All about the size of the bar

Today there is no need to convince that having your own country house or summer cottage, if not an urgent need, is desirable for every family. Wooden houses are especially popular. The list of proposals for finished houses and plots for construction is constantly growing.


Standard sizes
One of the most demanded building materials is timber. It is distinguished from other types of sawn timber by its dimensions - according to GOST 18288 - 77, it has a height and width of at least 100 mm. Its parameters are regulated by another standard - GOST 24454-80 "Softwood lumber: dimensions", which contains a range of standard sizes.
The most common timber comes in sizes 100 x 100, 100 x 150, 150 x 150 mm.

Length
The nominal dimensions of the length of sawn timber are established by GOST 24454-80: from 1 to 6.5 m with a graduation of 0.25 m. In practice, there is a wide range of values: more often than others, a six-meter bar is produced, but a bar with a length of 7 meters can be made to order. The maximum length of the material produced is 18 meters (for laminated veneer lumber).


Thickness
The most simple thickness is determined for two-edged and three-edged beams. For a square four-edged section, the thickness is equal to the width, for a rectangular section, the thickness will be measured on the smaller side.
According to GOST 24454-80, timber is made with a thickness of 100 to 200 mm with a step of 25 mm and a thickness of 250 mm.


Width
The width can be from 100 to 250 mm in 25 mm increments and must be equal to or greater than the thickness. The most common is 150 mm.

Calculation features
Modern woodworking technologies offer three types of timber:
- whole;
- profiled;
- glued.
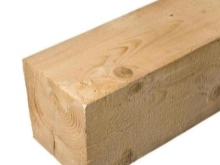


Solid timber is the most popular material for building a house. It is obtained in an extremely simple way: on a sawmill, four parts are sawn off from a log to obtain a square or rectangular cross-section and dried, as a rule, in natural conditions (humidity 20%). The bar can be:
- two-edged, when two opposite faces are processed, and the other two sides are left untreated;
- three-edged, when two opposite faces are processed and one perpendicular to them;
- four-edged - a timber in the most familiar form, which has faces on all four sides.
Working with this material does not require high qualifications, in addition, it is relatively inexpensive and not in short supply. At the same time, when starting to work with a solid bar, it is necessary to take into account its peculiarities.


Drying of the tree lasts for a year or more, so the formation of cracks and distortions is inevitable, in addition, due to the impossibility of ensuring a snug fit of each structural element of the house, the walls are blown through, even despite the presence of jute or tow. These circumstances force the exterior cladding of the house to be made using siding, blockhouse and other materials, which significantly complicates the work and increases the value of the house. An important point is the possibility of a fungus affecting raw wood, therefore treatment with an antiseptic solution is necessary.
Profiled beams are made on specialized woodworking machines, which provide not only high dimensional accuracy, but also create a special profile for tight fit of the elements to each other. Its main advantages:
- almost complete absence of blowing through the walls;
- attractive appearance (planed walls do not require additional processing);
- good weather resistance (a planed surface, unlike a sawn one, is less prone to getting wet and absorbs water worse).


If the enterprise that produces the profiled timber ensures its drying up to 3% moisture content, there are no difficulties - the walls are smooth and do not require insulation. Nevertheless after assembling the house, it takes about a year for settling and shrinkage, and at this time small cracks may appear.
Glued laminated timber is produced by joining several layers - lamellas with glue and then removing excess wood. The number of lamellas depends on the thickness of the product and varies from two to five. Manufacturing accuracy is higher than that of profiled timber, in addition, the possibility of skewing during drying is excluded - the house is ready for use almost immediately after assembly.
Today it is the best technology for the construction of wooden houses, but the cost of the material exceeds not only solid, but also profiled timber.


Calculation of material for solid timber
To accurately calculate the amount of material required for the construction of a traditional log house, it is necessary to have a project on the basis of which the volume of lumber that will be needed for the construction of finished walls is calculated - this is an ideal theoretical calculation. In practice, one has to face a number of circumstances that affect the actual amount of timber required:
- the quality of the material;
- shrinkage;
- accounting for door and window openings.
Among the purchased bars, as a rule, there are substandard ones: rotten, with black knots, cracks, etc., therefore, when buying, you need to ensure that their number is minimal.

When calculating the height of the log house, it is necessary to take into account that during drying, the wood shrinks, amounting to 4 - 8% of the original size. However, the manufacturer often cuts fresh, practically not dried wood. This can cause an increase in the percentage of shrinkage up to 10 - 12%.
You can often find a recommendation to subtract the size of window and door openings from the volume of the walls. The authors of these tips forget that when laying a log house, door and window openings should not be left free. The opening is indicated at a height of 2 - 3 crowns, and then it must be covered with a solid crown - and so on to the entire height of the opening.
Thus, when building a house from a solid bar, it is recommended to have a material reserve of 10-15% of the estimated volume of the walls.


Calculation of material for profiled and glued beams
When using a profiled bar, the calculation of the required amount of material can be made much more accurately. The likelihood of substandard products entering the batch is significantly lower, which is associated with its high price and relatively high production culture. High-quality profiled timber is made from dried wood and, as a result, has a shrinkage percentage of 1.5-2%.
Glued laminated timber practically does not shrink. Due to the high processing accuracy and the presence of profiled mating surfaces, door and window openings do not require periodic overlap, as when using a solid sawn timber. In general, the safety factor of the material when using profiled and glued beams is sufficient to take within 2 - 4%.

What size to choose for construction?
Purpose of the building
The size of the cross-section of the timber is dictated, first of all, by the purpose of the house. For a summer house, a section of 100x100 mm or 100x150 mm is sufficient (with the formation of a wall with a thickness of 100 mm). For a one-story residential building, walls with a thickness of 150 mm or more are required. The thermal calculation of the wall thickness will certainly give a greater thickness, but it must be borne in mind that walls made of ordinary sawn timber must be insulated and protected from blowing, therefore, the size of 150x150 mm can be considered optimal.For a two- and three-storey house, the wall thickness must be increased to 175-200 mm. This has more to do with the stability of the walls, especially during the assembly process.
The type of wood from which the timber is sawn depends on the financial capabilities and personal preferences of the customer. Pine can be considered optimal. It is undesirable to use fir due to its low resistance to decay, but if the foundation is planned to be high, then this is not critical.
In addition, in any case, it is recommended to treat the lower crowns with compounds that protect the wood from dampness, fungus and decay.
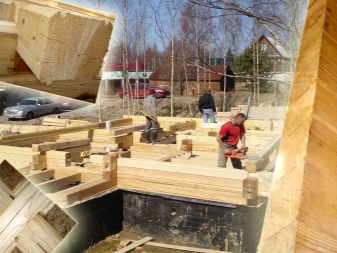

Floor and ceiling fabrication
When building from a bar, not only walls are erected, but logs for the floor and ceilings for the ceiling are made. When laying the floor, it is necessary to take into account temperature and humidity differences, therefore, the length of the timber should be taken 20-30 mm less than the nominal size of the room. It is recommended to use a rectangular material as a lag. The approximate width to length ratio should be 1.5 / 2.0.
When buying a timber for the floor, it is important to monitor the quality of the material - you cannot use deformed timber, since it will be impossible to lay a flat floor on such a basis. Humidity is of no less importance - exceeding the value of 15 - 18% will subsequently inevitably lead to warpage. It is strictly forbidden to use material with signs of decay and a large number of knots, as this will lead to a sharp decrease in bending strength.


The beam for ceiling slabs should not be inferior in quality to the material for the logs. A beam with an aspect ratio of 1.4 / 1 with a length of not more than 6 m is used on the ceiling. If it is required to cover large rooms, intermediate supports should be installed. The step between the beams is taken no more than 1.2 m. As a rule, it is dictated by the size of the sheets of heat-insulating material.
Profiled and glued timber on the ceiling looks very attractive, so it is not necessary to hide it under a suspended or suspended ceiling - there are modern options for combining timber with clapboard, blockhouse, etc.
Modern manufacturers offer a wide range of sawn timber products, and each consumer, focusing on their financial capabilities, can choose the appropriate option.

The comment was sent successfully.