Monolithic wood concrete: what is it and how to build a house out of it?
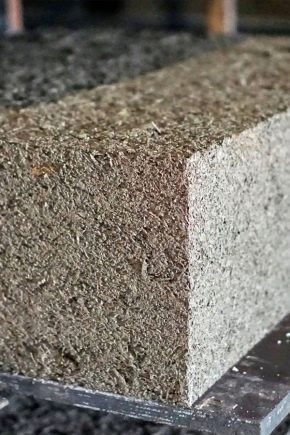
To date, the Russian suburban housing market has gained considerable experience in using all known technologies for the construction of low-rise buildings. Each construction method and material has its own adherents. The main competition for the popular frame-panel houses was made by monolithic concrete structures with removable or sliding formwork made of arbolite (wood concrete). This promising building material, due to the presence of wood chips in its composition in combination with high-grade cement, demonstrates a successful combination of all the valuable properties of both materials. Therefore, wood concrete houses are warm, environmentally friendly, strong and durable. Let's find out in detail what wood concrete is, what are its pros and cons, get acquainted with the installation technology and the features of using this material.
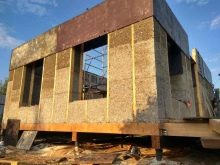
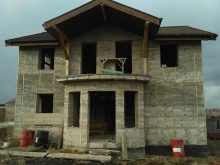
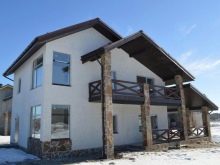
Main characteristics
Monolithic wood concrete is included in the group of concretes with porous aggregates. Its composition includes a hydraulic binder Portland cement with / without mineral components, various types of wood fillers and modifiers that increase the strength of the cement mass. There are three types of wood concrete mixture:
- thermal insulation with a density of 450 kg / m3;
- structural and thermal insulation - from 450 to 600 kg / m3;
- structural - from 600 to 850 kg / m3.
The table shows the main operational properties of a structural building material.
Options | Meaning |
Thermal conductivity, W / m * K | 0,08-0,17 |
Water vapor permeability, mg / (m * h * Pa) | 0,11 |
Compressive strength, MPa | 0,5-5,0 |
Flexural strength, MPa | 0,7-1,0 |
Elasticity in compression and tension, MPa | 300-2250 |
Noise absorption in the range of 125-2000 Hz | 0,17-0,60 |
Amount of water absorption (%) | 45-85 |
Shrinkage (%) | 0,4-0,5 |
Frost resistance (cycle) | 25-50, class F50 |
Fire resistance limit (in hours) | 1,5 |
Biological resistance (class) | V |
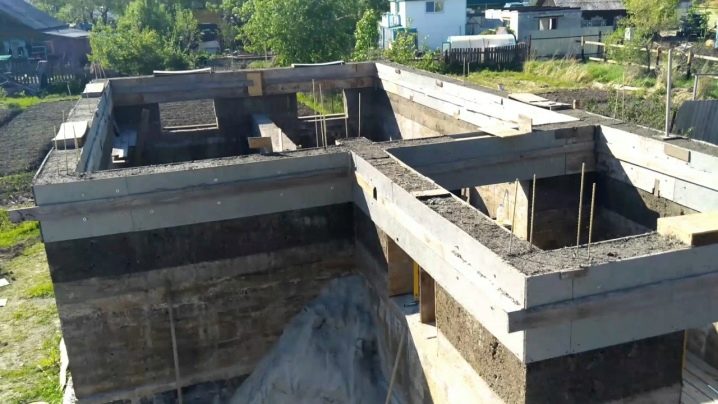
Advantages
Interest in the technology of housing construction by means of pouring monolithic arbolite walls is primarily due to the absence of temperature bridges and the possibility of constructing structural elements of non-standard geometry. Among other advantages of the monolith deserve attention:
- environmental friendliness - the material contains no compounds that can harm human health and pollute the environment;
- hygiene - wood concrete has resistance to mold fungi and decay processes;
- reliability - high strength characteristics allow the material to withstand operation under conditions of increased dynamic and static loads;
- wear resistance - the ability to restore its original shape when the maximum permissible dynamic load is temporarily exceeded increases the service life of wood concrete;
- high thermal insulation capacity combined with excellent sound insulation;
- safety, due to the ability of wood concrete to withstand high temperatures for a long time and not to support the spread of fire.
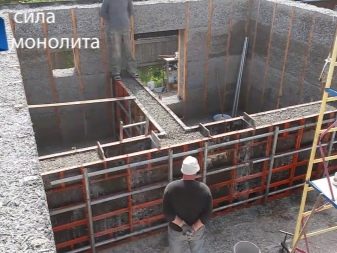
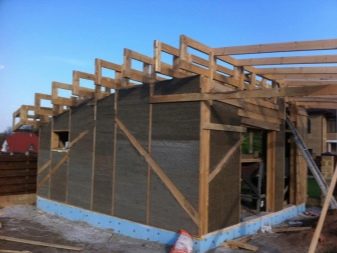
disadvantages
All building materials have strengths and weaknesses. Arbolit is no exception.Its main disadvantages are increased moisture permeability and reduced moisture resistance, which is due to the hygroscopicity of wood in the composition of the material.
In order to neutralize these shortcomings in monolithic construction from this material, a number of points must be foreseen.
- Arrangement of a decorative and protective layer on the facade of the house to protect it from capillary moisture.
- Organization of high-quality waterproofing of the foundation.
- Creation of large overhangs, which allows to protect the walls from the bay during moderate rainfall.
Eaves and / or gable overhangs of the roof must have a minimum size of 500-600 mm.
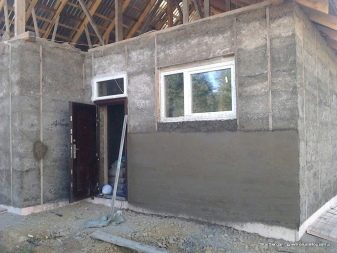
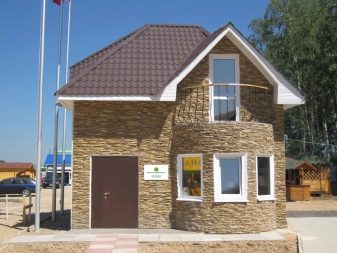
Frame options
It is permissible to erect compact structures from wood concrete blocks without installing a frame. In monolithic housing construction, structural elements are erected along the frame.
For these purposes, two types of supporting structures are used.
- Wooden. Plank frames are used in the case of the construction of one-story buildings. They are mounted in a vertical plane with a step of 1.2-1.5 m and the mandatory installation of supporting elements in place of door / window openings.
- Metallic. For the construction of a frame base of this type, steel and fiberglass reinforcement is used. Window openings are formed using metal beams. The metal frame has greater strength, which makes it possible to erect two- or three-story monoliths.
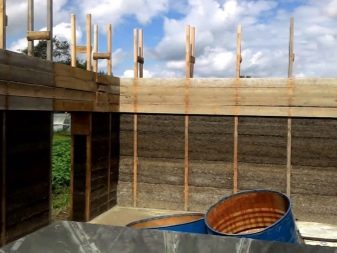
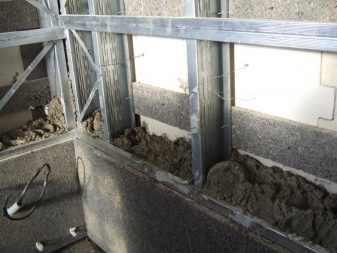
Construction methods and technology
Consider in stages the technology of monolithic housing construction from wood concrete.
Foundation and plinth
The choice of the type of foundation and the calculation of its size depends on the composition and properties of the soil, local climatic conditions, the depth of soil freezing, and the level of groundwater. One of the advantages of wood concrete is its low weight, which allows you to arrange a pile-grillage base or a strip base with shallow depth under the foundation. The minimum permissible values for the height of the basement part for arbolite monoliths vary within the range of 500-800 mm. When pouring a strip base, it is recommended to make it monolithic, as a continuation of the foundation structure.


Formwork installation
The use of a non-removable formwork system leads to an increase in the cost of construction. Therefore, most often, removable disposable panel or inventory formwork is used in the form of reusable blanks from boards, plywood, plastic, metal. The shaping elements are mounted on the supporting structure of the house in such a way that their lower edges overlap it. The boards are connected to each other by means of wooden jumpers with a pitch of 0.5-0.8 m and are additionally fastened with metal studs.
The gaps are closed with flat bars or narrow, thin edged boards.
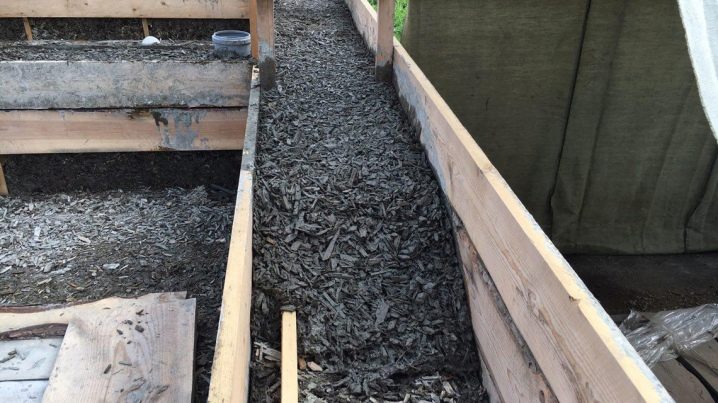
Preparation of working solution
The ratio of the components in the solution for the construction of external wall structures of a one-story house made of wood concrete of class B1 looks like this:
- organic component - 200 kg;
- cement mixture of the M500 / M400 brand - 300-330 kg;
- active fillers - 8 kg;
- water - 350-390 liters.
In the manufacture of homemade wood concrete, instead of expensive ingredients such as aluminum sulfate, the use of more readily available components - lime or water glass, mixed in equal proportions - is practiced as active additives.
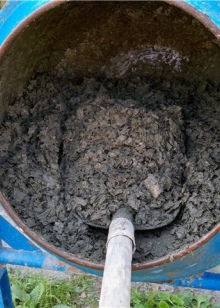

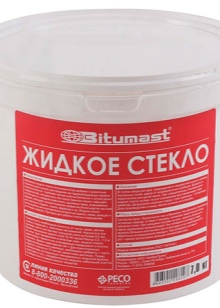
Walling
Today it is known three ways of pouring monolithic arbolite wall structures.
- By floors. The monolith is erected with a non-removable formwork of the floor or foundation by the method of continuous casting. The cement mass is supplied by a local concrete-mortar plant or an automatic mixer.
- By the belts. The entire contour of the building is equipped with formwork up to a meter high with sequential movement of molds for pouring the cement mass from bottom to top.
- By segment. In one pouring, a part of the wall structure with a fixed length, height and having lateral limiters is formed.
If you plan to build a house with your own hands without involving a pro, then it is better to abandon the first two methods of filling in view of their laboriousness in favor of the latter option. It is quite possible to implement it on your own, and without using a concrete mixer.
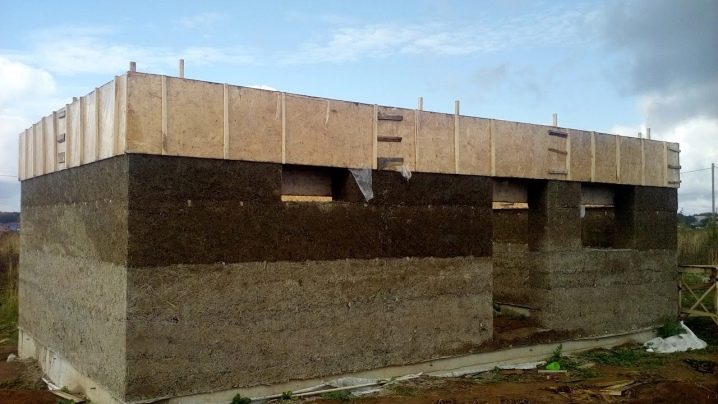
Work order:
- The prepared segment is filled with wood concrete mixture. When filling the form with mortar, it is not topped up by 4-5 cm to the upper border of the formwork panels.
- The poured mixture is compacted by hand using a pin, with which the formed mass of wood concrete is sequentially bayonetted in order to get rid of air bubbles inside the material.
- When the poured segment of the wall structure hardens, the formwork is dismantled and installed in the next section, repeating the same steps as in the previous pouring.
- The rearrangement of the shields and the pouring are first performed in one plane, forming a closed contour of the building, and then the entire system is raised to the higher tiers.
Upon completion of the construction of the walls on the ground floor, proceed to the implementation of the floor screed made of wood concrete.
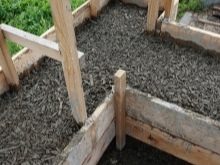
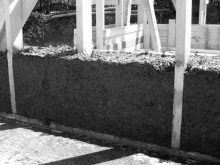
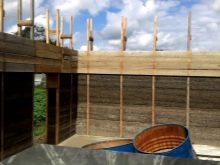
Floor arrangement
This can be done in several ways:
- install the formwork and fill it with wood concrete mortar in two layers;
- make an armored belt around the perimeter of the walls under the reinforced concrete slabs, and pour the leveling screed on top;
- to mount a precast-monolithic floor (SMP) for pouring a concrete mixture.
SMP is a frame system formed by reinforced concrete beams in combination with blocks installed between reinforced concrete elements. When the cement mass, poured into the lower part of the structure, solidifies, the NSR becomes a sealed monolith.
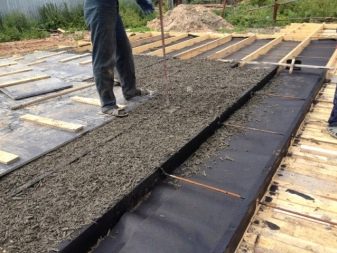
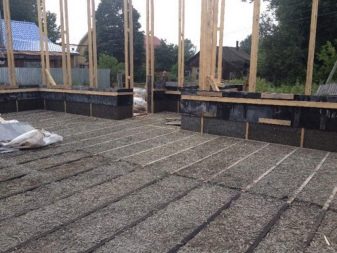
Installation of internal walls and ceilings
The construction of interfloor spaces is carried out using the same methods that were used for the floor. Partitions can be erected in a monolithic way or used to create internal walls arbolite tongue-and-groove blocks. At the end, the rafter system and the roof are installed, the facade is clad and the blind area is laid.
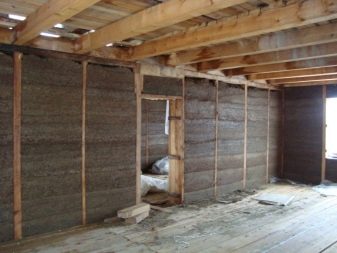
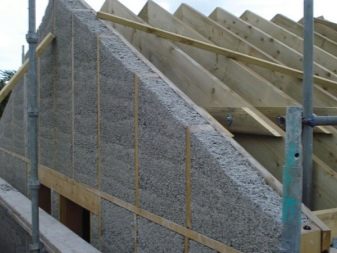
Features of the use of wood concrete
When casting monolithic arbolite walls in winter a number of points must be taken into account in order to avoid losses in the quality of construction.
- Using modifiers. To increase the plasticity and, accordingly, the workability of wood concrete, the wood concrete mixture is combined with plasticizers (lime, polymer gels, dispersions). The strength of the mortar can be increased by using texturing or reinforcing additives. It is advisable not to neglect the addition of antifreeze additives (calcium chloride) to the mixture, which slow down the rate of water crystallization.
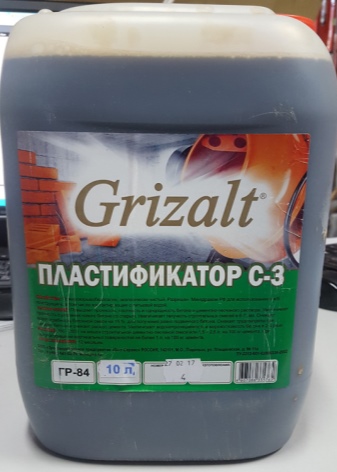
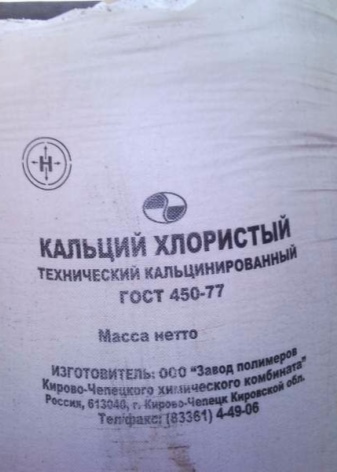
- Creation and maintenance of thermal conditions at the construction site. For this purpose, they arrange heating structures, called hothouses. In fact, they are a kind of greenhouse pavilion erected around a construction site. Outside, it is covered with nylon, tarpaulin, film, and inside a heat gun, fan heater, convector or infrared heater is installed.
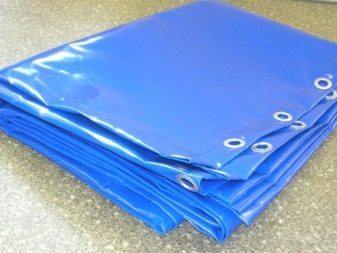
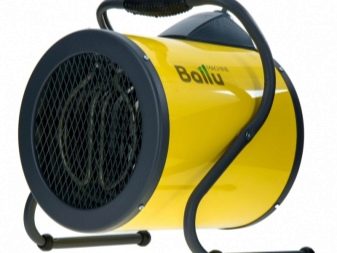
- Electric wave heating of concrete mass. For these purposes, electrodes of various shapes are used. Plate electrodes are placed on the inner side of the formwork panels, both sides of the formwork can be equipped with strip electrodes, and the cement can be heated with rod electrodes, placing them between the reinforcing bars of the supporting base. Heating the mortar in winter ensures its full setting and a set of design strength.
Due to the cooled water, which passes from a liquid to a solid state and crystallizes, the strength characteristics of the cement are greatly reduced.
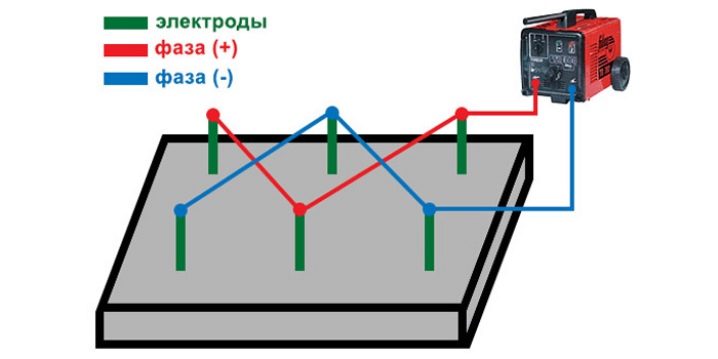
Reviews
Most of the reviews about monolithic arbolite were left by those who had a chance to personally work with this building material. Among them there are many self-taught craftsmen and part-time owners of various structures made of wood concrete.Many craftsmen note that they decided to deal with a monolithic arbolite precisely after they learned about the undemandingness of this building material to the level of professionalism of the performer. This makes it affordable to build an arbolite house with your own hands. Difficulties in the construction process mainly arise due to the installation of the formwork system, which takes a lot of time and effort.
There are also reviews of experienced builders, who mainly focus on the convenience of working with wood concrete., since it can be processed without any problems by any means. It can be sawed, cut, drilled. Any types of finishes are available with a wood concrete monolith: plaster, pasting, painting, which automatically simplifies the selection of the optimal facing option, taking into account the budgetary possibilities. As for the material itself, one of its advantages most often mentions excellent heat-insulating parameters, environmental friendliness and high strength properties.
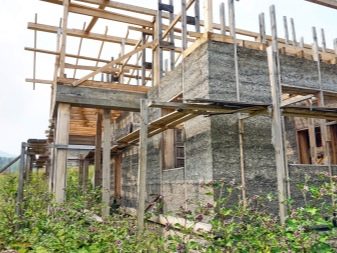
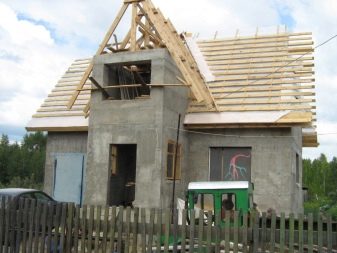
For information on what mistakes can be made when building from monolithic wood concrete, see the next video.
The comment was sent successfully.