All about polyurethane impregnation for concrete

The use of polymer compositions when creating a concrete screed is an indispensable condition for achieving high concrete strength and minimizing the formation of dust on its surface. Polyurethane impregnation is most suitable for this, providing excellent performance characteristics of the material.


Peculiarities
To improve the moisture resistance and strength properties of monolithic concrete, its ironing is used. This technological process involves the use of special adhesives that clog the pores, which are a significant disadvantage of the material and accelerate wear. In addition, without special treatment, such floors and other structures absorb a lot of moisture, form dust and quickly deteriorate if located outdoors.


To prevent this, professionals use strengthening polymer compounds. One of the demanded products that does its job well is polyurethane impregnation for concrete. The product is a low-viscosity liquid solution that fills the pores of the material, penetrating into its thickness by 5–8 mm. The impregnation has a one-component composition and does not require complex preparation before application: it just needs to be thoroughly mixed until smooth.
Polymer fluid is able to enhance the adhesion of concrete substrates with different coatings.

The material is suitable for repairing old, damaged concrete, as well as for creating new structures from it. Polyurethane is a versatile substance that can quickly be absorbed and create the necessary density without interacting with water from the environment. The product has the following useful technical characteristics:
- high plasticity, resistance to temperature extremes;
- increases the impact resistance of the material by 2 times;
- increases the wear resistance of concrete by 10 times;
- the use of the composition allows you to completely eliminate dust formation;
- hardens surfaces to acceptable categories (M 600);
- the ability to use at low temperatures (up to -20 °);
- fast setting in a day, the ability to operate with heavy loads after 3 days;
- simple impregnation technology that does not require special knowledge and skills;
- the composition can be applied to inexpensive concrete grades;
- provides an anti-slip effect and a pleasant appearance of the product after the application operation.
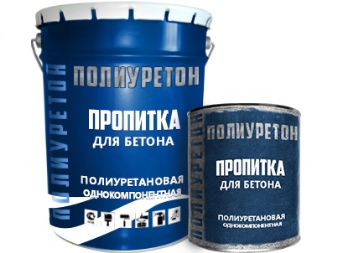

Of course, the listed parameters are positive qualities of polyurethane impregnation, in addition to its low cost. Of the relative disadvantages, one can name the need to use the polymer only after the final drying of the structures.
And also, if the concrete contains the wrong filler, for example, silicon dioxide, then the polyurethane can provoke stress inside the material, causing an alkali-silicate reaction.


Types and purpose
Impregnations for concrete are polymeric (organic), their action is aimed at increasing strength, moisture resistance, resistance to aggressive substances. The inorganic type of agent works differently. Chemical elements in their composition, when reacting with structural concrete particles, acquire inertness and dissolve. Due to this, the material acquires such qualities as water resistance and the necessary hardness. There are popular types of impregnations in terms of composition.
- Epoxy two-component mixtures of resin and hardener (phenol). These products are distinguished by low shrinkage, wear resistance to abrasion, increased strength and low moisture permeability. They are used to create structures for industrial buildings and workshops, basements, swimming pools. Unlike polyurethane, these are less resistant to physical deformation and aggressive chemicals.

- Acrylic impregnation for concrete floor - good protection against UV rays, moisture and chlorine compounds. Although they retain the color of the surface during the entire period of operation, they require renewal every 2-3 years.

- Polyurethane... Speaking about the useful qualities of polyurethane, one cannot fail to mention its protective properties due to the presence of organic substances and polymer resin in the composition of the solvent. This distinguishes the product from other impregnations - this type of material can be used in different weather and climatic conditions. In addition, the impregnation is quick and easy to apply and is inexpensive.

Due to the high quality of impregnation, a deep penetration impregnation stands out against the background of other agents, designed to improve adhesion to enamel, paint or other paint coatings. Thanks to its features any material used lasts much longer.
And also on sale you can find colored and colorless mixtures for removing dust on concrete and giving it a pleasant look. They are relevant both for industrial buildings and for residential premises.


Criterias of choice
Concrete simply needs to be impregnated with protective compounds due to its porous structure. During the hydration of cement, air, water, and a cement slurry in the form of a gel may be present in the concrete cavities. This weakens the strength of the products and shortens their service life. However, concrete can be transformed into monolithic stone using impregnations. General requirements for the choice of impregnations:
- security the resulting coating after applying the impregnating composition, no release of harmful components, the concrete surface should not be slippery;
- it is important to pay attention to the purpose of the solutions, their working properties, such as wear resistance, resistance to water, ultraviolet radiation, temperature conditions, and other external factors;
- optimal compatibility with the substrate, good penetration and adhesion;
- tangible result in terms of reducing dust formation;
- attractiveness appearance.
Polyurethane impregnation satisfies all these criteria, it is she who is the best way to improve the performance of concrete structures. In addition to strengthening the material, preventing its premature wear, dedusting and increasing the service life, the polyurethane composition allows you to give concrete structures a beautiful, deep and rich color due to the ability to pigment the solution.


Mode of application
Polyurethane impregnation can be applied not only to concrete, but also to other mineral substrates, but the technology is always unchanged.
- The first step is with grinding equipment the concrete surface is leveled, removed cement milk, loose layer, oil, layer obtained as a result of ironing.
- A hand grinder is used to clean the joints, the brush removes solid particles of cement, sand. Thus, the pores of the material are opened.
- Additional three-stage grinding is aimed at obtaining a filler pattern (crushed stone cut). First, rough processing is carried out by 2–5 mm, then moderate grinding, at the end - grinding with a fine-grained abrasive.
- Surface cleared of dust using a vacuum cleaner.
- Followed by polyurethane-impregnated primeruntil a uniform layer forms. The mixture should not be allowed to accumulate in the form of puddles.
- For different grades of concrete (M 150 – M 350), 3 coats are used. When screed concrete of a category greater than M 350, as well as for bricks, slate and ceramic tiles, 2 layers are sufficient.For this, material such as "Politax" is suitable.
- All layers must be thoroughly dried... At a temperature of 0 °, drying will take no less than 6 and no more than 24 hours, at lower, minus temperatures, no less than 16 and no more than 48 hours. A test application of impregnation will help determine the consumption of polyurethane.

In order to save money, you can not apply 3 layers of solution, but then the surface will be devoid of glossy shine.
To give more strength, on the contrary, it is recommended to make additional layers. Polyurethane impregnation ensures uniform penetration throughout the entire thickness of concrete, enhances the mechanical properties of the material and its chemical resistance, which guarantees an increase in the durability of the structure by 2-3 years, and also simplifies the procedure for maintaining the coating.



In the next video, you are waiting for the application of a hardening impregnation on a concrete floor.
The comment was sent successfully.