Equipment for the production of wood concrete blocks
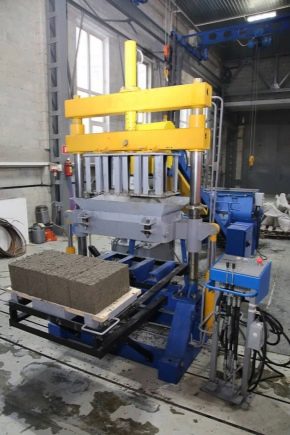
By means of special equipment, the production of arboblocks is realized, which have excellent thermal insulation characteristics and sufficient strength properties. This is ensured by a special manufacturing technology. For the formation of building materials, cement and wood chips are used, which are subjected to specific processing.
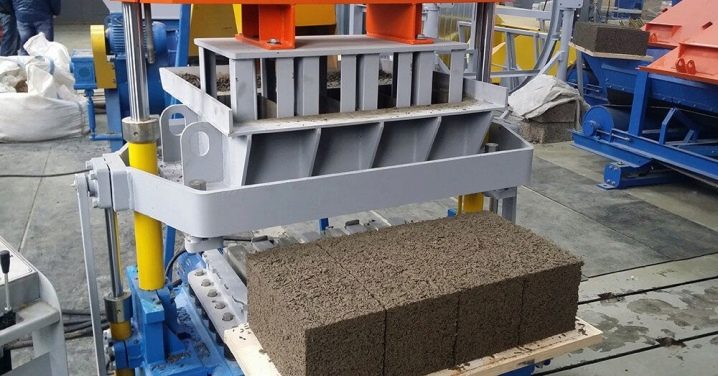
What is wood concrete?
Arbolit (wood block, wood concrete) is a progressive building material obtained by mixing and pressing wood chips (chips) and cement mortar. According to experts, it can easily compete with bricks. But at the same time, wood concrete is much cheaper in terms of cost.
Wood chips are the basis of wood blocks. Strict requirements are imposed on its parameters and volume - these two properties have a great impact on the quality of the final product and its brand. In addition, there are wood-concrete production facilities that use cotton stalks, rice straw or tree bark.
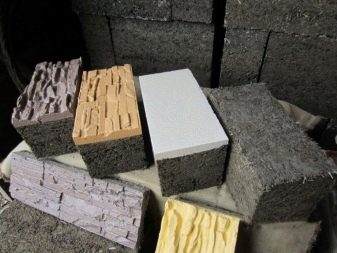
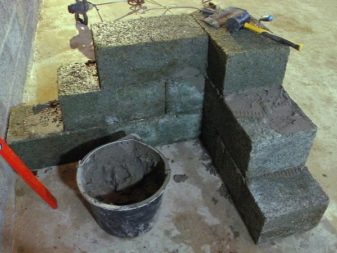
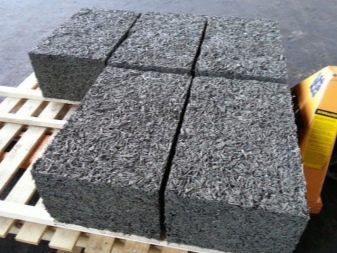
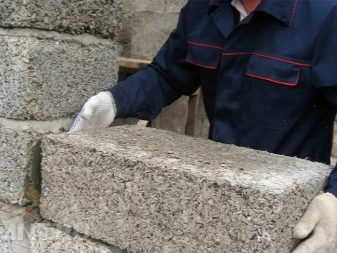
The binding ingredient is Portland cement of grade M300 or higher. Its variety has an impact on the stability of the finished product and therefore on its labeling.
In order to increase the efficiency of synthesizing the ingredients of the solution, specialized additives are mixed into it, which ensure rapid hardening, and so on. Most of them are an aqueous solution of sodium or potassium silicates (water glass), aluminum chloride (aluminum chloride).
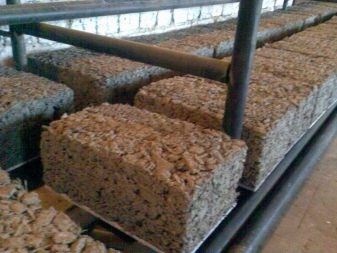
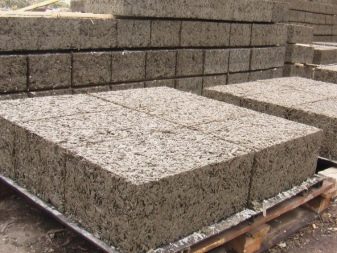
Necessary equipment for production
To make wood concrete blocks at home, you will need three types of equipment: an aggregate for crushing wood chips, a concrete mixer or concrete mixer and a machine for forming wood blocks. However, the primary material - chips, can be purchased from third-party manufacturers, in this case, the technological process will become much simpler.
There is a fairly extensive range of equipment on the market for the production of arboblocks - from small-sized units specifically for small-scale production to full-fledged production lines containing several types of equipment.
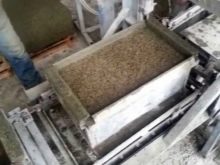
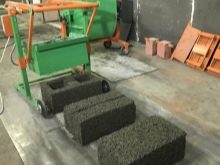
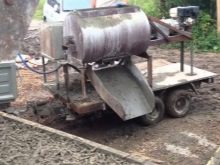
Chip cutters
A device for making wood chips is called a wood chip cutter. It is a drum-type or disc-type chipper that can grind chopped wood and bushes into chips that remain after cutting down a forest.
The completing of almost all units is identical, they consist of a receiving hopper, an electric motor, breaking knives, a rotor and a body part of the machine.
Disk installations are distinguished by their relatively small dimensions and lower cost, while drum chippers have increased productivity, which makes them popular in conditions of production of large series of products.
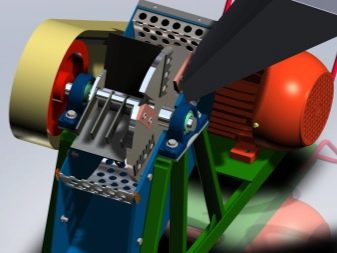
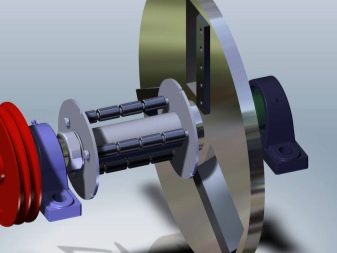
Disc aggregates allow to process trees up to three meters in size. The advantages of this type of aggregates include the smallest number of large components at the output - more than 90% of wood chips have the required configuration and dimensions, large particles are re-processed. It is the ideal equipment choice for small batch production.

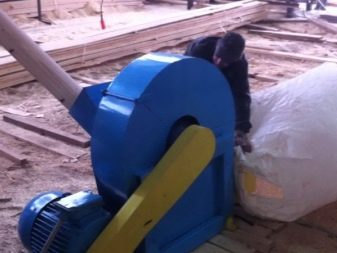
Machine
Such equipment can be confidently called semi-professional. As a rule, it is bought for the purpose of making arboblocks in private construction on order or for sale. It is easy to operate, does not require high professionalism, which is mainly associated with ensuring the safety rules.
Industrial units can be symbolically divided into three key groups:
- manual machines;
- units with a vibrating press and bunker feeding;
- complex combined units that connect the receiver with the initial weight, a vibration press and a static molder that maintains the density of the wood concrete solution until the final hardening of the wood block into the finished product.
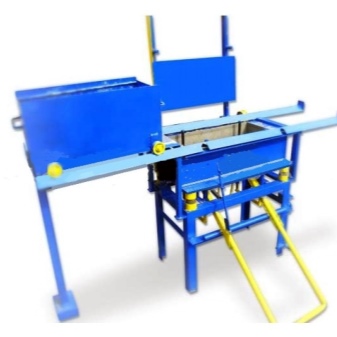
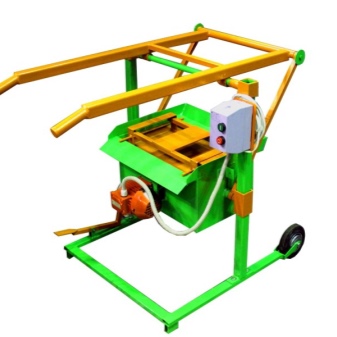
Concrete mixer
An ordinary mixer with flat blades is not suitable for mixing wood concrete mortar. Everything is explained by the fact that the mixture is half dry, it does not creep, but is able to rest in a slide; the blade simply drives it from one corner of the tank to another corner, and not all chips are covered with cement dough.
At the concrete mixer SAB-400 in the structure there are special "plows" - knives that cut the mixture, and effective (and most importantly, fast) mixing is obtained. Speed is critical, since the cement should not have time to set until it has covered all the crushed material.
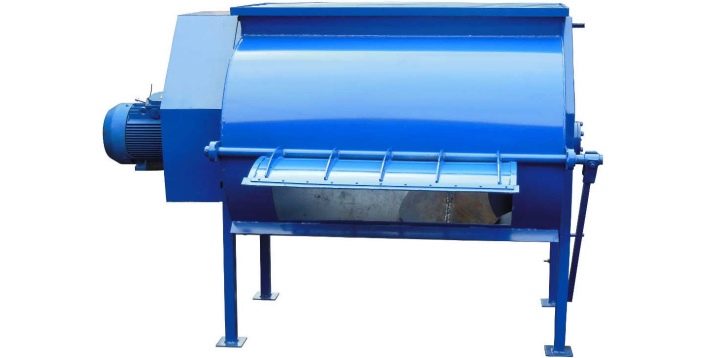
Concrete mixer
In the process of manufacturing arboblocks, as a rule, impulse agitators are used, from time to time - construction mixers. On large lines, where the production of building materials is carried out in large batches, equipment with a continuous nature is installed. In order to meet the needs of not very large industries, in most cases, ordinary concrete mixers are used, which have the following structural characteristics:
- are large containers with side loading of ingredients and bottom unloading of the prepared solution;
- the mixer is equipped with an electric motor with a gearbox with a maximum power of 6 kW;
- specialized blades are used to mix the wood concrete ingredients.
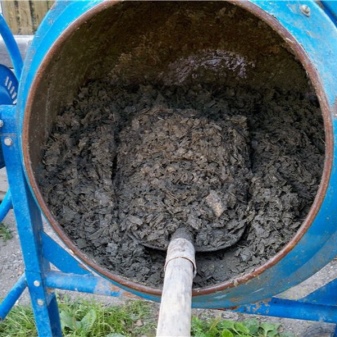
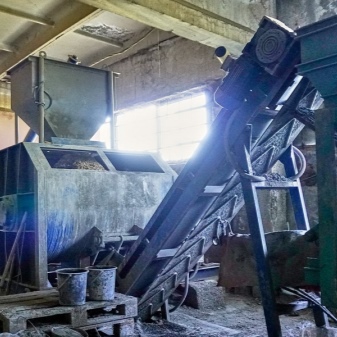
The volume of the mixer is calculated based on the daily need for materials to establish an effective technological process.
Vibropress
The area of the vibrating table (vibropress) also depends on the size of the molding batcher. Vibrocompression machine is a metal table proportional to the size of the dispenser, which is equipped with springs and is connected to the bed (main heavy table). A three-phase electric motor up to 1.5 kW is installed on the bed, on the axis of which there is an eccentric (a load whose center of gravity is shifted). When the latter is connected, regular vibration processes of the upper part of the table take place. These actions are required for optimal shrinkage in the forms of the composition of wood concrete blocks and the elimination of mechanical and external defects of the blocks after removing the mold.
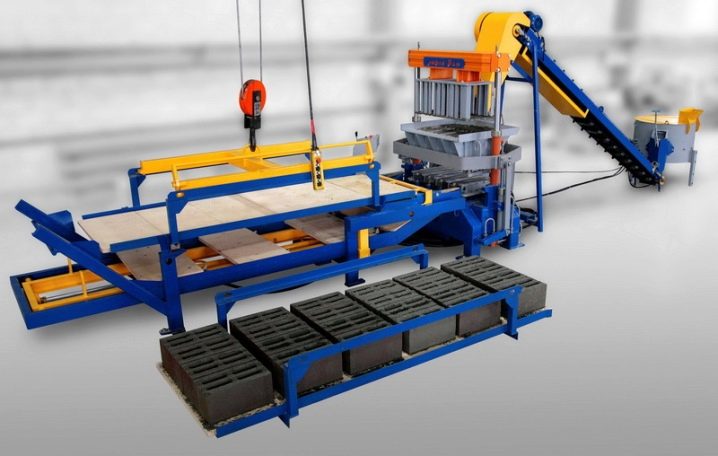
Forms
The matrix (form, press panels) for the manufacture of blocks is intended to give the product specific dimensions and configuration. Specifically, it depends on how accurate the shape of the block will be.
The matrix is a rectangular shape with an empty contour inside, in which the solution is filled. This form provides a removable cover and bottom. The form has specialized handles along the edges. Inside, it is equipped with a specific coating designed to facilitate the removal of the formed block.
Basically, a smooth artificial material is practiced for the inner coating, it can be plastic wrap, linoleum or other similar materials.
Drying chambers
Ready-made arboblocks, which are pressed properly, together with the dies, are sent to a specialized room.In it, the level of air humidity is tightly controlled, which makes it possible to create optimal conditions for the drying of the material.
Blocks are necessarily laid out on pallets and freed from dies. That optimizes the access of air masses to the material, this has a positive effect on its properties.
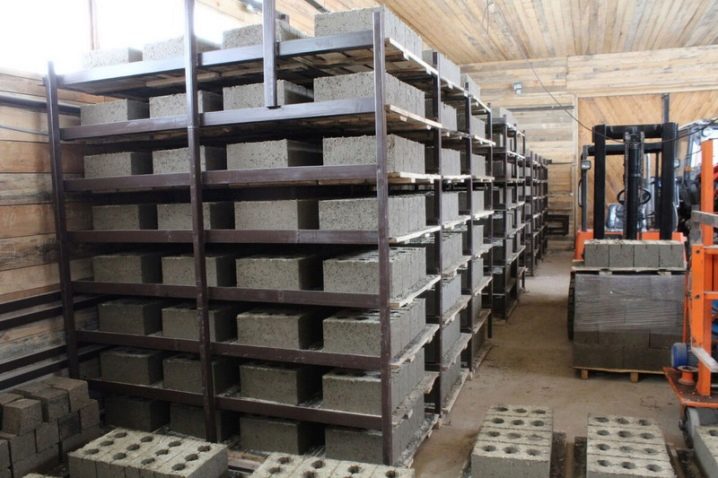
The adhesion of the solution, as a rule, takes place after two days. The design capacity of the building material is obtained only after 18-28 days... All this time, wood concrete must be in an environment of the required humidity and stable temperature.
In home production, as a rule, a pressed batch of arboblocks is laid out in a darkened place, covered with a polyethylene film and a protective fabric awning. After 2-3 days, the blocks are moved into the room and laid out in one layer on the stone floor. After 7 days, the blocks can be placed in packs.
How to choose equipment?
To create wood blocks, you will need 3 types of machines: for the production of wood chips, for making mortar and for pressing. They are both Russian and foreign made. Among other things, individual craftsmen manage to assemble equipment with their own hands (as a rule, they assemble vibropresses on their own).
Crushers
Shredders are mobile and stationary, disc and drum. Disk differ from each other in the principle of operation.
It is great if the installation is equipped with a mechanical feed of raw materials - this will greatly simplify the work.
Concrete mixer
A standard stirrer is ideal for this purpose. For industrial capacities, even within the boundaries of a mini-plant, a tank volume of 150 liters or more is required.
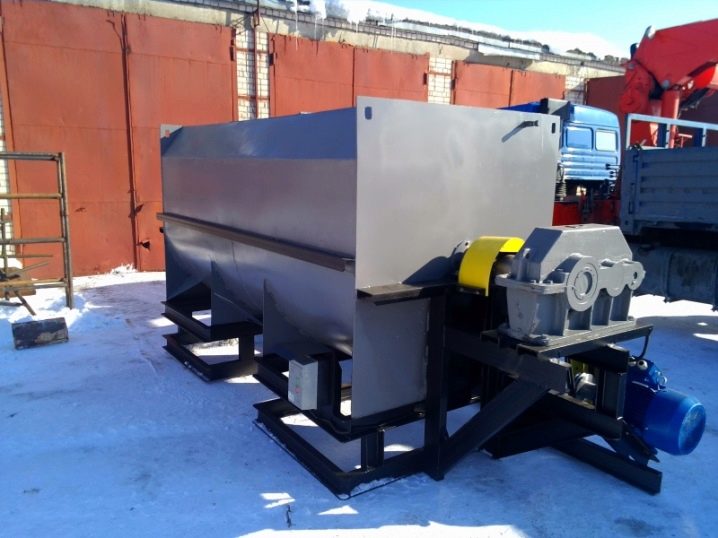
Drying chamber
You can accelerate the drying process by purchasing a specialized drying (mainly infrared) camera. When purchasing such equipment, it is necessary to pay attention to the parameters of power and energy consumption, as well as the ability to adjust the temperature level and drying speed. In the drying chamber, the blocks will dry out and be ready for use within 12 hours - almost 30 times fasterthan without special equipment.
For industrial production, high speed is considered a fairly significant indicator that directly affects income.
How to make a machine with your own hands?
To assemble a homemade vibrating machine, drawings and these materials are required (all dimensions are approximate):
- vibration motor;
- welder;
- springs - 4 pcs.;
- steel sheet 0.3x75x120 cm;
- profile pipe 0.2x2x4 cm - 6 m (for legs), 2.4 m (on the base under the cover);
- iron corner 0.2x4 cm - 4 m;
- bolts (for fastening the motor);
- special paint (to protect the unit from rust);
- steel rings - 4 pcs. (the diameter should correspond to the diameter of the springs or be slightly larger).
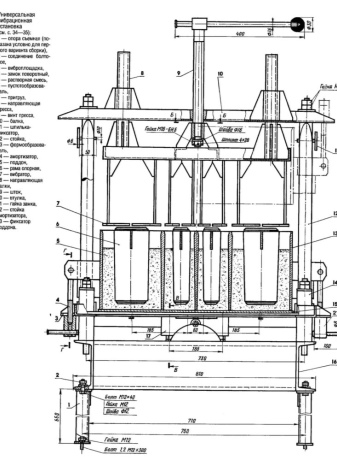
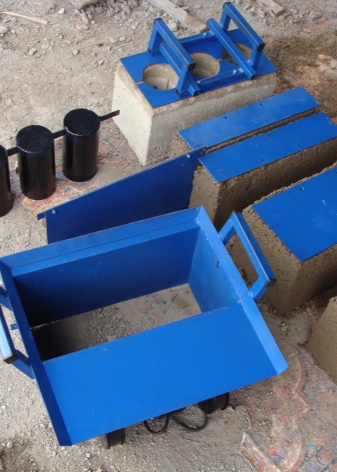
The assembly procedure for the vibrating table is quite simple.
- We cut the material into the required elements.
- We divide the pipe under the legs into 4 identical parts, 75 cm each.
- We divide the pipe for the frame as follows: 2 parts 60 cm each and 4 parts 30 cm each.
- Divide the corner into 4 elements, the length should coincide with the length of the sides of the iron sheet under the countertop.
- Welding work: assembling the skeleton for attaching the motor to the cover. We weld a quadrangle from two 30- and two 60-centimeter pieces. In the middle of it, 2 more short elements will be welded at a certain distance between them. This distance should be equal to the distance between the motor fixing points. Holes for fastening are drilled at certain points in the middle sections.
- At the corners of the iron sheet, we weld rings into which the springs will be threaded.
- Now we weld the support leg with the legs. To do this, we take pieces of a corner and pipes. Place the corners in such a way that their edges are oriented upward and outward from the inside of the structure.
- The welded frame for the motor is fixed by means of self-tapping screws or is cooked to the table top.
- We place the springs on the supporting rack in the corners.We put the table top on the rack so that the springs fit into the cells for them. We fasten the motor to the bottom. There is no need to fasten the springs, since the mass of the cover with the motor holds them securely in the right place.
The finished device can be painted.
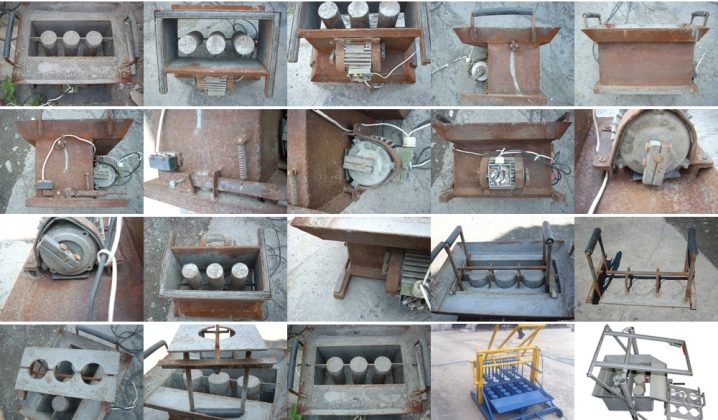
An overview of equipment for the production of wood concrete blocks is in the next video.
The comment was sent successfully.