All about plasticizers for concrete
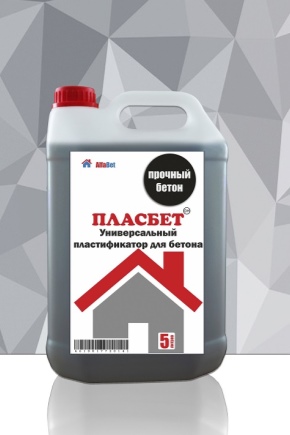
With the development of technologies used in modern construction, more and more people are eager to learn about plasticizers for concrete. First of all, it is worth recalling that this material is a mixture that includes cement, sand, gravel and water. At the same time, the main task of the developers was to create additives that can make the concrete solution more plastic.
Their use can significantly improve the performance properties of concrete.
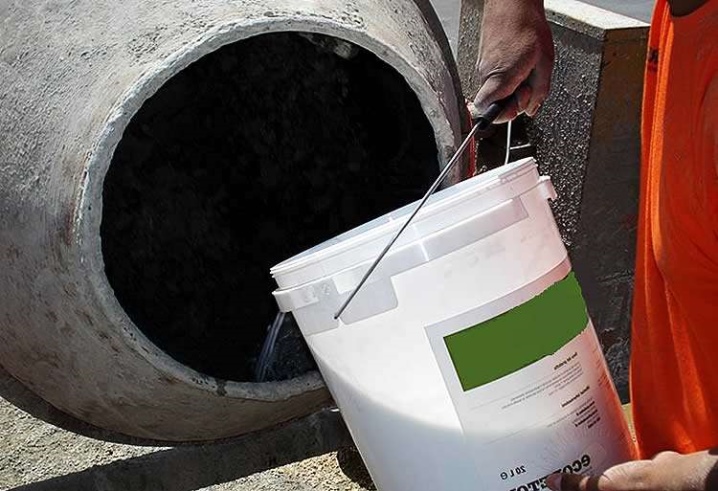
Peculiarities
The value of plasticizers for concrete can hardly be overestimated. They allow you to minimize the negative impact of external factors on the solution, as well as significantly improve its quality. The use of liquid additives, including for the production of sand concrete, makes the work easier. We are talking, in particular, about the laying of ready-made mixtures in the formwork.
Taking into account the principle of action, plasticizers are divided into hydrophilic and water-repellent. The first variety is characterized by high wettability. The second type is designed to maximize the saturation of the concrete mix with air. In modern construction, plasticizers as additives have long become an indispensable component of most solutions.
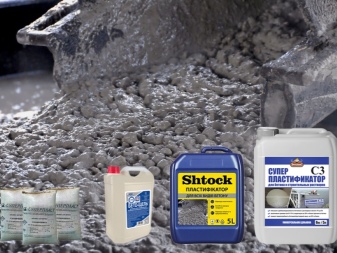
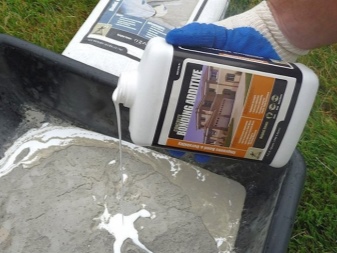
This approach is fully explained by some clear advantages.
- First of all, we are talking about maximizing the plasticity of the final product. This, in turn, greatly simplifies the use of concretes and mortars, since they are poured even into the most inaccessible places when creating structures with increased strength.
- The second advantage of modern plasticizers is a significant reduction in the consumption of building materials. Thanks to the use of such effective additives, it is possible to save money. To check, it is worth comparing the consumption of cement in the manufacture of concrete with and without additives. It is important that in the first case, the amount of used cement will be less by almost 17 percent.
- Plasticizers increase the strength of concrete by an average of 25 percent.
- The use of the described additives, due to which the solution becomes more fluid and elastic, allows the use of specialized installations when pouring. Such equipment, which are based on concrete pumps, is widely used, for example, in the process of constructing monolithic structures.
- The flowable mixture, characterized by improved adhesion, is indispensable, if necessary, to fill in the reinforced elements of future structures.
- The presence of high-quality plasticizers of various types makes it possible to multiply the density level of the concrete solution. It is also important to take into account that structures made of similar materials differ from their counterparts in maximum water resistance.
- Due to the minimal presence of moisture in solutions with plasticizers, frost-resistant structures are created. It is also about minimizing the risk of cracking over time.
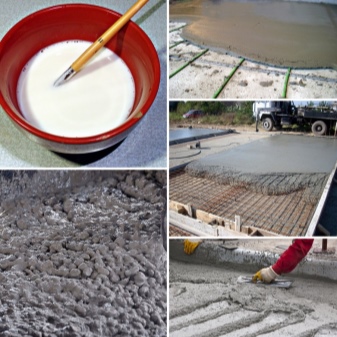
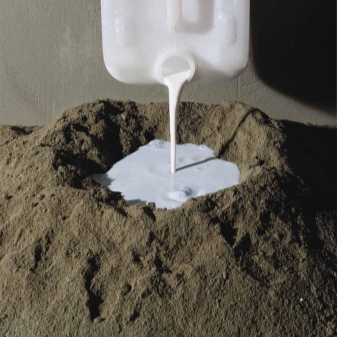
It is important to remember that the use of the considered additives significantly increases the curing time of concrete. In some situations, this can be a significant problem.
The solution, as a rule, is the addition of special additives to the mixture, which act as reaction accelerators.
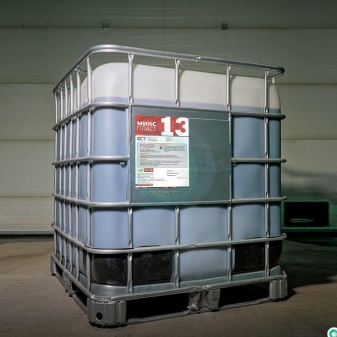
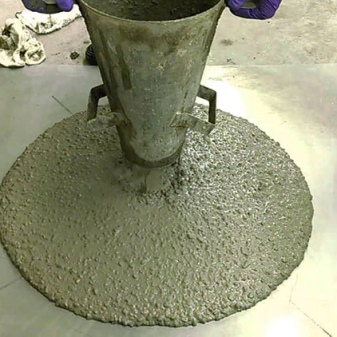
Views
Modern additives that increase the plasticity of the building mixture, taking into account their composition, are divided into organic and inorganic. If we take into account the class of their purpose, then two categories can be distinguished.
- Monoadditives, which are solutions with narrowly targeted action. It should be borne in mind that they are often characterized by side, negative effects.
- Complex additives that combine several one-component solutions that effectively neutralize all negative effects on the concrete mixture. This, in turn, contributes to a significant expansion of the scope.
Also, plasticizers currently on the market can be divided into several groups:
- compounds of surface-active components having a hydrophilic-hydrophobic effect;
- mixtures of electrolytes and surfactants, which effectively accelerate the solidification process;
- superplasticizers with enhanced air-entraining effect;
- reinforced additives used in the manufacture of concrete for laying in an aggressive environment.
It is important to take into account that the described mixtures can be produced in the form of a suspension, liquid, paste, as well as a crystalline powder.
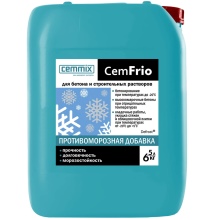
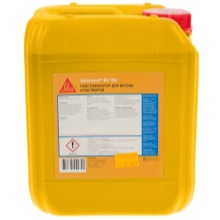
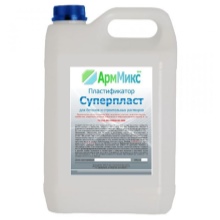
Water-reducing
This category of additives differs from other types in the first place by providing the possibility of significant water savings in the preparation of a concrete mixture. By the way, we are talking about reducing consumption by 5-20 percent.
In addition, such plasticizers increase the water resistance, strength and frost resistance of concrete.
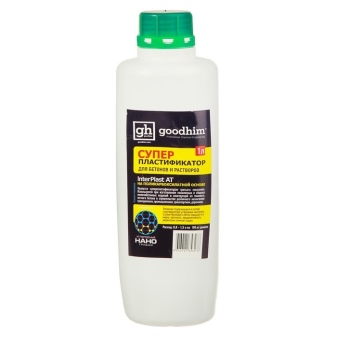
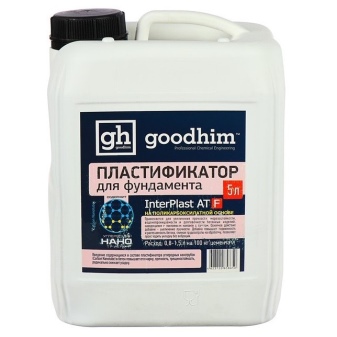
Stabilizing
Representatives of this category have a unique ability to preserve the mobility of solutions for the longest time possible. This also applies to their uniformity. Such properties are most relevant for long-term transportation of concrete mixtures, their pumping and directly laying.
At the same time, their stratification is prevented.
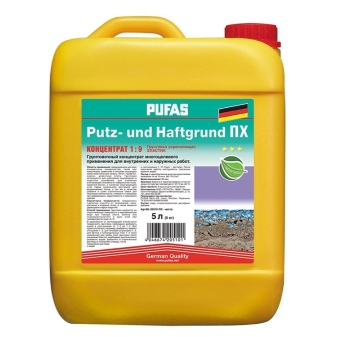
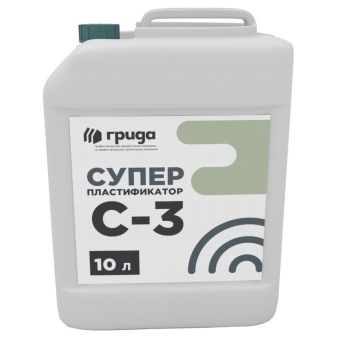
Hardening accelerators
These additives effectively reduce the time of concrete hardening (up to 25%). It is important to take into account that during the first day, the solution gains 20% more strength than the branded solution. Such additives, as a rule, are used in industries in order to accelerate the formation of concrete products, as well as in construction during the construction of structures in conditions of negative temperatures.
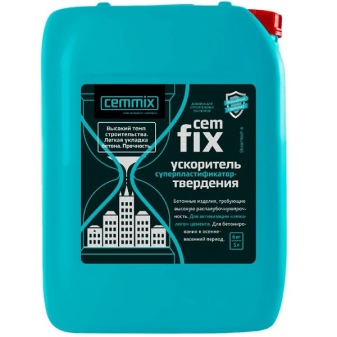
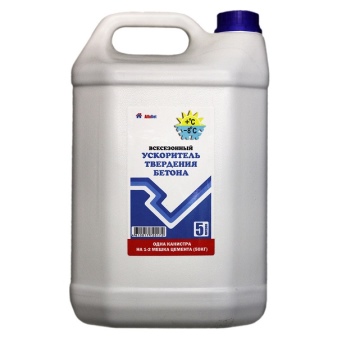
Retarders
These components are relevant for large volumes of concreting. With their help, you can significantly reduce the number of joints, called working seams.
Also, the extension of the setting intervals of concrete mixtures is required if long and frequent breaks are made in the work.
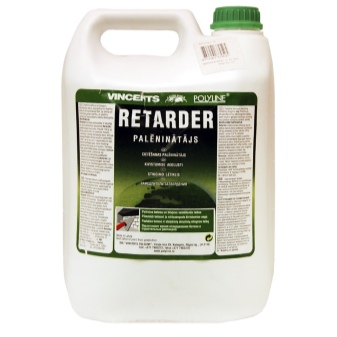
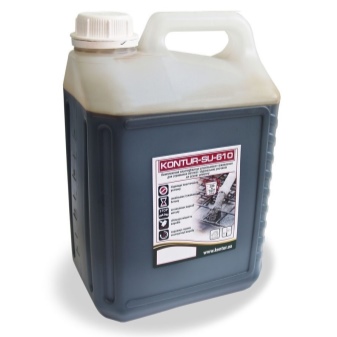
Hydrophobizing
Representatives of this category promote the active entrainment of air bubbles. The latter are evenly distributed throughout the mixture and, in parallel, lower the surface tension of the water present in it. As a result, the mobility and plasticity of the concrete mortar with increased water-repellency of the surface increases.
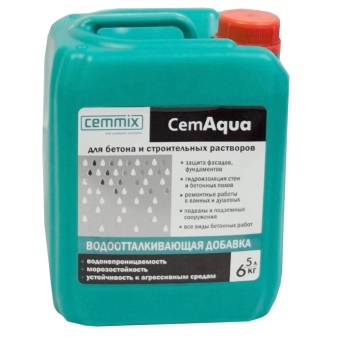
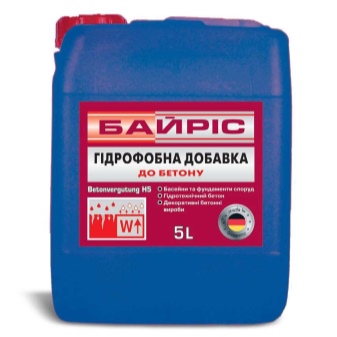
Leading manufacturers and their products
At the moment, many companies offer their products in the corresponding market segment. The current ratings of the popularity of plasticizer brands help to navigate such a variety. Taking into account the whole list of criteria, one can single out the clear leaders of the industry.
- Roskhimprom - a group of companies founded almost 20 years ago in Rostov-on-Don and now specializing in the supply of raw materials for companies operating vibrocasting and vibropressing plants.
- Corporation "TECHNONICOL", which is one of the leaders in the rating of international building materials manufacturing companies.
- Alligator - an enterprise founded back in 1959. At the moment, the company specializes in the production of modern building mixtures and paintwork materials.Products of this brand are in deserved demand in many countries around the world.
Plasticizers for concrete solutions "Optimist" S-3 deserve special attention. This is a popular and proven plasticizing additive. It is widely used in the production of monolithic and precast concrete structures of varying complexity.
Most often, this plasticizer acts as a component of light, heavy and cellular concrete.
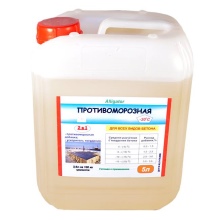
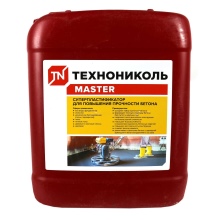
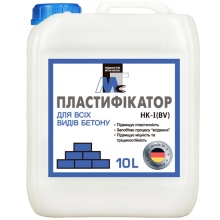
Scope of application
The use of modern plasticizers, including those added to sand concrete, provides a real opportunity to significantly reduce production costs. Naturally, do not forget about increasing the performance of the described building mixtures. Modern manufacturers present on the market more than a wide range of additives with different characteristics.
Nowadays, plasticizers are widely used both at large construction sites and enterprises producing concrete goods, and in small-sized housing construction. Such additives are relevant when pouring foundations of any configuration, bases for flooring and underfloor heating. By the way, plasticizing additives are often needed for gypsum and other building and finishing materials. Which additive is best used can be determined taking into account the purpose of the concrete itself.
One of the moments defining the scope of application of plasticizers is their ability to effectively reduce the concentration of water. This is most relevant for the monolithic construction that is popular today.
Also, additives are used to obtain frost-resistant structural elements.
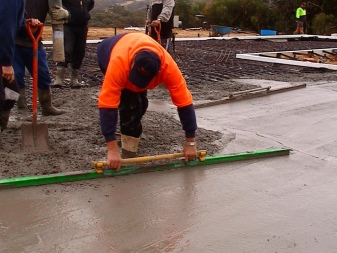
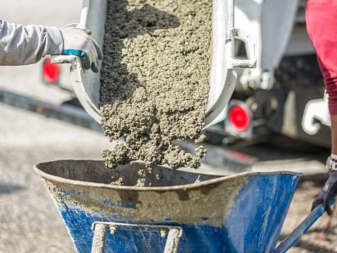
Today, plasticizing additives are actively used when pouring:
- floor screeds;
- blocks of different shapes and sizes;
- borders;
- pillars;
- slabs;
- columns;
- fountains.
All listed products are characterized by maximum strength, water resistance and long service life.
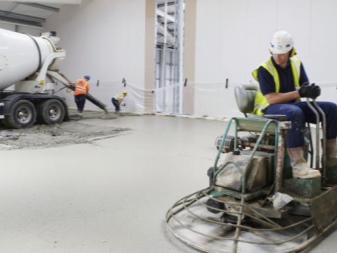
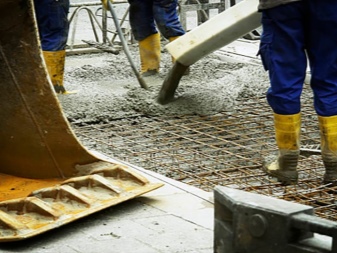
Self-production
Taking into account the cost of the described additives, many are trying to reduce costs and replace them with cheaper analogues. In this case, we are talking about making a plasticizer with your own hands. It is worth noting that, subject to the proportions and instructions for preparing the additive, concrete will receive all the necessary properties. Homemade mixtures are made using liquid soap, hair shampoo, or washing powder dissolved in water.
By the way, before the appearance of the first plasticizers and chemicals, the performance of mortars and concrete was increased by adding egg whites. This made it possible to maximize the strength of the mixtures.
The amount of plasticizer for its self-preparation is determined taking into account the solution to which it will be added.
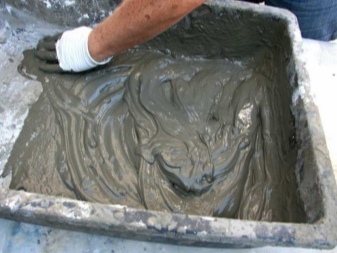
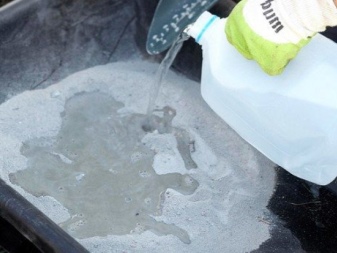
So, when combining one bag of cement with expanded clay, you will need to add about 200 ml of soap solution. As a result, it will be possible to provide resistance to solidification within 3 hours. It is important to remember that liquid soap must be added at the initial stage of concrete work. Otherwise, expanded clay will mix unevenly, due to which concrete will lose its key properties.
With all the advantages, soap solutions have one important drawback. In this case, we are talking about the almost inevitable formation of foam when all the components are combined. This is especially true if a concrete mixer is used. However, the problem is not critical, since work can be started immediately after the foam settles.
Another way to prepare a sufficiently effective plasticizer is to use hydrated lime. This mixture makes any solution as sticky and elastic as possible.
By the way, adding lime to the mortar for masonry greatly simplifies the whole process and contributes to an even distribution of the mixture.
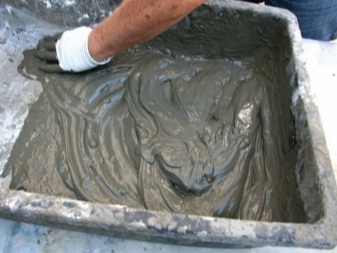

Instructions for use
The use of plasticizers, both industrially and independently, is regulated by clear instructions. To avoid problems, the following important points must be considered:
- the component is introduced in the process of adding water, and at the same time it must be in a completely dissolved state;
- the dosage per 1 m3 should be closely monitored;
- homemade additives in dry and dissolved forms are introduced at the rate of up to 150 and 250 g for each bag of cement, respectively;
- preparation of the solution is desirable to carry out in conditions of positive temperature;
- it is necessary to monitor the maximum possible cleanliness of all containers used;
- substances that have expired are strongly discouraged.
Now plasticizers are on sale in the form of:
- powders;
- concentrates (liquid);
- ready-to-use solutions.
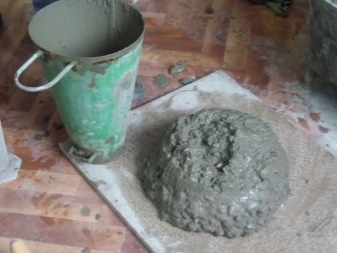
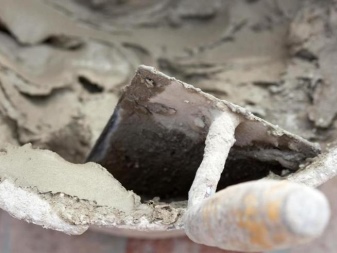
From a financial point of view, the first option is more profitable. When diluting powders, it is necessary to observe the proportions indicated on the packaging or in the instructions. This process includes certain stages.
- Heat the required clean water to a temperature in the range of 70 to 90 degrees.
- Add the powder with constant stirring until it is completely dissolved.
- Leave the solution to infuse for several hours with occasional stirring.
- Add additional connections if necessary.
- Stir the prepared mixture thoroughly before adding it to the water.
- Add ready-to-use plasticizing additive. The key point is that it must be injected exclusively into the water for the solution, and not into the ready-made concrete.
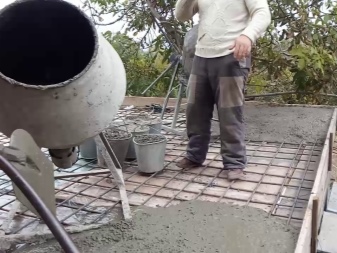
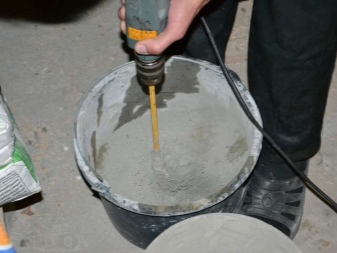
It is important to remember that the shelf life of a dissolved plasticizer is significantly shorter than that of a powdered product. It should also be borne in mind that the repeated introduction of the additive does not affect the dynamics of strength gain. The calculation of the consumption of additives is carried out using special tables compiled by manufacturers.
Particular attention should be paid to safety when working with the described additives. This is most important when working with concentrates. In such cases, rubber gloves, a respirator and safety goggles must be used. If drugs get on the skin, they must be quickly washed off with an abundant amount of preferably running water.
If it comes to contact with mucous membranes, you should immediately seek medical help.
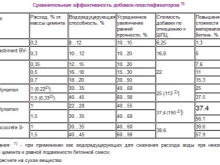
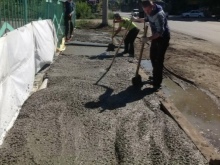
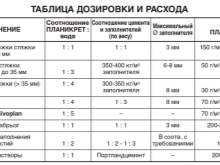
You can see a comparison of the quality of concrete with and without a plasticizer in the video below.
The comment was sent successfully.