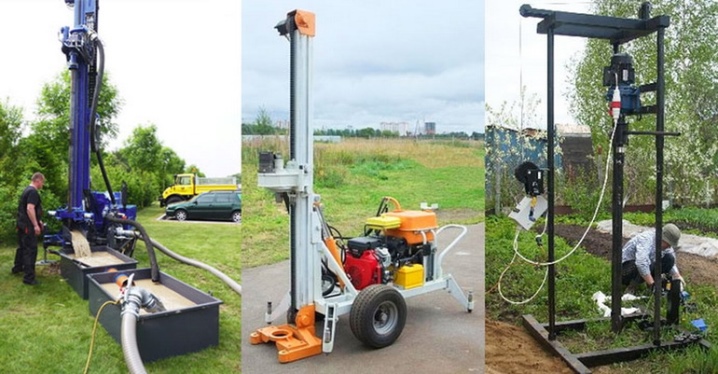
But this only applies when drilling equipment is used for the earth. The extraction of hydrocarbons - oil, natural and shale gas requires the obligatory drilling of hard rock for kilometers in depth. It has long been mastered the creation of powerful oil drilling rigs used on land or on the shelf. However, even with all the power of modern technology, the drilling of such wells takes many months (especially if we also take into account the preparatory work).
A very significant volume of oil and gas drilling still falls on the exploration of depths (even the most modern alternative methods provide only a probabilistic assessment of deposits and the prospects of individual places).
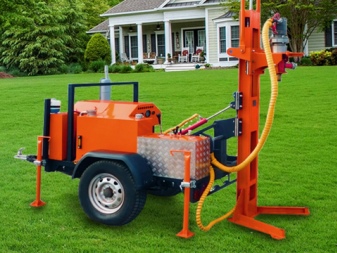
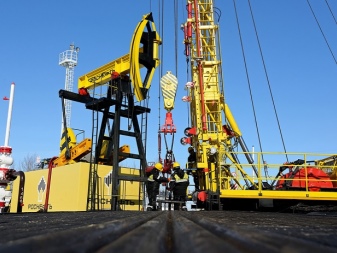
But drilling rigs are used, as strange as it may sound, in landscape design. This is especially true for work in rocky areas. Only drilling often allows you to get holes and blast rocks or hills, cliffs with precisely calculated charges.Drilling has to be done both when fixing bridges on river banks and when forming the main supports. In difficult cases, land is drilled for piles during the construction of houses and other capital structures.
Finally, drilling rigs are widely used in mining. Only they allow you to build an earthmoving tunnel below the surface. Injection wells allow supplying water and special solutions to a problem area. Control and observation drilling is carried out to monitor the effectiveness of reservoir development.
Pilot drilling allows you to give an overall assessment of the geological structure and production prospects in a fairly large geological area.
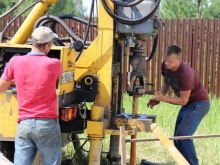
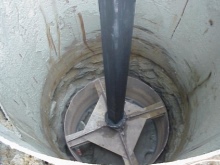
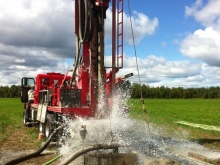
Views
Rotors
Rotary equipment can be used for drilling various types of wells, including drilling into water. The difference between the rotors lies not only in their power, but also in the permissible bore section. The depth can reach 1.5 km. Flushing is carried out with clay solution or water. The main properties of the rotary drilling method:
- higher speed than with percussive passage of the rock;
- versatility (the ability to handle both soft and hard rock);
- suitability for driving water intake workings with a cross-section of up to 1500 mm;
- minimum dimensions and metal consumption of equipment;
- the ability to transport the entire machine on mobile platforms;
- reduction of well production rate when using clay solutions;
- the need to bring clean water;
- increased cost in comparison with other options.
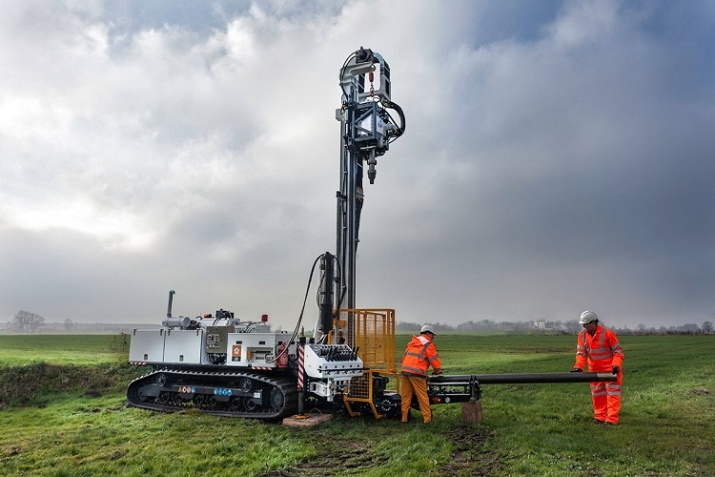
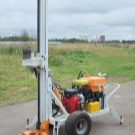
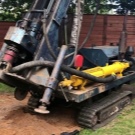
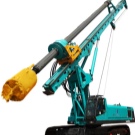
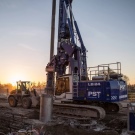
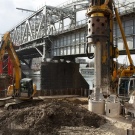
Carriages
Drilling carriages are very helpful where mobile equipment cannot cope. They are often installed even on excavators. SBL-01 is a good example. Using this technique, anchor piles can be placed. You can also:
- strengthen the slopes;
- drilling with flushing;
- perform auger drilling;
- pass the soil by pneumatic impact method.
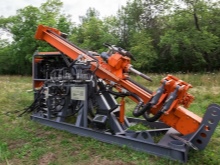


Winches
Such a system turns out to be the main part of the lifting complex of the drilling rig. With the help of winches, you can raise and lower drill, casing pipes. If necessary, the columns are supported in weight when it is necessary to perform certain work with them. Also winches:
- screw up and unscrew pipes;
- pull various tools and small auxiliary equipment to the drilling rig;
- put fully assembled towers in the working vertical.
A very important point is the classification of drilling rigs. The main classes of structures are specified in GOST 16293-89. Standardized:
- the level of load applied to the hook;
- conditional attainable depth;
- hook lifting rate - in the process of walking the string and without payload (measured in meters per second);
- estimated estimate of the power developed on the shaft;
- the minimum section of the hole in the rotary table;
- the calculated value of the drive power;
- height of the base of the machine.
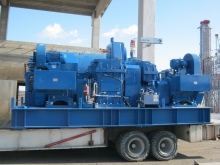
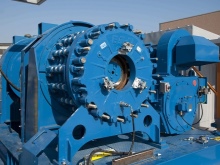
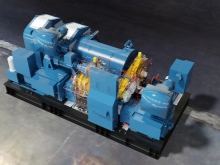
The tal system is very important. With its help, various drilling tools are lifted and suspended. If necessary, this unit has a point mechanical effect. For example, if you need to free the drill string from the well. A typical tackle system layout includes:
- traveling block proper;
- crown block;
- robust steel rope.
The crown block is always motionless. It is placed on the mast frame. Sometimes special under-crown-block elements (beams) of the drill tower are used. With the help of a rope, a stable, but at the same time flexible, mechanical connection between the winch and fixed parts is maintained. There are three key types of tackle complexes:
- with fixing the free part of the rope to the base;
- by connecting it to the crown block;
- with mounting on a talblock.

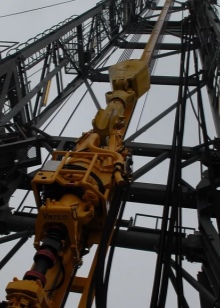
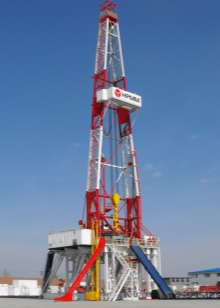
Whichever drilling methods are used, a circulation system must be used. It performs various manipulations with drilling fluid, from preparation to storage and use.If necessary, the solution is additionally cleaned from the cuttings mixed with it. Typically, the performance of circulation systems is provided by several rectangular containers. In any case, there is a separate standard for circulation - GOST 16350-80.
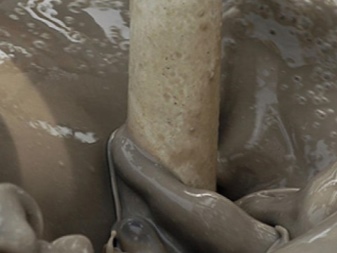
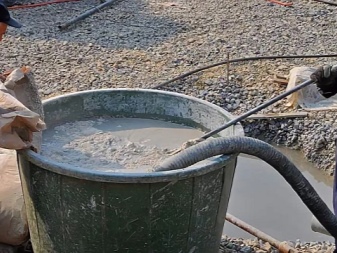
At home, hand-held drilling rigs are often used. The level of requirements for them is naturally lower than for mechanized systems. But even such equipment allows drilling water wells for private needs. It will also be possible to drill a channel under the piles, or equip the field for removing heat with a special heat pump.
If you have minimal welding skills, you can even make a manual system with your own hands - this technique serves for a long time.
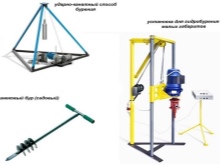
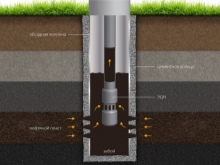
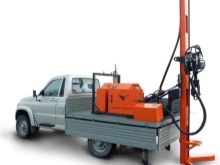
Modern crane and mounted drilling rigs are distinguished by more advanced characteristics. Usually they are assembled on the basis of on-board vehicles. Domestic ZIL, Ural and GAZ of various modifications turned out to be a very good basis. With this technique, you can mount poles and poles. Individual selection of the system layout for specific needs is allowed.
The gradation of drilling systems is also in terms of the level of power loss in the transmission. This indicator is determined:
- total generated power;
- the design of the machine;
- speed.
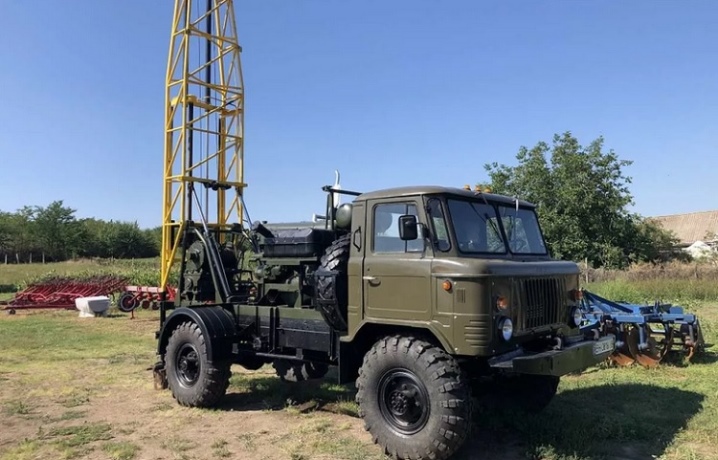
Drilling rigs are also subdivided according to the type of power plant. Diesel systems are used where stable power supply is impossible. Such drives are not very powerful, but they are characterized by increased mobility. In diesel-electric equipment, all structural elements are completely autonomous, which is very convenient. The main components will be:
- motor;
- a generator powered by this motor;
- a drive system that powers an actuator.
The electric rig can be powered from the mains power grid or from an external generator. It is very easy to commission such equipment, and therefore it is very popular. But electrical drilling equipment is inapplicable or limitedly applicable in hard-to-reach places. Diesel systems with a hydraulic component are easy to operate and operate on the basis of a turbo converter.
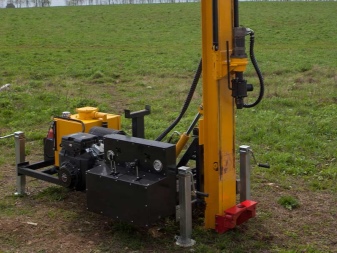
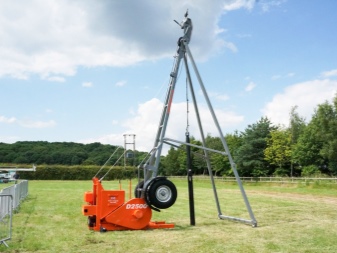
Jack-up drilling rigs are widely used in offshore conditions. The rise above the surface of the seabed and the sea is achieved by means of columns resting on the ground. The possibility of vertical movement of the columns in relation to the body is provided. The number of these supports, along with the design of the lower segment and the geometric shape, is an important classification feature. Non-self-propelled land systems can be divided into portable and trailed varieties. For the most part, portable devices are lighter.
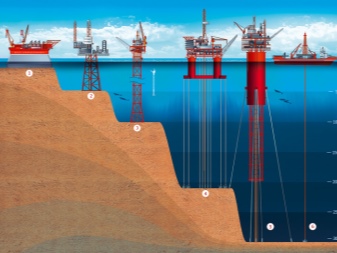
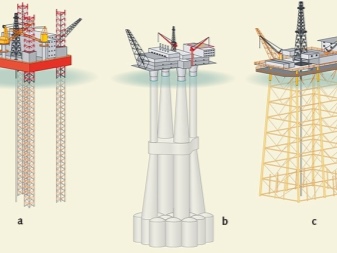
The auger drilling rig provides soil extraction from the borehole without interruption of work. The scheme is approximately the same as that of a conventional meat grinder. But the drill can overheat during very intensive work. As for the kinematic schemes, they differ in:
- the number of parts and control systems;
- share of technically complex nodes;
- features of shaft placement;
- the use of redundant circuits.
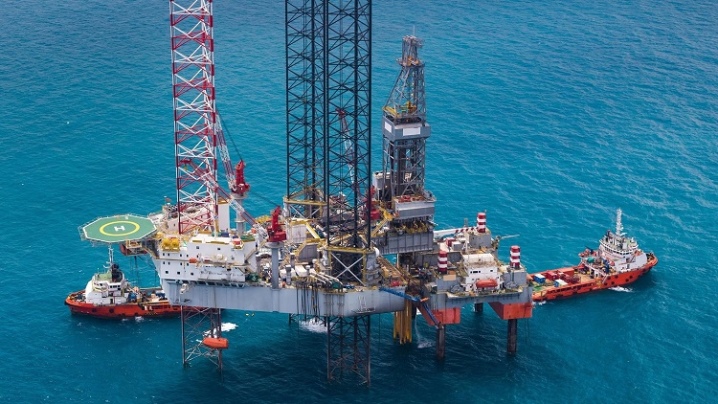
For oil production, stationary semi-submersible hardware systems are often exchanged. Their working depths range from 0.06 to 3.85 km. Engineers have already known 7 generations of semi-submersible equipment. The difference between them concerns not only the year of construction, but also specific technical characteristics. To build an underwater well, you need not only such a platform, but also a special drilling vessel.
Regardless of the technological features, the service life of the drilling rig (normative and calculated) is 10 years. The actual period of operation is also distinguished (after the normative and calculated period before the decision is made to withdraw from circulation according to the data of inspection, flaw detection).As for the depreciation period, it is strictly prescribed for drilling equipment by the order of the Ministry of Finance - 7 years.
Good cars are always equipped with safety systems. They allow you to avoid accidents and other incidents, even with a suspended load.
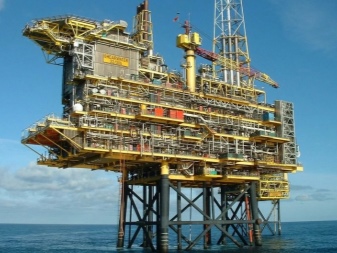
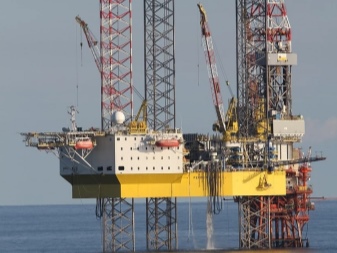
How to choose?
When choosing drilling rigs, the main parameters are the lifting capacity and the required depth of penetration of the earth layers. These parameters must meet the natural conditions of the area, the maximum degree of load on the road and the degree of arrangement of the territory. Be sure to pay attention to:
- climatic parameters of work;
- personnel qualifications;
- the possibility of drilling deep exploration wells and production wells or intended for drilling shallow structural and prospecting wells;
- type of top drive (power system);
- the likely maximum wind strength;
- drilling method;
- features of passable rocks;
- deep temperature;
- the degree of chemical aggressiveness of groundwater.
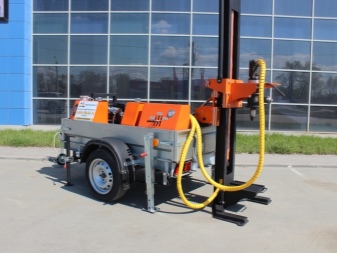
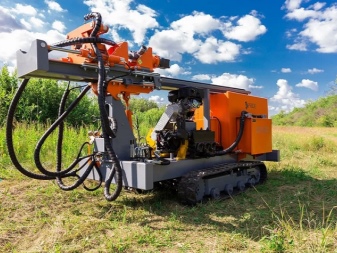
Mounting
The overwhelming majority of professionals use small-block, modular or small-block types of installation when commissioning a drilling rig. They follow the same tower installation techniques. First of all, the site needs to be leveled and excess plants removed from it. It is also worth getting rid of objects that can catch fire. Block-by-block layout implies the initial assembly of parts, which are subsequently connected already in place.
They begin with the installation of the assembled foundation and supports. The next step is to attach the rotor and winch bundle. In the last place, they put auxiliary equipment. Its composition is very diverse and should even be further analyzed.
Small-sized drilling rigs are usually delivered in a completely ready-to-use form, it remains only to put them on the base.
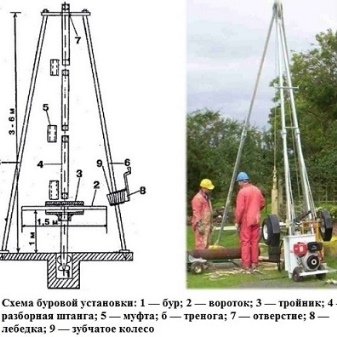
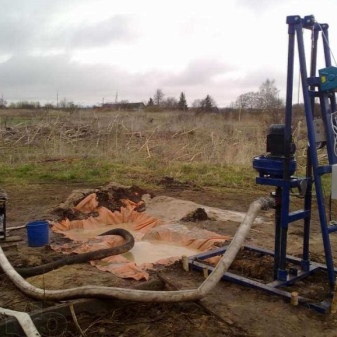
Stationary complexes are more difficult to mount. A serious problem is wiring, taking into account the required power and wiring rules. The aggregate technique is periodically used when working with installations of 9-11 classes. It is imperative to observe the "hook weight limit". Aggregate installation takes a lot of time, requires arranging a massive foundation, careful alignment of parts in space. In addition, a lot of materials are consumed.
The small-block approach is that they do not use foundations made of wood or rubble concrete, but a block-sled made of metal. They can serve as both a base and a vehicle. Installation, in essence, is limited only to the movement of the installation to the required point and its minimal preparation. The number of units, their capacity and other parameters are determined in advance, taking into account the existing needs and limitations. The small-block rig is widely used in exploration drilling, and in production drilling - only when transportation of large blocks is difficult. The problems are related to:
- difficulties in kinematic coordination of the mass of small blocks;
- great needs for tractors and other vehicles;
- the inability to deliver large drilling shelters and significant sections of communications.
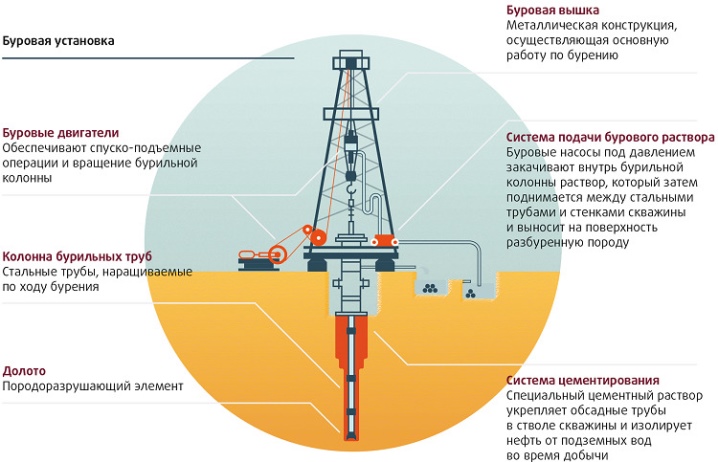
Maintenance
This procedure is divided into shift and technical care. Every shift should be in accordance with the operating instructions. They are necessarily carried out not only at the beginning and at the end of shifts, but also during an unplanned break in work. Maintenance is carried out when a certain time has been worked out. Physical condition and visual health are irrelevant for this procedure.
Maintenance and repair of the gearbox plays an important role. This component must be present on any type of drill. The reliable functioning of the main motor depends on its serviceability even in the extremely loaded mode, when driving "heavy" rock. Sometimes it is necessary to repair not only the gearbox itself, but also the electronic converter.Maintenance of the drilling swivel is necessary, first of all, in cases when the twisting of the necessary parts and / or the circulation of the fluid through the system is disturbed.
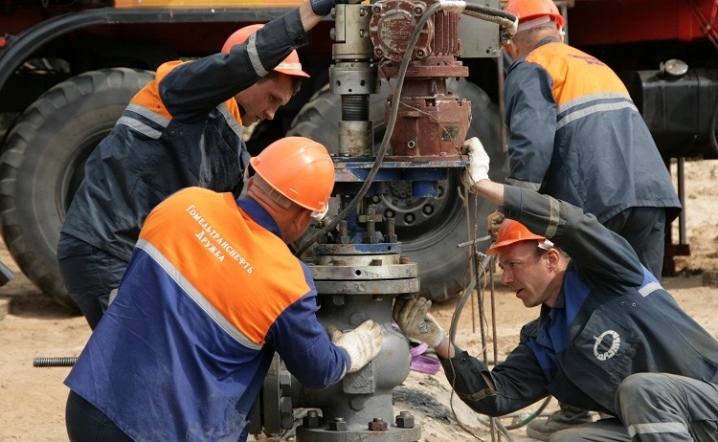
Attention should also be paid to the head rotators. Even the products of large proven firms can begin to fail over time. But if you have spare parts, you can repair any rotators, including the hydraulic type. As for electric drives, they must be checked according to operational safety standards:
- condition of drive transmission systems;
- centering of its units;
- stability of idling for at least 60 minutes;
- the quality of fastening the product to the support;
- tension of all belts, chains;
- condition of the lubricant.
Regardless of whether the drill stop is equipped with an auger or other type of tip, each time before starting work, it is necessary to assess the oil level and the tightness of all major fixtures. Twice a year at least, and with sudden changes in the weather and more often, they change the lubricant and other technical fluids according to the season. During major overhauls, the most thorough check is carried out.
All worn out parts and expired consumables must be replaced immediately. Therefore, a complete disassembly of the equipment and deep detailed diagnostics are needed.
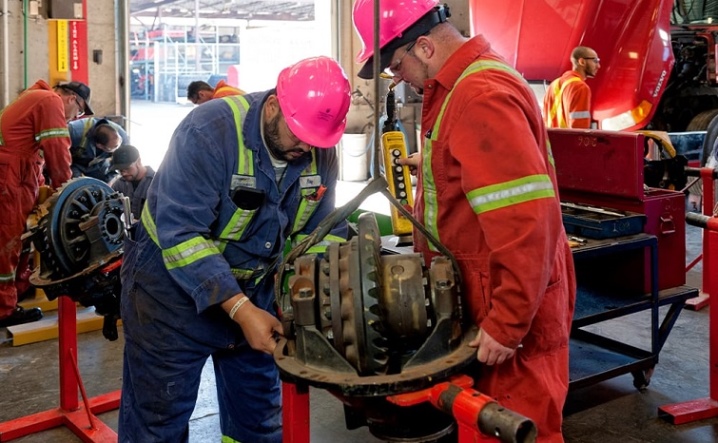
The comment was sent successfully.