All about warming the floor with expanded clay in the bath
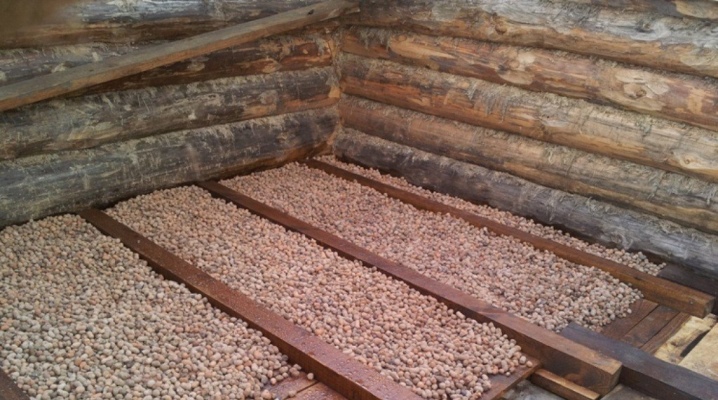
In winter, you need to take special care of floor insulation in the sauna room. Along with many effective thermal insulation layers, expanded clay is the most popular. This material, used in construction, is mainly useful in rooms where temperatures drop below 35 degrees. We will find out why many people prefer to use expanded clay.
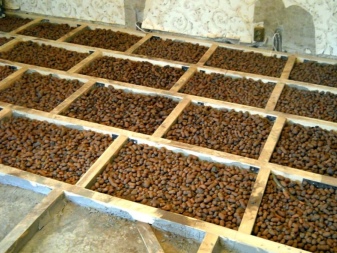
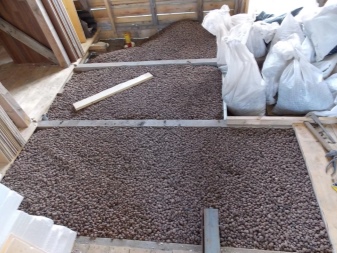
Peculiarities
Expanded clay in appearance is a different-sized granules obtained by firing clay or shale. As a result, a material with low thermal conductivity is formed, and it is also characterized by porosity. In the process of heat treatment, it is impossible to obtain pellets of a uniform size, therefore, the scorched mass is sorted into gravel and sand.
Pieces of clay that could not pass through the material for bulk masses are crushed into the following fractions: crushed stone and sand.
All over the world, people willingly use expanded clay to insulate a room. The material is lightweight, durable and low cost. But any material has a number of pros and cons, expanded clay is no exception.
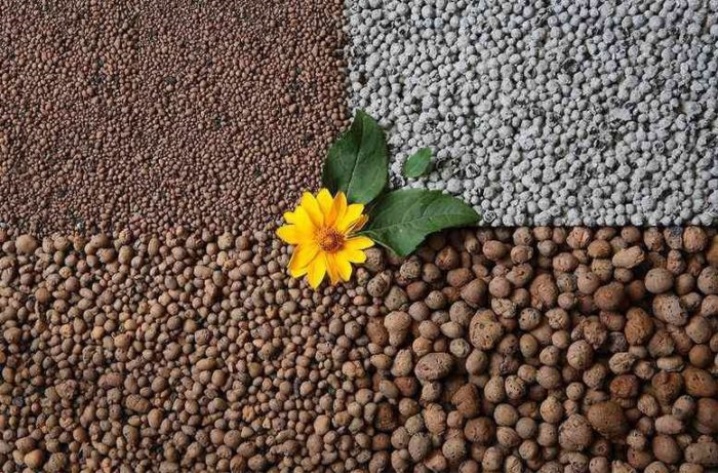
The pluses include:
- good heat-shielding properties, however, this advantage is achieved when using a thicker layer of material;
- subject to the operating conditions, expanded clay can last more than 40 years;
- the material belongs to the NG class (NG is non-combustible materials), therefore it is fireproof;
- many people care about the environmental side - as for expanded clay, it does not emit harmful substances when heated;
- even a person far from construction can lay the floor with expanded clay - installation is easy and quick;
- expanded clay is resistant to both low and high temperatures.
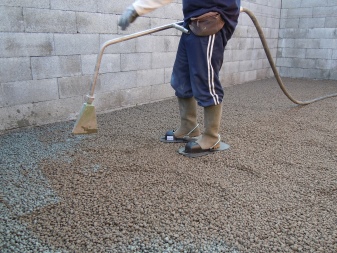
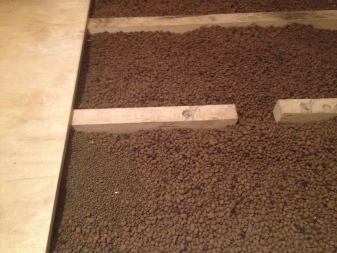
Of course, there are some drawbacks:
- if the material gets wet, its heat-shielding properties are significantly reduced;
- in the case of extremely low temperatures, the granules begin to break down;
- during backfilling, the granules can create dust - another drawback, but for many this item is only a side effect of construction, and not a repulsive factor;
- in the presence of a low ceiling, thermal insulation of the floor covering with expanded clay may be a bad idea.
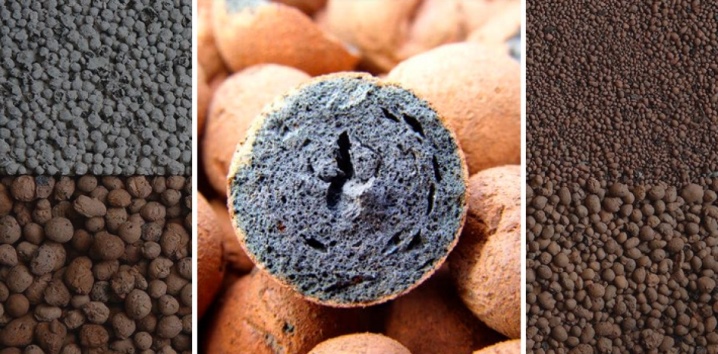
Types of material
Depending on the appearance, shape and technology of obtaining the material, it is divided into several types. In recent years, the production of gravel in Russia has increased by 30%, and the demand for it is gradually growing. Expanded clay gravel is readily used in construction for house insulation. External coatings, floor, insulation of water supply networks - all this is insulated with expanded clay gravel. Let's start with him.
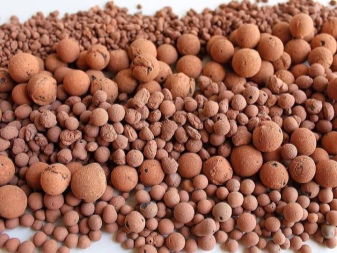
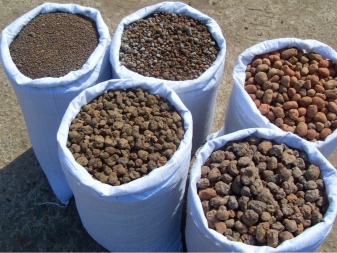
Gravel
It is a rounded pellet with a red-brown color. It is widely used for insulation.
Gravel is used:
- when improving paths in suburban areas;
- thermal insulation of bath rooms;
- creating a concrete screed and drainage system;
- manufacturing of building blocks;
- dumping of the foundation;
- thermal insulation of floors, walls and roofs.
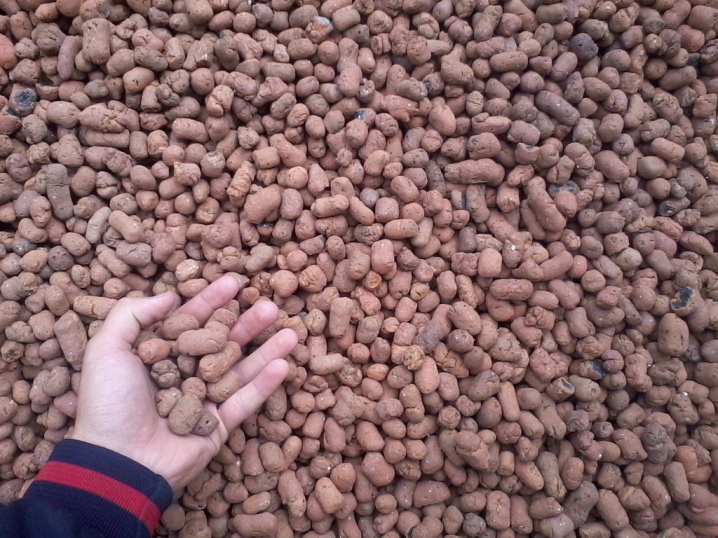
Sand
Mainly obtained by crushing. As a rule, it is cheaper than gravel and crushed stone, but its properties are almost no different from these materials.
Sand is used:
- when creating expanded clay concrete blocks;
- backfilling of the underground space;
- landscape design developments, for the equipment of garden paths;
- filtration of water.
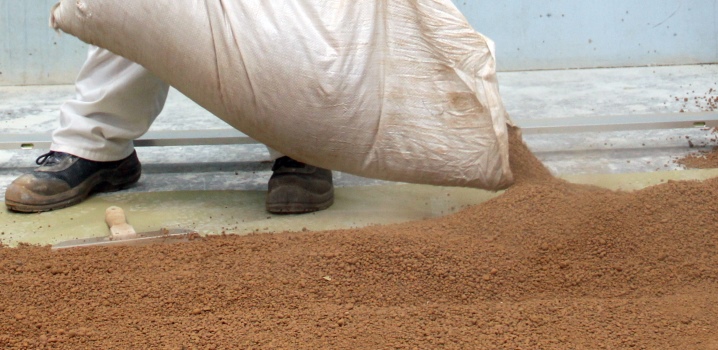
Crushed stone
It is obtained in the process of crushing large pieces of expanded clay. As a result, pieces of various shapes come out (from 5 to 40 mm.)
Crushed stone is used for filling lightweight concrete.
The appearance of expanded clay is unpresentable, but this is most often not paid attention to, and there is a reason for that. The material, as a rule, is rarely used open: it is usually included in concrete or insulated wooden floors. Expanded clay differs in low cost among other heat-shielding materials, for which it is in demand among the consumer.
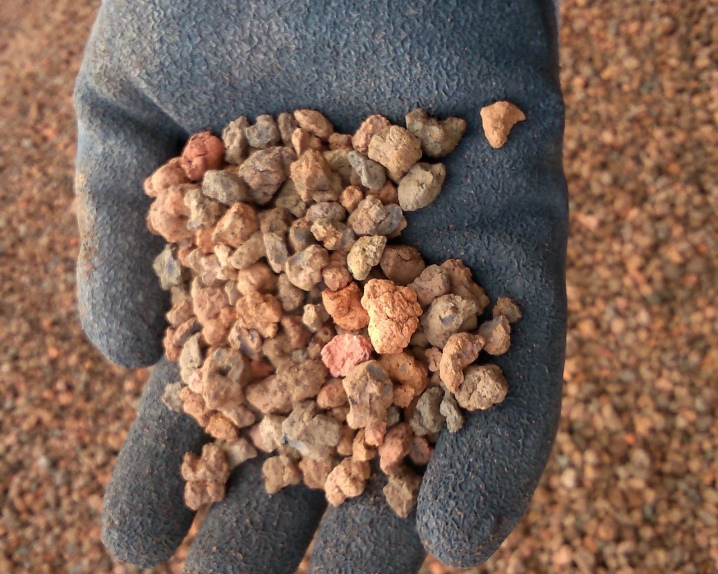
What is required?
In many ways, the warmth of the room depends on the type of floor. Expanded clay is undoubtedly an effective insulation. It should be borne in mind that the material is granules of different sizes, respectively, the thermal conductivity also differs.
In order for the floor to be well insulated, it is better to purchase a mixture of several types of expanded clay: sand and gravel (granules should be 5-20 mm in size). This mass is sold under the universal brand name M300.
For work, it is advisable to take a large volume of expanded clay, since the granules can break as a result of transportation. Before backfilling, beacons are installed (to level the screed), so you should take care of their presence. You will also need cement mortar, cement, reinforcing mesh (for the stability of the structure).
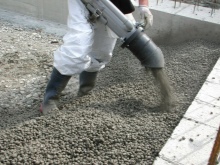
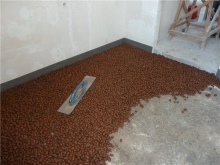
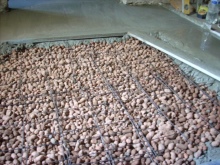
Please note: in order for the granules to stick together better, they must be of different sizes. It is important to ensure that there are no irregularities when filling the material, otherwise all work will be in vain. For stability after work, a metal mesh is installed - it is worth purchasing it in advance.
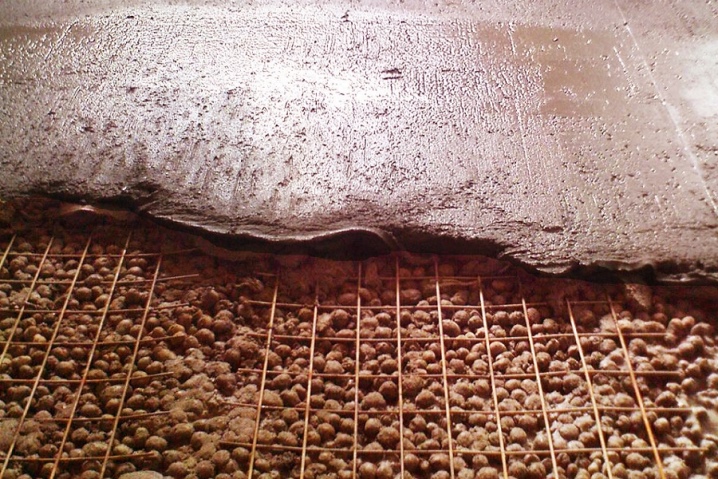
Step-by-step instruction
Each case of floor insulation is individual, like a bath building, but there is a general technology for backfilling expanded clay, suitable for any type of structure.
- The first step is to lay a waterproofing film (on the ground). For floors, a vapor barrier is used - it helps moisture escape from the heat-saving pillow.
- The joints between the laminated insulation strips are glued using ordinary construction tape.
- Attach construction beacons - a layer of the required thickness is poured over them.
- Expanded clay is poured, adhering to a layer of 20 cm. It is not recommended to make a layer thickness less than 15 cm.
- The created pillow is spilled with a mortar - cement milk. It reliably fixes expanded clay granules and holds them together, which is exactly what is needed.
- After 24 hours, a metal mesh is laid on the floor and subsequently a concrete screed is poured.
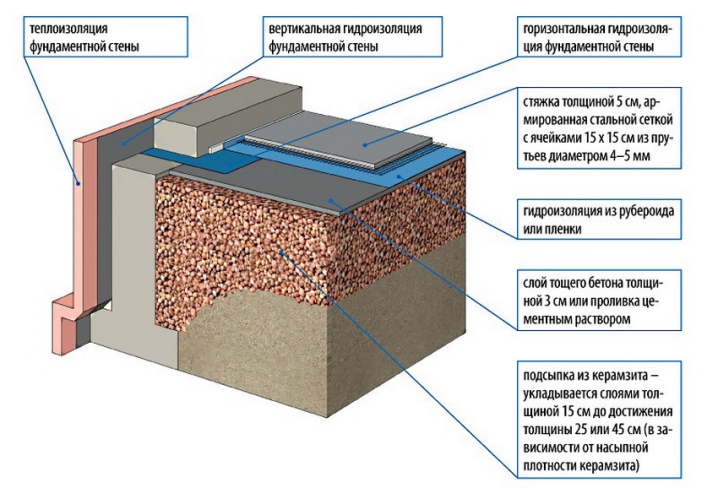
Walking on a self-built floor is possible after 24 hours, however, it will take at least a month for it to become fully durable.
When warming the surface on the ground, the expanded clay layer should be 350 mm. This indicator is very important to take into account even in the process of designing a bath, since the insulating layer will raise the floor level.
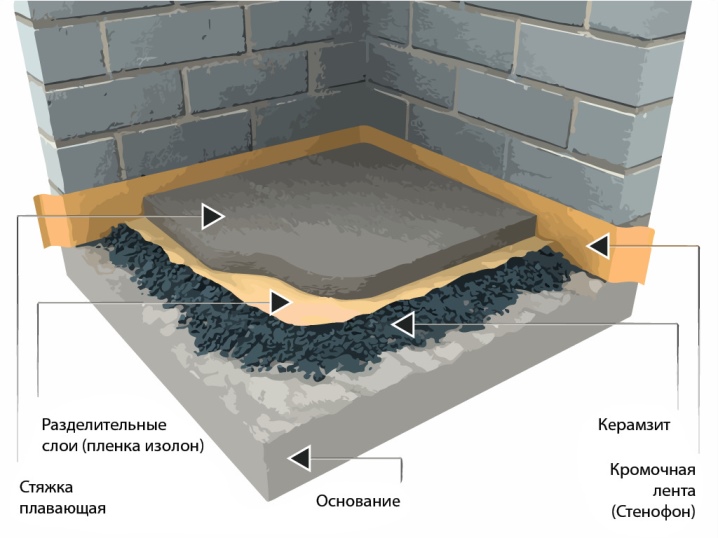
There is also another option for floor insulation - filling the material into the frame.
- In this case, a reliable base is first prepared, a layer of heat-insulating material is laid on top. Next, the frame is assembled - for this, they take bars and boards. If the floor is impressive in size, the frame base must be divided into a small number of sections - each of them is fixed, and as a result, a universal structure is created.
- Expanded clay is filled in in the same way as in the first case. A good option is to lay a membrane film under the boards (in case expanded clay is filled up between wooden beams).
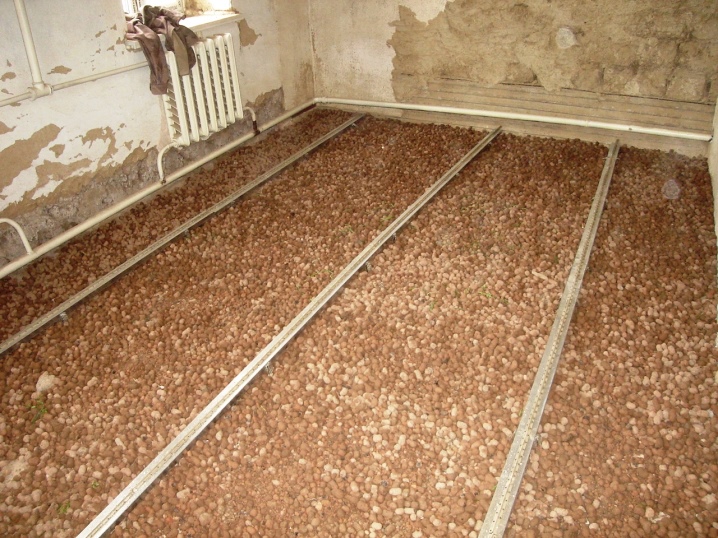
The technology of floor insulation in a room may vary - mostly inexperienced builders prefer to resort to the simplest option:
- you will need compressed soil, a mixture of sand and gravel, a vapor barrier, a concrete substrate, polystyrene foam, a polyethylene film, a reinforcing frame;
- for insulation, the base is initially prepared, leveling it from cracks and bumps;
- from above, a screed is poured from an insulating mixture.
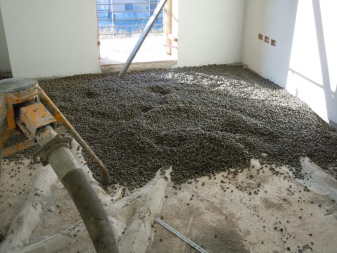
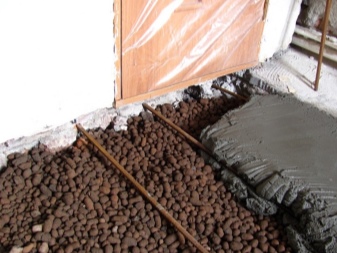
Another popular type of floor is with a floor screed. To insulate the flooring in the bath, pressed mineral wool and durable sheet polystyrene are used. The base is created from a concrete slab fixed to the walls. The lag technology is also popular. Pressed mineral wool and polystyrene are used as insulation.
Please note: usually builders use a complex solution and often fall asleep two or even three types of fractions. This is necessary for the highest efficiency of the material.
For example, if it is planned to insulate the floor covering on the ground, the central part is poured from the largest type of expanded clay, and subsequently a layer of a smaller backfill is created.
In conclusion, I would like to say that expanded clay is a fairly popular insulating material. It is non-toxic, lightweight and inexpensive compared to other materials. Do not forget that strengthening the top layer with cement milk is an obligatory stage that does not allow particles of insulation to penetrate into the air. To insulate wooden floors, they are first treated with an antiseptic solution.
How to insulate the floor with expanded clay, see the video.
The comment was sent successfully.