All about brick anchors
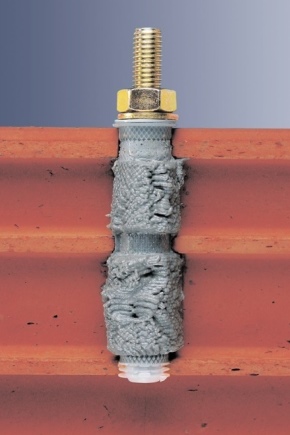
Conducting construction work is an integral part of the life of all inhabitants of the planet. This type of activity makes it possible to create the most comfortable living conditions and improve everyday life. For the construction of residential and industrial buildings, specialists use a large number of building materials, but brick continues to occupy a leading position for many years. Despite the ease of use of this building material, during the construction of structures, experts recommend using special fasteners - anchors. Manufacturers have developed several options for products that differ in size and design.
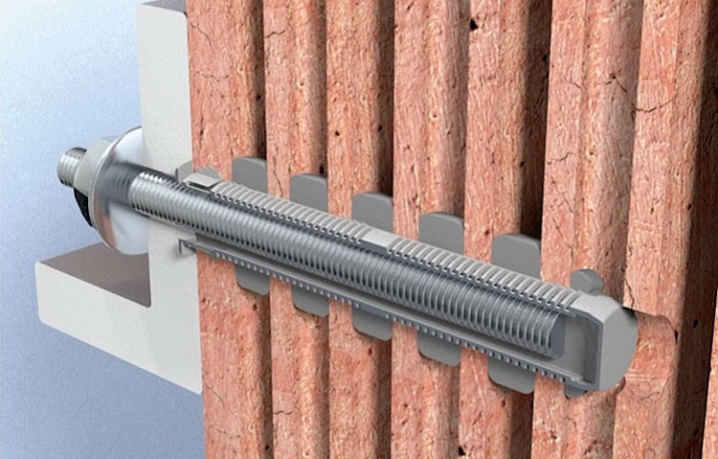
What it is?
The brick anchor is a popular type of fixing element that can be used both during construction and in the process of carrying out repair and restoration work. This product outwardly resembles an ordinary building bolt, but has design features that allow you to reliably connect all brick elements, as well as fix parts of different weights on their surface.
The fixing element must be placed in a pre-prepared hole, while in the process of deepening, the special sleeve begins to increase, which creates the maximum level of adhesion between the object and the wall.
Manufacturers artificially increase the level of adhesion on anchors by applying special notches to them.
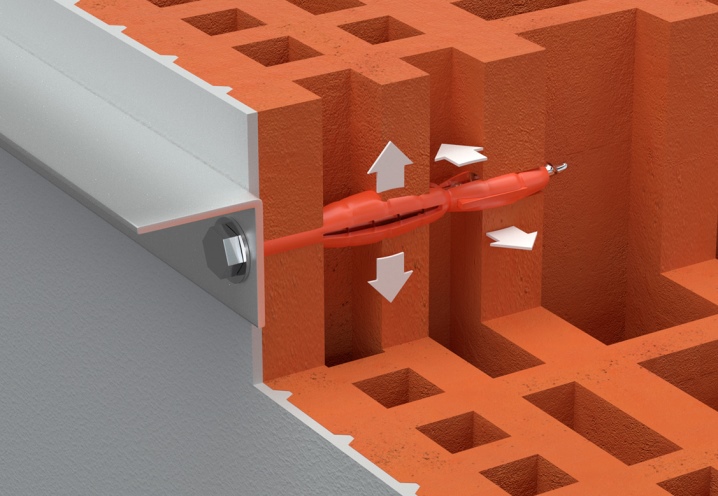
Species overview
The high level of demand for fixing elements and their wide range of applications have forced manufacturers to develop a wide range of parts that differ in size, design and technical characteristics. These features have a direct impact on the specifics of the operation of elements, and some details are designed to solve a narrow range of problems of increased complexity. Expansion anchors for brick wall and masonry can be used for solid, hollow and hollow building materialas well as for sand-lime and facing bricks. In order to study all types more thoroughly, it is better to consider each separately.
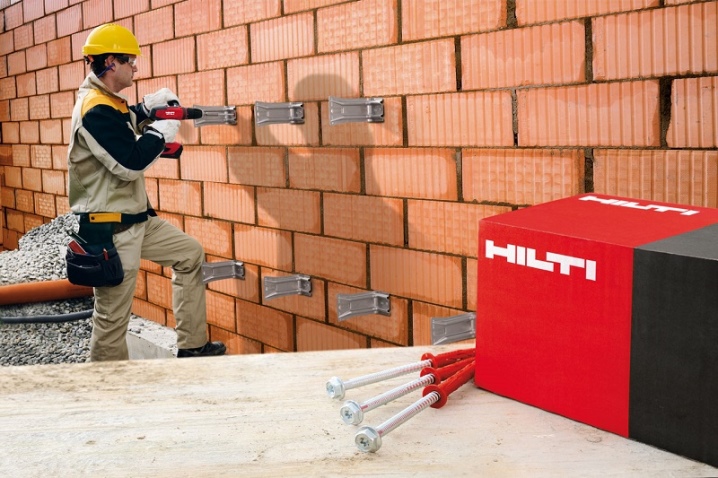
Double-spacer
A new version of the fixing devices - anchor double-expansion elements, which have a spacer sleeve that opens in two directions.
This feature allows you to enhance the fixing effect not only in ordinary masonry, but also in products made of hollow material.
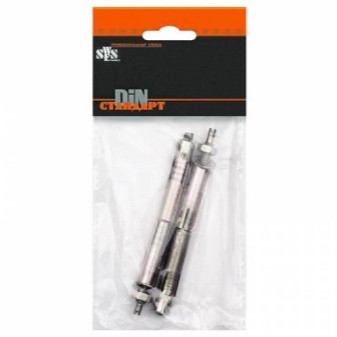
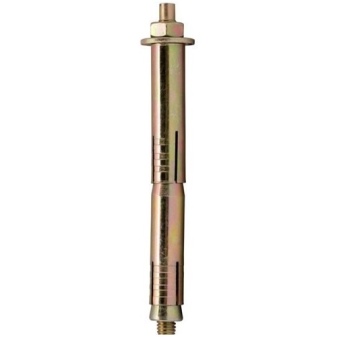
Hammered
The most common fastener used to work with solid bricks. The principle of operation of the driven anchor is the opening of the spacer in a previously prepared hole, followed by screwing the threaded part into the driven part.
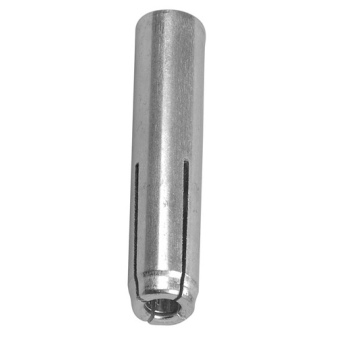
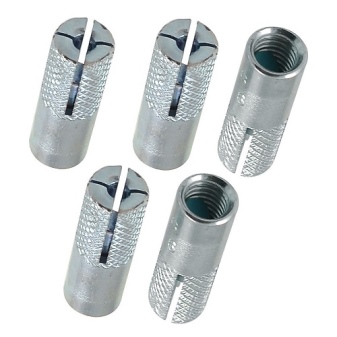
Wedge
Wedge fasteners are special fixing elements that are equipped with a special riving piece.
A distinctive feature is reliable fixation after full expansion in the prepared hole, the presence of screws and a recessed head.
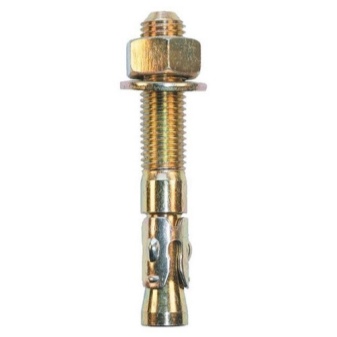
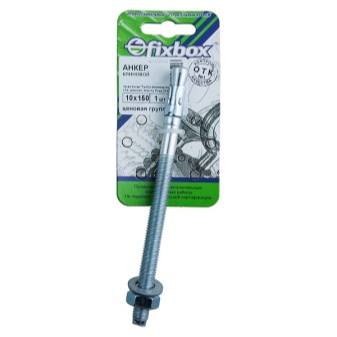
MSA
Type MSA products are improved locking devices that are equipped with special brass sleeves. The design feature is the presence of longitudinal cuts that divide the surface of the product into separate expanding elements.
The inner part is cylindrical in order to maximize expansion of the expansion sleeve.
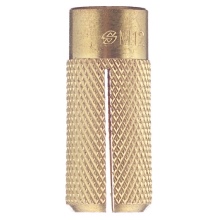
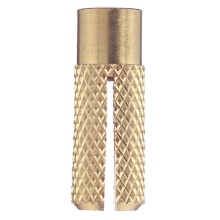
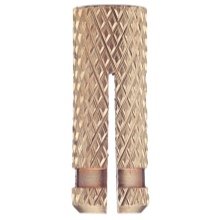
Hex head bolts
Anchor bolts with a hex head are a fixing element in which a classic bolt is used instead of a rod and a nut. A distinctive feature is the fastening of the element in the brick cavity at the moment of tightening the nut, which leads to deformation of the sleeve.
Manufacturers also produce models that can be tightened with a screwdriver.
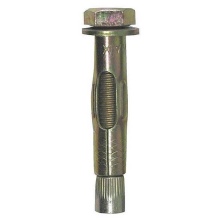
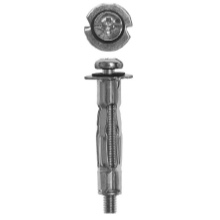
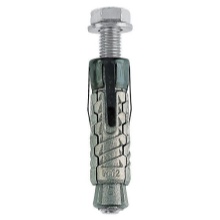
Chemical
Anchoring products, the principle of which is based on a chemical reaction, is a popular and popular device for working with hollow and porous bricks. Differences - filling the drilled hole with adhesive after placing the anchor inside it. Advantages - high fixing level. The disadvantage is the impossibility of using the structure until the glue has completely solidified. This period of time depends on the components and characteristics of the composition, it must be indicated by the manufacturer in the instructions.
The capsule with glue can be placed both inside the product and in a separate bottle.
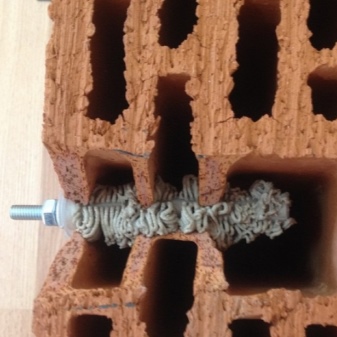
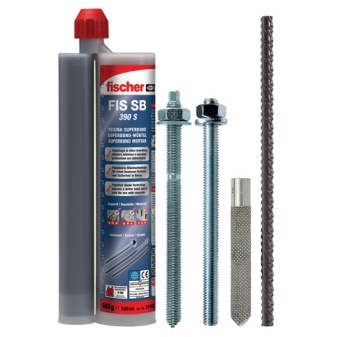
Materials (edit)
Due to the fact that anchor rods on a monolithic cladding are used when it is impossible to perform a strapping with a load-bearing wall, manufacturers use basalt and fiberglass for the manufacture of fixing elements. These materials have not only a high level of strength, but are also able to withstand a wide temperature range, and also have a low coefficient of thermal conductivity, which significantly reduces the likelihood of the formation of cold islands. During operation, fiberglass products behave best of all.
Experts do not recommend purchasing steel anchors, which, during operation, are capable of accumulating condensate, which will inevitably provoke corrosive processes.
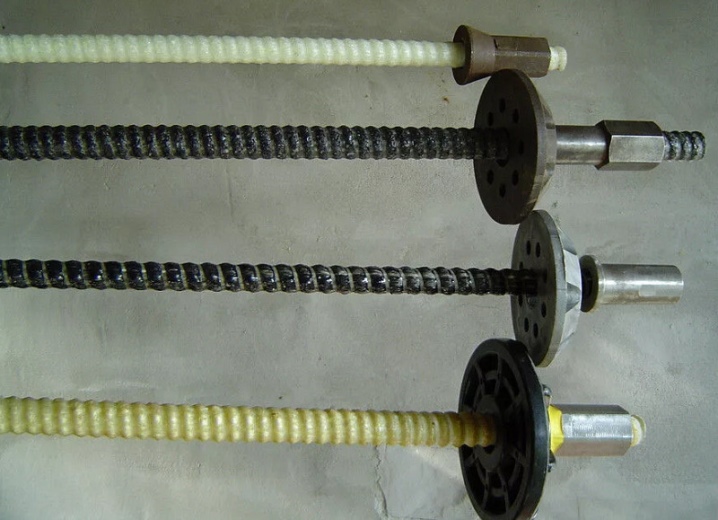
Dimensions (edit)
On the shelves of hardware stores, you can see a wide range of anchor bolts of various diameters and sizes. The choice of a model depends on its purpose and functional load.
Steel products with metric threads with diameters ranging from 6 to 24 mm, and the length varies greatly, are used when performing standard repairs.
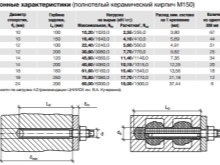
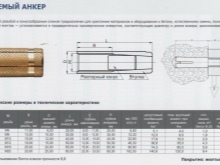
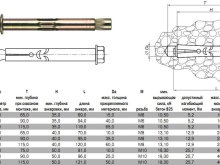
Fastening
To create reliable structures, experts recommend strengthening the structures with special fixing elements - anchors. Anchor fixing parts are simple products, the installation and fastening of which should not cause difficulties even for novice builders. Despite the simplicity of the procedure, before fastening the part, it is necessary to make a calculation for the pull-out and follow all the recommendations of specialists in order to securely fasten it.
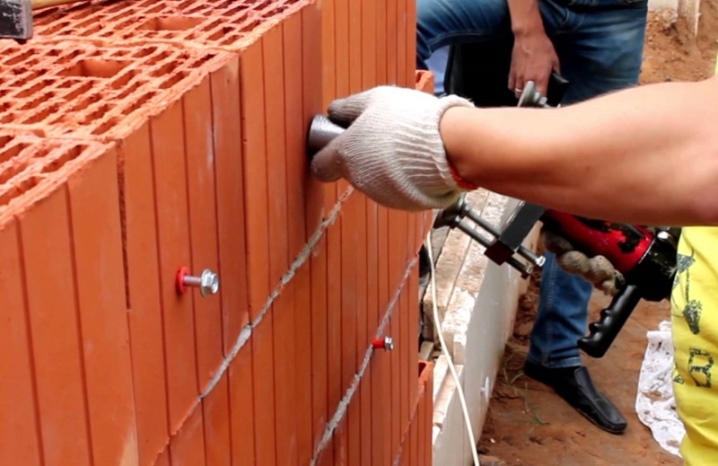
Fundamental rules
To obtain the maximum result, experienced craftsmen recommend taking into account a number of rules and technological features during the installation of anchors. The size of the drilled hole must strictly match the diameter of the fastener. Do not install small anchors in large holes.
It is strictly forbidden to install anchors at the joints between bricks that are filled with cement mortar. It is also undesirable to choose weak areas with a large number of cracks and chips for work.
To protect the threads from deformation, experts recommend avoiding direct contact of the hammer with metal and using wooden or rubber gaskets.
Before starting work, it is necessary to accurately mark the working area with the determination of the location of the anchor. It is categorically impossible to drill recesses close to each other, since the structure of the brick is porous and fragile, which will certainly provoke the destruction of the structure. When carrying out insulation work, the clamps can be purchased separately.
If necessary, you can carry out not only horizontal reinforcement, but also vertical - the main thing is to avoid the appearance of even a minimal bevel.
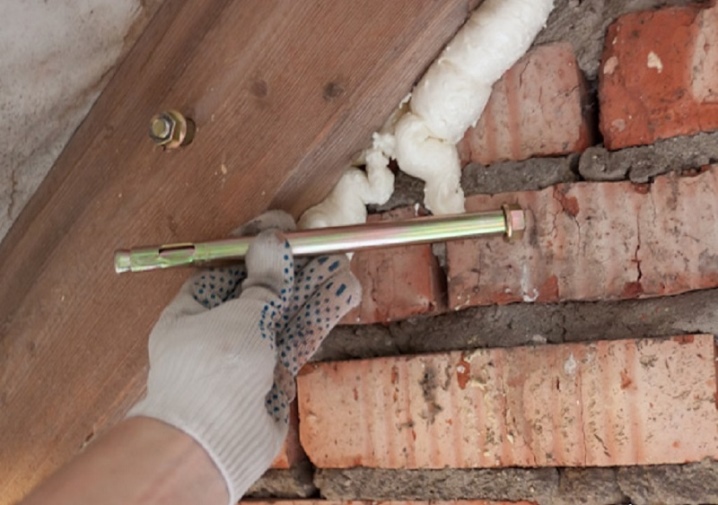
When choosing a fixing device, experts recommend adhering to the following standards:
- sleeve length should not be less than 6 cm;
- the optimal level of entry of the rod into the wall is 9 cm;
- the recommended number of anchors per 1 m2 is 4;
- areas near openings and at joints must be reinforced.
Improper selection of the size, type and material of the fixing element can provoke a weakening of the structure, as well as the appearance of cracks and faults on the walls.
Special brushes, a vacuum cleaner or any convenient means at hand will help to remove debris and dust from the recess.
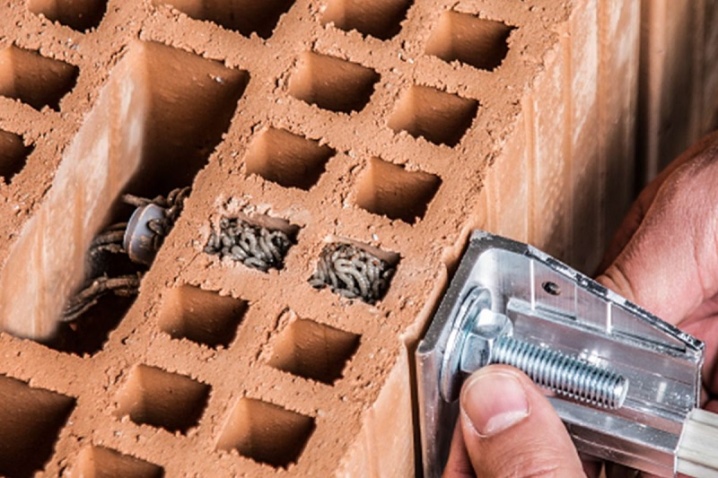
Technology
In order to obtain a reliable and durable design, experts recommend observing the following sequence of actions:
- marking work and precise determination of the location of the clamps;
- drilling a hole of the required diameter in the selected working area;
- complete cleaning of the groove from dust and foreign debris;
- installation of the fixing part;
- full tightening of the bolt head.
An important point is that the depth of the hole should not take into account the thickness of the finishing layer, which will not allow creating the maximum level of fixation.
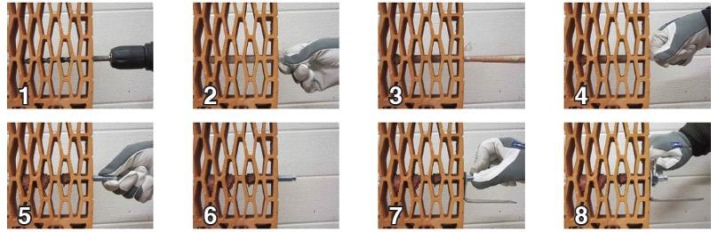
You can learn how to use a chemical anchor from the video below.
The comment was sent successfully.