How to make a concrete mixer with your own hands?
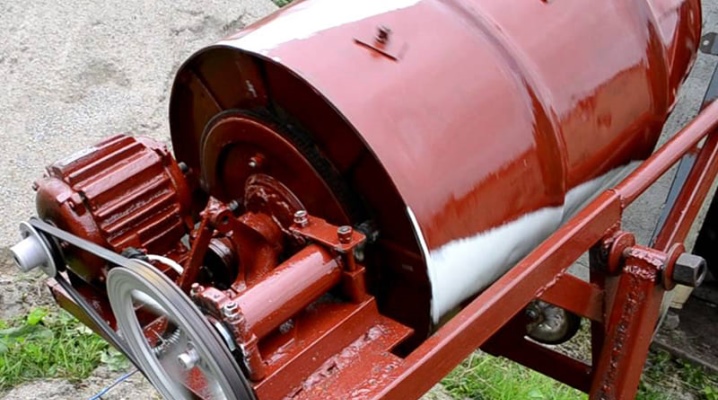
Construction of buildings and other structures is often associated with the use of concrete mix. Mixing the solution with a shovel on a large scale is impractical. It is more convenient in this situation to use a concrete mixer, which can be bought in a specialized store or made with your own hands. A homemade concrete mixer is an excellent alternative to a purchased unit with less cash costs.
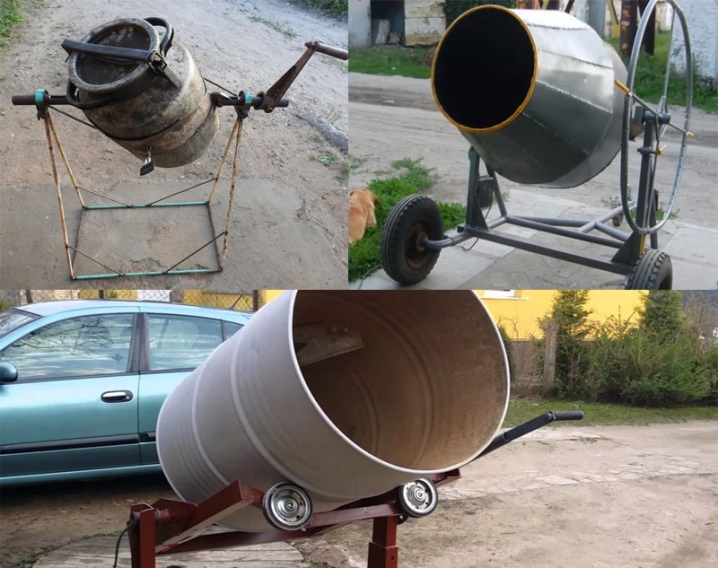
Drawings and designs
A popular option is a mechanical concrete mixer, which has a significant volume. In this case, the drive can be manual or electric. To unload the concrete, you need to tilt the bucket to the side. For all structures in the shape of a cylinder, the main drawback is inherent - poor mixing of the mixture in the corners. Also at 35 rpm, the mixture is sprayed. But this problem can be eliminated by welding the cut part back onto the barrel and drilling a small hatch.
Such an aggregate is capable of mixing a simple solution in about five minutes, a dry mixture up to 12 minutes.
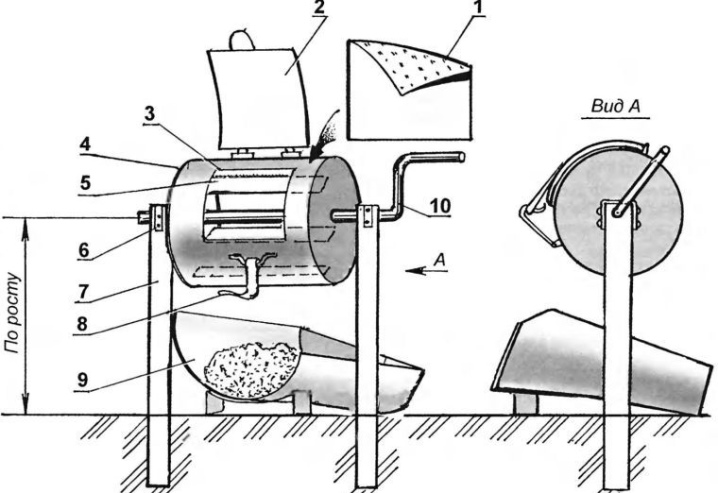
The second option is a combined horizontal type unit with combs. There are also two varieties: manual and electric. The main advantage is homogeneous mixing of concrete, as well as good speed and quality. The unit is made from a barrel, for example, 500 liters, and in quality it is not inferior to modern models. The mixing speed does not depend on time, but on the number of revolutions. To prepare the concrete mixture, it is necessary to make only 3-4 turns. Among the disadvantages is the complexity of the design. To make it by hand, you will need a considerable number of auxiliary elements. When constructing an unloading door, it is important to use only quality parts.
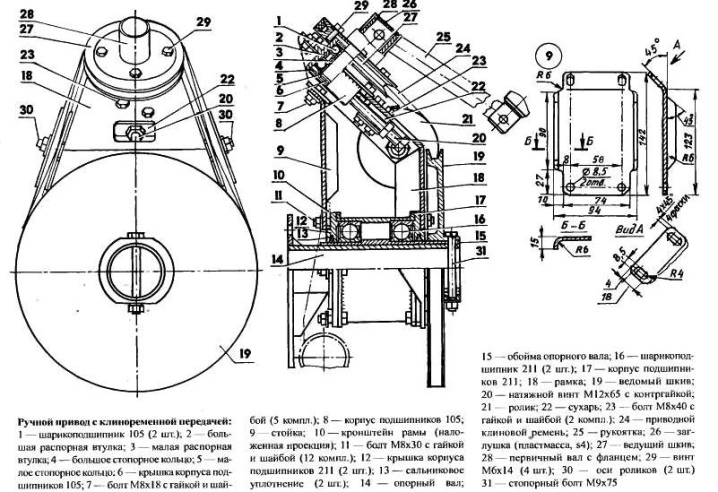
The third option is electrical construction. Basically, this model is copied by home craftsmen. Depending on the selected drawing, the finished concrete mixer differs in some details. The neck and bottom must be secured with strips that are welded with a cross. It is recommended to assemble the device so that the bucket rotates with the axle.
It is more difficult, but thanks to this design, the service life is increased.
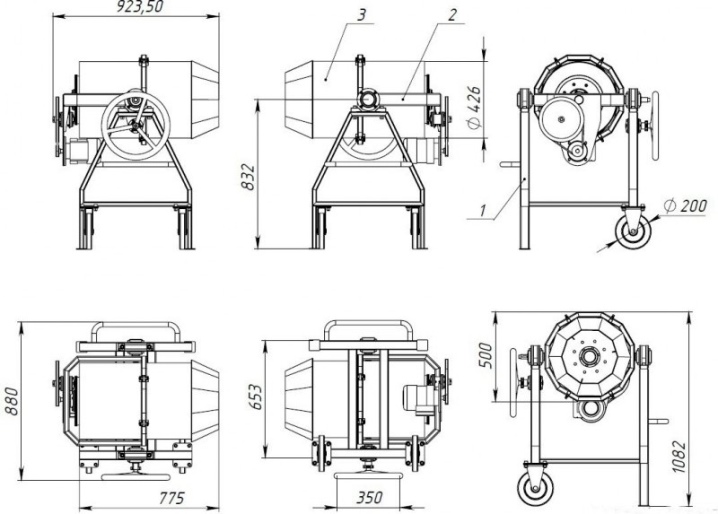
And the fourth option is a vibrating concrete mixer. Very often, craftsmen with a perforator with a power of up to 1.3 kW with a forced-action percussion mechanism attempted to independently manufacture the unit, but did not get the desired result. Errors can be as follows:
- incorrect selection of capacity - it must be high and round;
- incorrect location of the vibrator - it should be located on the axis of the container, at a distance from the bottom, similar to the radius of the vibrator itself;
- the use of a flat vibrator - in this case, it will not be able to create the necessary system of waves;
- very large vibrator - the diameter must be 15–20 centimeters, otherwise the device will not be able to mix the solution.
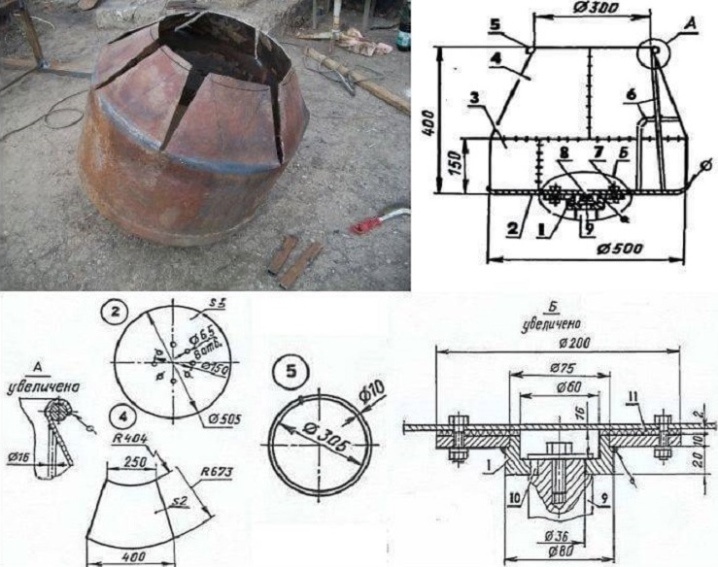
If all the requirements are met, concrete of amazing quality is obtained at the exit. For mixing tough concrete mixes, rotary concrete mixers are used, the production of which is much more difficult with one's own hands.
Some connect the electrical wire through a gearbox, which significantly increases the cost of the future unit.
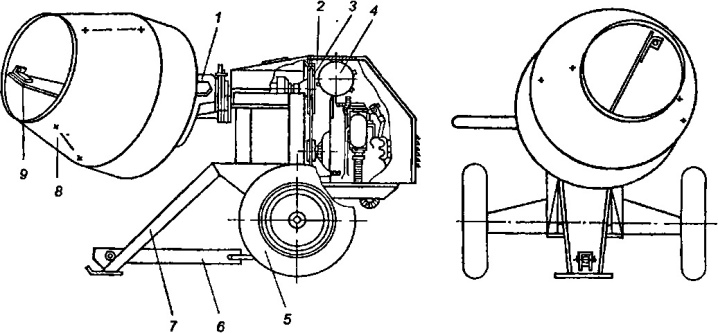
There are several classifications of concrete mixer structures that differ in parameters. If we consider the principle of action, then the following types are distinguished:
- gravitational - the rotation of the drum is due to the force of gravity;
- compulsory - due to internal blades;
- periodic - frequent stops are necessary due to low power;
- gear or crown;
- constant - use in large-scale construction due to continuous work.
By the type of concrete produced, mortar mixers and concrete mixers are distinguished. In mortar mixers, horizontal screw elements rotate in a stationary container are used.
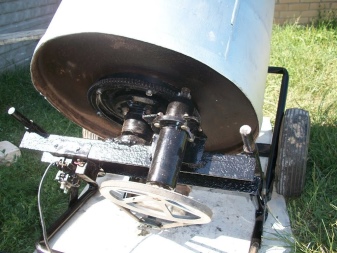
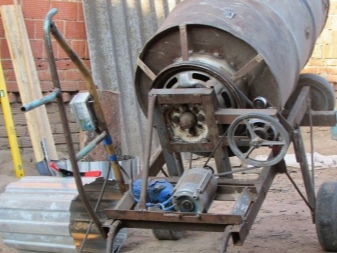
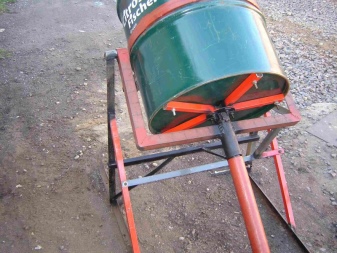
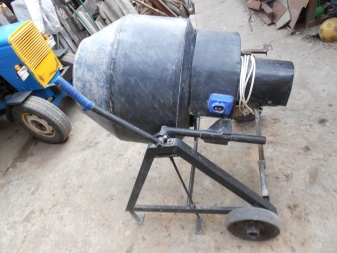
Many are wondering about the benefits of creating a homemade concrete mixer.
Some people use materials that are not designed for mixing concrete at all, such as a drill.
But this tool is good for drilling holes in walls, not for creating mortars from concrete. The same can be said for the various mixers. In fact, the benefits of a homemade concrete mixer are high and are as follows:
- minimal or zero production costs;
- lack of a complex technical scheme that requires a specific area of expertise;
- the availability of the necessary elements for assembly;
- the possibility of developing an individual project;
- the possibility of creating a collapsible structure.
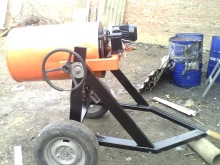
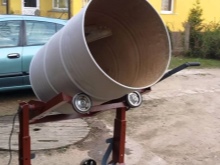
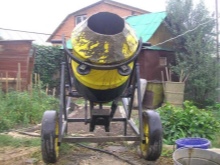
Thus, a homemade concrete mixer has a lot of advantages. This option is not suitable for those who do not want to work with their own hands or expect a quick result. Creating your own unit requires a lot of effort, patience and time. Something needs to be altered or adjusted right during assembly. And for those who are ready to take the risk, below are the popular methods of making a concrete mixer with their own hands.
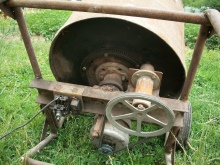
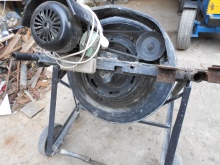
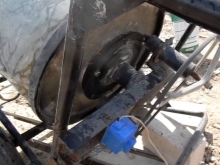
How to make from a washing machine?
For the construction in this case, you need a tank and an engine. We recommend using upright washing machines. If everything is fine with the case, then the necessary elements can be missed. There is one key disadvantage here - the scooping of the mixture with a trowel. To avoid such inconveniences, it is better to put the tank and the engine on a homemade frame.
The most common option is a swing. Main advantages:
- ease of quick cleaning from the mixture;
- the possibility of heavy loads;
- mobility.
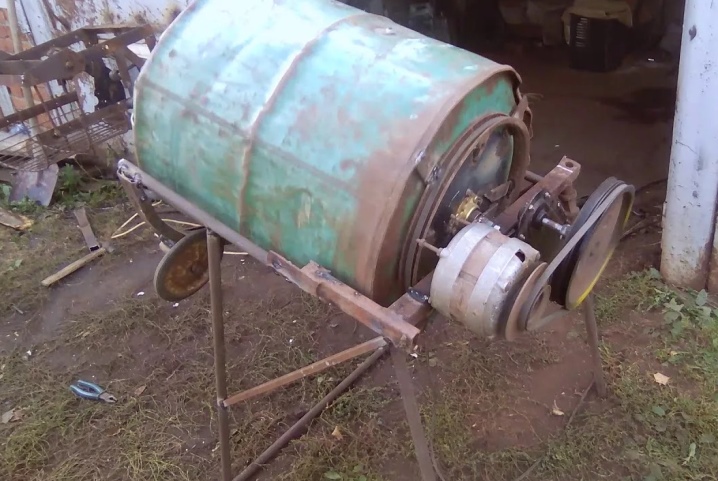
Tools and parts
You should prepare corners of various sizes, the engine from the washing machine and the tank. You can build a concrete mixer using the tools that you have at home.
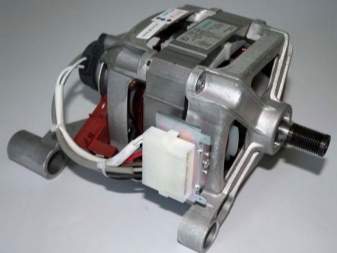
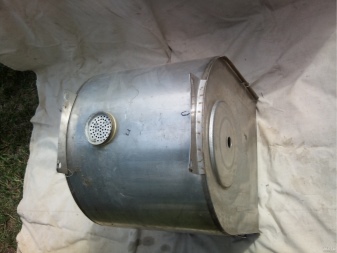
Assembly
To make such a structure, you need to weld two triangles from a corner of 50 * 50 millimeters, the size of which is 0.6 * 0.8 * 0.8 meters. Place them opposite each other and weld two 0.5 meter corners to each side. The result is a high-quality construction of a pair of triangles.
Weld two nuts on top of the triangles so that the 25mm shaft can move freely. So that it does not jump out of the hole, you need to weld along the edges of the shaft. Next, you need to take 2 corners of 1.4 meters each and 3 - 0.4 meters each. Place the middle corner in the center and make a ladder by welding. Weld the middle corner to the shaft, and the swing is ready.
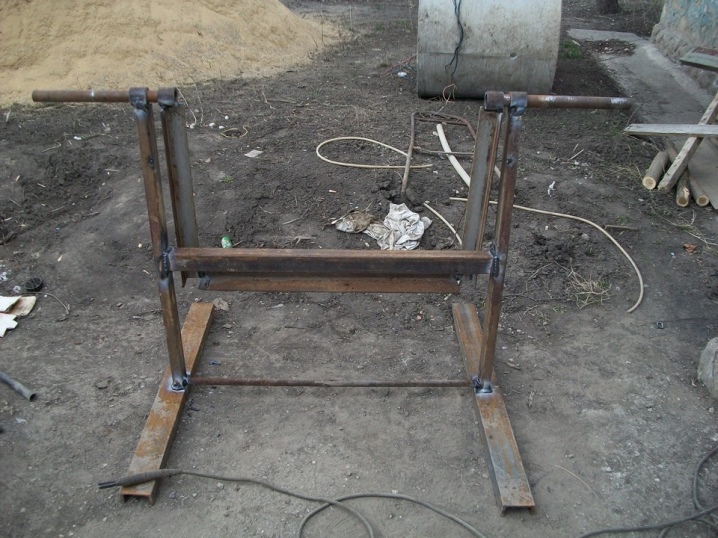
Next, you need to make two blanks 0.9 meters long, cutting steel strips 50 * 4 mm in size. In the center, make holes the size of the axle thread. To give the plates the shape of blades, they need to be bent a little and mounted on an axis at an inclination of 90 degrees, fixed with nuts and welded.
Place the tank on one side of the swing and weld. Its bottom should be directed towards the tops of the triangles. There is no need to drain - you can plug it. Now you need to test the blades.
The engine is located opposite the swing. To protect it from water, a rubber casing is cut into it.
It remains to check the unit by connecting it to the electrical network. To get the solution, the swing is lifted to the side behind the engine. The do-it-yourself concrete mixer is ready. Optionally, you can build a concrete feed tray.
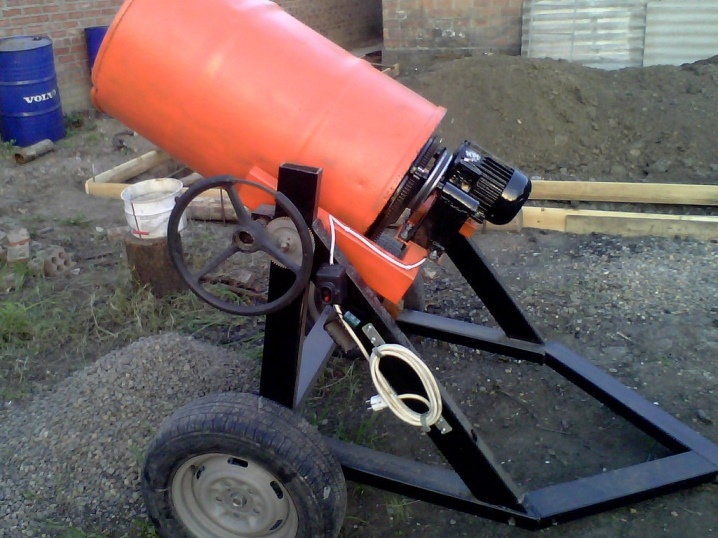
Making from a barrel
In the barrel device, the solution moves obliquely: the mixture moves from one side to the other. Two types of concrete mixer can be made here: manual or electric. Advantages:
- clear configuration for users;
- lower cost of the product;
- elimination of problems related to repair.
To create a concrete mixer at home, you will need a barrel of 0.1-0.2 cubic meters, a thick pipe with a diameter of 32 millimeters, a rod for an axle with a diameter of 30 millimeters, a car steering wheel, door hinges, a welding machine, a hacksaw for metal and a grinder.
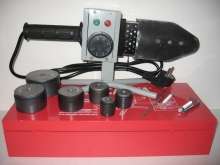
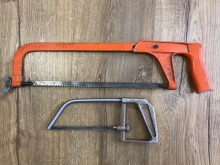
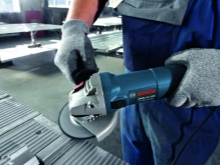
Make holes from the bottom and top in the center of the barrel, thread a metal axle with a diameter of 30 millimeters and boil it well so that the bucket attaches well. On the side (in the center of the barrel), cut a hole 90 * 30 centimeters in size for supplying the solution. A very small hatch will make it difficult for the mixture to fall asleep, and too large will affect the strength of the device. Next, build several blades from a square and weld inside the container to the axis and to the wall of the barrel. Mostly 5 blades are made. Now you need to install the lid and fasten it to the door hinges, which are welded to the barrel.
Then the device is installed on a support with a height of about a meter. To do this, you yourself need to weld the frame, weld the bushings and insert the axle, attach the steering wheel or other handle element to conveniently rotate the drum.
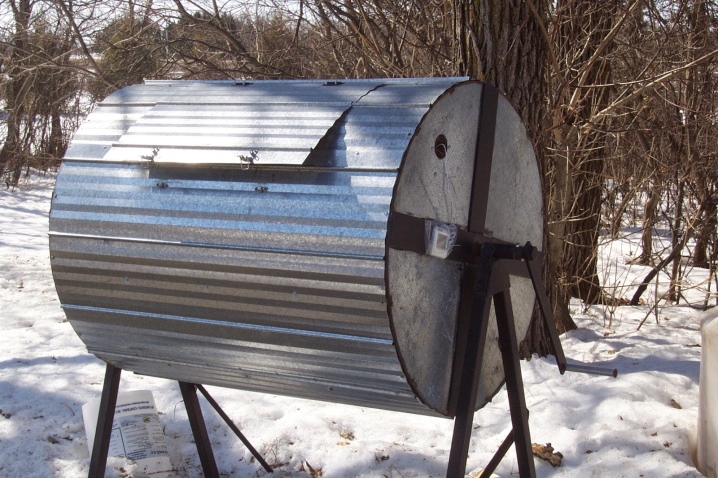
In order for the unit to serve for a long time, it is worth adhering to the following recommendations:
- when assembling, it is important to pay attention to the reliability of the connecting elements of the entire structure;
- if there is no welding machine, then all parts are bolted with washers;
- also, special attention should be paid to tightness;
- the tilt of the barrel should be approximately 5 degrees in relation to the ground;
- all rotating elements must be thoroughly lubricated to ensure trouble-free operation of the concrete mixer.
If desired, the unit can be made portable using wheels from any wheelbarrow or even a washing machine.
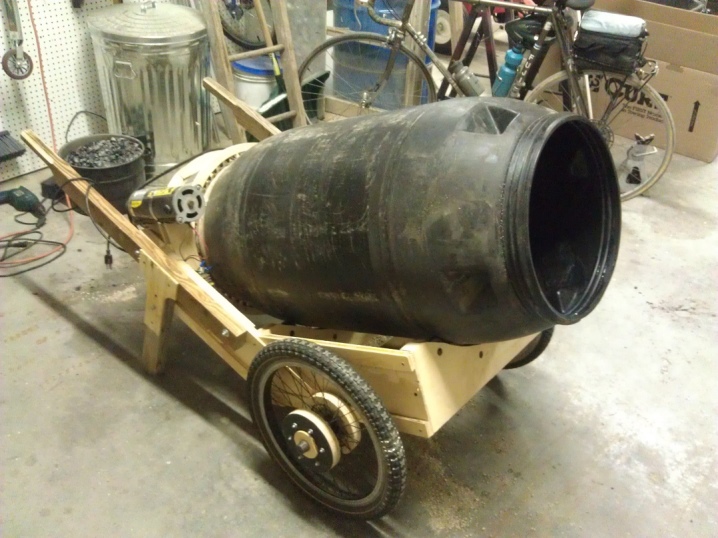
Recommendations
The highest speed of rotation of the shaft on a home-made concrete mixer should be 30-50 rpm. If you install a low-power motor, then high energy costs will be required, which will also affect the speed of construction work.
If there is no electricity on the site, it is advisable to build a manual concrete mixer by attaching a handle for self-rotation. When filling in the ingredients, you must adhere to the following sequence: first - water, then - cement, sand and gravel. The device must be thoroughly rinsed and cleaned after each use. Similarly to a concrete mixer from a barrel, you can make a miniature version from a bucket and a drill, and some craftsmen manage to build a unit from a gas cylinder.
Even experienced craftsmen can make mistakes when creating a concrete mixer.
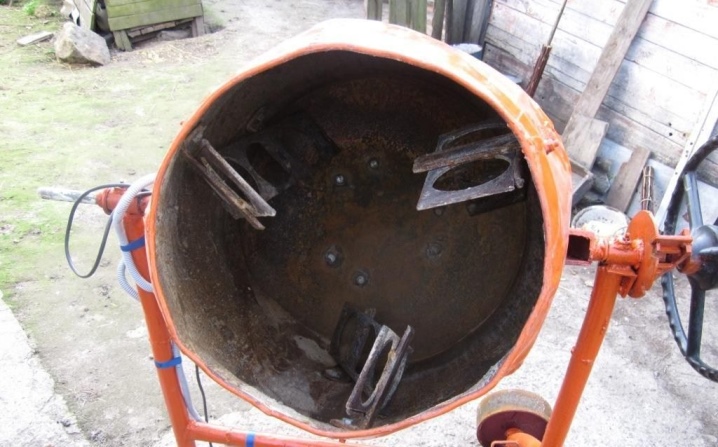
The most common among them are incorrect calculations during planning, power mismatch with the number of revolutions, fragile connections of structural elements, insufficiently stable base, too high location of the rotating vessel.
Some people use a drill to mix the mixture, which is impractical due to the fact that it cannot be used for a long time. It is recommended to take breaks every 15 minutes after 5 minutes of work. This significantly increases the construction period.
When creating a structure, special attention should be paid to wires and connections. They must be well insulated, since the work is done in conditions of high humidity, and compliance with fire safety rules comes first.
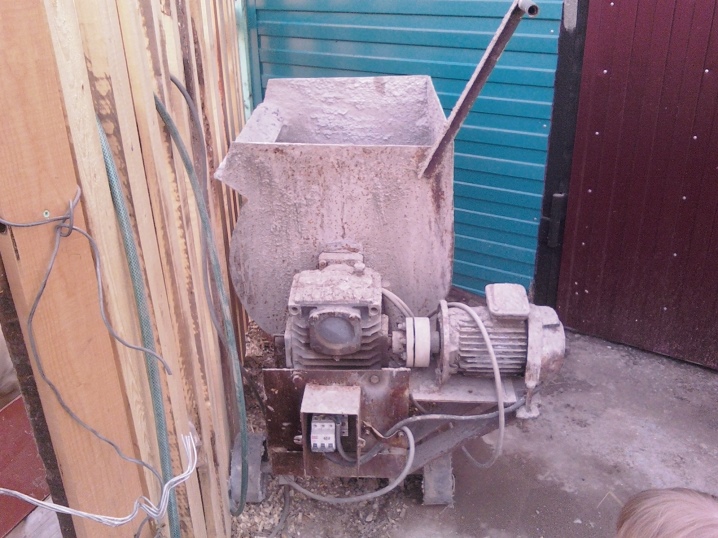
The mixing process is accompanied by certain vibrations that loosen the connections, so it is important to monitor and tighten the bolts if necessary. It is also worth paying attention to welded seams, which can also be destroyed as a result of work.
Before switching on the device, make sure that it is stable. Any stand must be firmly on the ground. If there are wheels, it is advisable to install wheel chocks.
During operation of the unit, it is forbidden to check the quality of the solution, otherwise you may get serious damage.
Finally, the switched on concrete mixer should not be left unattended in order to avoid unpleasant situations.
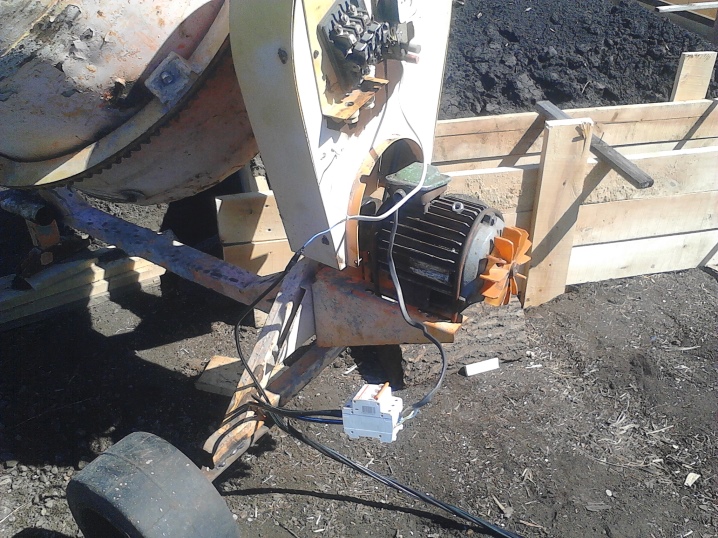
Nowadays, there are times of total economy, and the construction budget is often limited, so many are trying to save money on the services of third-party craftsmen. Despite the apparent complexity, the concrete mixer is ideal for home use.
From experience, the creation of any mechanical device increases labor productivity and reduces working time. A concrete mixer is not the most difficult invention that can be made from improvised means without special engineering education. The self-made device has a simple diagram, drawing and assembly sequence. The main thing is to decide in advance with the aim of creating a concrete mixer, and then the unit will not yield to the industrial model, even if it is made from a washing machine or a barrel.
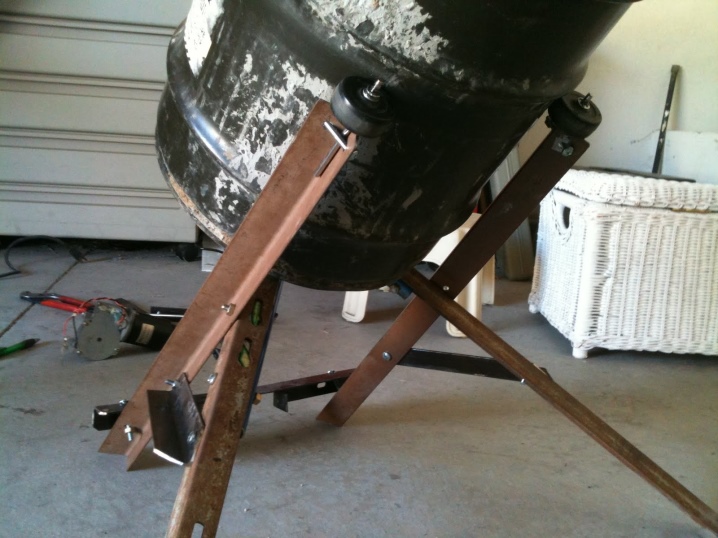
How to make a concrete mixer with your own hands, see below.
The comment was sent successfully.