All about chamotte mortar
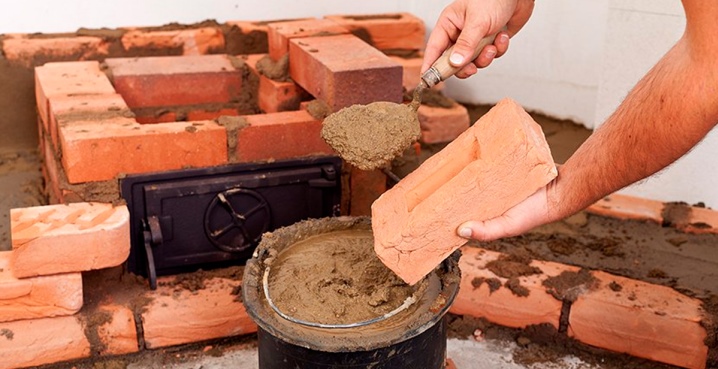
Fireclay mortar: what it is, what is its composition and features - the answers to these questions are well known to professional stove-makers, but amateurs should get better acquainted with this type of masonry materials. On sale you can find dry mixes with the designation MSh-28 and MSh-29, MSh-36 and other brands, the characteristics of which fully correspond to the tasks set for the refractory composition. To understand why fireclay mortar is needed and how to use it, detailed instructions for the use of this material will help.

What it is
Fireclay mortar belongs to the category of special-purpose mortars used in the furnace business. The composition is distinguished by high refractory properties, better tolerates an increase in temperature and contact with open fire than cement-sand mortars. It includes only 2 main ingredients - chamotte powder and white clay (kaolin), mixed in a certain proportion. The shade of the dry mixture is brown, with a fraction of gray inclusions, the size of the fractions does not exceed 20 mm.
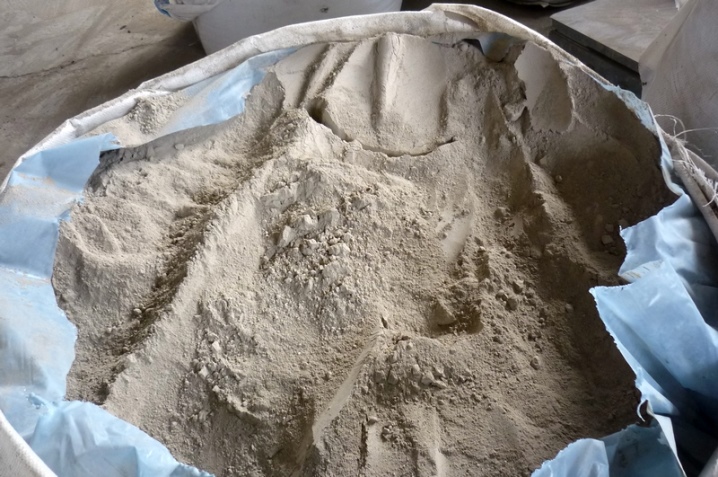
The main purpose of this product - creation of masonry using refractory fireclay bricks. Its structure is similar to that of the mixture itself. This allows you to achieve increased adhesion, eliminates cracking and deformation of the masonry. A distinctive feature of chamotte mortar is the process of its hardening - it does not freeze, but is sintered with brick after thermal exposure. The composition is packaged in packages of different sizes; in everyday life, options from 25 and 50 kg to 1.2 tons are most in demand.
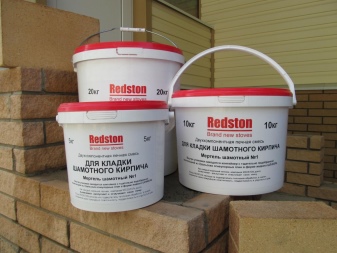
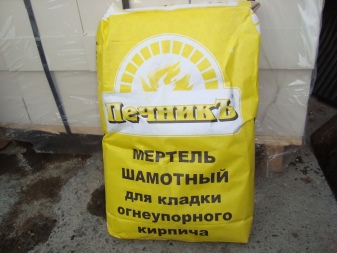
The main characteristics of fireclay mortar are as follows:
- heat resistance - 1700-2000 degrees Celsius;
- shrinkage on ignition - 1.3-3%;
- humidity - up to 4.3%;
- consumption per 1 m3 of masonry - 100 kg.
Refractory fireclay mortars are easy to use. Solutions from them are prepared on a water basis, determining their proportions based on the specified masonry conditions, requirements for its shrinkage and strength.
The composition of fireclay mortar is similar to that of a brick made of the same material. This determines not only its heat resistance, but also other characteristics.
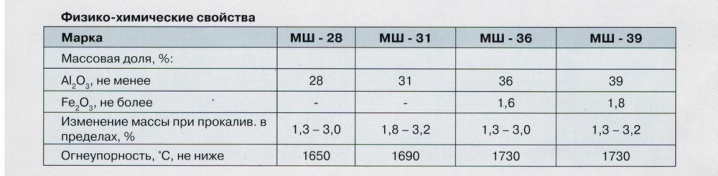
The material is completely safe for the environment, non-toxic when heated.
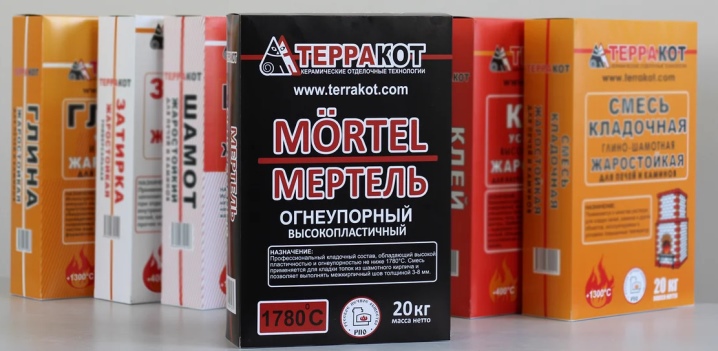
What is different from fireclay clay
The differences between chamotte clay and mortar are significant, but it is difficult to say which material is the best for its tasks. The specific composition is of great importance here. Fireclay mortar also contains clay, but it is a ready-made mixture with aggregates already included. This allows you to immediately proceed to work with the solution, diluting it with water to the desired proportions.
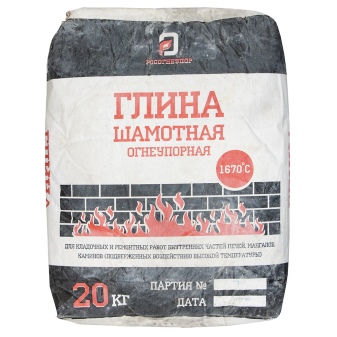
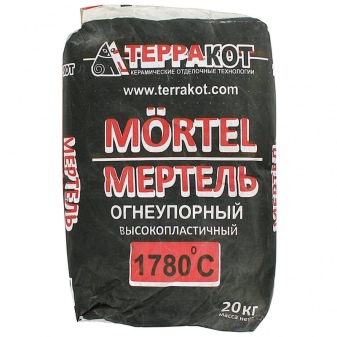
Fireclay - a semi-finished product that requires additives. Moreover, in terms of the degree of fire resistance, it is noticeably inferior to ready-made mixtures.
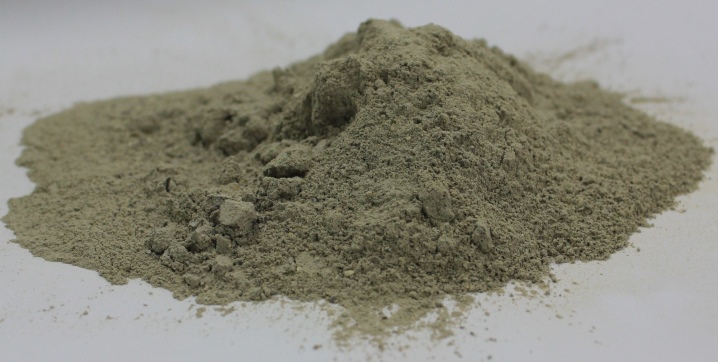
The mortar has its own characteristics - it must be used only in tandem with fireclay bricks, otherwise the difference in the density of the material during shrinkage will lead to cracking of the masonry.
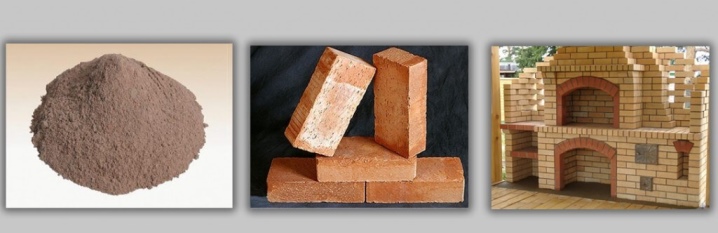
Marking
The fireclay mortar is marked with letters and numbers. The mixture is designated by the letters "MSh". The numbers indicate the percentage of components. On the basis of refractory aluminosilicate particles, plasticized mortars with other markings are produced.
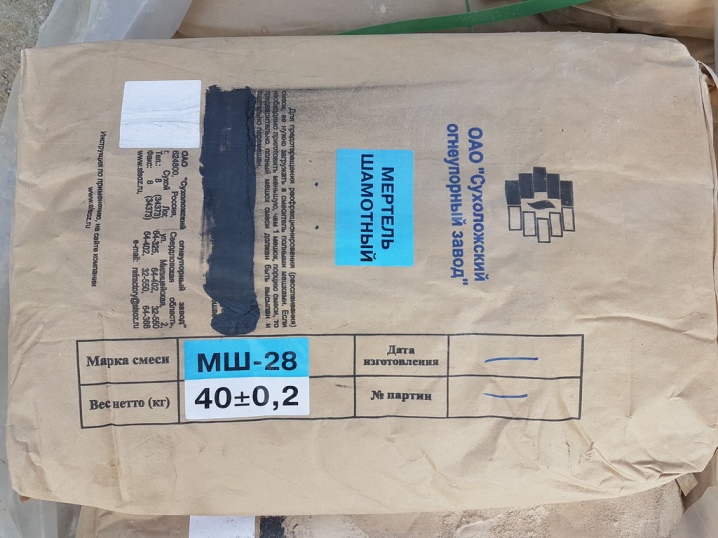
The higher the specified number, the better the heat resistance of the finished composition will be. Aluminum oxide (Al2O3) provides the mixture with the specified performance characteristics. The following grades of fireclay mortar are standardized by the standards:
- MSh-28. A mixture with an alumina content of 28%. It is used when laying fireboxes for household stoves, fireplaces.
- MSh-31. The amount of Al2O3 here does not exceed 31%. The composition is also focused on not too high temperatures, it is used mainly in everyday life.
- MSh-32. The brand is not standardized by the requirements of GOST 6237-2015, it is manufactured according to TU.
- MSh-35. Bauxite-based fireclay mortar. Aluminum oxide is contained in a volume of 35%. There are no inclusions of lignosulfates and sodium carbonate, as in other brands.
- MSh-36. The most common and popular composition. Combines fire resistance in excess of 1630 degrees with an average alumina content. It has the lowest mass fraction of moisture - less than 3%, fraction size - 0.5 mm.
- MSh-39. Fireclay mortar with refractoriness over 1710 degrees. Contains 39% aluminum oxide.
- MSh-42. Not standardized by GOST requirements. It is used in furnaces where the combustion temperature reaches 2000 degrees Celsius.
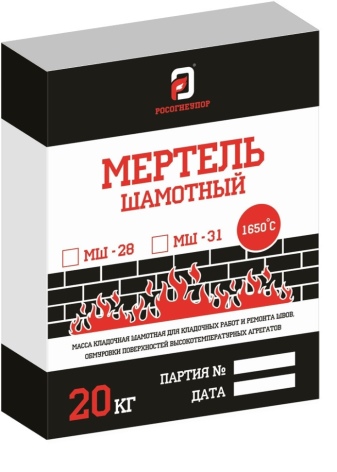
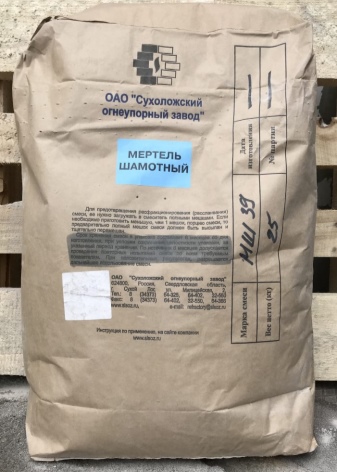
In some brands of fireclay mortar, the presence of iron oxide in the composition is allowed. It can be contained in mixtures MSh-36, MSh-39 in the amount of not more than 2.5%. Fraction sizes are also normalized. So, the MSh-28 brand is considered the largest, the granules reach 2 mm in a volume of 100%, while in the variants with increased refractoriness, the grain size does not exceed 1 mm.
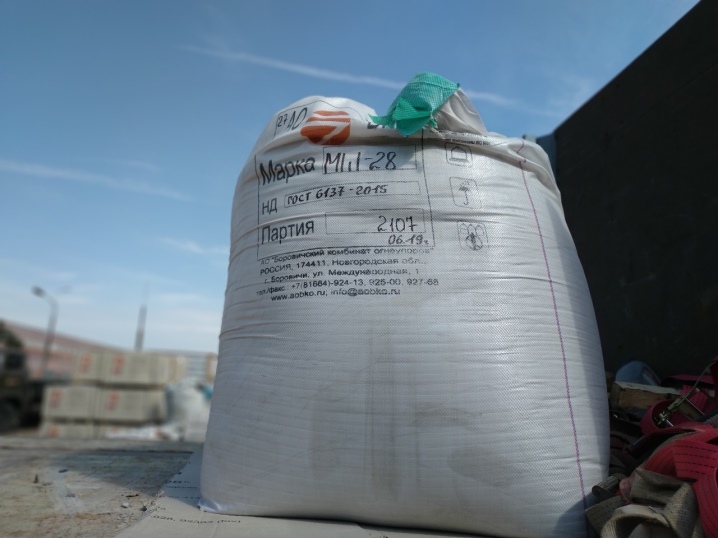
Instructions for use
A solution of fireclay mortar can be kneaded on the basis of ordinary water. For industrial furnaces, the mixture is made using special additives or liquids. The optimal consistency should resemble liquid sour cream. Mixing is carried out manually or mechanically.
It is quite simple to properly prepare fireclay mortar.
It is important to achieve such a state of the solution that it remains pliable and elastic at the same time.
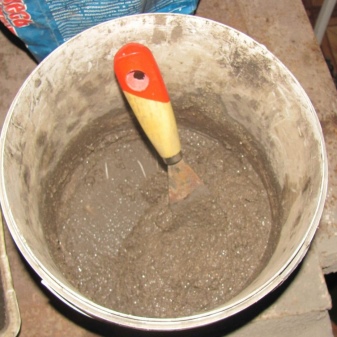
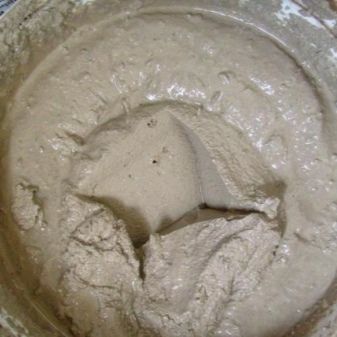
The composition should not delaminate or lose moisture until it joins the brick. On average, the preparation of a solution for the oven takes from 20 to 50 kg of dry powder.

Consistency may vary. The proportions are as follows:
- For masonry with a seam of 3-4 mm, a thick solution is prepared from 20 kg of chamotte mortar and 8.5 liters of water. The mixture turns out to be similar to viscous sour cream or dough.
- For a seam of 2-3 mm, a semi-thick mortar is needed. The volume of water for the same amount of powder is increased to 11.8 liters.
- For the thinnest seams, the mortar is kneaded very thin. For 20 kg of powder, there are up to 13.5 liters of liquid.
You can choose any cooking method. Thick solutions are easier to mix by hand. Construction mixers help to give homogeneity to liquids, ensuring an even connection of all components.
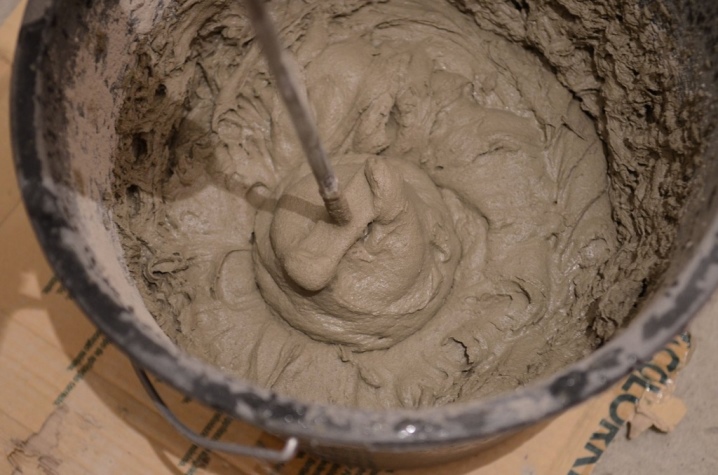
Since dry mortar produces strong dust, it is recommended to use a protective mask or respirator during work.
It is important to know that first, dry matter is poured into the container. It is better to measure the volume right away so that you do not have to add anything during the kneading process. Water is poured in portions, it is better to take soft, purified water in order to exclude possible chemical reactions between substances. The finished mixture should be homogeneous, without lumps and other inclusions, sufficiently elastic. The prepared solution is kept for about 30 minutes, then the resulting consistency is evaluated, if necessary, diluted again with water.
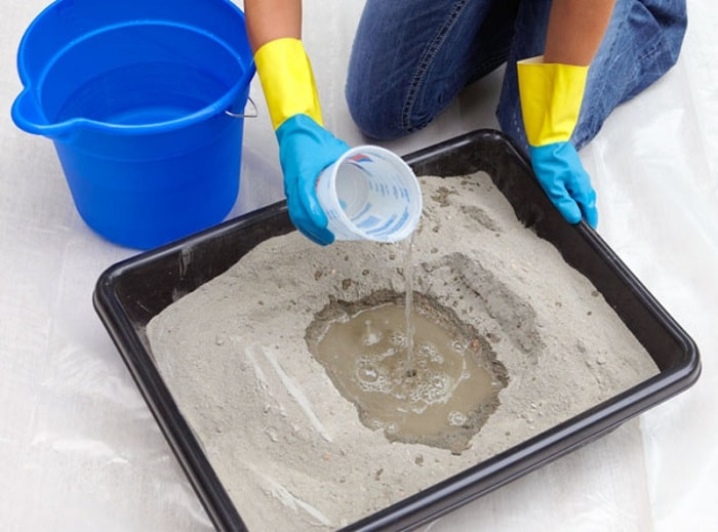
In some cases, fireclay mortar is used without additional heat treatment. In this version, methylcellulose is included in the composition, which ensures the natural hardening of the composition in the open air. Chamotte sand can also act as a component, which makes it possible to exclude cracking of masonry seams. It is strictly forbidden to use a cement binder in clay-based formulations.
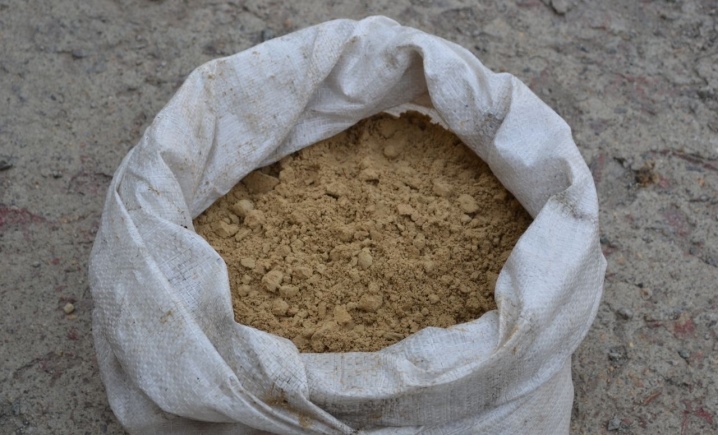
The solution for cold hardening of the mixture is prepared in the same way. A trowel helps to check the correct consistency. If, when displaced to the side, the solution breaks, it is not elastic enough - it is necessary to add liquid. Slipping of the mixture is a sign of excess water, it is recommended to increase the volume of the thickener.
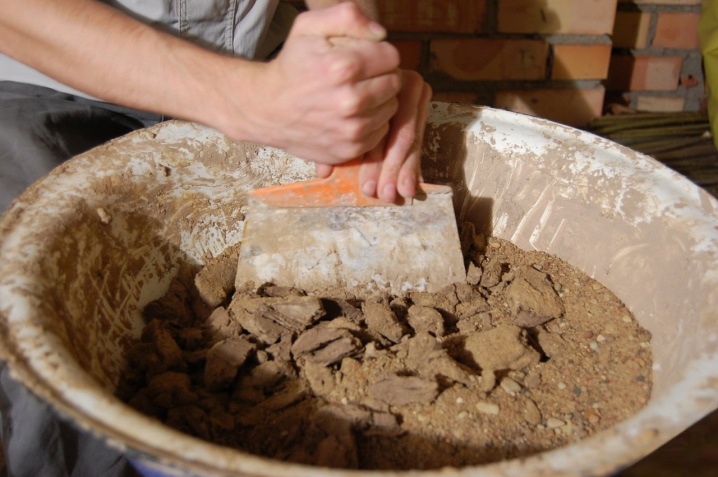
Masonry features
The ready-made mortar can only be placed on a surface that has been previously freed from traces of old masonry mixtures, other contaminants, and traces of limescale. It is unacceptable to use such compositions in combination with hollow bricks, silicate building blocks. Before laying the fireclay mortar, the brick is thoroughly moistened.
If this is not done, the binder will evaporate faster, reducing the strength of the bond.
The laying order has the following features:
- The firebox is formed in rows, according to a previously prepared scheme. Beforehand, it is worth performing a test installation without a solution. Work always starts from the corner.
- A trowel and jointing are required.
- The filling of the joints should take place throughout the entire depth, without the formation of voids. The choice of their thickness depends on the combustion temperature. The higher it is, the thinner the seam should be.
- The excess solution protruding on the surface is immediately removed. If this is not done, it will be quite difficult to clean the surface in the future.
- Grouting is done with a damp cloth or a bristle brush. It is important that all internal parts of channels, fireboxes, and other elements are as smooth as possible.
Upon completion of the masonry and trowelling works, fireclay bricks are left to dry in natural conditions with mortar mortar.
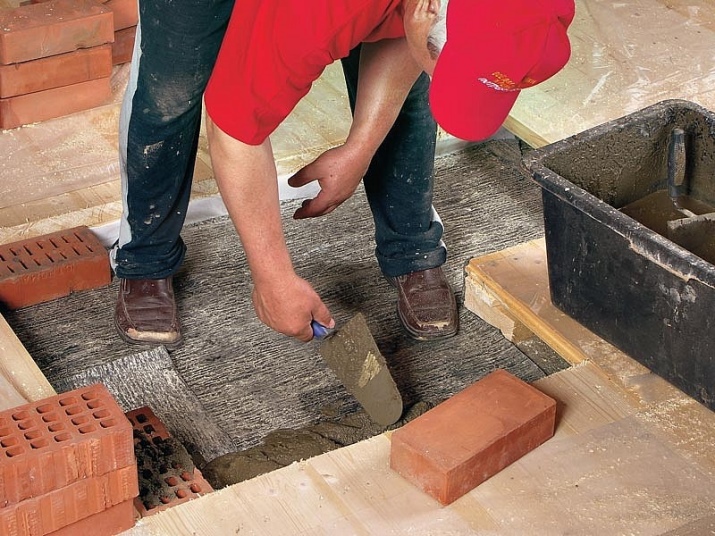
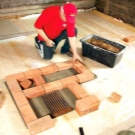
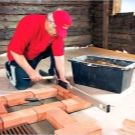
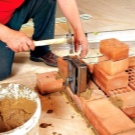

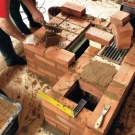
How to dry
Drying of fireclay mortar is carried out by repeated kindling of the furnace. Under thermal action, fireclay bricks and mortar are sintered, forming strong, stable bonds. In this case, the first ignition can be carried out no earlier than 24 hours after the completion of the laying. After that, drying is carried out for 3-7 days, with a small amount of fuel, the duration depends on the size of the furnace. The ignition is carried out at least 2 times a day.
During the first kindling, the amount of wood is laid, corresponding to the burning time of about 60 minutes. If necessary, the fire is supported additionally by adding materials. With each successive time, the volumes of burning fuel are increased, achieving gradual evaporation of moisture from bricks and masonry joints.
A prerequisite for high-quality drying is to keep the door and valves open - so the steam will escape without falling out in the form of condensate when the oven cools down.
A completely dry mortar changes its color and becomes harder. It is important to pay attention to the quality of the masonry. It should not crack, deform with the correct preparation of the solution. If there are no defects, the stove can be heated as usual.
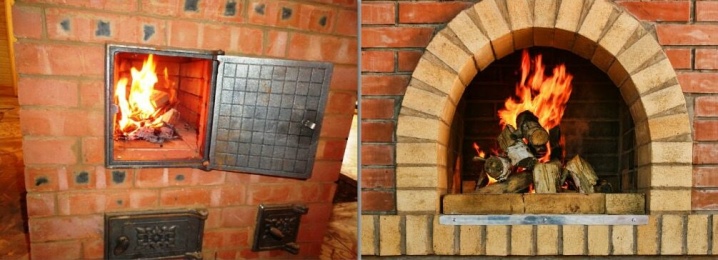
How to properly lay fireclay bricks using a mortar, you can learn from the following video.
The comment was sent successfully.