Baths made of expanded clay concrete blocks: advantages and disadvantages

For decades and even centuries, baths have been associated with wooden and brick buildings. But this does not mean that you cannot consider other materials (for example, ceramic blocks), choose them properly and apply them. One of the most modern and practical options is expanded clay concrete, which has a number of positive aspects.
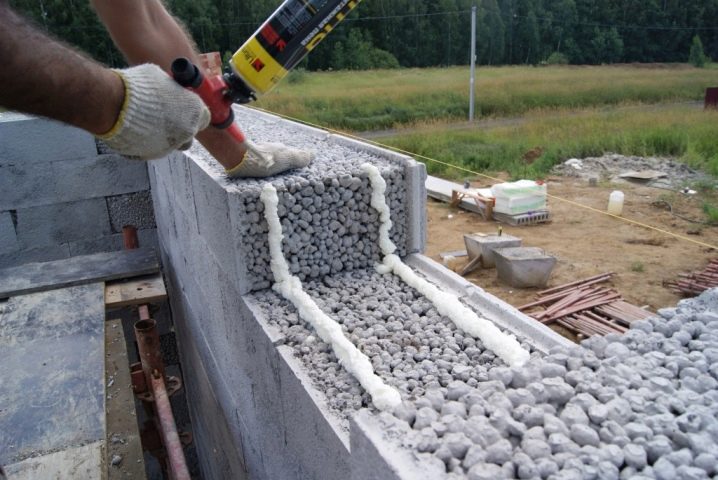
Peculiarities
The traditional view of the bathhouse as a log structure using wooden beams is still popular. Actually, the bath can be made of any material that meets the following requirements:
- retention of heat;
- insignificant water absorption;
- decent fire-fighting properties;
- environmental Safety.
Expanded clay concrete blocks fully meet these requirements, and even surpass specially treated wood in terms of fire protection.

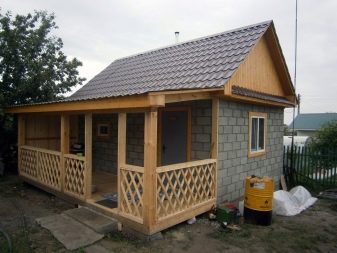
The basis of this material is, as the name implies, expanded clay, that is, clay balls that have been fired. Building blocks are formed by combining expanded clay with a cement-sand mixture; the combination of substances then needs to be moistened, shaped and passed through vibrating presses. The choice between a fine and a coarse fraction of the material is determined, first of all, by how light the blocks should be created: if the size of the balls is large, lightweight expanded clay concrete structures are obtained from it.
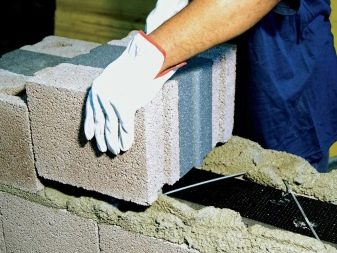
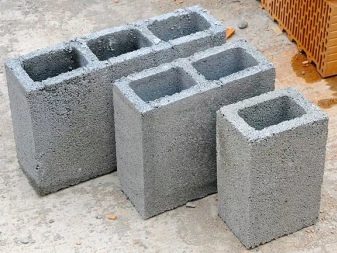
Advantages and disadvantages
Expanded clay concrete almost does not absorb water, which makes it one of the best options for buildings with a high level of humidity inside or outside. An undoubted plus will be the fact that this material is stronger than foam concrete, aerated concrete, ceramic blocks and perfectly stabilizes wall fastenings. Expanded clay multi-slot blocks (these are the ones that should be used in baths) are supposed to be lubricated with mortar only along the outer contour. To ensure the tightness of internal voids, it is advisable to use a jute-based insulation. This allows you to automatically remove the problem of external insulation of the steam room.
It is possible to build a bath from expanded clay blocks much faster than from other materials. After all, each block replaces an average of 12 rows of bricks, depending on the size of the structure the developer chooses. Importantly, the cycle of construction work is not interrupted, since expanded clay concrete does not shrink, unlike wood, which requires waiting from three months to six months.
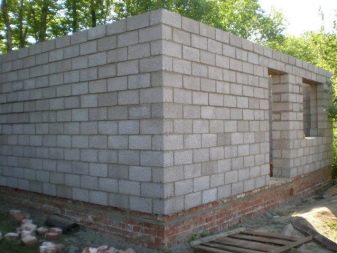
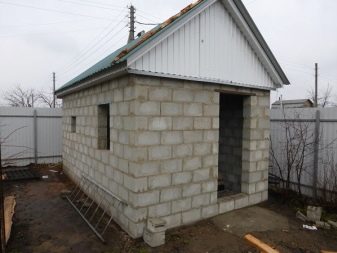
Installation is extremely simple, even for those who know very little about block stacking. And very few tools are required.
There is no need to use a masonry mixture; the wall will be very flat, no finishing is needed before the facade work begins. The total cost of all work, even taking into account the projects, will be 1.5-2 times lower than when using a tree. The bathhouse will last at least a quarter of a century.
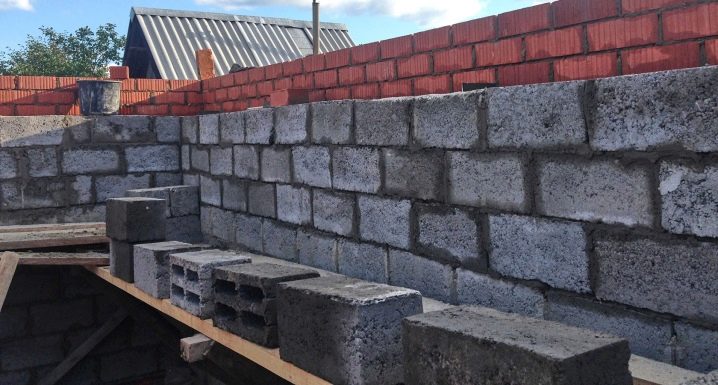
Expanded clay concrete also has several weak points that all developers should definitely know:
- it is impossible to build a bathhouse above two floors;
- the material does not tolerate mechanical destruction very well;
- lining of both the inner and outer planes must be carried out.
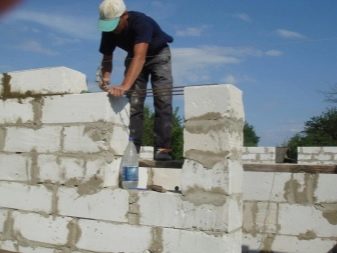
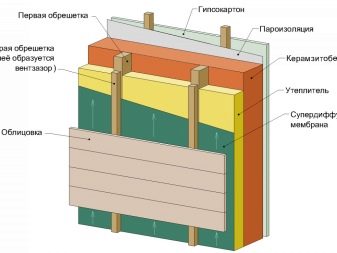
Views
Expanded clay concrete blocks are quite diverse in their design. So, modern versions of them are able to endure up to 300 cycles of heating and freezing, which is very decent even for a bath room.But, of course, this does not negate the need for good insulation and waterproofing, both inside and outside. The strength grade varies from M25 to M100, this figure expresses the calmly tolerated impact (in kg per 1 cubic cm). For the needs of housing construction, only blocks not weaker than M50 can be used, all the others are suitable only for outbuildings.
It is important to consider that the stronger the type of block, the denser and heavier it will be. Sometimes, even the small thickness of the walls made of dense expanded clay concrete does not allow them to be significantly lightened. The specific weight of a particular block can reach 400 kg per 1 cubic meter. m.
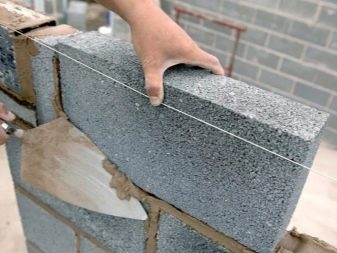
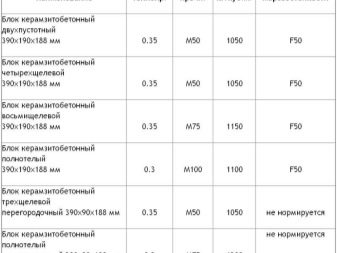
It is also customary to divide expanded clay blocks into:
- wall;
- used for partitions;
- ventilation (in which holes are initially prepared for the passage of air and for the passage of air pipes);
- foundation (the most durable and heavy, it is undesirable to use them to form the walls of the 2nd floor of the bath).
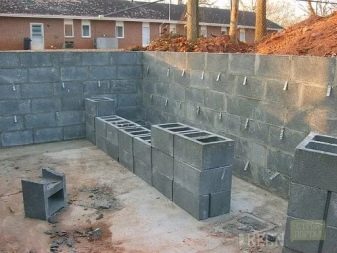
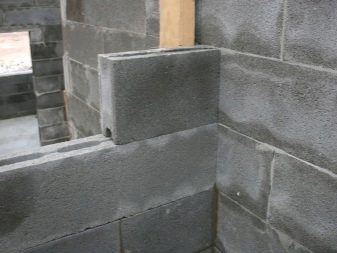
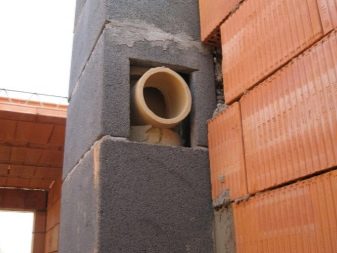
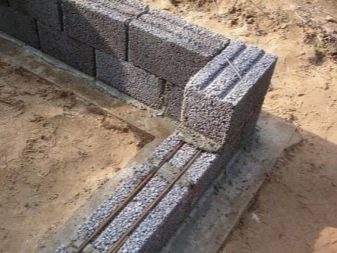
Full-weight products made of expanded clay concrete, due to the elimination of cavities, are more mechanically stable, but hollow versions are lighter and make it possible to radically improve the thermal insulation of the bath. The properties of voids can be very different, in some cases blocks with two voids are best suited, in others - with seven slots, and so on. Differences are also manifested in the number of facing planes: in some structures there are not one, but two such planes.
It is useful to choose an option with a front finished layer when there is an intention to abandon the decoration of the outer side of the bath.
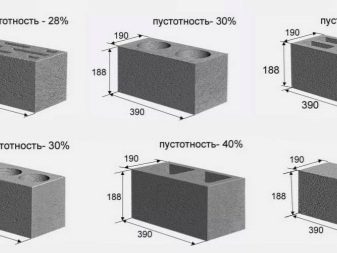
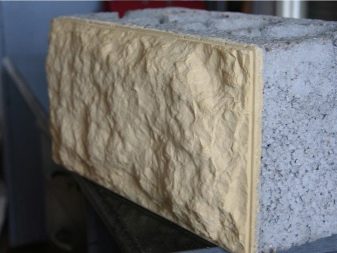
By texture, expanded clay blocks are often subdivided into:
- smooth (there should not be even the slightest traces of machining);
- subjected to grinding;
- corrugated (with geometrically precise distribution of depressions and grooves on the block surface);
- chipped, or Besser (the most commonly used variety).
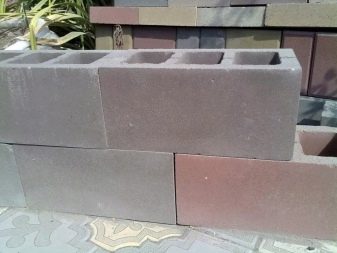
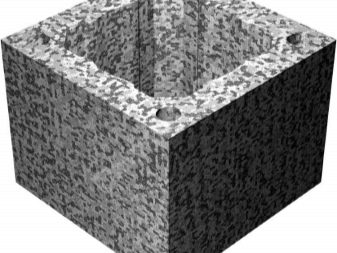
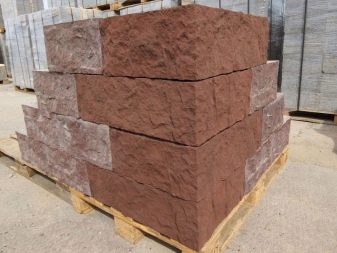
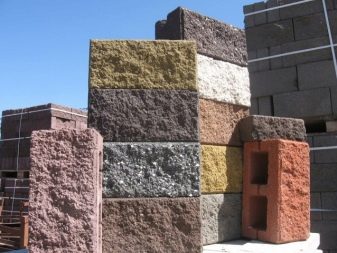
Almost any color can be used: modern technologies allow customers to get the desired result in a relatively short time.
Which projects to choose?
When choosing a project for a bath from expanded clay blocks, you need to give preference to those options that do not contain bends, arched structures and other uneven shapes. You can use them, but this immediately increases the cost of work many times over and makes the building structure less strong. In typical projects, a pitched roof is often provided over a building measuring 6x4 or 6x6 m, although anyone can revise these values and remake the project to suit their tastes or the characteristics of the site.
Judging by the reviews, it is best to work out projects using computer programs. A three-dimensional model of a future building shows it much more perfect and more accurately than any diagram drawn on paper. In this way, it is possible to facilitate the calculation of the location of window and door blocks, more accurately calculate the need for building materials.
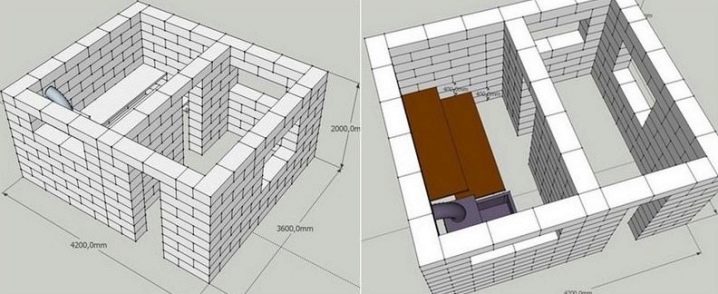
Construction process
Any step-by-step instruction cannot ignore such a moment as the construction of a foundation. Since expanded clay concrete is relatively light, it is possible to form a strip base with a shallow depth. This is very economical, but when there is no complete confidence that the soil will be stable enough, you will need to contact geologists to investigate the area. With the slightest doubt, it is worth deepening the basis of the structure under the border of soil freezing. Strictly according to the drawing, the space is marked out to create future walls and internal partitions.
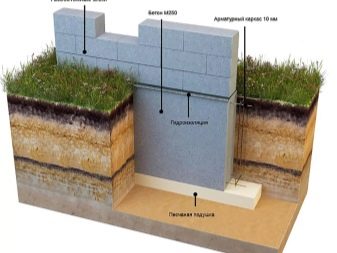
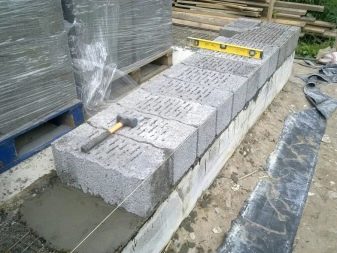
Further construction is carried out as follows:
- digging a pit;
- a pillow of sand and gravel is poured;
- formwork is made under the monolithic foundation, reinforcement is placed and mortar is poured over it;
- as a replacement, a set of expanded clay concrete parts with fine grain can be used;
- wait until the foundation is settled (the monolithic version - at least 30 days, and the masonry of expanded clay blocks - at least 7 days);
- the base is covered with a layer of waterproofing - not only the top, but also the side.
Strengthening the bearing qualities of the foundation is achieved due to the reinforcing mesh, and one or two layers of roofing material will help to ensure the proper level of waterproofing.
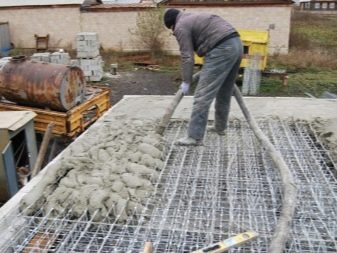
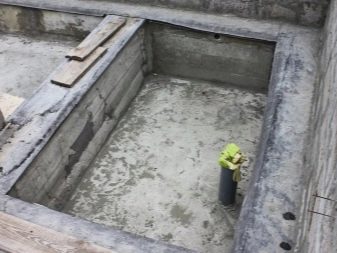
Next, a box is built, which they begin to mount from the highest corner of the base. Immediately after placing the first row of parts, their level is carefully checked, and if the slightest deformations are found, they must be corrected with wedges. Whether working with your own hands or hiring builders, you cannot divide the construction of the box into stages. The shorter the time intervals between the successive stacking of blocks, the better the result achieved and the lower the risk of making a serious mistake. In the same way, you need to immediately remove the excess concentration of solutions and open the seams.
The most durable structure is created if every 4th or 6th row is reinforced. In large baths, the uppermost row is sometimes reinforced with a reinforced concrete belt.
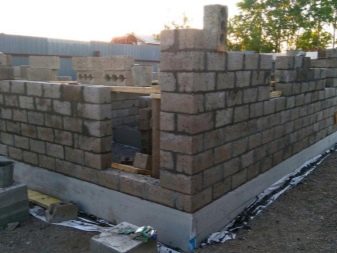
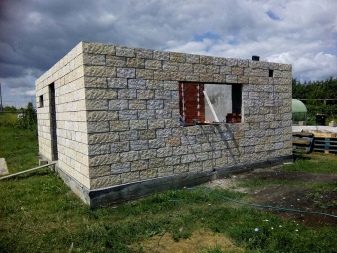
The construction of truss systems and roofs does not differ significantly from the construction of similar parts of a residential building:
- first beams are laid;
- rafters are placed on them;
- a layer of waterproofing, vapor barrier and thermal insulation is created;
- the roof is formed (the choice of slate, tiles, metal or any other solution is determined by specific conditions).
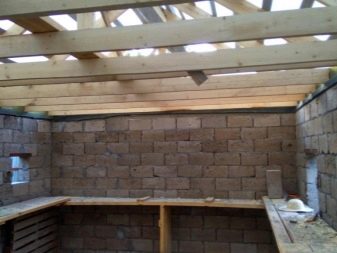
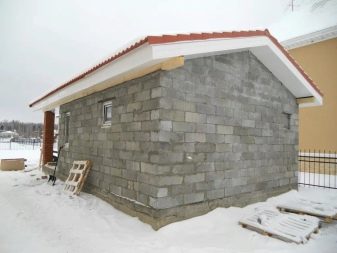
Exterior decoration, although not needed for technical reasons, is very useful, since it increases the evenness of the walls and their resistance to external influences. At the same time, the costs are relatively small, and the structure will be much more aesthetically pleasing. Brick cladding is not the only option, the use of embossed plaster, plastered surfaces for painting, hinged facades and many other solutions has been worked out. If a decision is made to additionally insulate the bath, it is advisable to choose the most environmentally friendly materials, the same requirement applies to the products with which the bath buildings will be wrapped inside.
Before the start of finishing work, all communications are supposed to be carried out. Among all natural materials, the first place in finishing should be given to high-quality wood, since it best matches a traditional sauna. After finishing, it will be right to immediately install the stove, buy (or do it yourself) sun loungers and the rest of the furniture.
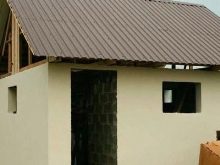
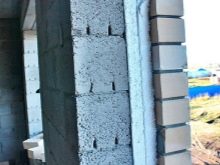
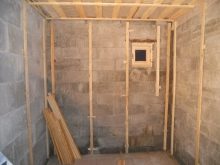
Tips & Tricks
- In the uppermost row of walls, niches for beams are necessarily provided. Taking into account the selected roofing material, the pitch of the lathing is determined. The niches dividing the rafters are filled with heat-insulating materials, on top of which a vapor barrier is placed. Among all the premises of the bath, the steam room needs insulation most of all, where the floor insulation is laid with an overlap of about 0.2 m on the walls.Only then the walls themselves are insulated, the sheathing step is made the same width of the insulating material. The reflector is overlapped and glued on top.
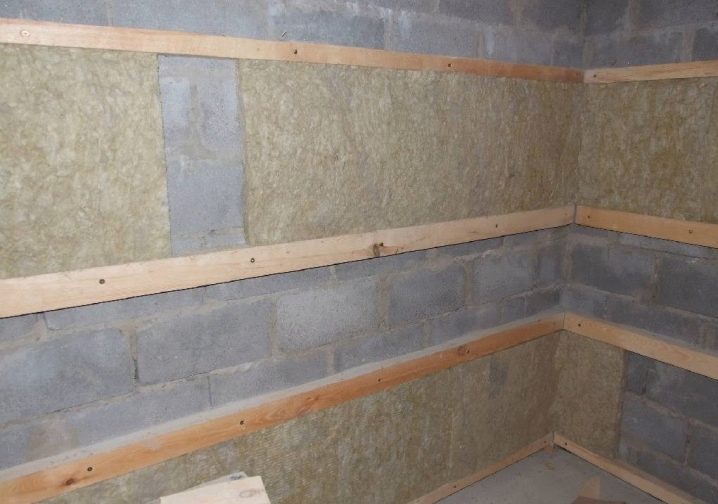
- The optimal laying of the walls is half a block, that is, 30 cm thick. The rows are laid according to the "ligation" scheme, which allows sequential overlap of the seams. For the preparation of solutions, a cement-sand mixture is recommended (1 share of cement and 3 shares of sand in the volume of dry powder). Add just enough water to balance the binding properties and density of the material. The joint width is 20 mm; both standard and thinner blocks can be used for the partitions.
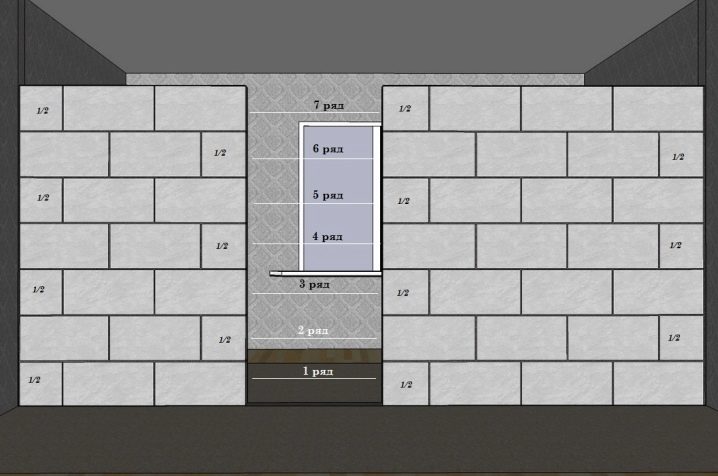
- To protect the outer walls from wind, precipitation and give them a pleasant appearance, it is best to use cement plaster, which is kneaded from one part of cement and four parts of sand. When finishing, two layers are applied with an interval of a day, each layer is rubbed immediately after application until completely homogeneous with a special construction float. As a topcoat, paint for facades based on acrylic resins is widely used.
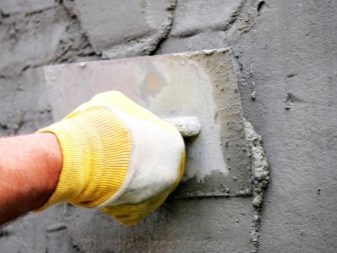
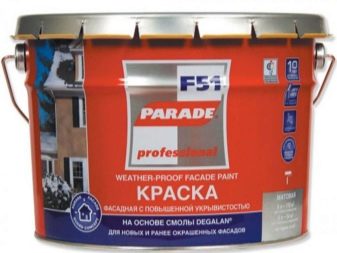
See the next video for more on this.
The comment was sent successfully.