Features of PDC bits
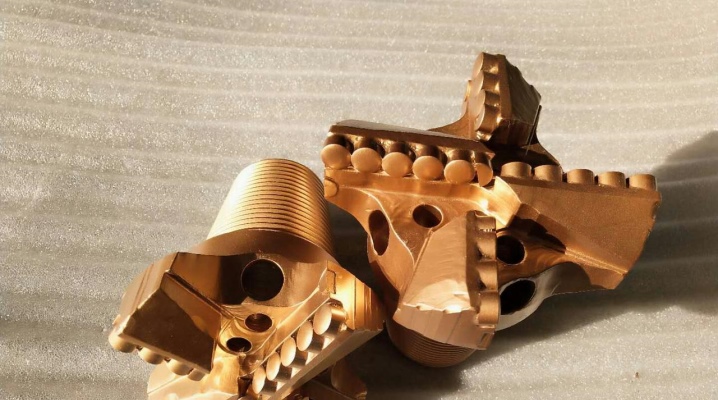
The drilling tool is used both in everyday life, when organizing wells, and on an industrial scale, when it is necessary to drill out a rock.
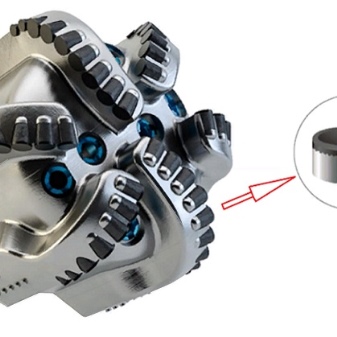
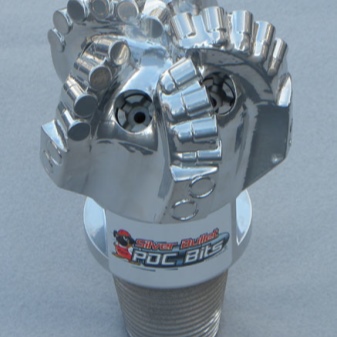
Design and purpose
First of all, diamond PDC bits are used for drilling with compact rigs, when it is not possible to provide the required load when drilling with a roller cone unit. It is important to apply less supply pressure at a comparable or higher rotation speed.
This drilling equipment has an efficient rock breaking mechanism. The drilling itself is performed after coring. It is possible to use it to organize wells.
Due to the inaccessibility of movable components of the bits of this type, when compared with roller cone bits, there is no risk that part of the tool may be lost, and all due to the highest wear resistance. At the same time, the service life at absolute load is 3-5 times longer.
Drilling with the indicated equipment is quite possible in rocks from malleable to hard and even abrasive. The principle of operation is easy to understand if you think about the design features of the installations. Since the destruction of the rock is observed by the cutting-abrasive method, which, in fact, is much more effective than other methods, the rate of penetration in pliable soils is higher. This indicator may be 3 times higher than that established with other methods.
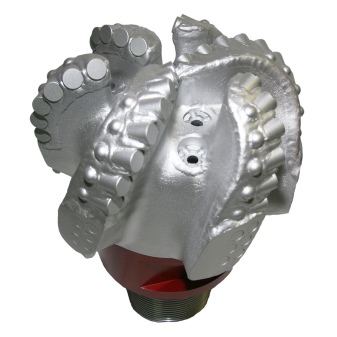
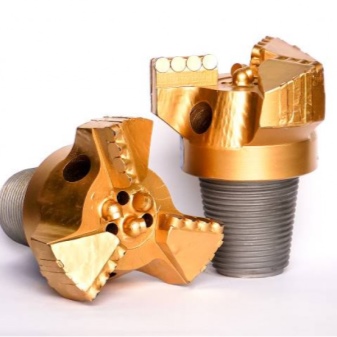
A similar effect is achieved due to the special housing and the materials used from which the cutting mechanism was made.
The cutters of these bits can be self-sharpening. They are also on a carbide base covered with a layer of polycrystalline diamond. Its thickness is 0.5-5 mm. The carbide base wears out more quickly than polycrystalline diamonds, and this keeps the diamond blade sharp for a long time.
Depending on the rock to be drilled, the bits of this group can be:
- matrix;
- with steel body.
The metal case and the matrix have all the chances to surpass each other in some points. From the first, for example, the method of fastening the cutting elements depends. In the matrix tool, they are also soldered into the system using a simple solder.
To install cutting elements in steel, the tool is heated to a temperature of 440 ° C. After the structure cools down, the cutter is firmly seated in its place. Cutters are manufactured in accordance with GOST. The decoding of the marking is carried out according to the IADC code.
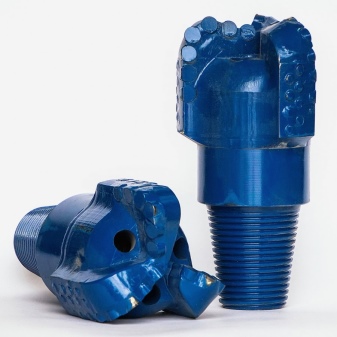
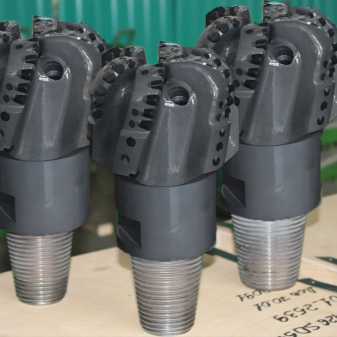
Advantages and disadvantages
It is definitely worth mentioning the pros and cons of the products in question. Benefits:
- wear resistance;
- high efficiency in some soils;
- there are no moving elements in the structure;
- the supply pressure is reduced.
But there are also significant drawbacks that need to be mentioned. Among them:
- price;
- more energy needs to be applied per turn of the bit.
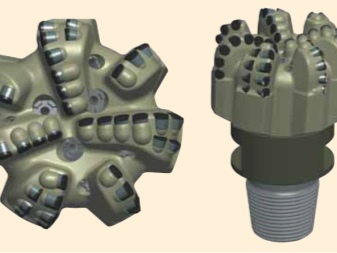
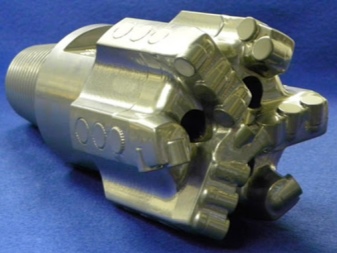
Classification and labeling
The marking on the described tool is represented by four symbols, which, in turn, mean:
- frame;
- what kind of rock can be drilled;
- the structure of the cutting element;
- blade profile.
Body types:
- M - matrix;
- S - steel;
- D - impregnated diamond.
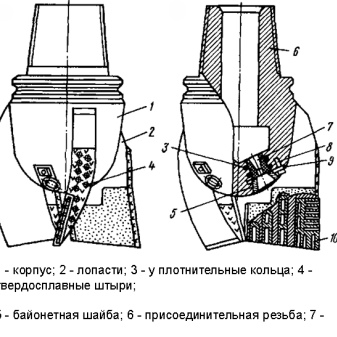
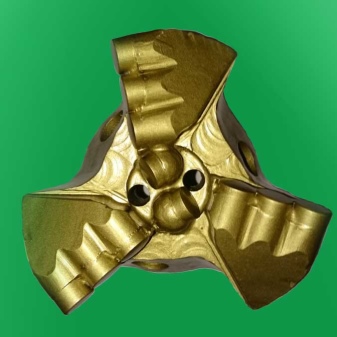
Breeds:
- very soft;
- soft;
- soft-medium;
- medium;
- medium-hard;
- solid;
- strong.
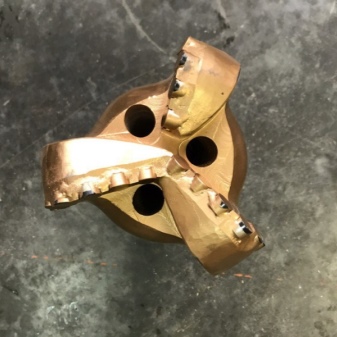
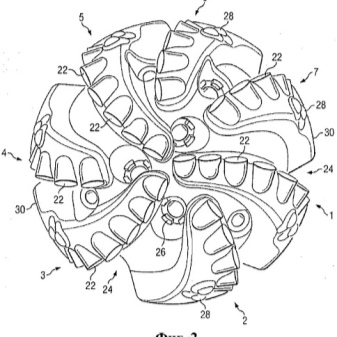
Structure
Regardless of the breed being worked, the cutter diameters can be:
- 19 mm;
- 13 mm;
- 8 mm.
Sizes are prescribed in GOST, there are also bicentric models.
Profile:
- fish tail;
- short;
- average;
- long.
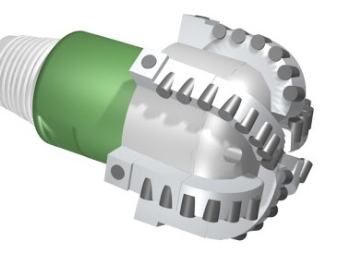
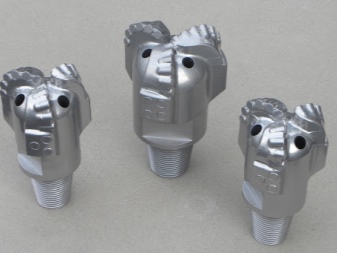
Manufacturers
The production of such bits is now on a grand scale. The most popular are the Silver Bullet with a flat profile.
This tool is distinguished by high performance. Scope of application - pilot drilling on horizontal directional projects. A large area is covered with this type of bit. The unit perfectly copes with the cement plug and is suitable for the installation of a geothermal probe.
Moto-Bit is another equally popular brand. These bits do an excellent job of working with a small downhole motor. They are widely used in the organization of wells.
When it is necessary to work with composite plugs, it is advised to use Plugbuster bits. Their main distinguishing feature is a special tapered profile, which has been patented. Compared to other similar tools, this one stays in the hole longer and can be used at a higher RPM. The sludge is small. The chisel is made of nickel alloy steel.
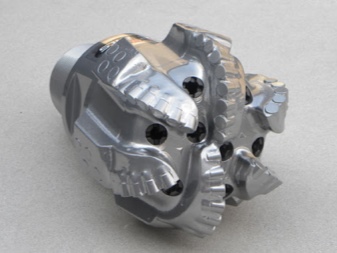
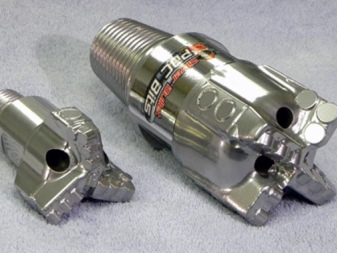
When drilling geothermal wells, Mudbug bits are often used, which are considered a versatile tool with high productivity. They have been designed to handle large amounts of mortar.
Wear codes
The IADC wear code contains 8 positions. The established sample card looks like this:
I |
O |
D |
L |
B |
G |
D |
R |
1 |
2 |
3 |
4 |
5 |
6 |
7 |
8 |
In this case, I - describes the internal elements of the weapon on a scale:
0 - no wear;
8 - complete wear;
O - outer elements, zero and eight mean the same;
D - a more detailed description of the degree of wear.
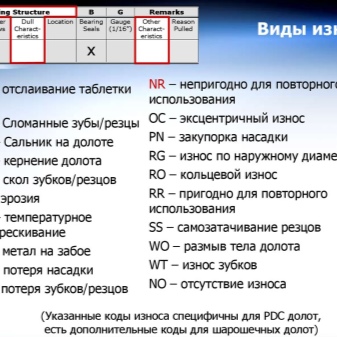
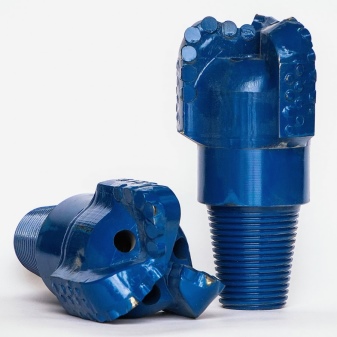
BC |
scrap cutter |
Bf |
scraping the diamond plate along the seam |
BT |
broken teeth or cutters |
BU |
chisel seal |
CC |
crack in the cutter |
CD |
loss of rotation |
CI |
cones overlap |
CR |
punching a bit |
CT |
chipped teeth |
ER |
erosion |
FC |
grinding of the tops of the teeth |
HC |
thermal cracking |
JD |
wear from foreign objects at the bottomhole |
LC |
loss of cutter |
LN |
loss of nozzle |
LT |
loss of teeth or cutters |
OC |
eccentric wear |
PB |
damage on trip |
PN |
nozzle blockage |
RG |
outer diameter wear |
RO |
ring wear |
SD |
chisel foot damage |
SS |
wear of self-sharpening teeth |
TR |
bottomhole ridging |
WO |
rinsing the instrument |
WT |
wear of teeth or cutters |
NO |
no wear |
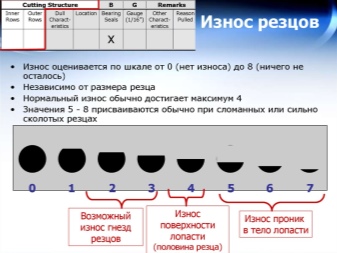
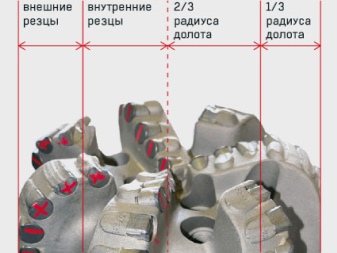
L - location.
For cutters:
"N" - nasal row;
"M" - middle row;
"G" - outer row;
"A" - all rows.
For a chisel:
"C" - cutter;
"N" - top;
"T" - cone;
"S" - shoulder;
"G" - template;
"A" - all zones.
B - bearing seal.
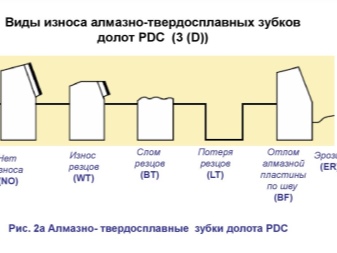
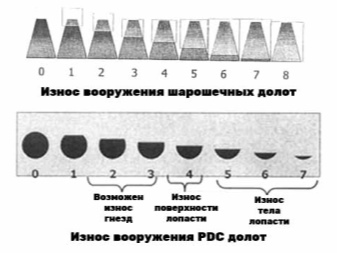
With open support
A linear scale from 0 to 8 is used to describe the resource:
0 - resource is not used;
8 - the resource is fully used.
With sealed support:
"E" - seals are effective;
"F" - seals are out of order;
"N" - impossible to determine;
"X" - no seal.
G is the outer diameter.
1 - there is no wear on the diameter.
1/16 — Wear 1/16 in. In diameter.
1/8 — Wear 1/8 ”in diameter.
1/4 — Wear 1/4 ”in diameter.
D - minor wear.
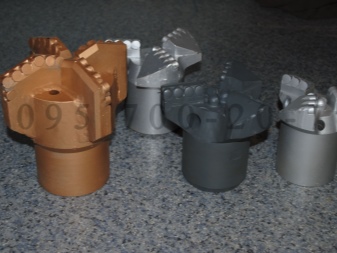
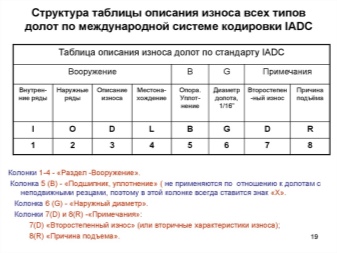
"BC" - scrap cutter.
"BF" - scrap of a diamond plate along the seam.
"BT" - broken teeth or cutters.
“BU” is the gland on the bit.
"CC" - a crack in the cutter.
"CD" - cutter abrasion, loss of rotation.
"CI" - cones overlap.
"CR" - punching the bit.
"CT" - chipped teeth.
ER stands for erosion.
"FC" - grinding of the tops of the teeth.
"HC" - thermal cracking.
"JD" - wear from foreign objects at the bottom.
“LC” - cutter loss.
"LN" - nozzle loss.
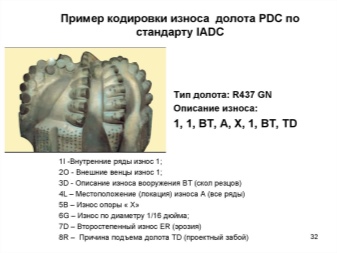
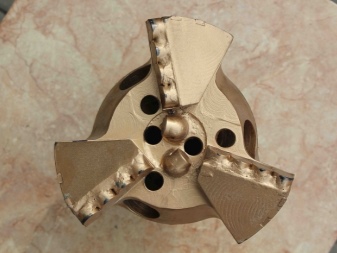
"LT" - Loss of teeth or cutters.
"OC" stands for eccentric wear.
"PB" - damage during trips.
"PN" - nozzle blockage.
"RG" - Outside Diameter Wear.
"RO" - annular wear.
"SD" - damage to the bit leg.
"SS" - wear of self-sharpening teeth.
"TR" - formation of ridges at the bottom hole.
"WO" - instrument rinsing.
"WT" - wear of teeth or cutters.
"NO" - no wear.
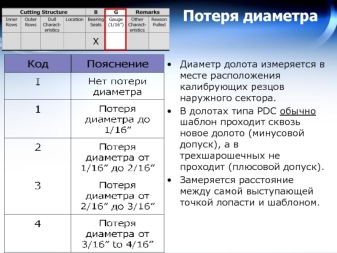

R is the reason for lifting or stopping drilling.
"BHA" - BHA change.
"CM" - drilling mud treatment.
"CP" - coring.
"DMF" - Downhole Motor Failure.
"DP" - cement drilling.
"DSF" - drill string accident.
"DST" - formation tests.
"DTF" - Downhole Tool Failure.
"FM" - a change in the geological setting.
"HP" - accident.
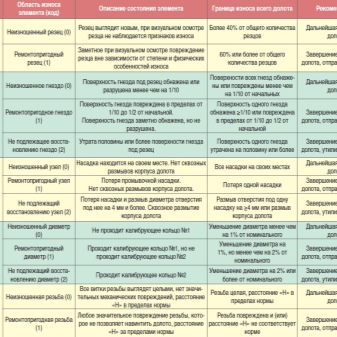
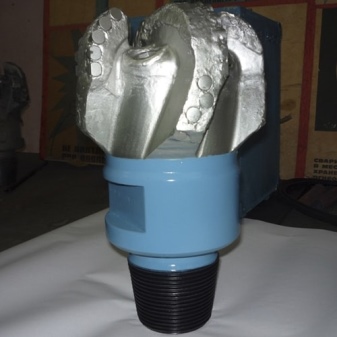
"HR" - rise in time.
"LIH" - tool loss at the bottom hole.
"LOG" - geophysical research.
"PP" is the rise or fall in pressure across the riser.
"PR" is the drop in drilling speed.
"RIG" - equipment repair.
"TD" is the design face.
"TQ" - torque rise.
"TW" - tool lapel.
WC - weather conditions.
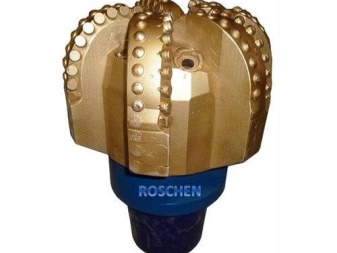
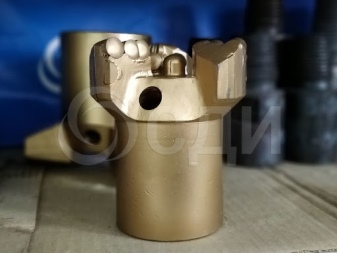
Features of PDC bits in the video below.
The comment was sent successfully.