How to make a hand drill with your own hands?
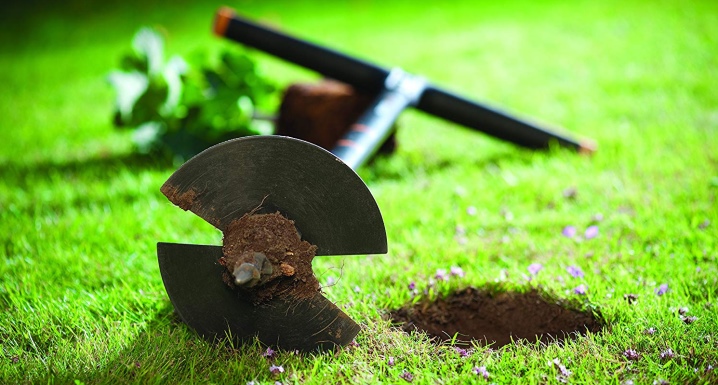
A carefully crafted, hand-made well drilling attachment is as functional as an industrial auger. Anyone can make an excavation drill on their own.
What materials are needed
The main alloy used as a starting material is steel. For the drill, round pipe and sheet steel are suitable. Pipe diameter is 3/4 to 1.5 inches. If it is not possible at the moment to get a pipe with a circular cross-section, it is permissible to use a professional pipe of a square or polygonal (regular polygon) cross-section. The square tube has sectional dimensions from 2 * 2 to 3.5 * 3.5 cm.
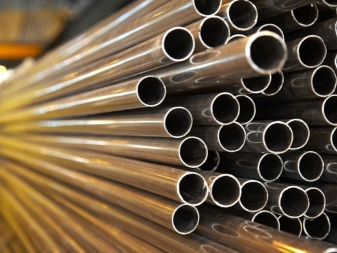
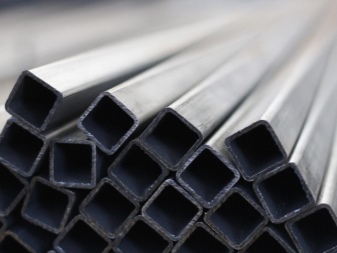
It is unacceptable to use a rectangular one, since the center of gravity is shifted. The use of a rectangular profile is difficult.
For paddle knives that cut the ground, sheet steel with a thickness of at least 3 mm is used. Thinner sheets bend, the geometry of the working part is violated, and the tool leads to the side, which is unfavorable for the operation of the drilling mechanism (drive).
If there is no access to a lathe (milling) machine, a circular saw for wood used on a grinder is used as the material for the blades. Cutting from scratch the blades for a drill is more difficult than using a ready-made disc. And if, as a source, the owner of the site already has a knife of the correct shape, centered at the factory, it is enough just to cut it in half. It may be necessary to sharpen the side edges to make the drill more efficient.
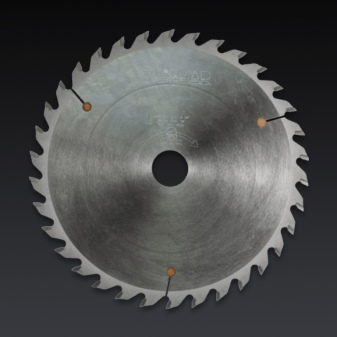
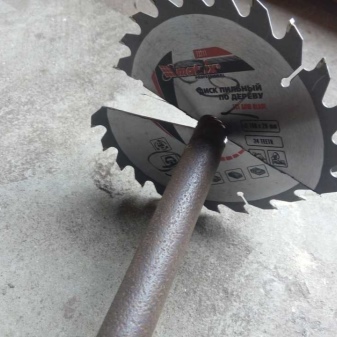
A peak drill, which sets the center of the circle, along which holes are drilled in the selected place, is made based on the end of the pin to which the cutting edges are attached. In the simplest case, the rod is already sharpened, and its end looks like a cone. It is allowed to cut grooves for a drill using a lathe.
Many craftsmen weld a ready-made short drill on concrete, carefully setting the center so that the tool does not drift to the side.

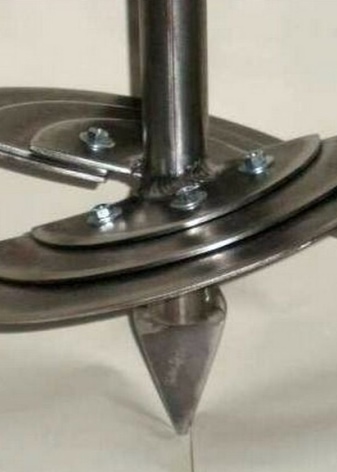
The handle of the drill is made from a round tube. Hand tools - T-shaped design: the worker rotates the drill with his hands behind the horizontal bar, simultaneously pressing on the product so that it enters the ground faster and more easily. For it, he pulls out the tool, cutting off and destroying part of the soil.
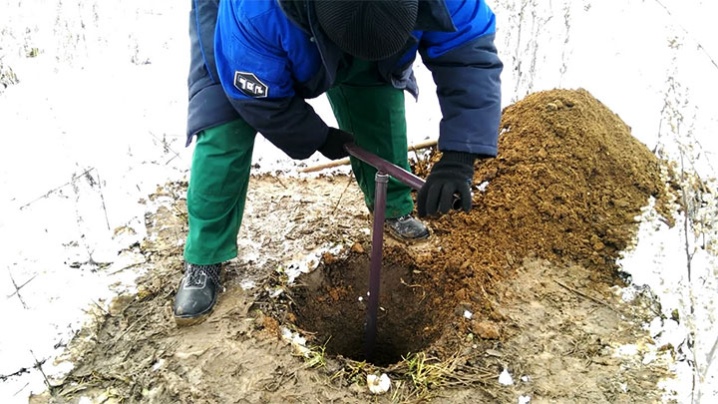
The drill, made for a powerful hammer drill, has an adapter for the chuck of the latter. In the simplest case, instead of a horizontal handle, another drill is welded to the rod for concrete (for the tip). At the same time, the shank is free - it is inserted into the perforator itself. The universal ground drill has both a perforator shank and a small transfer device, on which pipe sections of a suitable diameter are put on.

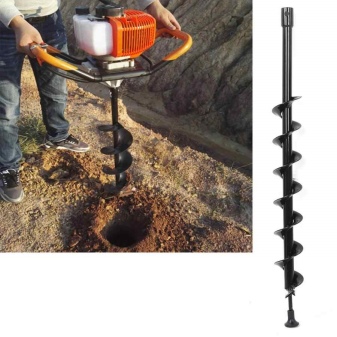
Instrument preparation
Having decided on the materials, prepare a set of the following tools:
- a welding machine (it is rational to use an inverter), electrodes and a protective helmet for the master's eyes;
- grinder and cutting wheels for metal, protective casing (prevents the scattering of metal shavings towards the worker);
- hand or electric drill with a set of drills for metal (both high-speed steel and diamond are suitable);
- hammer, pliers and vise;
- sharpening machine (craftsmen purchase a round sharpening stone with a shank inserted into a perforator or drill);
- construction marker, tape measure, compasses.
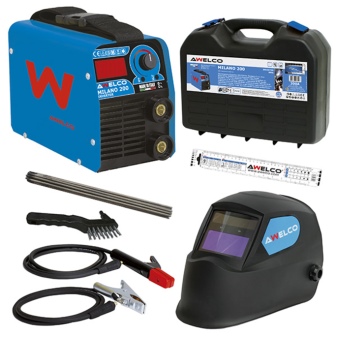
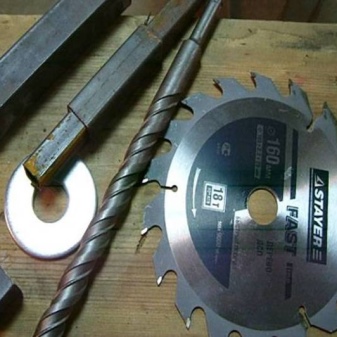
Before starting work, determine the characteristics of the yamobur. There are the following varieties:
- Simple (suburban) - in it, the cutting part includes two half-discs. They are installed symmetrically, with an inclination, on the axis opposite each other.
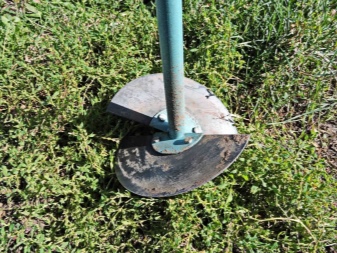
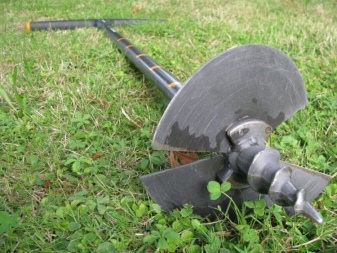
- Auger. A helical blade is twisted from a strip of steel in several turns. It is inseparable. It is imperative that the strip width, slope, bend curve along the entire length and the same spacing between the turns be kept constant. One inaccuracy and the drilling equipment will become unstable, leading to slowdown and runout when drilling the ground.
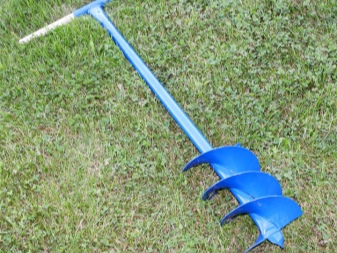
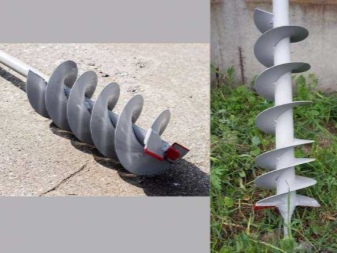
- Bur-wedge most often made from the working part of the shovel. The main principle of its action is not screwing the tool into the ground with the subsequent destruction of the latter, but wedging in and immediately throwing the cut soil out of the working area. The blades are located strictly vertically.
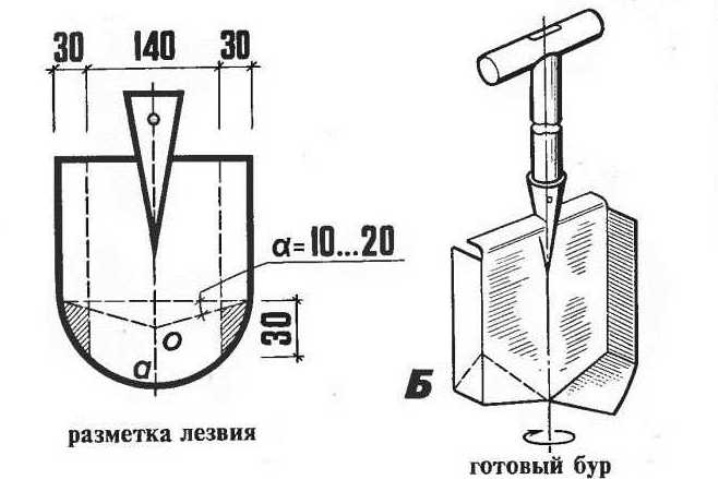
Drawings and dimensions
The product diagram is a template and allows you to visually estimate how the stages of the manufacturing process of the future tool are located. The sizes of the garden drill can be as follows:
- handle (if the product is hand made) - a crossbar with a length of 0.5 m;
- rod - about 1 m (without additional sections);
- diameter of the disc cut into pieces - 15-25 cm (reference point - ready-made saw blades for the grinder);
- tip length - up to 10 cm (lance or drill);
- the distance on the axle given for the installation of the disks (taking into account the slope), after the peak or drill - up to 15 cm;
- the angle of inclination of the knives up - up to 30 degrees.
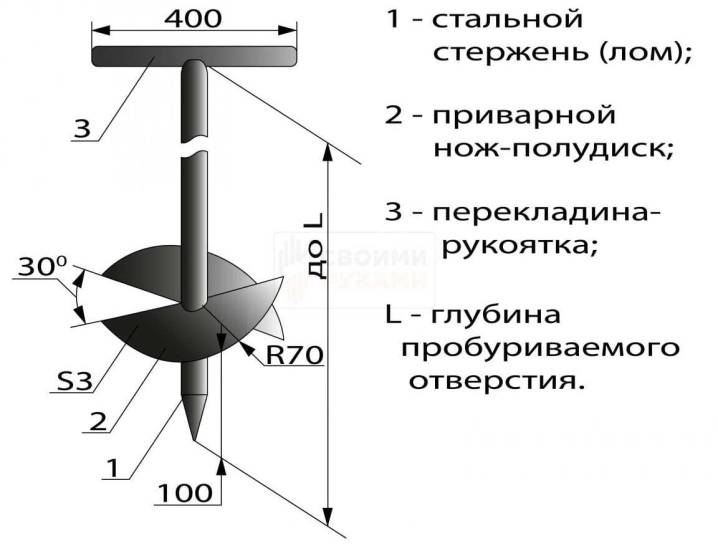
In auger auger, the length of the "screw" (monoblock in several turns) can reach up to half a meter. The inclination of the screw stroke can reach all the same 30 degrees (at any point of the monoblock). The rest of the auger auger is the same as a simple two-bladed.
The auger drill is more often used with a drilling mechanism, since it is much more difficult to manually rotate several turns than the only one in a simple drill.
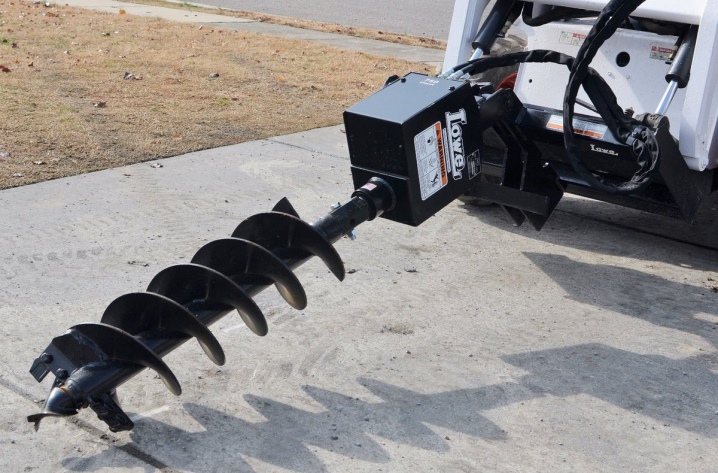
The dimensions of a drill for planting seedlings, for example, tomatoes, generally coincide with the dimensions of the working part of an ordinary bayonet shovel. Its cutting edges are trimmed so that the spade bayonet from a round one becomes straightened and sharpened at an obtuse angle. A sheet fold is cut from the opposite (upper) edge. A long (more than half a meter) concrete drill can be welded into the hole from which the handle is pulled out (for the universal clamp of the hammer drill). It is advisable to use a drill made from a shovel bayonet with a drive, since for manual drilling it requires more effort than an inclined screw auger or a half-disk of a conventional garden drill.
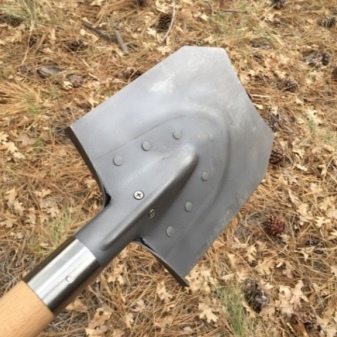
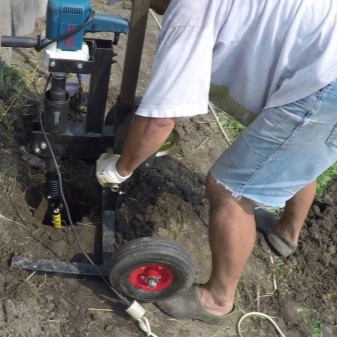
A drill of any type can be completed with additional sections. Each of them increases the depth of soil drilling by a meter. These extension sections are used when the owner decided to independently drill a water well. One such section is used when the ground is soft. These can be pillars for a fence and other non-capital structures, buried 1.4 - 2 m.
Having decided what kind of hole you need, cut out a sketch for the blades from cardboard. It became easier and faster to cut the sheet along it.
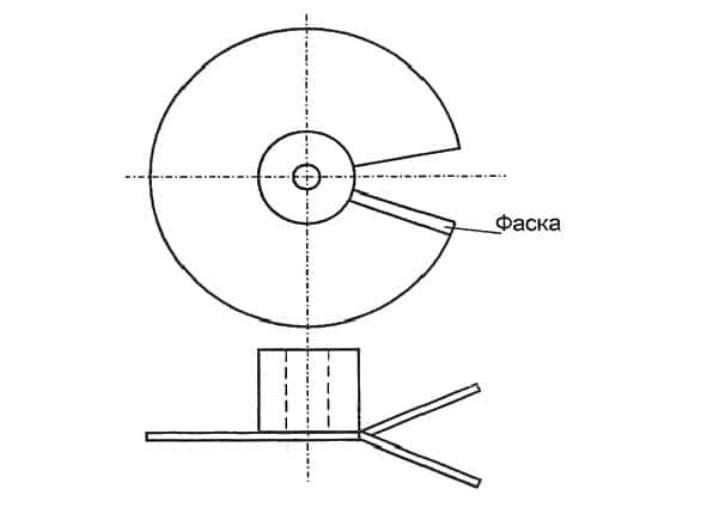
How to assemble a drill
The drill assembly provides for welded and bolted fasteners.
From the saw blade
The best solution is a diamond saw blade. It can even cut and crush small stones in rocky ground.
The disc may not be new - diamond discs are durable and have increased wear resistance.
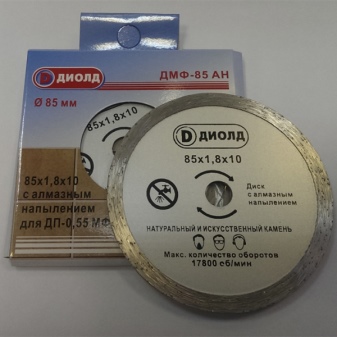
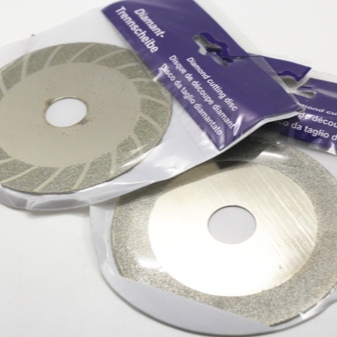
Circular saw blades are made from hardened sheet steel. A distinctive feature of hardened steel is low flexibility; it is preferable to divide such a disc into two halves.
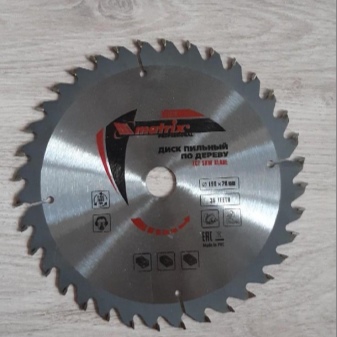
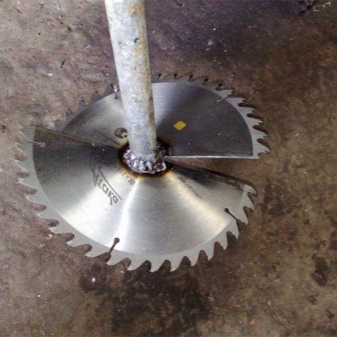
Saw the disc in half and secure the halves opposite each other by rotating them 30 degrees. It is impossible to cook hardened steel - it will lose its strength properties (high-temperature tempering). It is recommended to secure the disc halves with bolts. Both diamond and hardened steel discs cannot be welded.It is difficult to cut a diamond disc without the help of a machine, without disturbing the spraying,
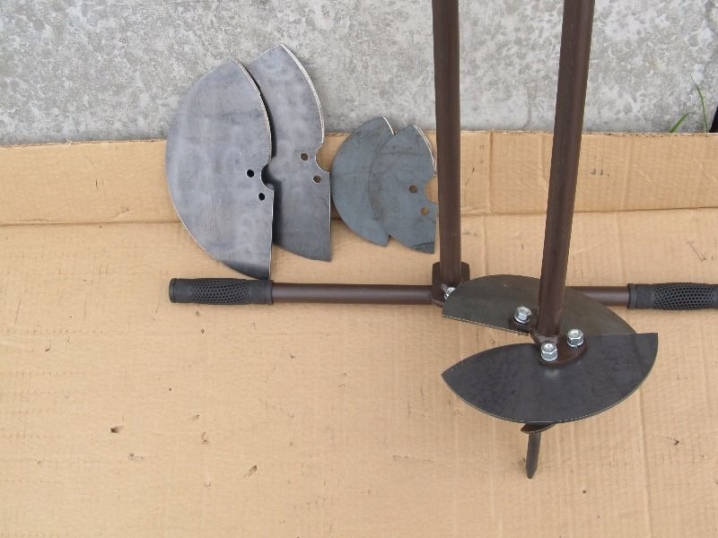
Sheet steel
To assemble a removable drill (including for a summer cottage) with detachable blades, do the following:
- On one side of the axle, weld the landing pads from thicker (4 or more millimeters) sheet steel. They should have a divergence angle of 25-30 degrees.
- Drill holes in each of the platforms and future removable blades, for example, for M10-M12 bolts.
- Align the blades with the axial platforms and secure.
This mount is more suitable for drilling in dense soil, almost entirely consisting of compressed clay. The platforms for removable blades allow the use of cutting parts made of hardened steel, which has several times higher resistance to deformation compared to conventional black steel.
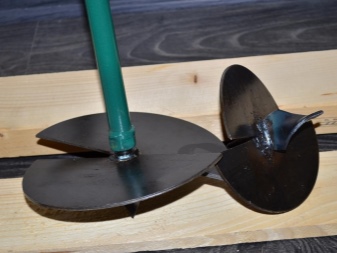
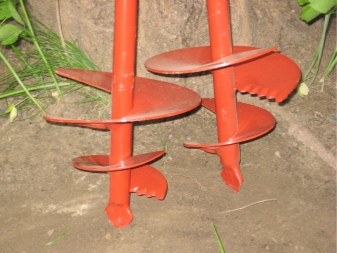
Welding and finishing
The general sequence of steps for making a welded drill can be as follows:
- mark pipes and steel sheets according to the drawing (using a construction marker);
- saw them according to these marks using a grinder;
- make marks at the joints of the handle, axis and blades (the pipe of the axis of the future drill should enter the newly cut blades without noticeable effort);
- using a welding machine, weld these parts in the required sequence, observing the drawing proportions and dimensions.
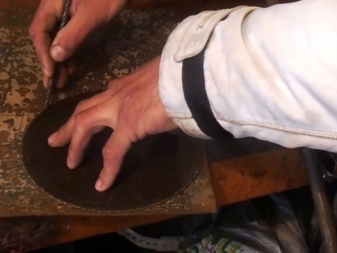
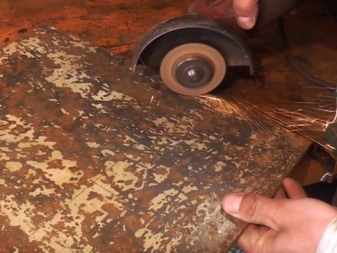
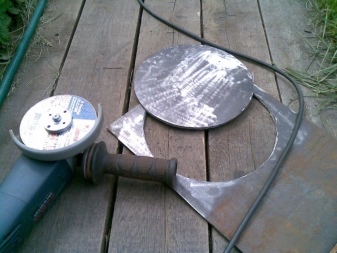
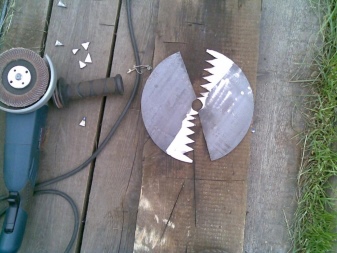
The final processing of a homemade drill is as follows:
- Grind the drill - get rid of burrs, trim the welds (if unevenness remains). The tidy tool is easy to use, does not hurt hands and does not cling to overalls.
- Put on the handle (if the drill is hand-held) hose sections. The ends of the horizontal bar (gate) must be forced into the hose.
- Sharpen the cutting edges. This will allow you to more efficiently drill the ground.
- Paint the tool after fabrication.
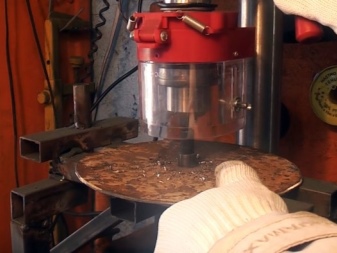
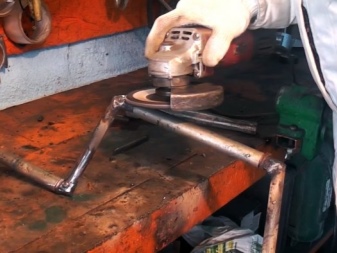
It is best to use a rust primer, especially when the material (pipes, sheet steel) is not completely new.
Any paint dries in a maximum of two days. The product is ready for use.
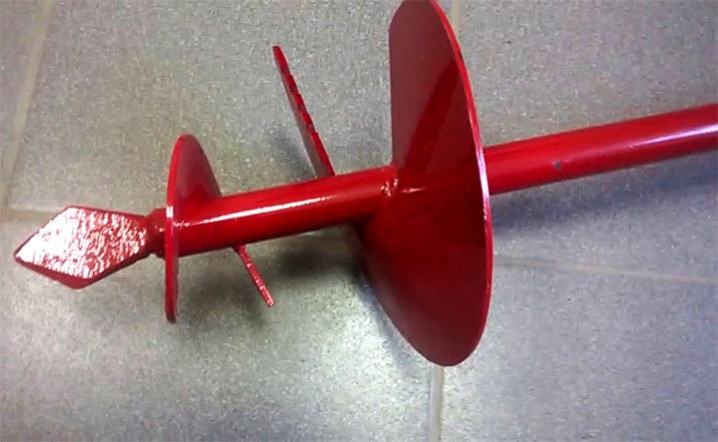
Follow-up care
Extension sections designed for deep drilling are assembled before work and disassembled immediately after work is completed. It is advisable to lubricate all bolted and coupling joints of the drill and additional sections regularly - oil or grease will not let them "stick" to each other. If the drill enters the ground tightly, then its blades and cutting edges are cleaned of adhering clay and wound roots, which noticeably impede the advancement of the tool during drilling.
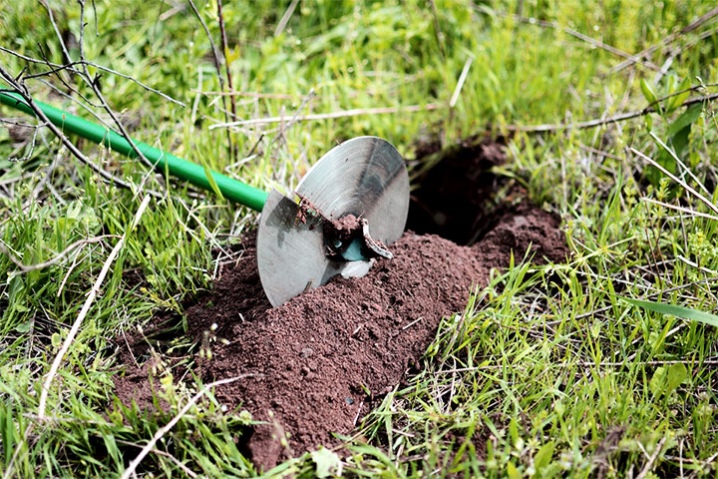
You can see a visual overview of how to create a hand drill with your own hands in the following video.
The comment was sent successfully.