Features of the production of wood concrete blocks with your own hands
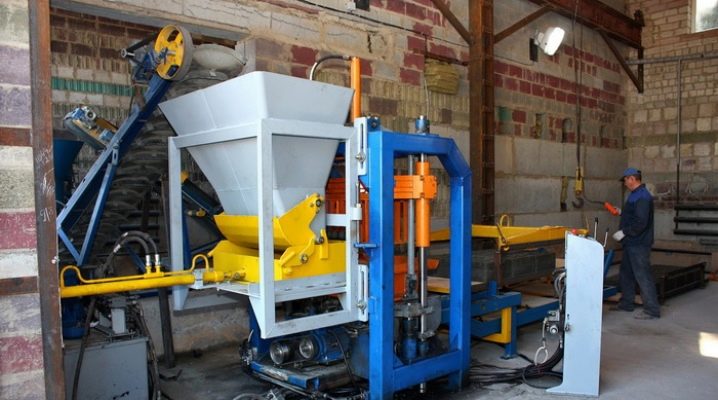
Arbolit is described enthusiastically in many publications; advertisers do not tire of attributing various advantages to it. But even with the marketing gimmicks aside, it's clear that this material deserves close scrutiny. It's good to know how to do it yourself.
Types and sizes of blocks
Arbolite panels are divided into several types:
- large-format blocks (intended for wall capital masonry);
- hollow products of various sizes;
- plates for strengthening thermal insulation.
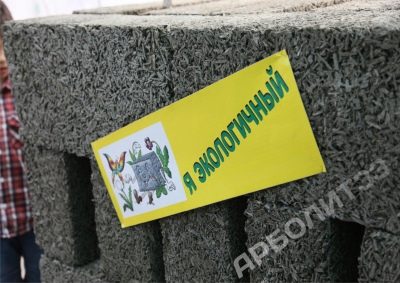
Also wood concrete is used to make liquid mixtures, with which the enclosing structures are poured. But most often, in practice, the word "arbolit" is understood as masonry elements with or without cladding. Most often, blocks with a size of 50x30x20 cm are made. However, more and more the nomenclature is expanding, and manufacturers are mastering new positions. The technical characteristics of the produced blocks are provided only in the complete absence of impurities.
Elements with a density of 500 kg per 1 cu. m. and more are traditionally considered structural, less dense - intended for thermal insulation. They can be used where the load from above is taken up by other parts of the structure. Usually, the density is measured only after the block has lost all excess moisture.
From cast wood concrete with a specific gravity of 300 kg per 1 cu. m. walls can also be erected, while in terms of strength they are not inferior to structures made of heavier material.
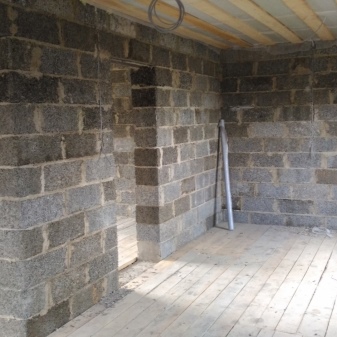
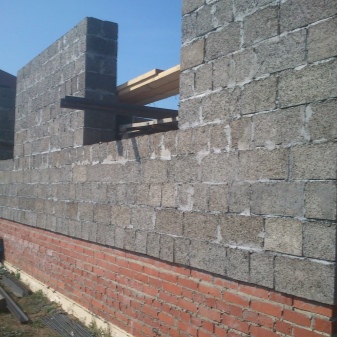
To build carriers walls of one-story houses, the height of which does not exceed 3 m, it is necessary to use blocks of at least category B 1.0... If the structures are above, Category 1.5 products are required and higher. But two-story and three-story buildings should be built from wood concrete of group B 2.0 or B 2.5, respectively.
According to Russian GOST, wood concrete enclosing structures in a temperate climatic zone should have a thickness of 38 cm.
In fact, usually the walls of residential buildings from blocks of 50x30x20 cm are laid out in one row, strictly flat. If you need to form an auxiliary thermal insulation, a so-called warm plastering system is made of wood concrete... It is prepared by adding perlite and creating a layer of 1.5 to 2 cm.
When the premises are not heated or are heated from time to time, use the method of masonry on the edge. Heat-shielding wood concrete blocks have a water absorption coefficient of no more than 85%. For structural elements, the permissible value is 10% lower.
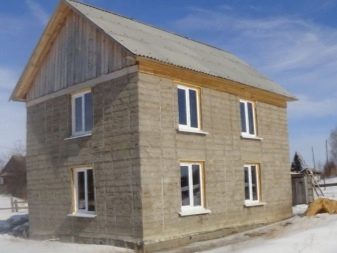
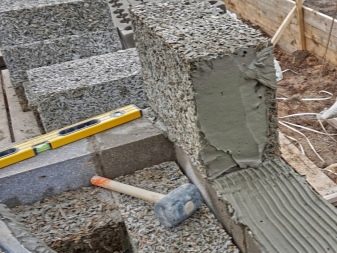
It is customary to divide wood concrete blocks into three categories according to fire protection:
- D1 (difficult to catch fire);
- IN 1 (highly flammable);
- D1 (low-smoke elements).
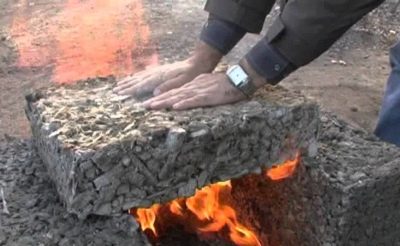
The need to produce wood concrete at home is largely due to the fact that existing manufacturers often produce low-quality goods. Problems can mainly be associated with insufficient strength, weak resistance to heat transfer, or violation of geometric parameters. Blocks of any kind should certainly be covered with plaster.... It reliably protects against wind blowing. Only finishing coatings capable of "breathing" are combined with wood concrete..
There are 6 brands of wood concrete blocks, distinguished by the level of frost resistance (from M5 to M50). The number after the letter M shows how many cycles of transition through zero degrees these blocks can transfer.
Minimum frost resistance means that the products should only be used for internal partitions.
Most often, their size is 40x20x30 cm. Depending on the device of the groove-comb system, the area of the masonry and the thermal conductivity of the walls depend.
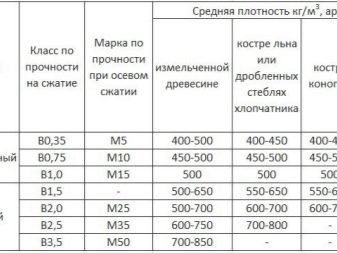
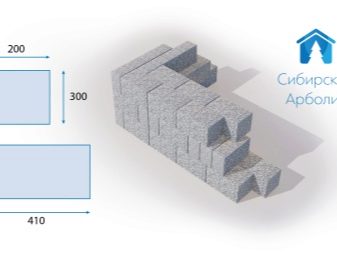
Speaking about the dimensions and characteristics of wood concrete blocks in accordance with GOST, one cannot but say that it strictly regulates the maximum deviations of dimensions. So, the length of all ribs may differ from the declared indicators by no more than 0.5 cm... The largest diagonal difference is 1 cm. A violation of the straightness of the profiles of each surface should be no more than 0.3 cm... The higher the structure, the fewer seams there will be during installation, and the fewer the number of seams will be.
In some cases, blocks with a size of 60x30x20 cm are most convenient. They are needed where the length of the walls is a multiple of 60 cm. This eliminates the need to cut blocks.
Sometimes the so-called "northern arbolite" is found, the length of which does not exceed 41 cm. In some of the rows, when bandaging, the width of the wall coincides with the length of the block, and in the other part it is the sum of the two widths and the seam separating them.
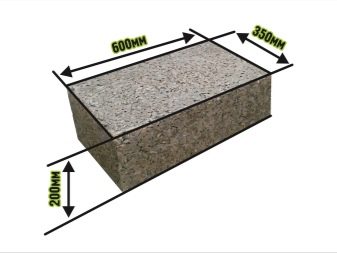
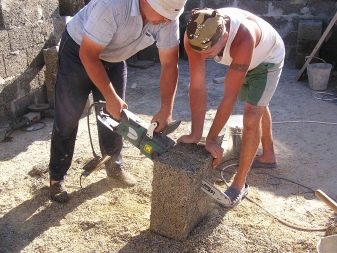
Almost all manufacturers make baffle blocks. In the line of each company, the size of such products is 50% of the standard size. Occasionally, constructions of 50x37x20 cm are found. This allows you to erect walls exactly 37 cm without resorting to bandaging blocks or applying panels.
In some regions, completely different sizes may occur, this should be specified additionally. In case of self-production, they must be selected at your own discretion.
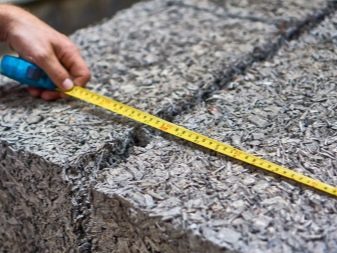
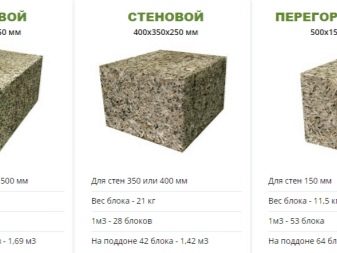
Mixture composition and proportions
When preparing the production of wood concrete panels, it is necessary to carefully select the composition of the mixture and the ratio between its parts. Waste from wood processing invariably acts as a filler. But since wood concrete is a type of concrete, it contains cement.
Thanks to organic components, the material perfectly retains heat and does not allow extraneous sounds to pass through. However, if the basic proportions are violated, these qualities will be violated.
It should be understood that only some types of shavings can be used for the production of wood concrete. This is its essential difference from sawdust concrete. According to the current GOST, the dimensions and geometric characteristics of all fractions of the material are strictly regulated.
Chips are made by crushing non-marketable wood. The length of the chips varies from 1.5 to 4 cm, their maximum width is 1 cm, and the thickness should be no more than 0.2 - 0.3 cm.
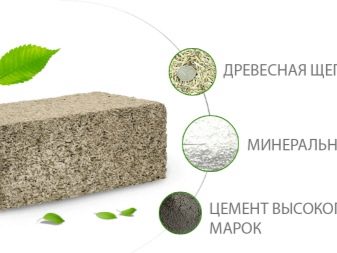
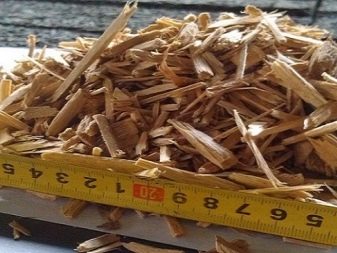
As a result of special scientific and practical research, it was found that the best wood chips:
- resembles a tailor's needle in shape;
- has a length of up to 2.5 cm;
- has a width of 0.5 to 1 and a thickness of 0.3 to 0.5 cm.
The reason is simple: wood with different proportions absorbs moisture differently. Compliance with the dimensions recommended by the researchers makes it possible to compensate for the difference.
In addition to size, wood species must be carefully selected. Spruce and beech will work, but larch will not work. You can use birch and aspen wood.
Regardless of the breed chosen, it is imperative to use antiseptic mixtures.
They allow you to avoid the occurrence of mold nests or damage to raw materials by other pathological fungi.
In the production of wood concrete, bark and needles are sometimes used, but their maximum share is 10 and 5%, respectively.
Sometimes they also take:
- flax and hemp fire;
- rice straw;
- cotton stalks.
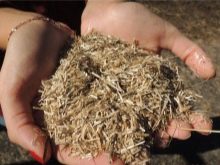
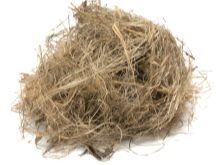
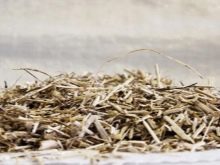
The greatest the length of such components is a maximum of 4 cm, and the width should not be more than 0.2 - 0.5 cm.It is forbidden to use tow and tow more than 5% of the mass used filler. If flax is used, it will have to be soaked in lime milk for 24-48 hours. This is much more practical than 3 or 4 months outdoor exposure. If you do not resort to such processing, the sugar contained in flax will destroy the cement.
As for the cement itself, Portland cement is most often used for the production of wood concrete... It was he who began to be used for this purpose several decades ago. Sometimes auxiliary substances are added to Portland cement, which increase the frost resistance of structures and improve their other characteristics. Also, in some cases, sulfate-resistant cement can be used. It effectively resists the effects of a number of aggressive substances.
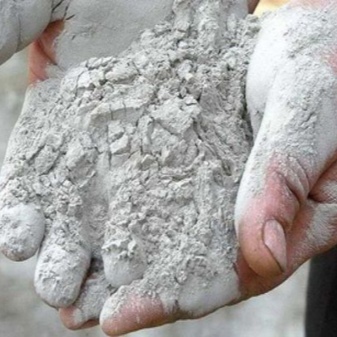
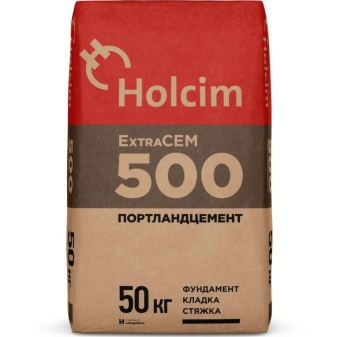
GOST requires that only cement grade M-300 and higher be added to heat-insulating wood concrete. For structural blocks, only cement of a category not lower than M-400 is used. As for the auxiliary additives, their weight can be from 2 to 4% of the total weight of the cement. The number of components introduced is determined by the brand of wood concrete blocks. Calcium chloride and aluminum sulfate are consumed in a volume of no more than 4%.
The same is the limiting amount of a mixture of calcium chloride with sodium sulfate. There are also a couple of combinations in which aluminum chloride is combined with aluminum sulfate and calcium chloride. These two compositions are used in an amount of up to 2% of the total mass of the laid cement. In any case, the ratio between auxiliary additives is 1: 1... But for the astringent components to work effectively, you need to use water.
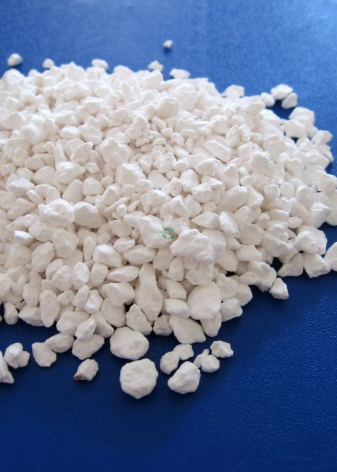
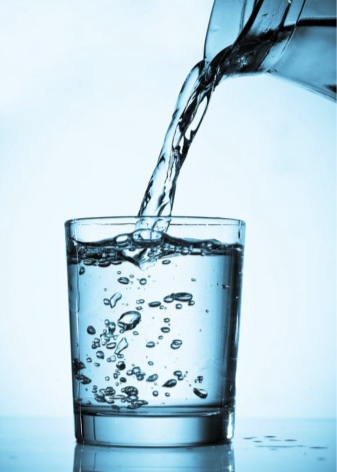
The GOST prescribes strict requirements for the purity of the liquid used. However, in the actual production of wood concrete, they often take any water that is suitable for technical needs. Normal setting of cement requires heating up to +15 degrees... If the water temperature drops to 7-8 degrees Celsius, chemical reactions are much slower. The ratio of the components is selected so as to provide the necessary strength and density of wood concrete.
Arbolite products can be reinforced with steel meshes and rods. The main thing is that they comply with the industry standards.
The standard requires manufacturers to test the prepared mixture twice per shift or more often for compliance with the following indicators:
- density;
- ease of styling;
- tendency to delamination;
- the number and size of the voids separating the grains.
Testing is carried out in a special laboratory. It is carried out for each batch of the mixture at 7 and 28 days after hardening. Frost resistance must be determined for both decorative and bearing layers.
To find out the thermal conductivity, they measure it on samples selected according to a special algorithm. Determination of moisture content is carried out on samples taken from finished stone blocks.
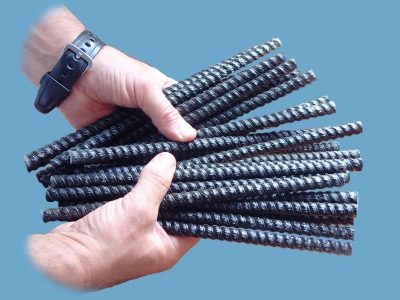
Necessary equipment
Only in the case when all the requirements of GOST are met, it is possible to launch a certain brand of wood concrete into production. But to ensure strict compliance with the standards and release the required amount of the mixture, and then blocks from it, only special equipment helps. Chips are divided into parts using industrial grinders. Further, it, together with other components, enters the device that agitates the solution.
You will also need:
- apparatus for dosing and forming wood concrete blocks;
- vibration table, which will give them the necessary qualities;
- devices drying chips and cooked blocks;
- bunkers where sand and cement are laid;
- lines supplying raw materials.
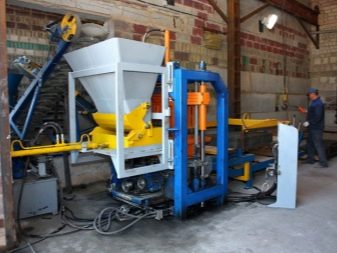
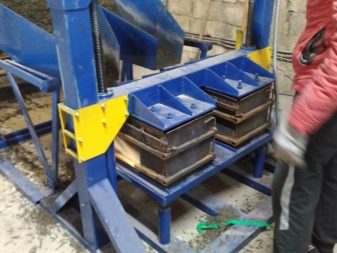
You should not use home-made devices if you plan to produce large batches of wood concrete. They are not productive enough, because the profitability of the enterprise falls.
It is useful to consider the features of each type of equipment. Chip cutting devices have a special drum with "knives" formed from high quality tool steel. Additionally, the drum is equipped with hammers, which allow automating the supply of raw materials for subsequent crushing.
In order for the raw material to pass inside, the drum is made perforated, it is surrounded by several. A larger (outer) drum of the same shape, which prevents the scattering of debris.Usually the device is mounted on frames with three-phase electric motors. After splitting, the chips are transferred to the dryer. It is the quality of this device that most of all affects the perfection of the finished product..
The dryer is also made in the form of a double drum, its diameter is approximately 2 m. The outer drum is perforated, which allows for the supply of warm air. It is fed using an asbestos pipe or a flexible fireproof hose. The twisting of the inner drum allows the chips to stir and prevent the raw material from igniting. High-quality drying will be able to bring 90 or 100 blocks to the desired condition in 8 hours... The exact value depends not only on its power, but also on the dimensions of the processed structures.
The stirrer is a large cylindrical vat. All the raw materials needed are loaded from the side, and the mixed composition comes out from the bottom. Typically, electric motors and their gearboxes are located on top of the mortar mixer. These motors are fitted with blade assemblies. The capacity of the tank is determined by the daily capacity of the line. Miniature production produces no more than 1000 designs per day shift, while vats with a capacity of 5 cubic meters are used. m.
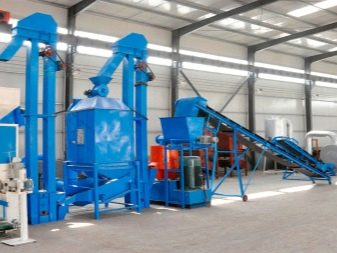
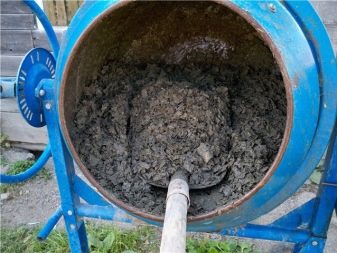
Production technology
To prepare wood concrete blocks for a private house with your own hands, you need to use 1 part of shavings and 2 parts of sawdust (although in some cases a 1: 1 ratio is preferred). Periodically, all this is properly dried. They are kept outdoors for 3 or 4 months. Periodically chopped wood is treated with lime, turned over. Usually 1 cubic meter. m. chips consume about 200 liters of lime in a concentration of 15%.
The next stage of making wood concrete blocks at home involves mixing wood chips with:
- Portland cement;
- slaked lime;
- potassium chloride;
- liquid glass.
It is best to make blocks of 25x25x50 cm at home.... It is these dimensions that are optimal for both residential and industrial construction.
Compaction of mortar requires the use of vibratory presses or hand rammers. If a large number of parts are not required, a miniature machine can be used. Special shapes help to set the exact size of the finished product.
Forming slabs
You can make a monolithic wood concrete by pouring the prepared mixture into this form manually. If liquid glass is added, the finished product will become harder, but at the same time its fragility will increase. It is advisable to knead the components sequentially, and not all together. Then there is less danger of lumps. Obtaining a lightweight construction is very simple - you just need to put a wooden block in the mold.
It is necessary to keep the workpiece in shape for at least 24 hours... Then air drying begins under a canopy. Drying time is determined by the air temperature, and if it is very low, sometimes it takes 14 days. And the subsequent hydration at 15 degrees lasts 10 days. At this stage, the block is kept under the film.
In order for the wood concrete plate to last longer, it should not be cooled to a negative temperature. Wood concrete almost inevitably dries up on a hot summer day. However, this can be avoided by resorting to periodic spraying with water. The safest method is to process it under fully controlled conditions in a drying chamber. Desired parameters - heating up to 40 degrees with air humidity from 50 to 60%.
For information on how to make wood concrete blocks with your own hands, see the next video.
The comment was sent successfully.