Comparison of wood concrete with various materials
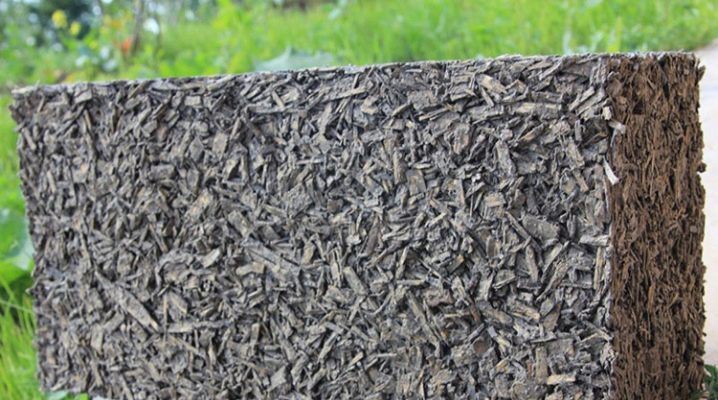
One of the most relevant and demanded industries today is the construction industry. After all, people will always dream of their own housing and improving living conditions. And the more often new building materials appear, the more opportunities there will be to build a quality building. For example, arbolite. This novelty has already become as popular as expanded clay concrete. But which one is better?
According to the statistics of the Google Trend service, search queries on the Russian Internet regarding arbolite are much more popular than questions about its counterparts.
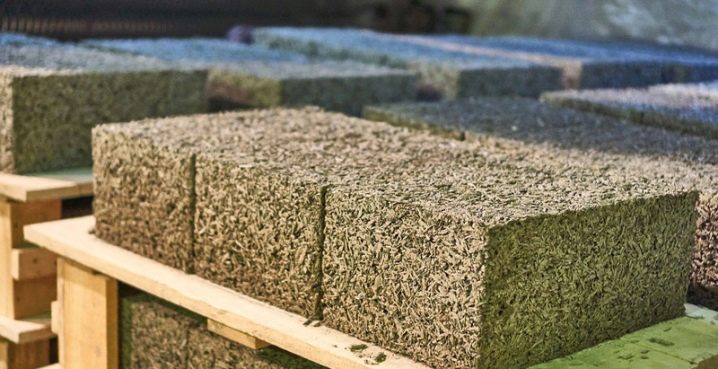
Characteristics of wood concrete
This is a type of lightweight concrete, consisting of 80-90% organic matter, chemical additives, water and cement. The main raw materials can be shredded wood chips, flax or hemp fire, shredded cotton stalks or rice straw. In another way, this component is called wood concrete.
It appeared in the 30s of the XX century in Holland. Due to its environmental friendliness, heat-saving and sound-insulating properties, the building material is widely used in the USA, Canada and European countries.
The combination of wood waste and cement mortar makes the wood concrete block a unique composition characterized by the properties of these two components.
... And in order to increase the level of adhesion of wood and cement, mineralization is necessary.
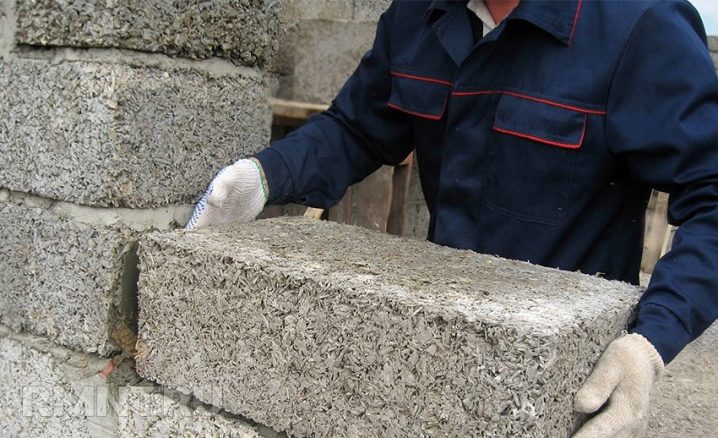
This process involves chemical additives such as aluminum sulfate, calcium chloride and nitrate, and water glass. Thus, the influence of organic matter on the hardening of concrete is neutralized.
Arbolite has an excellent thermal conductivity (0.08 - 0.17 W / m · K) and a good density (400 - 850). The strength is evidenced by high frost resistance (25-50 cycles) and shrinkage resistance (0.4-0.5). Such properties guarantee a long service life of the structure. Also, the material has good fire resistance and noise absorption (0.17-0.6). It has excellent compressive strength (0.35 - 3.5 MPa), flexural strength (0.7 - 1.0 MPa) and high moisture absorption (up to 40-85%).
Heat-insulating plates and mixtures for fillings are made of wood concrete. But the most demanded product is blocks.
They are produced in standard sizes 500 x 300 x 200 mm. The material is used for the construction of walls of low-rise buildings (up to 3 floors). According to the manufacturer's assurances, one layer of wood concrete foam blocks is quite enough to preserve heat.

Production technology
Today, several methods are used for the manufacture of wall blocks for external and internal walls. Most often they are produced by direct pressing or by means of vibration casting (vibrocompression).
The first method is a relatively young and fairly low-cost technology. It provides for daily exposure of wood concrete in forms. But the resulting mass is not homogeneous, which threatens with internal stresses in the finished product.
Vibration casting is a traditional method that has been proven over the years. The components in the mixture are evenly distributed and, as a result, a better quality block is obtained.
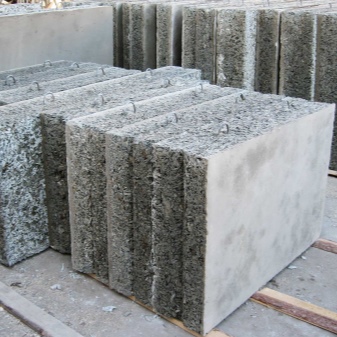
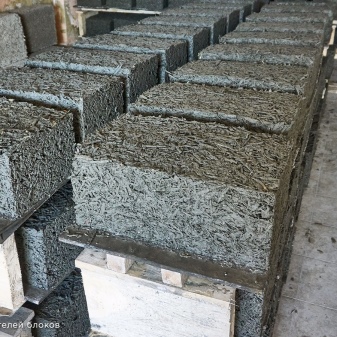
However, the basic manufacturing process in both methods is the same.
It consists of three important steps.
- Sorting and crushing organic matter.
- Mixing wood chips with chemicals, cement and water. The operation takes 10 minutes.
- Forming and drying of the finished solution.
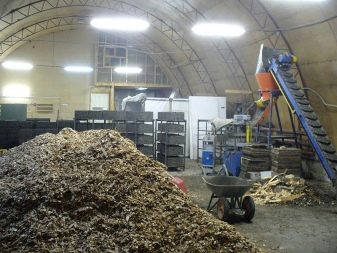
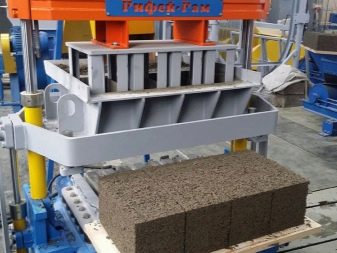
Varieties
There are several types of wood concrete depending on the compressive strength indicators.
- Heat insulating... It is characterized by low compressive strength and low density. In this regard, it can withstand loads poorly. It is used only for thermal insulation purposes.
- Structural and heat-insulating... This material has a strength of 1.5 - 2.5 and is used in the construction of walls and partitions. The composition is characterized by low density and low thermal conductivity.
- Structural... This is the most durable type. The compressive strength index reaches up to 3.5 MPa, and the density index - up to 1200 kg / m³. It is used for laying structures up to 3 floors. However, a structure constructed from such blocks will need additional thermal protection.
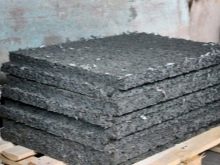
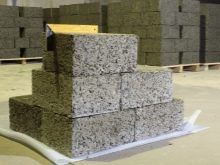
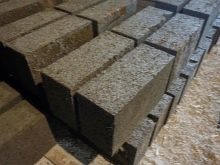
Advantages and disadvantages
Arbolit has a huge number of advantages compared to other building materials.
- Environmental friendliness of raw materials... It is made mainly from natural ingredients.
- High fire resistance... Despite the fact that arbolite mainly consists of wood waste, it is not flammable.
- Good vapor permeability... This property allows buildings to breathe and maintain their microclimate.
- Low weight of wood blocks... This factor greatly simplifies construction.
- Easy processing with cutting tools... The block can be easily shaped to any desired shape.
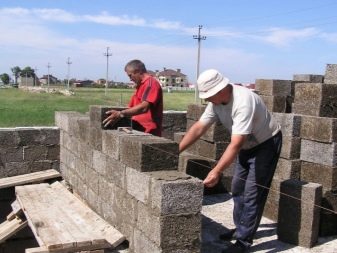
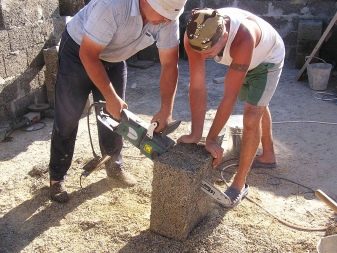
- Ease of handling... When laying wood concrete blocks, they do not require professional skills.
- Mold resistant, fungi and pests. The material has IV class of biostability.
- High thermal conductivity... For this reason, wood concrete is often used in the construction of private houses.
- Shrinkage resistance... In this case, walls and partitions will not crack.
- High sound absorption... Thanks to this, the material can also be used for the construction of industrial buildings.
- Seismic resistance.
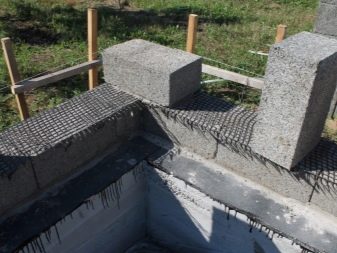
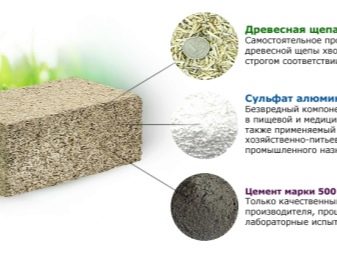
The disadvantages include the following factors.
- If you do not take measures to protect against moisture, wood concrete quickly begins to decompose, losing its properties.
- The blocks do not have a perfectly flat surface due to the characteristic features of the composition.
- Arbolite walls require additional finishing.
- The material has a low level of adhesion to plaster mixtures.
- Due to the huge number of handicraft industries, poor-quality goods are often found on the market.
- Poor assortment of products.
- The lack of large-scale production affects the high cost of the material and difficulties with delivery.
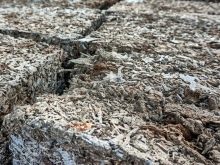
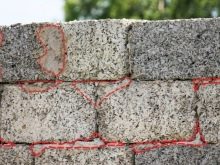
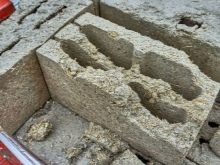
Comparison with other materials
For the construction of a residential building or outbuilding, it is very important to choose the right building components. But you should know that there are no good or bad materials, there are only suitable and not very good ones.
- Expanded clay concrete... Like wood concrete, it is an environmentally friendly material and belongs to the class of lightweight concrete. It consists of expanded clay (burnt clay or shale), cement, sand and water. However, expanded clay blocks have an indicator of thermal conductivity (0.5 - 0.7 W / m · K), that is, slightly worse than that of wood concrete. Therefore, for the house, from the point of view of keeping warm, it is better to choose wood blocks. Despite its higher strength, expanded clay concrete may not withstand excess pressure. This is due to the hollow space inside the product.
Arbolite has good bending and impact strength.
- Foam concrete... It is a porous concrete consisting of cement, sand, water and a foaming agent. Blocks made of it have a good margin of safety, however, unlike wood concrete, they practically do not work in bending and give a large shrinkage. The thermal conductivity coefficient is better than that of expanded clay concrete (0.14 - 0.5 W / m · K), but worse than that of wood concrete.

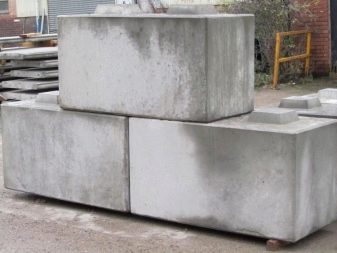
- Sawdust concrete... In composition, this material is very similar to wood concrete. In both cases, wood waste is used.Just like wood concrete is considered an environmentally friendly building material, it has high heat-shielding qualities and is resistant to stretching, bending and impact.
- Aerated concrete... The cellular composition consists of sand, cement, water and a blowing agent, due to which the characteristic porosity appears. Unlike wood concrete, the aerated block has a clear geometry of the product. The material is characterized by high water resistance and fragility. If we compare this material and wood concrete, then in many respects aerated concrete wins.
However, when building a 2-3-storey house with an attic, it is better to give preference to the second component, since it is able to withstand heavy loads.
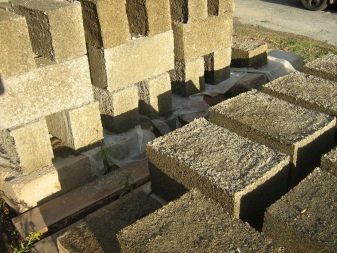
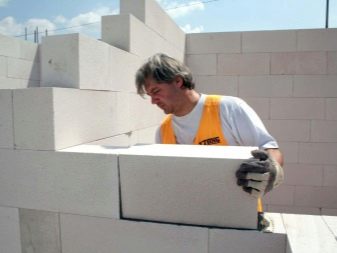
- Polystyrene concrete... This is a type of lightweight concrete, consisting of Portland cement, expanded polystyrene granules and air-entraining additives. It is distinguished by its high structural strength. Gives shrinkage, but much less than gas blocks and foam blocks. As well as wood concrete, it has good thermal insulation properties. Polystyrene concrete blocks do not need additional insulation.
- Straw blocks... They are a building material consisting of environmentally friendly raw materials - pressed straw. Straw blocks have a better thermal conductivity index than wood concrete (0.05 - 0.065). But they also have disadvantages such as high moisture absorption and low fire resistance.
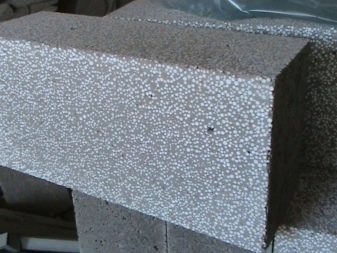
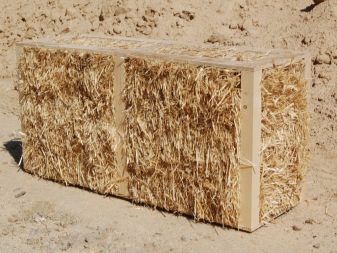
- Beams... It is a highly eco-friendly breathable material made of glued boards or logs. Differs in a remarkable indicator of thermal conductivity and high strength. It is a worthy competitor to wood concrete.
- Gas silicate... This cellular material is obtained from a solution of fine sand, lime, blowing agents and water. It is similar in structure to aerated concrete, but there is a difference in composition and, consequently, in properties. It is characterized by good thermal conductivity, high fragility and increased moisture absorption.
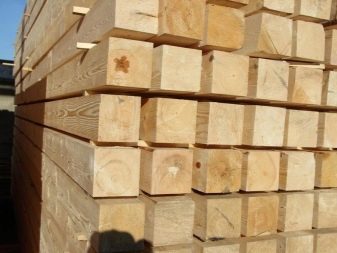
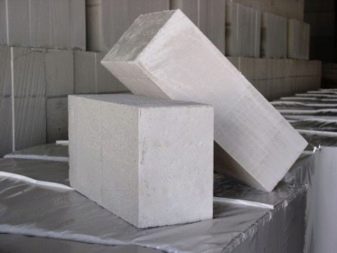
- Fibrolite... This is an analogue of wood concrete with a very similar composition. In both cases, wood waste acts as components. But if in the first version there are shavings, then wood fiber is used in the fiberboard, made in the form of thin and narrow strips. Just like wood concrete, it has good thermal conductivity (0.08 - 0.1 W / m · K) and needs additional protection from moisture.
- Sibit... Consists of concrete, gypsum, aluminum powder with the addition of surfactants and water. It is considered environmentally friendly materials, as an artificial stone is formed as a result of reactions. Possesses extremely high frost resistance (up to 250 freeze and thaw cycles), but low fracture strength. Usually not used for a low-rise building.
- Adobe... It is the oldest building material, consisting of environmentally friendly raw materials - clay soil and straw. Saman has an excellent thermal conductivity coefficient (0.1 - 0.4). However, it has an important disadvantage - increased moisture permeability.
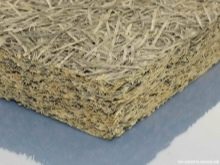
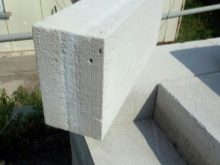
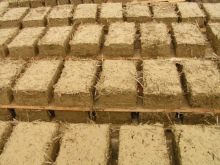
About the pros and cons of wood concrete, in the video below.
The comment was sent successfully.